Sustainable Production
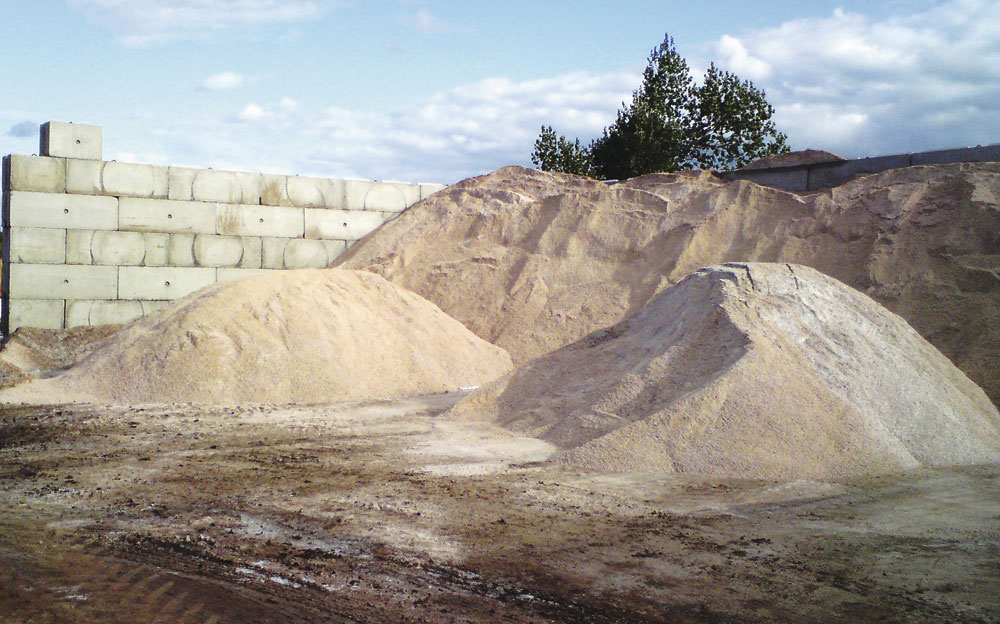
Owen Batham, managing director of Shropshire-based Elite Precast Concrete Ltd, explains how a locally sourced secondary aggregate is helping to reduce demand for primary resources without compromising the quality of the company’s end product.
The construction industry is facing huge pressure to move towards more sustainable production processes, with the spiralling cost of purchasing primary materials only heightened by the ongoing economic uncertainty, which has resulted in fewer construction projects to share around what was already an extremely competitive sector. These factors are exacerbated by increasingly strict environmental rules and regulations, including the Government’s ambitious target to halve the amount of construction waste sent to landfill by the end of the year, not to mention the countless EU regulations that companies must meet.
With the UK construction industry estimated to use more than 275 million tonnes of aggregates a year, it is no surprise that one area pinpointed for improvement is the need to reduce the reliance on primary aggregates by increasing the use of more sustainable recycled or secondary aggregates. Less than a third of the 275 million tonnes currently required each year is actually sourced from recycled or secondary sources.
Precast concrete, which is said to account for 35 million tonnes of building products per year and which can incorporate a high proportion of recycled content in its material make-up, obviously has potential to play an important role in significantly improving recycling rates. However, this possibility also throws up a dilemma as to which type of material is the most economically and environmentally suitable to use.
It may come as a surprise, but for precast concrete production, recycled aggregate is not the environmental answer its name would suggest. Because the quality of recycled material is variable, it may not be possible to be entirely certain of the content or condition of recycled aggregate, which often leads to inconsistencies in concrete quality. Continuity of supply can also be an issue with recycled aggregates.
Also, an inferior end-product made from substandard material will obviously need replacing more often than one made to a superior standard, leading to additional use of energy, materials, labour and transportation. And this does not even take into account the fact that precast concrete produced with recycled aggregate cannot easily be recycled at the end of its life.
So, what at first glance appears to be a ‘sustainable’ solution can actually turn out to be a more costly and resource-intensive one, especially in the case of Elite Precast Concrete Ltd, whose nearest source of recycled aggregates is Birmingham.
As an alternative to the more expensive yet inferior-quality recycled aggregate, Elite Precast Concrete tasked their technical team with the challenge of sourcing a local secondary aggregate – a material that a local quarry would be happy to sell at a competitive price (ie not primary quality) and which has excellent environmental criteria (ie being of limited demand and requiring further processing prior to being sold into the more conventional construction materials industry).
The secondary aggregate sand that Elite Precast now use is consistent, uncontaminated and an ideal raw material for use in the production of the company’s durable interlocking concrete blocks, which have a strength of more than 50kN and offer 120-year lifespan. It virtually eliminates the variable end results associated with concrete produced using recycled aggregates. As the blocks tend to be used in particularly harsh environments, such as waste storage and segregation or embankment retention, a resilient product that can withstand these conditions is essential. In many cases, the blocks will be used repeatedly across a number of different projects because of their durability. Another advantage of using a secondary aggregate sand is that the concrete can be 100% recycled at the end of its useful life.
In addition to the use of secondary aggregates, another element of Elite Precast’s production process that has helped minimize environmental impact is the fact that the company’s precast concrete blocks are made to ‘stock’, rather than as bespoke or made-to-order products. As this involves a repetitive process using concrete moulds of exactly the same size time and time again, any potential margin for error is minimized and, as a result, very little material wastage occurs.
Manufacturing for stock rather than to order also makes it easier to implement take-back schemes, which the British Precast Concrete Federation has been extremely keen to promote in recent years as a way to improve sustainability – once a project is completed, the blocks can be returned to the supplier and re-sold for future use.
This approach has forced Elite Precast’s sales team to adopt a new strategy, not necessarily selling what the customer may initially want – arguably the easy bit – but selling what the company makes and working with the customer to find ways of making this work. This ensures the lowest possible cost and highest levels of customer service – it typically takes just 24h from receipt of order to actual delivery.
Elite Precast have also embraced the principle of conserving precious water resources – the company’s unique, fully integrated rainwater harvesting system can hold more than 19,000 litres of water at any one time – enough for three days of continuous production.