Impact of Decarbonization on the Outlook for Cement
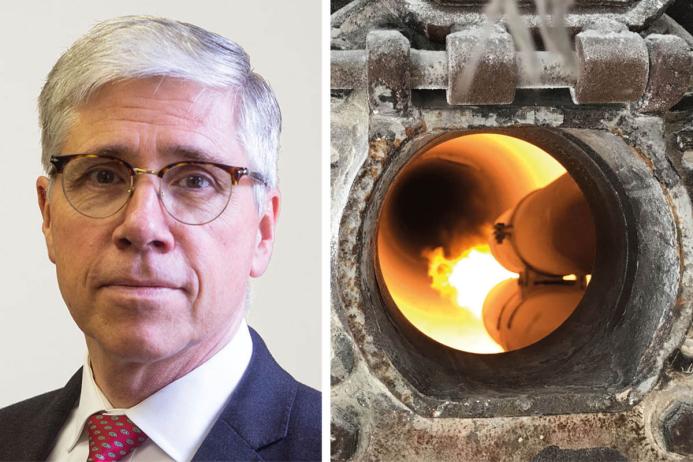
First published in the December 2024 issue of Quarry Management
By Ian Riley, chief executive officer, World Cement Association
Concrete is the most used man-made substance, with around 30 billion tonnes used every year. That is about 4 tonnes for every person on earth. It is used in such huge quantities because it is very cheap and essential to modern urban life. Cement is the binder used to turn a mixture of aggregates and sand into concrete. It is responsible for 7–8% of global greenhouse gas (GHG) emissions.
Outlook for global cement demand
In an often-cited report setting out the challenges faced by the cement industry, the Energy Transitions Commission referred to the International Energy Agency’s (IEA) 2018 report, which stated that global demand would increase from 4.2 to 4.7 billion tonnes/annum by 2050, an increase of 12% from 2020 levels. Other forecasts suggested an increase to 6 billion tonnes/annum.
For reasons looked at later in this article, these forecasts of significant growth are unlikely. Indeed, in its latest forecast the IEA is now projecting flat demand (at 2020 levels) until 2035. World Cement Association (WCA) estimates of 2024 cement demand show a reduction of 9% from 2020 with a further decline of 5% expected by 2050, resulting in a level of 3.6 billion tonnes/annum. The forecast drop in demand for clinker is even steeper due to the steady reduction in clinker factor (the proportion of clinker in cement) and the use of clinker-free binder systems.
Behind these headline numbers are four key trends. First, demand in China will decline before reaching stability. In 2020 China had a cement demand of 2.4 billion tonnes, representing 57% of world consumption. This has fallen to 1.8 billion tonnes in 2024 and is projected to continue its steady decline to 0.9 billion tonnes in 2050.
Secondly, developed countries will be broadly stable. This includes the largely developed markets in Europe, North America, north-east Asia, and Oceania and represents just 13% of world demand for cement.
Thirdly, middle-income countries will experience sustained slow growth. In countries in this group, including the CIS, Middle East, North Africa, Latin America, and south-east Asia, steady growth is expected from 0.8 billion tonnes in 2024 to 1.0 billion tonnes in 2050. This represents an average growth rate slightly ahead of population growth.
Fourthly, emerging markets will see both population and consumption growth. Emerging markets in South Asia and Sub-Saharan Africa will see rapid growth in cement demand, almost doubling from 0.7 billion tonnes in 2024 to 1.2 billion tonnes in 2050. Per capita consumption will increase from 220kg per year to 270kg, almost reaching Western European levels.
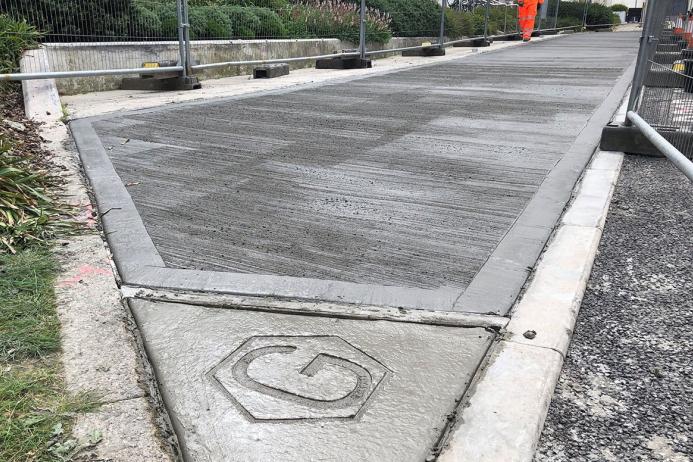
Potential reduction in demand for cement
Being responsible for 7–8% of global GHG emissions, the cement industry is under increasing pressure to reduce carbon emissions. Over the last 30 years the industry has cut per tonne emissions by about 25%. Most cement companies in developed economies have carbon reduction roadmaps approved by SBTi to reduce emissions to net zero by 2050. The measures being taken include the replacement of fossil fuel with alternative, often biogenic fuels, improved fuel efficiency, replacement of clinker with supplementary cementitious materials (SCMs) such as slag and fly ash, and carbon capture and storage (CCS).
There have been several well-publicized high-rise buildings that have used timber to replace concrete and steel. No doubt more of this will be seen in the future. However, limitations in the supply of sustainable timber mean this will not replace a significant portion of concrete.
There is considerable waste in the concrete supply chain with over-design and over-ordering commonplace. Current design and usage practices have been based on cost considerations. Engineers and architects will increasingly deploy modern technology to reduce the quantity of concrete used to achieve specific design objectives and reduce waste.
In addition to the reduction of wastage, there is potential to reduce binder demand with greater use of admixtures and the addition of novel materials such as graphene and carbon nanotubes. These additives claim substantial increases in flexural strength and hence the possibility of reducing concrete thickness by 30% for the same performance.
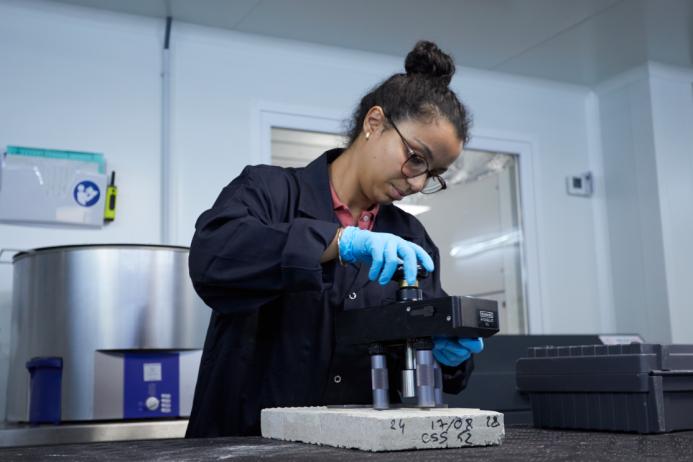
Alternatives to traditional cement
Many companies are exploring and developing clinker-free binder systems both with traditional replacements such as ground granulated blast-furnace slag (ggbs) and based on geopolymer concretes with steel slag, mine tailings, and other industrial by-products. These are likely to be accepted initially for less-sensitive applications such as non-structural and sub-surface uses, which comprise well over half of total concrete demand.
Several companies have developed technologies to reduce the carbon footprint of precast concrete using a CO2 curing process. These use lower-carbon materials and mineralize CO2 during the curing process. Examples include CarbonBuilt and Solidia Technologies.
New clinker-free binder systems have been developed although there are only a few examples of large-scale projects, such as the use of Wagner’s Earth Friendly Concrete (EFC), a geopolymer concrete, in the construction of Brisbane Airport in Toowoomba, where approximately 40,000m3 of EFC was used.
Another company that the WCA has spoken to on its podcast, The Clinker Factor, is Cemonite (formerly Saferoc), a Norwegian company developing an innovative concrete product that as well as using mine tailings to reduce carbon emissions by 80%, also recycles titanium mine waste. The Cemonite factory is located on the west coast of Norway.
Although not entirely clinker-free, Ecocem’s ACT (Activating Cementitious Technology) is a low-carbon cement technology that reduces carbon by 70% and has potential for rapid scaling. ACT uses raw materials already approved by cement and concrete standards and Ecocem have signed a partnership agreement with Cemex for its use in their French ready-mixed concrete plants.
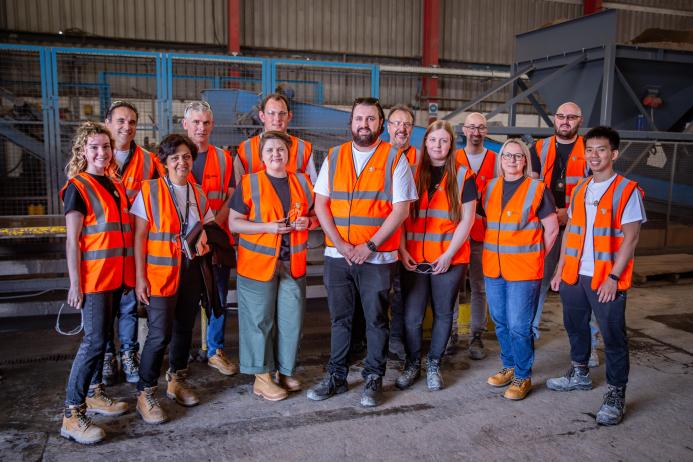
Material Evolution are about to launch the UK’s largest ultra-low-carbon cement plant in Wrexham, where annual production capacity will be 150,000 tonnes. The Material Evolution cement will have 80% less embodied CO2 and the plant will make Material Evolution the largest producer of low-carbon cement in the UK.
Like Ecocem, Hoffman Green Cement Technologies is another company that received investment from Breakthrough Energy. In the first half of 2024, Hoffman announced sales of 7,833 tonnes of clinker-free cement based on slag and other industrial waste materials. Based in France, they have also announced a plant in Saudi Arabia.
Have we reached a tipping point?
In most cement decarbonization roadmaps, CCS is by far the largest contributor to emission reduction, for example making up 61% of the MPA roadmap. However, CCS projects are complex, high cost, involve many parties, and have typically had lead times of seven years from announcement to commissioning. Furthermore, demand for CSS is accelerating around the world and projects are already behind schedule. Supply chain constraints around key components and engineering skills are further delaying projects. At the recent European Cement Decarbonisation Summit in Hamburg, several speakers referred to delays in CCS projects due to lack of standards for the gas to be transported and delays in shipping infrastructure. In the UK, most cement plants are not in the catchment areas of government-supported CO2 transportation networks. In short, it seems unlikely that CCS will make much of a contribution to carbon reduction before 2035 or even later.
Looking at the carbon reduction challenge from a cement producer’s standpoint does not give the full picture. From a client perspective, cement and concrete are only 2–3% of their total costs. In the past this was enough to consign concrete to the ‘not very interesting’ category. However, concrete represents roughly 35% of the embodied carbon on a project. As developers and contractors struggle to meet both self-imposed and government-imposed standards, they cannot afford to wait for CCS projects to come on stream.
Conclusions
Driven by pressures to decarbonize, the cement industry faces change on a scale it has not seen in the past and no forecast can be considered definitive. However, it is clear that demand for clinker will decline substantially. In 2024 clinker production is projected to be 2.8 billion tonnes, a drop of 370 million tonnes from its 2020 peak in just four years. This is projected to fall to less than 1.9 billion tonnes by 2050, and perhaps as low as 1.0 billion tonnes.
This has significant implications for demand for CCS equipment and may be sufficient to reduce the capital and supply chain limitations that the industry will face as demand for CCS grows rapidly over the next 25 years.
The decline of clinker demand to perhaps half of current levels is a huge challenge for the cement industry which is already beset with the problems of overcapacity in most countries. However, it is also a big opportunity. Concrete is used in huge quantities because it is an excellent, long-lasting material, and because it is very cheap. The future offers the prospect of greater customization not only to reduce embodied carbon, but also to tailor concretes to application requirements. This is a future in which the agile and forward-looking will prosper.
Subscribe to Quarry Management, the monthly journal for the mineral products industry, to read articles before they appear on Agg-Net.com