Pumps in the Ready-mixed Concrete Industry
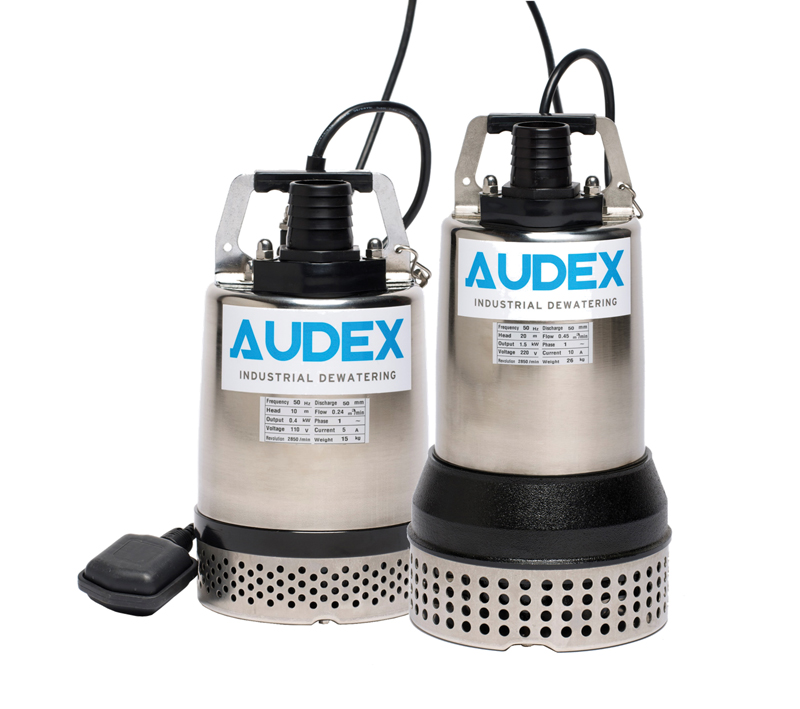
First published in the December 2015 issue of Quarry Management as Meeting the Challenges
Mark McCreadie of Atlantic Pumps discusses pumping applications in the ready-mixed concrete industry and looks at some solutions to the challenges faced
With the UK concrete industry again showing growth, primarily due to the resurgence of the construction industry, it is opportune to look at the vital role pumps play in keeping ready-mixed concrete plants operational, and ways of reducing downtime.
The industry faces the challenge of large fixed costs, such as maintaining trucks and operating batch plants, coupled with a competitive market; this puts a premium on maximizing production and avoiding downtime. Delays caused by a pump being taken out for repair can lead to problems such as a wedge pit becoming inoperable, truckmixers not being cleaned and batching plants coming to a halt.
So, what are the pumping applications at a ready-mixed concrete plant, and what can be done to minimize downtime and keep the site producing?
Wedge-pit pumps
A submersible pump is usually required to remove the waste water out of the wedge pit, often to be stored and recycled. This water can be reused to clean out truckmixers, although it will often contain aggregate particles and metal or plastic fibres. This presents a challenge as these particles and fibres can clog the pump and/or damage it internally.
Clogged pumps have to be dismantled and cleaned, and damaged parts have to be replaced. This leads to downtime as the parts have to be sourced and the pump taken apart and re-assembled. It is worth considering an industrial-type pump for this application, as the slightly higher purchase price will be more than compensated for by the reduction in downtime these pumps offer. An example of an industrial pump that is well suited to this application is the Audex AL-Series submersible pump range.
Audex AL-Series pumps have, as standard, the following features:
- High-chrome impeller – these last much longer than plastic impellers when handling abrasive material such as concrete slurry
- Durable stainless steel casing – stainless steel outer casing, stator casing, strainer, shaft and hardware for maximum corrosion resistance
- Class-F motor insulation – this provides greatly increased protection from overheating
- Large stainless steel strainer – this offers a bigger surface area leading to less clogging by particles and fibres
- Double seals – this means the pumps are much more reliable, typically having longer wear lives and a reduced chance of failure.
As well as reducing downtime, these pumps will last much longer in the harsh environment of the ready-mixed concrete plant, so the customer will get more value for their investment.
Fresh-water pumps
These are used to pump fresh water from the storage tank to the batching plant. This application is much less damaging owing to the absence of abrasive or corrosive material in the liquid. Typically, brands such as Varisco or Ebara are used in this application.
Admixture pumps
These pumps are used to add liquid additives to the concrete being mixed in the batching plant. Many sites use Mono pumps or equivalent small electric gear pumps, or similar. However, it is worth considering an alternative air-operated diaphragm pump, such as the XairePro XP15 ½in pump.
The use of a diaphragm pump offers the following advantages:
- Ability to run dry – not only is it self-priming, it will not be damaged if allowed to run dry
- Powered by air – this is safer than running electric cables through the plant. These small pumps have low air consumption, so will not draw too much off the compressor.
- Simple to repair – a big advantage is that these pumps can be repaired on site and fewer parts are required. Moreover, parts are stocked in the UK for rapid despatch.
The XairePro range of pumps integrates into all common admixture systems.
Flap-valve pumps
Some heavily used wedge pits face particular challenges with the water containing larger lumps of concrete and metal and plastic pins. This can prove challenging for any kind of submersible pump.
The XairePro flap-valve pump replaces the normal ball valves found in an air-operated diaphragm pump with flap valves which open wide enough to allow large particles to pass through. Using a pump with this capacity can significantly reduce internal damage and clogging.
Multi-stage pumps
These are often used to increase the pressure of the water used to wash out truckmixers. Ebara and Lowara are among the commonly used brands in this application.
A proactive pump supplier
The pump supplier should be a key partner in the management of any ready-mixed concrete plant. A pump company that understands the challenges the operator faces and can specify the appropriate pump is vital. Equally important is an understanding that minimizing downtime is critical to the success of the operation. Instant reaction to quote requests and rapid despatch of correct parts and equipment are crucial.
Atlantic Pumps recently demonstrated their ability to supply industry at short notice when they helped avert a costly site closure at a Hanson ready-mixed concrete plant. The Sheffield-based pump distributor was contacted by Justin Johnson, district operations manager for the Manchester area, after a submersible pump used to drain a recycled water tank failed, leaving the tank in danger of overflowing. This would have damaged the plant, breached the conditions of the site’s environmental permit and resulted costly downtime.
The Atlantic Pumps team had a 5.5kW Audex AS Series 3in pump installed and operational on site in less than 4h from Mr Johnson’s initial phone call to their office. During that period, Atlantic worked remotely and on limited information (details could not be taken from the existing pump), co-ordinated with Mr Johnson for clarification on some essential points, specified the correct pump for the site, prepared a quotation, supplied delivery options and delivered the pump.
Commenting on the speed of the operation, Atlantic Pumps’ managing director, Andy Smith, said: ‘It has been the guiding principle from day one at Atlantic Pumps that we respond to our customers’ needs quickly. In this instance, it was clearly demonstrated that rapid assistance to a customer’s needs saved them from some large costs. With the ready-mixed concrete industry showing welcome growth, the uptime of a plant is more valuable than ever.’
For more information visit: www.atlanticpumps.co.uk
- Subscribe to Quarry Management, the monthly journal for the mineral products industry, to read articles before they appear on Agg-Net.com