Moisture Measurement
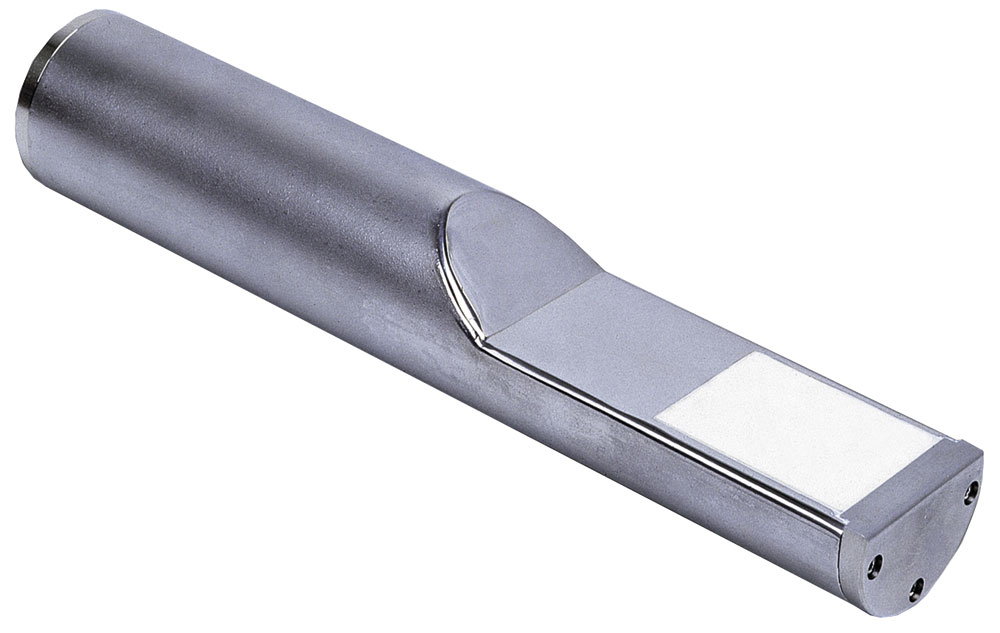
A Technology That Concrete Cannot Do Without
By David Serra, international sales manager for Hydronix Ltd
At a time when most organizations are looking to maximize profits while reining in costs and maintaining quality, it is no longer economical to overlook the benefits that moisture measurement can bring to the manufacturers of concrete, both ready-mixed and precast.
One of the major sources of inconsistency in concrete production is the ever-varying- moisture content of the sand and aggregates. Water content changes can originate from different parts of the concrete production process with differing effects:
- Natural moisture content variation in aggregates.
- Accuracy of water feeding system into the concrete mixer (not usually an issue in modern concrete plants).
- Uncovered material transport or storage systems allow increments of water content by rainfall (or reduction by evaporation).
The most significant source of moisture variation is the natural aggregate moisture content. A variation of 1% moisture content in a dry aggregate by weight results in a 10kg change in aggregate loaded into the mixer for every 1,000kg of dry aggregate weighed. Therefore, the greater the variation in moisture, and the greater the weight of aggregate used, the more serious this condition becomes. Water content in aggregates can be as high as 16%, which has large repercussions for the economics of trading in this material.
As can be seen from the table, the range of moistures which different size aggregates can ‘hold’ as free water, increases with the fineness of the aggregate. Therefore, concrete producers should initially concentrate on measuring moisture in the finest materials.
Options for moisture measurement in concrete production
Today, there are products available in the market that allow measurement of the moisture content of aggregates and fresh concretes with a high degree of accuracy. The microwave technique has emerged as the most suitable for measurement of moisture in concrete production, mainly due to its accuracy (usually in the range of ±0.2%, depending on the quality of the calibration), its lack of influence by dust or colour, and the competitive cost-benefit relationship of this type of equipment.
Measuring moisture in aggregate bins
In ready-mixed concrete, varying moisture content affects both the yield achieved for a given amount of cement and the quality and strength of the concrete. A modern ready-mixed concrete plant would typically install microwave moisture sensors at the gate of the aggregate bins. Once the sensor has been set up correctly, average moisture readings can be taken for each batch. The plant’s control system can then use these values to adjust the ‘wet weights’ of the aggregates to ensure that the correct dry weight of each aggregate is loaded into the mixer. A plant producing 160m3 of concrete would see a payback period for moisture measurement equipment of three months at 3% moisture error, thereafter gaining considerable benefits in both increased yield and improved quality.
For precast and concrete product manufacturers, high-quality materials and well-controlled moisture levels are critical to ensure consistent products. Significant savings in cement, colour and admixtures, as well as reductions in the number of wasted batches, are all common benefits of moisture measurement. As well as installing aggregate bin moisture sensors to ensure aggregate dry weight gradings, precast and concrete product manufacturers generally also opt for a mixer system to ensure the correct total water in the mix, batch after batch.
Measuring moisture in mixers
Measuring the moisture of fresh concrete in a mixer allows the concrete producer to have full control over the final moisture content before the mix is discharged. This ensures that variations due to aggregate wetting/drying during transport from the hopper to the mixer, or variable water pressure are eliminated.
There are two options for moisture measurement in mixers: flush mounted sensors that are fitted to the floor of the concrete mixer, or ‘in-mix’ sensors that either rotate with the mixer arms or remain static in rotating pan mixers. The latest version of the ‘in-mix’ sensor, the Hydro-Probe Orbiter from Hydronix, uses a fully ceramic sensing head unit to offer producers the fastest response available in the market.
The measurements from mixer-floor moisture sensors and in-mix sensors are used to calculate the correct volume of water required to achieve constant water contents inside the mixer, batch after batch.
Homogeneity control using moisture measurement
Using moisture as an indicator of the degree of homogeneity achieved by the concrete mixer at any stage of mixing is also possible using microwave mixer sensors. Based on the use of water as an indicator of material dispersion, when materials are loaded into the mixer the sensors ‘see’ variable moisture contents over time as usually aggregates will be wet and cementitious materials will be dry. As these materials mix with water and admixtures, gradually a flatter trace is achieved as the water disperses evenly over the entire mix. A flat trace output from the mixer sensor indicates that homogeneity has been reached (see graph).
The use of homogeneity control allows the optimization of mix cycles. Once the producer is able to evaluate whether the mix is homogenous or not, the mixing time can be adjusted as required to ensure a homogenous t mix is used. This, in turn, has large benefits in terms of reduced power consumption, reduced wear of parts, and increased production output.
Asphalt and other quarry product applications
In asphalt production, cost savings and quality improvements can also be achieved. Initial correction for dry weight before the aggregate reaches the burners can help to prevent incorrect material gradings and the consequent effect on quality. With too high a moisture content, the bitumen will not bond correctly with the aggregate. Too low, and moisture and fuel will be wasted heating the aggregate to higher temperatures than actually required. Moisture correction optimizes the efficiency of the burners and can, therefore, lead to a reduction in energy costs.
There is increasing pressure on users of quarry products to ensure that their yields are maximized while ensuring their products conform to the required standard. If raw materials delivered by the quarry are of varying moisture contents, in-line measurement allows the control of the exact ‘dry weight’ of material used. Consequently, the next logical step is to associate or compare the final yield to the production costs and purchased materials. With a heightened awareness of both material and energy costs, producers who previously would not have considered moisture measurement or control can now justify this cost-effective investment.
Moisture measurement in concrete production is cost-efficient
As well as improvements in quality, the use of moisture control also allows improved profitability for a concrete production operation. Concrete producers will achieve reduced material costs and increased production yield. Although more difficult to quantify, the reduced number of sub-standard batches, reduced wear parts and energy savings, all increase profitability. The improvement is such that the general consensus among Hydronix customers is that the equipment’s return-on-investment period is between three and six months.
Anyone considering using moisture-control equipment, or wishing to receive further advice, should ensure that they choose a reputable company that is able integrate the equipment with existing production systems and will be able to provide effective customer service and after-sales support.
For further information on the Hydronix range of products, visit: www.hydronix.com