Net zero: charting the collective journey
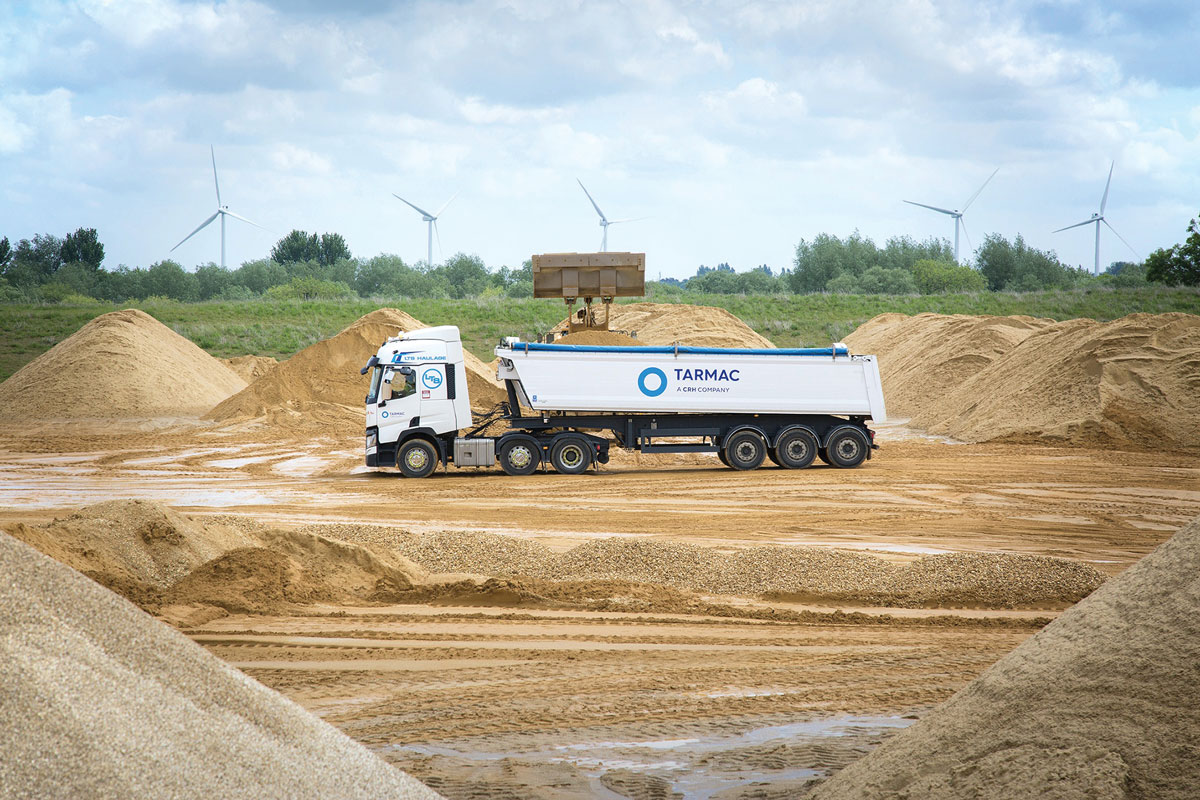
First published in the January 2022 issue of Quarry Management
By Dr Martyn Kenny, sustainability director, Tarmac
No matter what industry you operate in, the reality is that net zero does not come with an instruction manual. The net zero 2050 destination is clear, but how each sector and business get there will be a different journey. Common across all strategies and roadmaps is a need for corporate and industry commitment, innovation, investment, cross-industry partnership, behavioural change, and the right government policies.
Tarmac started their own decarbonization journey several decades ago and have successfully cut CO2 by 24% per tonne of product since 1990. We have continued to evolve our strategy and committed to delivering net zero before 2050. In the shorter term our aim is to reduce CO2 by 45% per tonne of product by 2030 (from 1990).
Tarmac have a clear understanding of the technologies needed to achieve net zero but, like many industrial businesses, we cannot deliver net zero in isolation. Partnership with other sectors, suppliers, government, and our customers will be essential and must define the way we continue to work.
What are the fundamental pieces in our net-zero roadmap? Part of the transition to net zero is focused on key technologies and enabling infrastructure. We need access to fully decarbonized electricity via a decarbonized electricity grid and through on-site renewables such as solar and wind. This is vital as in time it will facilitate the adoption of new low-carbon technologies that require electrical power, such as carbon capture and electrical heat – potentially including plasma energy.
A decarbonized transport network will also be critical. We are already making significant CO2 savings by driving modal shift, increasing the use of rail freight to transport materials, electrifying our car and van fleet, and working with suppliers on future net-zero HGV technologies. Clear government plans for the creation of a comprehensive network of electric charging and hydrogen refuelling infrastructure are essential, so that we can move away from petrol and diesel vehicles and invest in new fleet and reduce delivery emissions.
Continued fuel switching in our cement, lime, and asphalt plants to transition away from fossil fuels is also important. We are building on many years of successfully using alternative fuels, including waste biomass fuels, in our cement kilns, and switching to lower-carbon fuels in our asphalt operations.
As an industry, we estimate that, where available, biomass wastes can in future be used to generate more than 70% of the heat needed for cement production.
Investment in the use of hydrogen, electric plasma, and other new heating technologies will be transformative. We are currently part of a Department for Business, Energy and Industrial Strategy (BEIS) funded trial project using plasma energy with waste biomass in a cement plant, as well as exploring the use of hydrogen as an alternative to natural gas for lime manufacturing.
Carbon capture, usage, and storage (CCUS) is an essential technology to manage the CO2 emitted from the chemical reactions involved in cement and lime production. This technology will allow CO2 emissions to be captured and either permanently locked up in long-term storage or used in other industrial processes. CCUS is a known technology, but to unlock the opportunity there is a need to develop the necessary CO2 transport and storage infrastructure and for a supportive policy regime from government to enable this transition whilst our industry remains competitive.
The continued development of low-carbon asphalts, cements, and concretes is already at the heart of our offer today. We are continuing to innovate products which reduce the whole-life carbon in buildings and infrastructure. We are not only designing products with reduced embodied carbon, but also designing these products to reduce CO2 during the construction process, during the operational phase of the building or asset, and at end of life. This means there are already many low-carbon solutions that can be adopted by our customers today.
Concrete mixes with innovative low-emission constituents will continue to evolve and be enabled by revisions to product and building standards, which, in turn, will encourage wider adoption of their use across the built environment.
This links to a final point. Helping our suppliers and customers to make more-informed decisions to deliver sustainable outcomes is a crucial piece in the net-zero jigsaw. The opportunity to unlock significant environmental gains calls for early engagement with clients and designers to discuss how product design, selection, logistics, and in-use benefits can significantly cut the whole-life carbon impact of a project.
Collaborative partnerships with our supply chain are vital too. We recently launched a new decarbonize club – a collaborative forum of 16 suppliers to drive shared innovation and develop new low-carbon approaches.
Technological advances are a key part of the transition to net zero. But meeting the challenge and accelerating the pathway to decarbonization also require behavioural change across the whole construction value chain too.
- Subscribe to Quarry Management, the monthly journal for the mineral products industry, to read articles before they appear on Agg-Net.com