Continuous Mercury Monitoring in Cement Kilns
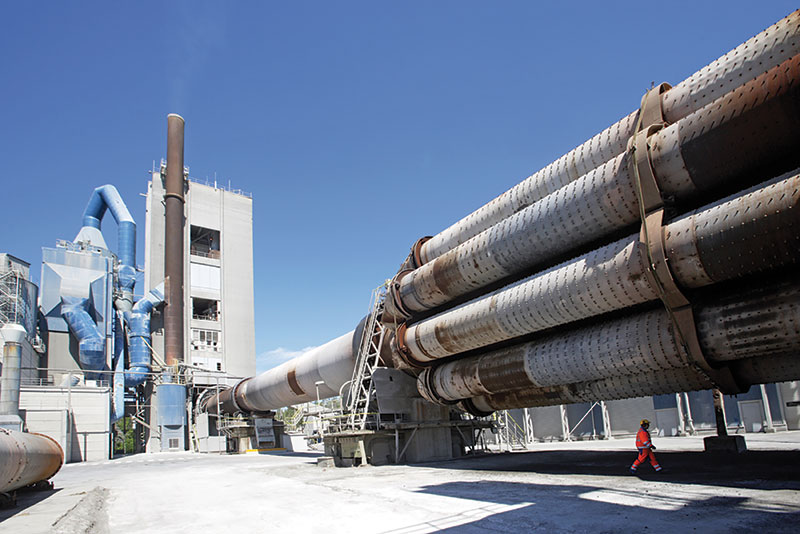
First published in the December 2014 issue of Quarry Management
Antti Heikkilä from Gasmet Technologies highlights the challenges faced when monitoring mercury in cement kilns, and explains how a new continuous mercury monitoring system addresses these issues and provides process operators with an opportunity to improve environmental performance and demonstrate compliance with forthcoming legislation
The production of cement clinker and lime in rotary kilns is responsible for 10.7% of mercury emissions to air (3,337kg), according to a recent study. Most of the mercury and mercury compounds pass through the kiln and preheater; they are only partly adsorbed by the raw gas dust, depending on the temperature of the waste gas. For this reason, monitoring and controlling emissions of mercury to air is important and steps are being taken in several countries to impose emission limits. In the European Union BREF guidance for cement kilns (CLM BREF), mercury has a BAT-associated emission level of 0.05mg/Nm3 (50µg/Nm3) for the half-hour average.
New monitoring technology
Gasmet Technologies, a Finnish manufacturer of emission-monitoring instruments, have launched a new continuous mercury emission-monitoring system (CMM) based on the cold vapour atomic fluorescence (CVAF) measurement principle. The analyser is integrated in an air-conditioned cabinet together with a vacuum pump, an automatic calibrator and a nitrogen gas generator (see fig. 1). The sample gas is extracted from the process duct with a dilution probe and heated sample line specially designed for sampling mercury from harsh process conditions. The analyser has a detection limit of 0.02µg/Nm3 and the lowest measuring range for total mercury concentration is 0–10µg/Nm3 when a dilution rate of 1:50 is used in the sample extraction probe.
Since the CMM analyser employs a CVAF spectrometer, the sensitivity of the instrument is excellent and the main source of measurement uncertainty that needs to be addressed by the analyser and the system design is the quenching effect; this is where other gases present in the sample, such as O2 and H2O, lower the fluorescence signal due to mercury atoms. In order to avoid these adverse effects, a dilution sampling approach is used and the dilution gas is synthetic nitrogen formed in a nitrogen generator inside the analyser cabinet. As the detection limit of the analyser is much lower than would be needed to monitor mercury in low µg/Nm3 ranges, dilution does not compromise the sensitivity of the instrument. On the other hand, dilution lowers the quenching effect by lowering the concentration of interfering gases by a factor of 50. Measuring mercury in a gas consisting of 98% nitrogen guarantees consistent measurement regardless of the fuel or emission-abatement techniques used in the plant.
The CVAF spectrometer measures atomic mercury vapour (Hg0) and in order to measure total mercury, including oxidized forms, a thermal catalytic converter is used to convert all forms of mercury, such as mercury chloride, into atomic mercury. The converter is close-coupled with the fluorescence cell to minimize the risk of recombination reactions where the atomic mercury converts back to oxidized forms between the converter and spectrometer.
The system has been field-tested on various types of industrial plants (coal-fired power plant, hazardous waste incinerator, sulphuric acid plant and a cement plant) to characterize the suitability and long-term stability of the sample probe and dilution system in various processes. Given the reactive nature of mercury, special care has been taken to ensure that mercury in the flue gas is not absorbed into dust accumulating in the sample probe filters. Mercury reacts readily with limestone dust, resulting in analyte loss and increased response time of the analyser. The Gasmet CMM solution includes a smaller filter element, which minimizes the amount of dust deposition on the filter, and a two-stage blowback mechanism which first removes dust from the filter element and then, in the second stage, expels the dust from the probe tube back into the process.
Field test at Finnish cement plant
The CMM was installed on the emission stack of a rotary kiln cement plant with an electrostatic precipitator (ESP) for particulate emission control (see lead image). The test period lasted 30 days. The fuels used during the test included coal, petroleum coke and recovered fuels. The flue gas composition at the measurement point is summarized in table 1. During the field trial, the raw mill was periodically stopped and the variation in mercury levels was monitored together with changes in other process parameters. Average mercury concentration when the raw mill was running was 6–8µg/Nm3, and when the raw mill was stopped the concentrations could increase to 20–40µg/Nm3. The plant had an emission limit value of 50µg/Nm3 for total mercury.
Figure 2 shows a typical 24h period of emissions including raw mill on and raw mill off conditions. In addition to Hg0 concentration, the dust loading and raw mill state are shown because these are the main parameters expected to have an impact on the mercury analyser.
Results
The main goal of the test was to ensure the stability and repeatability of mercury measurement in demanding process conditions and to determine whether cement dust causes analyte loss and increased response time in the sample extraction probe.
The only process variable which clearly correlates with mercury concentration is the raw mill on/off state. When the raw mill is on, the variation in dust loading or other gas concentrations (O2, H2O, acid gases such as SO2 and HCl etc) does not correlate with variation observed in mercury concentration. When the raw mill is switched off, all gases, including mercury, undergo a change in concentration but this is clearly brought about by the raw mill state.
In order to estimate the repeatability of the Hg measurement at zero and span levels, the CMM analyser was configured to perform zero tests with synthetic nitrogen and span tests with Hg0 test gas generated by the mercury calibrator in the CMM system at four-hour intervals. The normal test interval required by the analyser is 24h, but in the interest of creating more test data, the interval was shortened in this test. All test gases were injected into the probe upstream of particle filters so that the test gas had to pass through the potentially contaminated filters.
The results from six repeated span/zero test cycles are shown in figure 3. The target level for the span check was 6.5µg/Nm3 and the average span level was 6.60±0.036µg/Nm3. The average result for the zero check was –0.006±0.036964µg/Nm3. If the dust accumulating in the sample extraction probe were to cause analyte loss during span tests, the later tests would show a decrease from the span check target value, but this was not observed. If the dust in the probe were to make the response time longer (memory effect), the later tests would show a slower response than the first tests. Again, there was no systematic change in the test results and tests 1 to 6 exhibited very consistent results.
The span and zero checks also provided an opportunity to characterize the response time of the analyser when the span test at a known concentration is followed by a zero check with a zero concentration. The data from all six tests in figure 2 were combined together into one dataset in figure 3 by synchronizing the moment when the span/zero check cycle was started. A Boltzmann sigmoidal curve (see equation below) was fitted to the experimental data using GRG non-linear fitting routine in the Microsoft Excel Solver package.
Equation: y(x) = A2 + A1 – A2
1 + e(x-x0/dx)
The parameters of the response curve are summarized in table 2. The response time was evaluated as T90-10, the time interval between a reading representing 90% of the span check value and a reading representing 10% of the span check value. The response time from this calculation was 10.15 minutes or just over two measurement cycles (measurement data is obtained as five-minute rolling averages of the mercury concentration). The live data from the emissions shows peaks of comparable sharpness, but these were not subjected to the same analysis as the span/zero check data.
Summary
The requirements of a continuous mercury monitoring (CMM) system in a cement plant are:
- the capability to measure a low baseline level with high sensitivity when the raw mill is on and the fuel feed contains low levels of metals
- the capability to measure excursions to higher concentrations when the raw mill is off
- low cross-interference from gases, eg SO2
- no analyte loss or other sampling issues in high dust loading
- stable calibration and simplified calibration check routine with built-in calibration gas generator.
Since the main application areas for continuous mercury monitoring systems have been in hazardous and municipal waste incineration, and coal-fired power stations with conditions that are different to cement plants, care must be taken to ensure that the monitoring system, and especially its sample extraction probe, is suitable for the process conditions. This study demonstrates that a CVAF spectrometer and dilution sampling approach can be successfully used in this application.
- Subscribe to Quarry Management, the monthly journal for the mineral products industry, to read articles before they appear on Agg-Net