Block it Out: When recycling is not appropriate
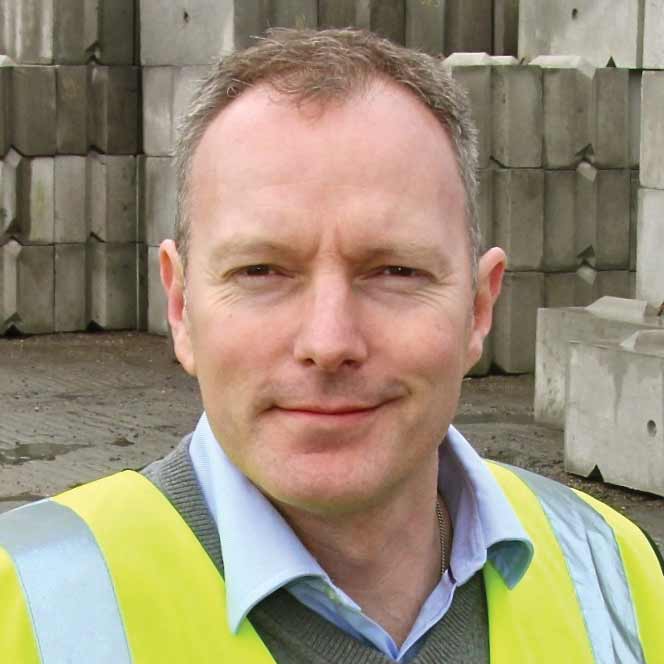
First published in the November 2019 issue of Quarry Management
Owen Batham, sales and marketing director at Elite Precast Concrete, highlights the dangers of using recycled materials in concrete blocks
Recycling is one of the buzz words of the 21st century, with companies in most sectors considering how they can reduce the environmental impact of the work they do. But a ‘one-size-fits-all’ approach where everyone recycles as much as possible is not always the best way forward, especially when it comes to precast concrete.
Around 200 million tonnes of aggregates are used in the UK every year, around 28% of which comes from recycled or secondary sources. Not only do these reused materials appeal to those wanting to be more environmentally conscious, they are also cheaper to produce – a cost saving that can be passed on to the customer.
But while manufacturers look to reduce the proportion of primary aggregates used within concrete production, this must be carefully balanced with the need to produce concrete of a top-level standard. There are many applications in which recycled aggregates can be appropriately used, such as sub-base and fill for road construction projects, but where the strength and durability of the concrete is key to structural integrity, the desire to recycle across the board needs to be weighed against careful consideration of the safety and environmental concerns of such practices.
Take, for example, the use of these materials within interlocking concrete blocks. There is an increasing number of cases where hazardous materials, or aggregates from an unknown source, have been encapsulated into blocks and sold on – with the new owners being none the wiser about what their purchases contain. The production of sub-standard concrete not only has a cost implication for the customer, if the materials have to be replaced within a shorter time frame than would normally be expected, but there could also be a high risk to human life should the inadequate quality control result in crumbling or collapse.
Due to their nature, the origins of recycled aggregates can be very difficult to pinpoint. They can consist of a mixture of brick rubble, glass, plastic and other materials, which impacts their ability to consistently meet the requirements of the British Standards used as guidelines for those working with aggregates. The motivation for some manufacturers to use them is clear; using recycled materials they may already have on site to produce concrete blocks drives down costs. Rather than paying to dispose of their waste, they are reusing it and then being paid for the material when a customer buys the blocks. They are also able to offer their products at a lower price (thanks to the lower production cost), which is why many customers opt to purchase from them.
Research has shown that many blocks do not meet the general concrete standard regulations – something that will no doubt continue if action is not taken imminently. One research source states: ‘The relative proportions of the three main constituents within recycled aggregates (unbound stone, crushed concrete and crushed brick) can vary widely and it is generally assumed that, as a result, the performance of concrete containing recycled aggregates can vary significantly’.
Elements including physical, geometrical and chemical requirements, plus the durability of aggregates, are, of course, included in the BSI guidelines most manufacturers choose to adhere to. Crucially, the BS EN 12620 and BS 8500 regulations make no distinction between primary and recycled materials, and even the BES 6001 guidelines, which make specific mention of sourcing and traceability, have no set guidelines about recycling (except to say there should be no set requirement for more use of recycled aggregates, as this would see materials being transported further if no local materials were available, which would be contrary to any environmental benefits, eg a reduction in carbon footprint).
Given these regulations are essentially optional, conscientious companies will opt to follow them, but there are no sanctions for any firm that chooses to produce blocks which do not meet the minimum testing requirements.
There is an additional concern where blocks are being used to create fire breaks within stacks of waste – those produced from high-quality concrete are, by their nature, Class A1 fire resistant. However, where recycled or organic elements amounting to more than 1% of the overall volume have been used, no such claim can be made. It is imperative that customers buying blocks containing recycled materials are told in no uncertain terms that they cannot be guaranteed as fire resistant.
When it comes to hazardous materials (rather than those simply from an unknown source), there is a loophole which allows companies to reuse them entirely legally. Normally, waste materials must be transported or sold with a waste-transfer note that includes information about whether they are deemed hazardous by the Environment Agency. But if that waste is reused to make a new product, a Court of Appeal OSS end-of-waste test can be applied for and, if granted, means it is no longer defined as waste and such a note is not required.
This effectively gives the green light for companies to take hazardous materials and reuse them in interlocking blocks, without telling customers buying those blocks what is contained within them. Whilst this is dangerous and dubious, it is not illegal.
This is not simply a theoretical concern. The example of leaded glass from cathode ray tube (CRT) screens being exported to the Netherlands, where it was used in concrete blocks that were sold back into the UK in their thousands, shows this practice happens and has been happening for a number of years – and there are many more cases which have not yet caught the attention of the media. Whilst the Environment Agency came under pressure to act after UK companies, including Elite Precast, teamed up to shine a light on the issue, it claimed the process had been ‘properly regulated’ by the Dutch authorities, although it later asked for more evidence to provide reassurance of the quality of the product and restricted import to be done under waste controls.
It was not until three years later, however, that a new Dutch government waste-management plan was implemented, preventing the use of CRT glass in concrete products. In the meantime, there are thousands of blocks that could be anywhere within the UK. While it is maintained they were manufactured to a high standard, because they were not imported as waste materials there is no note associated with them, so when they come to be disposed of there is no record of the fact that they contain CRT glass.
Put simply, there is no way of knowing which of the millions of blocks in existence in the UK have been made and tested using high-quality aggregates that will stand the test of time and are as strong and durable as they need to be. As experts have stated: ‘Discovery of any shortcoming or problem associated with concrete or reinforced concrete structures will become a matter of considerable public concern – both from a safety perspective and associated costs of rectification.’
What can be done about the problem? A real focus on educating both those within the industry, and customers too, would be of benefit to alert more people to the fact there are already sub-standard or potentially hazardous materials within existing concrete blocks. This would also help customers to be more discerning and ask the right questions when purchasing, rather than focusing on cost and assuming the materials will be high quality.
There must also be a wholesale review of the regulations surrounding the use of recycled materials within the concrete industry. Underpinning this would be much more research into the exact consequences of materials that are of an unknown source or were previously classified as harmful waste. This research would allow experts to put in place a set of regulations that would satisfy customers and the industry alike that every block produced or sold into the UK met strength and durability standards and all materials had been properly tested.
Crucially, these regulations must be stringently enforced. There must be a threat of real sanctions being imposed to deter less-conscientious companies who may have little regard for the impact if their blocks were to start crumbling or hazardous materials were to be released into the environment.
In conclusion, recycling as a general principle is to be applauded and the more that can be done to educate everyone about the appropriate use of such materials, the better. But it is clear to those companies that comply with current guidelines that there are also inappropriate ways to use those materials, and the issues of strength and durability must remain of the highest importance.
There would be grave implications if these products were to fail by crumbling or collapsing. In addition, there are environmental implications relating to the end of life when a block containing such materials is set to be disposed of.
More must be done to ensure regulation across the industry and to stop unscrupulous firms making money from risky practices such as encapsulating hazardous waste within concrete blocks. Issues have already arisen, and the longer these practices are allowed to continue, the more wide-reaching these issues become.
Action must be taken now to begin a programme of better enforcement of guidelines and research into the specifics and the impact of unsafe practices, as well as an update of the rules to clarify appropriate use of recycled and hazardous waste within concrete.
- Elite Precast Concrete’s concerns about the future of the industry if action is not taken have led them to commission the independently written white paper: Recycled waste and the UK precast concrete industry. The white paper can be found at: http://bit.ly/elitewhitepaper
Subscribe to Quarry Management, the monthly journal for the mineral products industry, to read articles before they appear on Agg-Net.com