Wirtgen Slipform Pavers Chosen for Mongolia's New International Airport
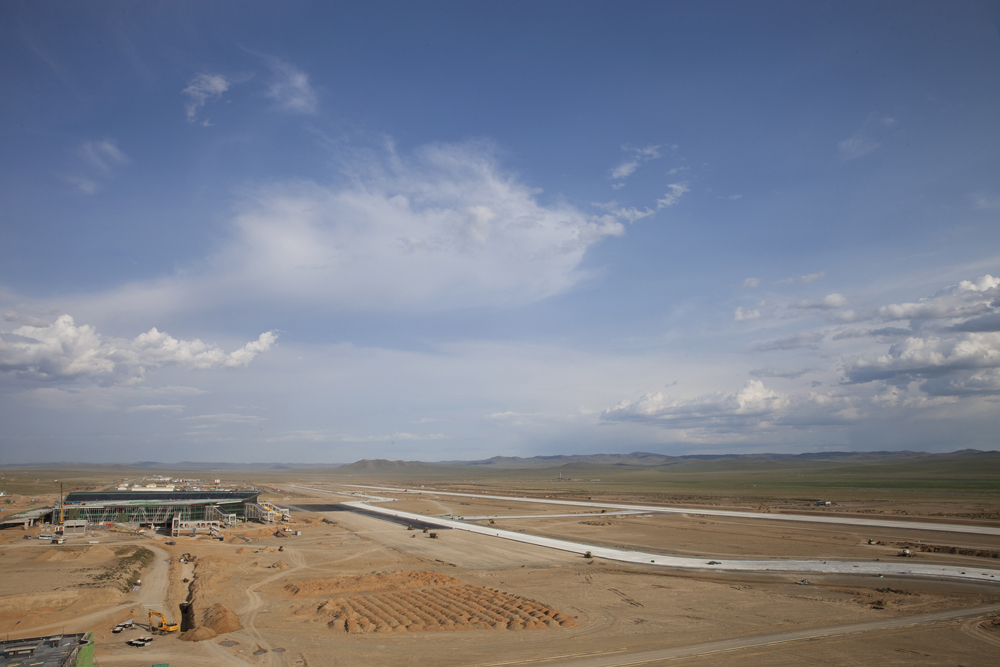
First published in the December 2016 issue of Quarry Management as Facing the NUBIA Challenge
Mongolia’s New Ulaanbataar International Airport will treble passenger capacity and increase cargo handling ten-fold. Wirtgen’s high-performance SP1600 and flexible SP500 slipform pavers were chosen to guarantee a high-quality concrete paving result and to meet the tight project deadline
The capital city Ulaanbaatar is the hub for Mongolia’s growing economy and the center of expansion of trade and industry in the country. As the world’s second largest landlocked country, Mongolia depends heavily on air traffic for transporting passengers and cargo in to and out of the country. As such, the nation’s existing Chinggis Khaan International Airport, which was built in 1956 and upgraded for international traffic in 1987 and 1997, was in urgent need of upgrade and expansion.
‘The current airport faced safety, usability and operational difficulties, such as: unidirectional landing due to the 2.5% slope of the runway and high mountains to the south; flight delays caused by limited visibility due to smoke pollution from domestic heating during the winter time; and deficiencies in the passenger terminal building configuration and capacity,’ said Enkhbat Navaantseden, project director of the New Ulaanbataar International Airport (NUBIA).
‘For this reason, the country’s new international airport is located in the Khushigiin Khundii valley, in the province of Tuv, some 52km from Ulaanbaatar. NUBIA is being built on an easily accessible elevated plain with no mountains in the immediate take-off and landing air corridor.’
High-grade concrete runway
The new airport has been designed with a robust, 3,600m long, category 4E runway constructed from concrete. This will be better equipped to withstand the harsh weather conditions of Mongolia’s extreme continental climate, and will be able to handle large aircraft such as Airbus A340s and Boeing 747s.
The new location together with its advanced design and installations plus 24h all-weather air traffic control system will help to improve safety at the airport. NUBIA has been designed to deal with 3 million passengers a year, 300% more than currently, and the airport will be able to handle 10 times more cargo than at present.
To finance the airport project, the Government of Mongolia signed a 40-year soft-loan agreement for JPY65.6 billion with the Japan Bank for International Cooperation (JBIC). The Mitsubishi-Chiyoda Joint Venture (MCJV) won the technical bid and in May 2013 the main construction contract was signed between MCJV and the Civil Aviation Authority of Mongolia, with the entire construction operation awarded to prime subcontractors Samsung C&T. Longstanding South Korean Wirtgen customers Sungdo Construction, specialists in slipform paving operations, are carrying out the concrete paving work, which started in May 2014.
Dongin Park, Samsung C&T’s project manager for the NUBIA project, summarized the construction challenges: ‘We have to face the extreme continental climate with short, hot summers and long, icy winters. This gives us a construction time window of only three to four months during summertime. The wind from the Gobi desert and the intensive sunlight quickly dry out the concrete. That’s why the main paving operation with the SP1600 had to happen during night shifts.’
High-performance paving
The SP1600 is the flagship among Witrgen’s large slipform pavers. It paves high-quality concrete slabs at widths of up to 16m, and a concrete paving kit is available for integration into the SP1600 to allow the economical paving of dual-course concrete slabs in a single operation. For the new airport, the SP1600 is paving the 45m wide x 3,600m long runway in several segments with a paving width of 11.25m and an average paving thickness of 38cm.
The first layer paved by the SP1600 is a 27cm thick cement concrete slab. This is followed by a second layer consisting of an 11cm thick cement concrete slab paved wet-in-wet immediately after the first layer to achieve a perfect bond between both courses. Wire bar fabric is placed between the two layers for additional reinforcement in accordance with the specifications of the Japanese Azusa Sekkei and Oriental Consultants Joint Venture, which developed the airport design. Optimal material compaction is ensured by up to 48 electric vibrators that emit high-frequency vibrations, while the correct functional properties of the concrete surface are achieved by the SP1600’s oscillating beam and super smoother.
‘We save a lot of time and money with the SP1600,’ said commercial manager Seunghwan Lee. ‘Instead of using four SP500 pavers, we decided to go just for one SP1600, as we have had good experiences with this high-performance paving train in the past. Dual-layer paving with a single machine speeds up our operation.’
He added: ‘We are paving concrete with a material cost of around US$20 million and using around 135,000m3 of concrete for the runway, taxiways and aprons.’
The SP500 takes care of the slightly curved aprons and some taxiway sections. Here, up to five adjoining parallel slabs are paved by the easily manoeuvrable machine, which has a paving width of 5.625m. In total, the SP500 will pave around 50,000m2 of taxiways and 7,500m2 of aprons.
Customer service support
Paving specialists Sungdo Construction brought several containers of spares/wear parts to the remote job site. The regional service network of the Wirtgen Group supports the operation in several ways. If there is a need for additional spare parts, these can easily be flown in via a daily direct flight from Ulaanbaatar to the South Korean airport of Incheon. The local Wirtgen dealer in South Korea, Sambo Heavy Industries, can supply the spare parts or, if necessary, order them directly from Wirtgen’s headquarters in Germany. Moreover, as Ulaanbaatar Airport has a twice-weekly connection with Berlin-Tegel Airport in Germany, the timely availability of parts is also ensured in an emergency. Service engineers from Wirtgen China and the Wirtgen headquarters in Germany can also be on site within 24h.
For more information visit: www.wirtgen.com
- Subscribe to Quarry Management, the monthly journal for the mineral products industry, to read articles before they appear on Agg-Net.com