Microwave Sensors for the Concrete Industry
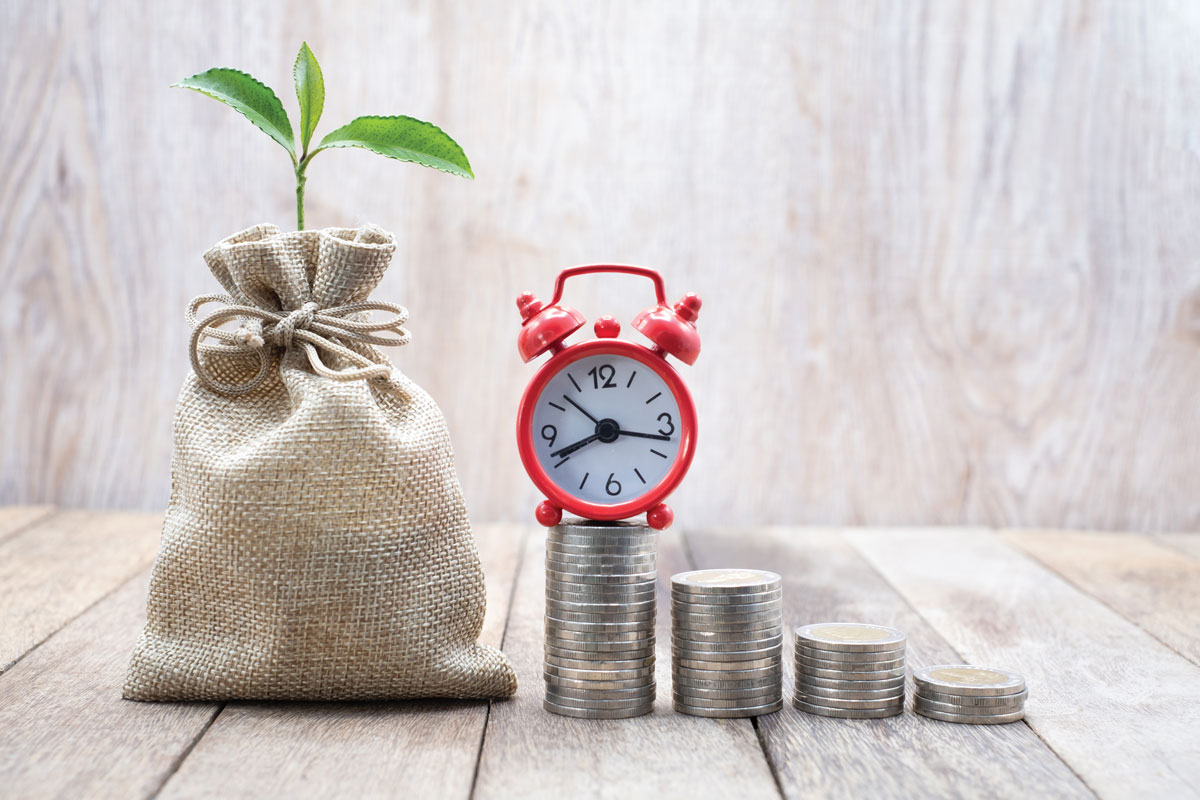
First published in the December 2020 issue of Quarry Management as Moisture Control: Is it worth it?
By Alessandro Mario, technical sales engineer, Hydronix Ltd
Imagine that you could make perfect concrete every batch. How would it feel to save money and time, and to reduce your CO2 footprint and energy consumption without compromises? What would be necessary to achieve this?
Since ancient times, concrete has been the bone that keeps our houses, bridges, cities, and infrastructures standing. Two important aspects of concrete are workability and strength.
In terms of workability, concrete should be easy to place and consolidate, it should be homogeneous, and the ingredients should not separate. Depending on the application and the technology available to place the concrete, different levels of workability are required.
Variations in workability and final strength are very difficult to control as they can be caused by multiple factors such as temperature, grades and proportions of aggregate, water content, admixes, entrained air, cement characteristics, method of delivery and placement.
When designing a concrete structure, one of the most important requirements is the compressive strength. Abrams’ law states that the strength of a concrete mix is inversely related to the water/cement ratio, therefore changes in the water with a fixed quantity of cement will cause variation in the strength.
The making of concrete seems simple, but achieving repeatable results is more complicated.
Whilst workability is determined by slump tests, concrete strength is measured by crushing samples of the batches after seven- or 28-days curing time. The results of these tests are used to adjust the mix design.
To guarantee with certainty that all the concrete manufactured is above the required strength, the BS 206-1:2013 (British Standard) requires concrete manufacturers to overdesign the concrete by 1.48 standard deviations of at least the last 15 strength tests.
To guarantee a lower water/cement ratio, a simple method is to add cement to the mix. Cement, however, is expensive, both economically and environmentally, causing the release of the equivalent of 928kg of CO2 for every 1,000kg of cement produced.
To achieve a stable result, it is important to control and stabilize as many variables as possible during the manufacturing process. Once the mix recipe is defined, it is important to ensure the ingredients are dosed accurately and to control the temperature and moisture.
Temperature influences the workability of the concrete, its curing time and its initial and final strength. For example, a concrete batch set and cast at 10°C has lower early strength and higher later strength, whilst the same mix design set and cast at 32°C has a higher early strength and lower later strength.
It is possible to condition the temperature of the aggregate with refrigerators or steamers and, equally, to regulate the temperature of the water with cooling units or heaters. Cooling the aggregate will lower the water content while steaming will add moisture. Another solution is to use an admix, depending on the temperature of each batch.
Depending on the storage method and the size of the particles, the aggregate can hold up to 18% of its weight in water. Even if temperature conditioning is not used, the moisture in the aggregate can often be deceptive; in normal conditions, after a manual moisture test, it can still have a variation of 1% to 6% in water content during the day.
As aggregates can vary between 1% and 6%, it is possible to take an average example of 2%.
In the batch example shown in table 1, with a small uncompensated variation of moisture in the aggregate, even a very small variation such as a 2% error in moisture of the aggregates can change the ratios of the water/cement and aggregate/cement.
Much more cement would be needed to reach the target water/cement ratio with a simple proportion 360kg x 0.60/0.50 = 434kg of cement or an extra 74kg.
Assuming the cost of cement at £70 per tonne, this would mean an extra £5 per batch on average. Whilst this may seem inconsequential, over 75 batches a day, over 261 working days, adds up to £101,398 per year.
If the aggregate/cement ratio is lower than the design requirements, the workability will also be different to that required by design and could fail the slump test.
By keeping the moisture under control, it is possible to reduce the standard deviation and, consequently, save cement and CO2 by reducing the amount of overdesign.
Moisture test labs are often too slow and not always representative of the variations in the aggregate because of sampling error, so an online method that can measure the moisture of all the material on every batch is best.
Using an online sensor makes it possible to know the moisture in the aggregate. The control system can then measure the wet weight and add the right amount of additional aggregate to compensate for the weight of water; thus, correcting the aggregate/cement ratio.
A second online moisture sensor can be used inside the mixer to accurately control the final amount of water needed for the batch. The sensor in the mixer would also allow precise determination of when the mix reaches perfect homogeneity, allowing optimization of the mixing time to reduce the probability of segregation.
Water content is an indirect measurement, which means the value must be calculated from another measured characteristic. It is necessary, therefore, to keep all the other variables as constant as possible, ie:
- Material composition
- Particles size
- Pressure on the sensor
- Flow speed
- Position of the sensor
For this reason, it is important to calibrate the moisture sensors for each material, only after the system installation. The calibration must be realized by accurate lab tests; calibrating any sensor with another, different, sensor can cause a sum of errors resulting in incorrect calibrations, defeating the initial objective completely.
Independently from the method used in the process, whilst calibrating any sensor, during the lab test it is critical to completely remove moisture from the sample to reach the dry weight, as this is what will be used to define the moisture reported by the moisture sensor.
Many moisture sensors are available on the market and their different technologies can be summarized in five categories, as shown in table 2.
An essential, often overlooked, difference in digital microwave technology is the linearity and stability of the output. Resistive, capacitive, and analogue microwave sensors have a nonlinear output, making them very difficult to calibrate as they require numerous points to design the curve. Nonlinearity also implies low accuracy at the wet and dry end of the scale (fig. 1).
Sensors with a digital measurement technique have a linear output; the sensor reading and water content are directly and proportionally related. This method allows systems to achieve optimal calibration with a few points. In theory, with a linear system it is possible to achieve calibration with only two points.
After these considerations, it is possible to define the ideal requirements of the moisture sensor:
- In line with multiple readings per second, providing quick feedback for the control to adjust on every batch.
- Robust, made with high-quality materials to withstand tough industry conditions.
- Linear output, stable over time, accurate in every condition and easy to calibrate.
- Store multiple calibrations to be used with different materials.
- Ability to measure into the flow of the material.
- Unaffected by dust or colours.
- Unaffected by salt and mineral content.
- Self-contained and easy to integrate into a pre-existing system.
- Low maintenance and cost-effective.
- Able to monitor from any device for full connectivity and remote analysis.
All of the above characteristics can be found in Hydronix microwave sensors with unique digital microwave technology made for the concrete and aggregate industry.
- Subscribe to Quarry Management, the monthly journal for the mineral products industry, to read articles before they appear on Agg-Net.com