Powering up Hinkley Point C with ‘nuclear concrete’
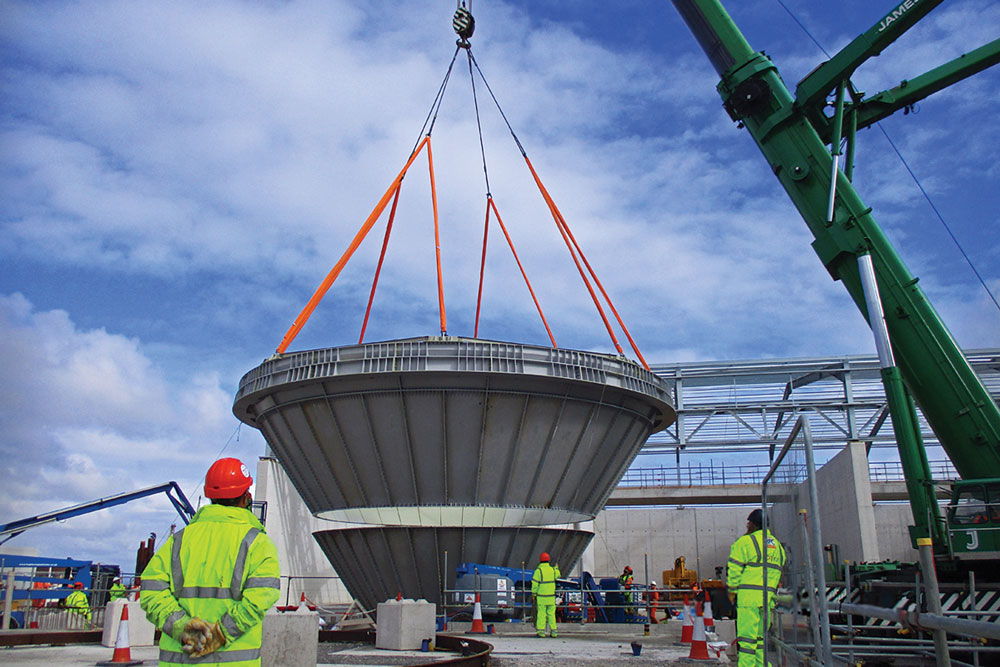
First published in the December 2018 issue of Quarry Management as The Nuclear Option
ConSpare help design mixing and batching equipment to power up Hinkley Point C with 'nuclear concrete'
EDF Energy’s Hinkley Point C is the first of a new generation of power stations to be built in the UK. It is the biggest construction site in Europe, providing 25,000 jobs over the lifetime of the project. Once operational, it will employ 900 people and generate 7% of the UK’s low-carbon electricity.
Because of the nature of the project, the concrete used to construct the power station must be of the very highest quality – ‘nuclear concrete’ is the term that’s been coined to describe it. It is being produced by Hanson Aggregates on behalf of project contractors Bylor, a joint venture of construction giants Bouygues and Laing O’Rourke.
To achieve nuclear concrete, a very precise mix needs to be followed in every batch of concrete made, and each batch must comply with extremely stringent quality standards laid down by an independent regulator, the Office for Nuclear Regulation.
The journey towards nuclear concrete for the site began in 2013, and it took three years of rigorous development, testing and refining to get to the point where concrete of the required quality was being produced on a consistent basis.
The challenge
From a concrete point of view, Hinkley Point C is one of the most complex and challenging construction projects the industry has ever seen. Extreme precision is required to create concrete to the highest of specifications, and this is both demanding and time-consuming to achieve. The sheer volume of concrete required also presents challenges.
ConSpare have been involved in supplying concrete know-how, equipment and ongoing logistical spare parts support to major construction projects for more than 30 years. Past projects include the Channel Tunnel, DP World London Gateway and Crossrail.
When plans to build Hinkley Point C nuclear power station were first put on the drawing board, the company was contacted at an early stage by specialist concrete batching plant manufacturers D&C Engineers and asked to assist in designing mixing and batching equipment that could cope with the demands and challenges of a project of this size.
Making concrete involves a series of different processes, all of which are interdependent upon each other. Working closely with D&C Engineers, ConSpare drew upon their experience and expertise in all aspects of the production process to develop a high-quality, robust solution, with the aim of delivering end-to-end co-ordination and ensuring no single part of the process would let the whole project down.
The solution
It was determined that three concrete batching plants would be required to achieve the levels of concrete production needed to complete the Hinkley Point C development. Teka TPZ 4500 planetary mixers were specified for each plant, based on successful performance in similar-sized projects in the UK and globally. This model incorporates a unique counter-rotational mixing action that is well suited to the quality demands being placed on the equipment. Having ensured that the right mixing action was deployed, the next step was to ensure that performance would be maintained over the long term, batch after batch.
Clean mixers mix better, so the challenge for batching plant operators in projects such as Hinkley Point C is to ensure that mixers are kept clean, otherwise mixing efficiency quickly starts to diminish. Due to the nature of the mixing process, concrete residue accumulates in the mixer over the course of every production shift, and this build-up must be removed.
Walter mixer washout systems were specified by D&C Engineers and are fitted to each Teka mixer. An automatic 12-minute cleaning cycle uses high-pressure water jets to effectively remove concrete residue from all mixing tools after every shift, allowing the mixers to maintain optimal mixing performance.
Dust containment during the mixing process was another challenge facing the team at Hinkley Point C. D&C Engineers specified ConSpare CDX mixer dust extraction systems to filter displaced air and retain cement dust within the mixing process. This creates a safer working environment on each mixer platform and helps prevent waste as all cement is returned directly to the mixer to reduce environmental impact.
As the UK’s leading suppliers of mixer wear parts and batch plant spare parts, ConSpare’s expertise in specifying the right grade of specialist components was essential. Worn mixing tools have a very detrimental effect on mixing efficiency and so wear parts were upgraded to ensure mixing performance was maintained to cope with the high production volumes involved.
It is easy to underestimate the level of logistical support required on site during busy construction phases, but as veterans of similar projects, the ConSpare technical spares team has worked closely with site staff to put in place highly efficient maintenance support systems to ensure the right parts are available on site when they are needed most.
A focus on quality
Another challenge was to ensure the concrete mix formulation was correct. The attention to detail which Bylor used to identify the right raw materials was exceptional and reflects an absolute determination to achieve the highest quality standards. The cement is shipped in from France and each load is quality tested automatically via a cement fill pipe sampling device developed by D&C Engineers.
All the limestone is crushed to a specific grade, then washed and stored on site in 57,000-tonne aggregate bays. All sand is stored in huge weather-protected aggregate storage bays. The strictest of quality controls have been put in place to monitor moisture levels in the raw materials to an accuracy within 0.2%. Hydronix microwave moisture probes are used in every sand bin to continuously monitor moisture and allow batching control systems to compensate for any variation. Additional moisture control probes in each mixer manage the mixing process to ensure accurate homogeneity and to monitor the concrete mix. This essential equipment plays a key role in keeping the mix quality at nuclear standard.
The result
From the outset, the primary goal of the project was to allow the production of the best-possible concrete on a consistent basis. Steve Peterson, ConSpare’s engineering director, said: ‘I’m proud that we were able to contribute and help deliver nuclear concrete from day one, once production started in earnest.
‘What we’ve provided in conjunction with D&C Engineers is a concrete production system that is one of the most accurate facilities of its type in the world; it is safe, efficient, effective and requires minimal maintenance.
‘It was extremely challenging to get right. Many different elements needed to be considered to produce concrete to the quality levels required, and the technology and equipment used to mix and batch it consistently every time had to be the best.
‘We were convinced that we could provide all the equipment needed to create nuclear concrete from one source which, coupled with our experience and innate understanding of the entire concrete production process, meant that we would be able to produce what is probably the finest-grade concrete the industry has ever seen.’
Peter Abel, chief materials engineer at Bylor, said: ‘To do nuclear quality concrete, everything has to pull together, everything must work. How do we deliver it? It’s a one-team approach.
‘The ethos of Team Concrete has set and maintained a high standard of work. There’s a real sense of pride on the plants. The teams really look forward to us coming to site, so they can tell us how their plant is performing, both technically and operationally.
‘The focus and attention to constituents, batching start-up surveillances, continuous feedback and improvement, and overall batching consistency has delivered the best operational batching plant in the UK and also production trends that really set the standard.’
- Subscribe to Quarry Management, the monthly journal for the mineral products industry, to read articles before they appear on Agg-Net.com