Special Concretes Help Construction Reach New Heights
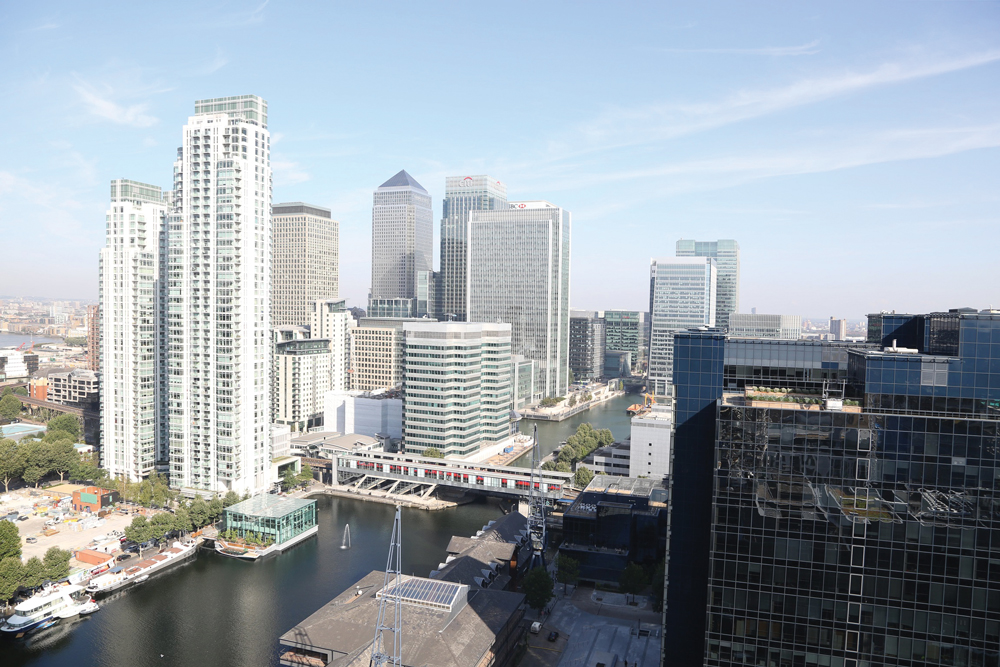
First published in the December 2017 issue of Quarry Management as Tower of Strength
Special concretes helping regional construction reach new heights
By Brian Kent, national technical director, Tarmac
Over recent years, a trend in construction has begun to emerge across the UK: developers are increasingly looking beyond London, drawn by significant opportunities for multi-residential developments and lower construction costs. As a result, cities such as Birmingham and Manchester are seeing more of these types of construction project being delivered.
As more high-rise projects begin to come on line, there is an increased requirement for materials providers to ensure consistent availability of innovative construction materials across regions to meet the demand of this activity. This must, however, be matched with a consistency of quality in the final product.
The volume of available prime development space in the UK’s major cities is declining at a time when the demand for new residential and commercial space is growing. The solution for a large proportion of developers is multi-storey buildings.
The interesting challenge for the wider construction industry is identifying the best approach for delivering these superstructures, and there has been a striking shift in the way that buildings are now designed.
This trend for taller structures necessitates the use of innovative materials with significantly higher compressive strengths, which can be up to 90MPa, when the standard for anything up to 12 storeys is generally around 60MPa. To fulfil these more challenging load path, robustness and stability criteria, developers often specify special high-strength concretes for the vertical elements of new tall buildings.
Aggregate supply
Key to managing the expectations that come with changes in regional construction demand is ensuring that products are sourced and manufactured to the same rigorous high standards. The manufacture of a high-quality product is contingent upon ensuring that there is a reliable local aggregate source; a point that is crucial to keeping the regional project pipeline moving.
Aggregate selection is of paramount importance to the production of specialist concretes. The strength, size, and surface characteristics of the chosen aggregate all play an important role in the ultimate strength of high-strength concretes. Get these wrong and any one of these properties could potentially limit the bond between the cement paste and the aggregate, resulting in a lower final strength.
In high-strength concrete, the interface between the aggregate and cement paste has a more pronounced effect on the final product than in conventional concretes. A weak interfacial bond can have a serious impact on the level of stress at which cracking occurs. This can be altered by a number of factors, including shape, texture, grading, cleanliness and nominal maximum size of the aggregate.
For example, rough-textured and angular coarse aggregates provide a stronger bond and are, therefore, generally more suitable for use in high-strength concrete than smooth-textured aggregates. The ideal aggregates for high-strength concretes are generally cubical in shape, and should not contain large quantities of flat or elongated pieces.
The use of crushed aggregates in high-strength concretes helps to further prevent and eliminate potential zones of weakness in the final product. Smaller, rougher-surfaced pieces typically produce higher concrete strengths since they allow a stronger bond between the cement paste and the aggregate. Aggregates used for special concretes should also be cleaned of impurities prior to use, to prevent any structural defects during the material’s application.
The ingredients that make up high-strength concrete are, therefore, no different to conventional mixes; they are simply optimized to maximize the strength of the product. Manufacturers of special concretes adapt the design of their materials by varying the proportions of cement, water, aggregates and admixtures to achieve the highest-strength final product.
Beneficial outcomes
Using special concretes can, undoubtedly, have a significant number of benefits for tall building construction. The use of high-strength and high early strength concretes can extend beyond merely the vertical components of a new build, yet these special concretes only tend to be adopted if the schedule of a project begins to slip.
This need not be the case: if specified from the outset, these types of products can maximize the usable space within a structure, as well as generate savings and have a positive effect on the overall build programme.
The higher mechanical properties of high early strength concretes can be benefited from in the early days immediately after pouring, in addition to having increased strengths once dried. Long-term deflections can also be controlled by using high-strength concrete, while keeping floor thickness to a minimum.
Equally, using the same product for both the walls and the floors can reduce the risk of differential stiffness between vertical and horizontal elements. Laying thinner, stronger material for both the walls and the floors not only has a beneficial outcome on the amount of light in the subsequent rooms, the available space and the external envelope, but also makes the building weigh less.
Clearly, consideration of special concretes at the design and construction stages for tall buildings can be beneficial in supporting the growing regional construction pipeline. However, the key to manufacturing these products to the highest standards is in the supply of aggregates and selecting materials with the optimal characteristics.
Upon application, being able to reduce element sizes, speed up construction and facilitate easy installation of the product at height by using special concretes, all create project cost savings while boosting productivity, maximizing space and reducing materials.
Identifying the right materials and considering the life cycle of the build are crucial to addressing the challenge of tall building construction as our regions continue to grow. We need to ensure that we are building and sourcing our materials smarter in order to create the new skylines that showcase tall buildings.
With increasing opportunities for developers to deliver multi-storey residential and commercial buildings, the construction materials industry has a more important role than ever in ensuring that the innovative products required to fulfil these projects are readily available across the UK.
Efficiency savings
An independent study commissioned by Tarmac and conducted by Arup on real-world projects, has demonstrated how self-compacting and high early strength concretes are able to add value to multi-storey developments. Cost savings can be achieved due to smaller foundations and a reduced façade surface, because less material is needed for construction compared with traditional concrete.
The study showed that efficiency savings can be realized for composite slabs and shear cores for steel-framed commercial buildings, as the material can be poured more quickly and requires less finishing than a standard mix. In a 21-storey steel-framed building, for example, this could unlock overall savings of approximately £268,000, with faster construction also allowing earlier access for follow-on trades.
For a 16-storey concrete-framed residential building, the combined savings on materials, plant and labour with the reduced external envelope totals £391,000, representing a cost saving of 8.4%.
If the concrete cores for these types of buildings are on the critical path and constructed using jump-form, the use of high early strength concrete in this way can potentially offer a 40% time saving for the core construction, translating into a 5% reduction to the total overall programme.
- Subscribe to Quarry Management, the monthly journal for the mineral products industry, to read articles before they appear on Agg-Net.com