Sustainable Versatility
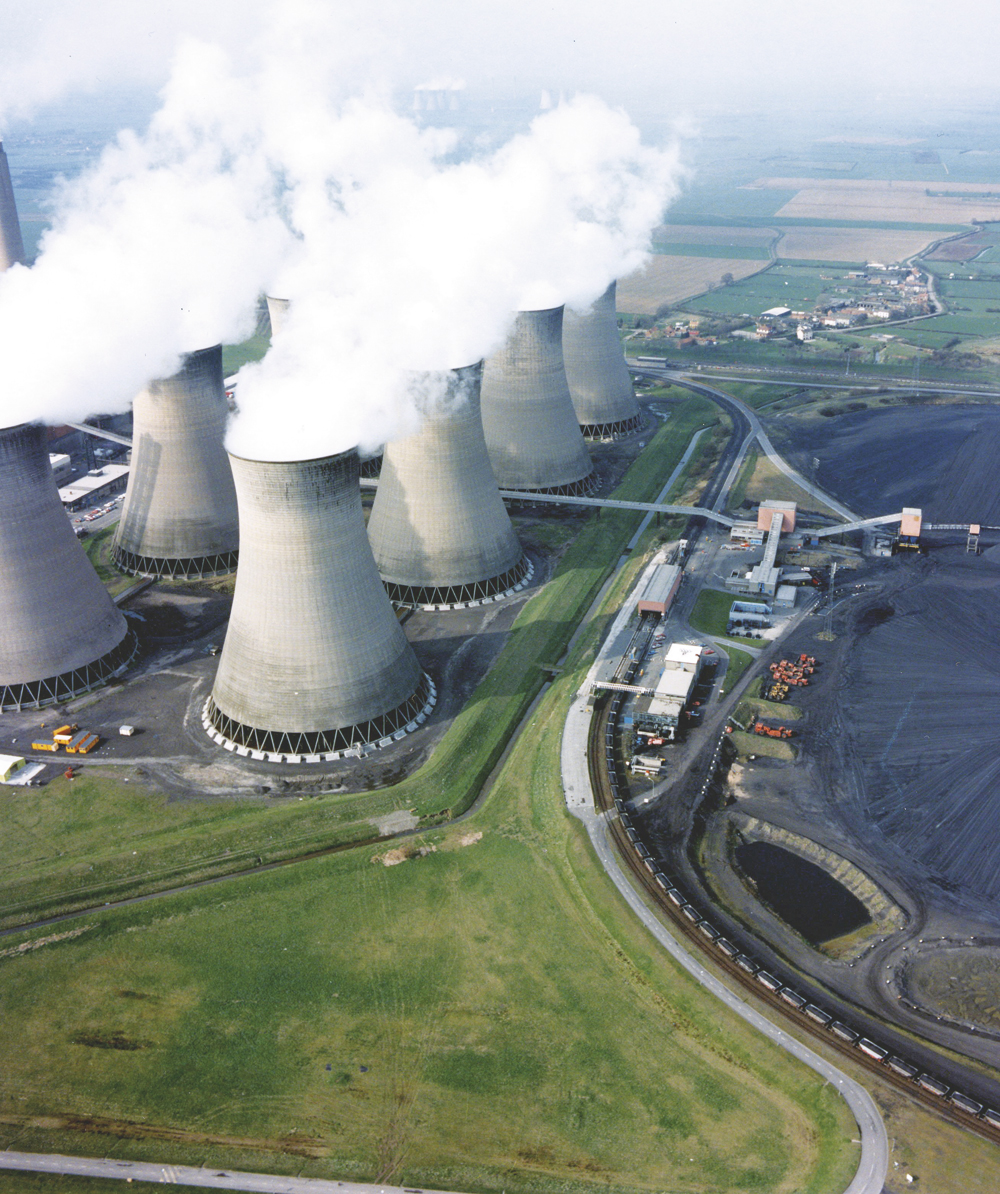
Can fly ash produced at UK power stations help reduce the environmental impact of concrete production in the UK? Yes – and without harming quality, consistency or durability, says Dr Lindon Sear from the UK Quality Ash Association
Concrete remains one of the construction industry’s most durable and effective materials. While the rise of the steel and glass skyscraper is well documented, they are nothing without the core strength and effectiveness of high-quality concrete. But concrete has not always been known for its green credentials, and in a world where sustainable accreditation is essential in new buildings, the industry is under considerable pressure to ‘green up’.
And it needs to; concrete and cement production accounts for 5% of global carbon emissions each year – more than aviation – and has become a significant consumer of natural resources, including raw aggregates and water. As a result, in 2008 MPA The Concrete Centre, the British Precast Concrete Federation and the UK Quality Ash Association (UKQAA) launched the Concrete Sustainability Strategy to reduce the impact the sector has on the environment in the UK.
The Strategy consisted of three key targets: to cut carbon emissions in the UK – where the industry is responsible for around 2.6% of national CO2 emissions – by 30%; to reduce waste sent to landfill by 90%; and to ensure that 95% of concrete is accredited to BRE standard BES 6001. It also aimed to help the industry prove it is willing and able to protect quality and innovate in the light of climate change.
That is a considerable challenge, but it is one the sector has worked hard to tackle. Since 2008 the concrete industry has reduced waste by 60% and ensured that 88% of production meets BES 6001, but it is also looking at other ways to make concrete greener and cleaner. Fly ash – as produced by coal-fired power stations – has been an important material in this respect and provides manufacturers and contractors with an opportunity to improve concrete while reducing the carbon footprint of products and buildings.
In its raw form, fly ash is the residue left behind once coal has been burned and collected by electrostatic precipitators in coal-fired power stations. This involves a series of charged rods that attract ash particles and force them into ‘hoppers’ which catch and hold the material. Coal-fired power stations produce three by-products: gypsum, which is used for plasterboard; furnace bottom ash (FBA), which is used in block making; and fly ash (sometimes called pulverized fuel ash – PFA), which holds significant benefits when used in concrete manufacture.
As a very fine, inert and lightweight material, fly ash is ideal when used in the concrete mix as a substitute for cement. It is less susceptible to water permeation and aggressive chemicals than traditional cement, making it particularly suitable for use in sea defences, bridges or tunnelling. During the construction of the Channel Tunnel, for example, fly ash-based concrete was used extensively to improve strength and durability in complex circumstances.
Crucially, it also requires less water during the production process, which makes it an easier and more versatile material to work with. For this reason, it is not unusual for contractors working with fly ash concrete to produce work that has sharper, cleaner corners and edges and a smoother surface appearance. And because there is less water in the mixture, it is stronger over the long term and less prone to cracking and discolouration. This has been a key reason for its use in major high-rise structures, such as the Burj Khalifa in Dubai and the Shard in London, to ensure stability and strength in demanding conditions.
There are also considerable environmental gains on offer. As well as reducing the amount of water required in the mixture, fly ash can limit demand for natural resources. Studies conducted by the UKQAA and partnership bodies have shown that fly ash can be included in the concrete mix at rates of up to 80% of the cement content, significantly reducing the need for both natural aggregates and water, while reducing the concrete’s carbon footprint. While cement creates approximately one tonne of carbon in the manufacturing process and contains 913kg/tonne of embodied carbon, fly ash contains 4kg/tonne.
The marriage of sustainability and versatility is extremely encouraging, but fly ash is also carefully controlled in the UK. To ensure the quality and consistency of fly ash (and both PFA and FBA), the Waste Framework Directive and Quality Protocol for PFA and FBA exist to monitor the control, transportation and use of all ash products. All UK power stations follow these regulations and any material that complies with the Quality Protocol is guaranteed to be consistent, reliable and, importantly, safe for use. It also denotes fly ash as a commercial product rather than a waste, which makes it easier to source and transport around the country.
These quality assurances are vital and have provided a framework for the increased use of fly ash across the UK, providing end-users with the technical information and confidence they need to specify the material in their products. The UKQAA is encouraged by the response from the industry, and with globally significant projects such as the Shard and the Burj Khalifa leading the way with this material, is certain it will only get better.
For more information about fly ash or PFA and how to source it, visit: www.ukqaa.org.uk