Advances In Concrete Technology
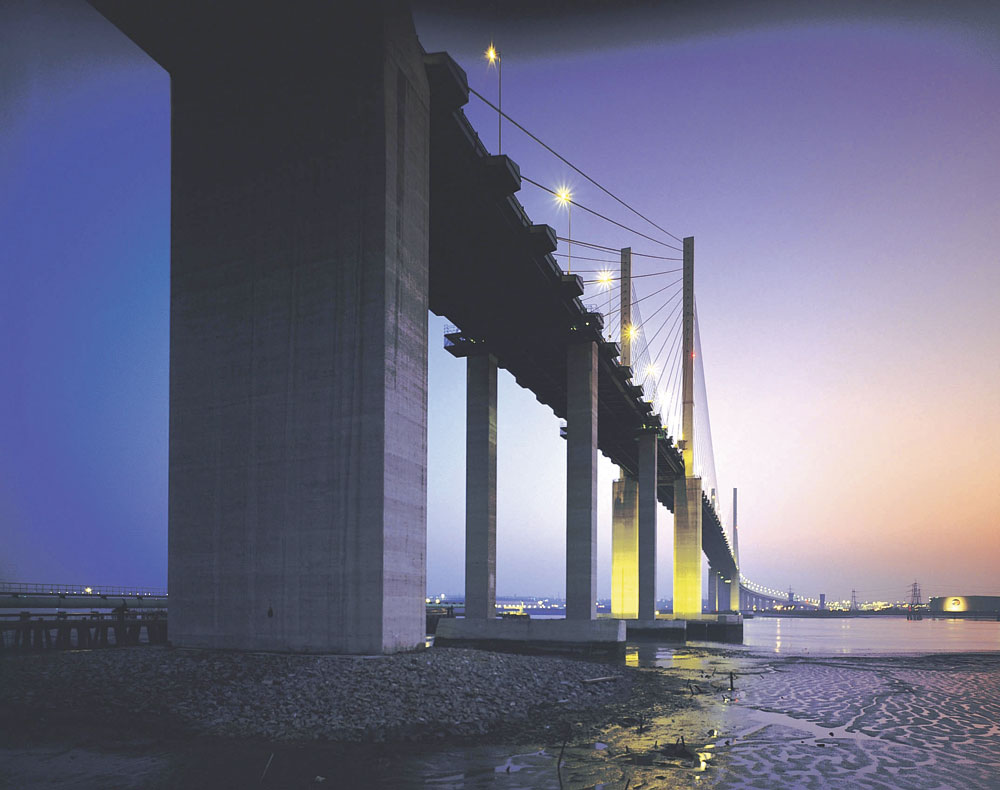
Using Advances in Concrete Technology to Enhance Readymix Solutions
By Steve Crompton, national technical director, CEMEX UK Materials
Ready-mixed concrete was first used almost 100 years ago on a construction site in Baltimore, in the US, and in many developed countries it now accounts for over half of all the cement used in construction. With an estimated worldwide annual output of 4 billion cubic metres, concrete is the most widely used construction material in the world thanks to its unique combination of versatility, economy and durability.
Although the basic concept of the product remains unchanged, today’s concretes bear little resemblance to those first produced in the early part of the 20th century. Remarkable developments in the technology of cementitious materials, mineral additions and admixtures, coupled with advances in production methods, have led to a wide range of high-performance concretes that can provide cost-effective, environmentally sound solutions for the most demanding applications.
Customer requirements, competing technologies and the increasing desire for sustainable construction methods have increased the pressure on the industry to introduce new and innovative ways to meet these demands. The industry has responded by moving innovations in concrete technology from the research laboratory out into the field, and the range of concretes currently available is greater than at any time in the history of the industry.
However, translating research ideas into practice is not straightforward. Scrivener and Kirkpatrick(1) identified three main barriers to the implementation of innovation in the concrete industry:
- Structural safety – The need for a design life of 100 years or more can lead to a conservative approach to the adoption of new ideas to avoid the consequences of failure.
- Empirical knowledge base – The lack of knowledge of the physical and chemical processes which govern the performance of cementitious materials at the macroscopic level, leading to the need for iterative and full-scale testing.
- Market niche and critical mass – The success of concrete as a construction material is largely based on the fact that it is cheap to produce. This is only possible, however, because of economies of scale, particularly in cement production. Smaller-scale niche requirements can rapidly increase costs, negating one of the fundamental benefits of the product.
Despite these barriers to implementation, there have been notable successes in the application of advanced technologies in the ready-mixed concrete industry with developments such as high-strength concrete, fibre-reinforced concrete, the use of self-compacting concrete and the widespread use of high-performance admixtures and additions to modify the properties of concrete.
This paper examines some of the key developments in concrete technology that have led to changes in the design and production of ready-mixed concrete during the last 30 years, and considers some current research which may impact further on the nature of the industry.
CEMENTITIOUS TECHNOLOGY
Advances in cement production technology have led to greater consistency and improved performance of traditional cements. There have been significant developments in the use of alternative fuels that reduce the environmental impact of cement production, which remains an energy-intensive process that, by the very nature of the chemical reactions involved, produces CO2. However, the cement industry has been successful in reducing the amount of CO2 released during manufacture, and the often quoted statistic that each tonne of manufactured cement releases an equivalent weight of CO2 is no longer true, with many manufacturers claiming to have reduced CO2 output by 30% or more.
The last 30 years have seen a dramatic increase in the availability and use of supplementary cementitious materials. In particular, the benefits arising from the following materials has led to their use becoming widespread:
Ground granulated blast-furnace slag
Ground granulated blast-furnace slag (ggbs) is a by-product of the production of iron and is formed when molten blast-furnace slag is rapidly quenched. The cementitious properties of ggbs have long been known (evidence of its first use dates back more than 80 years) and its use is widespread in a number of countries around the world.
It can be interground with cement clinker to produce a factory-blended cement and this approach is common in Europe, although in the UK ggbs is generally added at the concrete mixer to produce an equivalent cement combination.
Typically, ggbs is used to replace 50% of the CEM I component of the mix, although in specialist applications it can be used at replacement levels of up to 90%.
Significant improvements in the resistance to chloride attack are realized when ggbs is used at replacement levels in excess of 40%. Its use also improves the resistance of concrete to sulphate attack and this is recognized in British Standards where the use of high levels of ggbs replacement is encouraged for the most severe chemical-attack categories.
The use of ggbs also reduces the risk of deleterious alkali-silica reaction (ASR), and again this is recognized in national guidance documents which encourage the use of ggbs where there is potential for ASR.
A further benefit of ggbs is the lower heat of hydration, making its use popular in mass structures to reduce issues associated with high temperature development.
Not surprisingly, given the potential benefits of using ggbs, there has been a steady increase in its use in ready-mixed concrete, although there are implications for the producer when using the material:
- A requirement for additional storage capacity.
- Additional quality-control requirements for the increased range of mixes.
- A small increase in cementitious content where an equivalent 28-day strength is required.
- Extended setting time, particularly in cold weather, can lead to increased bleeding, although this can be controlled with the use of admixtures and changes to the mix design.
In general, the use of ggbs presents few problems for the ready-mixed concrete producer and it is the most commonly used supplementary cementitious material in the UK.
Pulverized fuel ash
Pulverized fuel ash (PFA) is a by-product from the generation of electricity in coal-fired power stations, and the pozzolanic reactivity of the material is well documented when used in conjunction with Portland cements.
PFA can be interground with cement clinker to produce a factory-blended cement or it can be added at the concrete mixer to produce an equivalent cement combination. Both methods are commonly used in the UK.
PFA is generally used at lower replacement levels than ggbs, typically around 30%, although higher levels are sometimes used for specific applications.
The use of PFA has been shown to improve the durability of concrete(2) by reducing chloride penetration, improving sulphate resistance and minimizing the risk of deleterious ASR. It can also enhance the fresh properties of concrete with reduced water content leading to less bleeding and improved flow characteristics.
The use of PFA has continued to increase although the cyclical availability of the material has restricted its growth compared with ggbs.
From a ready-mixed concrete perspective, there are some implications when using PFA:
- A requirement for additional storage capacity and a need for enhanced aeration on silos to handle the finer nature of PFA when compared with cement or ggbs.
- Additional quality-control requirements for the increased range of mixes.
- An increase in cementitious content where an equivalent 28-day strength is required. These incremental increases are somewhat larger than those seen with ggbs and can be up to 40kg/m3.
Microsilica
Microsilica is a by-product from the production of silicon and ferrosilicon. It is a very fine, highly reactive, high-SiO2 pozzolan which significantly reduces the porosity of the concrete.
Microsilica is typically used as an addition to enhance the properties of high-performance concretes and is used at addition rates of between 5 and 20% by weight of cement.
Microsilica has been shown to improve durability, abrasion resistance and the strength performance of concrete, but the material is significantly more expensive than cement and its use is largely restricted to specialist applications or high-strength concretes (typically >80N/mm2).
Metakaolin
Metakaolin is manufactured from calcining kaolin at temperatures between 700–900°C to produce a highly reactive pozzolan when mixed with CEM I. It is typically used in a similar way to microsilica, ie as an addition (5–15% by weight of cement) to produce high-performance concrete.
Limited availability and field experience with metakaolin has led to a lower rate of usage than other mineral additions, such as ggbs, PFA and microsilica. However, research data indicates performance levels similar to those seen with microsilica.
Summary
Considerable research and field experience has demonstrated that the use of mineral additions enhances the performance of concrete by improving a number of key properties. This has been recognized in British and European Standards, with designers increasingly specifying the use of such materials. The ready-mixed concrete industry has responded by making such materials widely available and an estimated 75% of all ready-mixed concretes now contain a mineral addition.
ADMIXTURE TECHNOLOGY
Perhaps the most significant advances in concrete technology have been in the field of admixtures, which has permitted the development of a range of high-performance concretes that has allowed designers to fully exploit the benefits of the material. The major admixture companies invest heavily in research and development, and during the last 30 years there has been significant increase in the range of admixtures available to both the cement manufacturer and the ready-mixed concrete producer:
Water-reducing admixtures
These are the most commonly used admixtures, typically added to reduce water content while maintaining workability and thereby reducing the cement content for a given strength.
High-range water reducers
Increasingly used to increase the consistence of concrete while maintaining strength. Arguably, the most significant advances have occurred in this area of admixture technology with the development of polycarboxylate ether (PCE)-based products. These have led to the development of self-compacting concrete and have been critical in the achievement of ever greater concrete strengths. PCE admixtures can be manipulated to modify their impact on important properties of concrete, such as cohesion, rate of strength gain, consistency and slump retention.
Viscosity-modifying agents
Viscosity-modifying agents have been developed to maintain cohesion at very high consistency values and are routinely used in the manufacture of self-compacting concrete.
Grinding aids
Grinding aids that optimize the cement manufacturing process and reduce energy consumption are now commonplace alongside chemicals that enhance the strength performance of cement.
Shrinkage-compensating admixtures
This range of admixtures reduces the inherent shrinkage of concrete, which is an inevitable result of the hydration process. Use of these admixtures is particularly beneficial in the construction of concrete floors, where they permits much wider joint spacing. In conjunction with other technological developments, such as steel fibre, they can even be used to produce ‘jointless’ floors.
Corrosion inhibitors
Additional resistance to the corrosion of reinforcement can be obtained by the incorporation of corrosion inhibitors in the concrete, and such admixtures are often used in critical projects.
Pigments
Pigments come in a wide range of colours and give artistic licence to designers, allowing them to use concrete in many different ways.
Water-proofing admixtures
Pore blockers are increasingly being used in the design and construction of waterproof structures and there is continual development in this area to improve the performance of such admixtures, particularly where concrete is subjected to externally applied water pressure.
The above list is by no means exhaustive and other admixtures, such as retarders and air-entrainers, are routinely used to modify the fresh and hardened properties of concrete.
The benefits of admixtures in increasing durability, improving placing times, reducing costs and improving the sustainability credentials of concrete are widely acknowledged, and the growth in the use of admixtures reflects this with the volume of sales in the UK trebling over the last 15 years, as shown in figure 1.
In the ready-mixed concrete industry, it is now the exception rather than the rule for concrete to be produced without an admixture, and an increasing proportion incorporates high-range water reducing admixtures (HRWRA), which is also reflected in figure 1.
FIBRE TECHNOLOGY
The use of fibres in concrete and mortar is not new, as evidenced by the use of animal fibres in some of the earliest recorded concretes. As with admixtures, there have been significant developments in the type, availability and performance of fibres, and there are three generic types of fibre available in the market:
Steel fibres
Steel fibres are produced in a range of shapes and sizes, and although generally manufactured from mild steel they are available in stainless steel and in galvanized form. They are typically added at dosage rates of between 15–50kg/m3 depending on the type of fibre and desired properties of the concrete.
Steel fibres can increase the toughness and ductility of concrete and are widely used in industrial flooring applications throughout the world. More recently, composite construction techniques have been developed which allow steel fibre to replace traditional structural reinforcement in some applications.
Steel fibre concrete is available from most ready-mixed plants across the UK, although a few days’ notice may be required to ensure that the specified fibre is in stock at the plant. It is essential to ensure that the fibres are fully dispersed in the concrete and it is common for steel-fibre concrete to also include a high-range water-reducing admixture to enhance the consistency of the concrete and facilitate thorough mixing.
Polypropylene fibres
Polypropylene fibres are generally incorporated at much lower dosage rates than steel fibres, typically less than 1kg/m3, and are essentially used to modify the plastic properties of concrete to minimize plastic cracking problems. They also contribute to improved abrasion resistance, enhanced impact resistance and increased spalling resistance in fires.
The use of polypropylene fibres has grown steadily since the 1980s and estimates suggest that over 5% of all ready-mixed concrete in the UK now incorporates such fibres. From a producer’s perspective, the fibres are easy to handle and easy to add to the concrete, although care is required to ensure that the effects on consistency strength are accounted for.
Synthetic macro fibres
Synthetic macro fibres are a more recent development and are generally manufactured from blends of various organic polymers, including polyethylene and polyolefins(3). Recent developments have allowed the manufacture of higher-modulus materials with a variety of anchorage mechanisms that enhance bonding and lead to improved performance of this type of fibre.
Although relatively new to the UK, their reduced dosage rates (typically 2–7kg/m3) make them popular with ready-mixed concrete producers as they can be easier to handle than steel fibres. Their use in applications such as industrial flooring and composite steel decking continues to increase.
Combinations of fibre types can also be used to realize the plastic-state benefits provided by polypropylene fibres coupled with the hardened-state benefits that are associated with the use of steel or synthetic macro fibres.
SUSTAINABILITY
The concept of sustainability has become an important topic in all areas of construction and the production of ready-mixed concrete is no exception(4). Sustainability will become a major driver for the future development of cementitious materials and increasingly companies will be looking to reduce the environmental impact of their products.
Sustainability can be considered to be the combination of social, economic and environmental impacts, and together these influence how a product is viewed. A sustainable material needs to demonstrate:
- Minimal damage to the environment (renewable, non-toxic, recyclable, biodegradable etc).
- Minimal waste associated with its use (waste in manufacture; over-ordering; off-site pre-assembly etc).
- Local supply (if found locally, travel kept to a minimum, reducing harmful fuel emissions).
- Low embodied CO2 emissions (account for all emissions during sourcing, manufacturing and life cycle of a material/product).
In addition, a sustainable material must also be durable, robust, resistant to fire and provide adequate security.
The ready-mixed concrete industry has responded to these challenges by:
Reducing pollution and emissions
- dust emissions cut by 90% over the last 20 years
- 18% reduction in carbon dioxide to air
- 46% reduction in sulphur dioxide
- 17% reduction in oxides of nitrogen
- 60% saving in particulate matter.
Increased use of recycled raw materials
- The UK cement and concrete industry is continuing to contribute to the UK Waste Strategy by consuming waste produced by other industries and recycling its own waste
- The cement industry is playing an important role in minimizing some of the country’s waste-disposal problems by processing selected wastes into alternative kiln fuels
- The use of ggbs and fly ash in concrete and cement is increasing, allowing a reduction in CO2 emissions of up to 45%.
Reduced waste and increased efficiency
- compliance with strict environmental legislation
- ISO 14001 accreditation becoming the norm
- concrete plants now recycle water (up to 65% is achievable)
- across the EU, specific energy consumption in the production of cement clinker has reduced by 30% since the 1970s.
Less reliance on primary minerals
- 1.5 million tonnes of ggbs and fly ash used in UK each year as cementitious replacement
- reduction in CO2 emissions by 1.5 million tonnes
- reduction in primary energy usage by 2,000 million kilowatts per hour
- saving 1.5 million tonnes of quarrying
- saving 1.5 million tonnes of landfill.
Reduced use of primary aggregates
- 45% decrease in the production of primary aggregates from 1989–2011
- 94% increase in use of recycled and secondary aggregates
- By 2011, 30% of aggregates (70 million tonnes) will come from non-primary sources.
The industry is aware of its responsibilities in relation to sustainability issues and continues to invest time, money and resources to further improve its performance in this important area. Although concrete is a small net contributor to global warming, responsible for only 2.6% of UK CO2 emissions in 2006, it continues to promote the use of materials and technologies that will further reduce its impact on society(5).
MIX DESIGN
To make the most of the developments highlighted above requires the concrete technologist to tailor mix designs to meet the requirements of the specifier, and this is highlighted here by considering three applications that have developed as a result of advances in concrete technology:
High-strength concrete
The specified strength of concrete has steadily increased over the last 30 years. During this period average strengths have risen by around 10N/mm2 and an increasing amount of all concrete is specified by strength characteristics.
A more dramatic increase has been seen in the development of high-strength concretes. Whereas C50 was once considered to be high strength, it is now commonplace to see C80 concretes routinely produced and strengths up to C130 have been produced by some ready-mixed concrete plants.
These strengths are only possible by the careful selection and combination of raw materials and the utilization of high-range water-reducing admixtures in combination with selected cementitious components, such as PFA and microsilica. Particle packing theory and the rheological behaviour of the concrete become important parts of the mix-design process in these applications.
The boundaries of high-strength concrete have been pushed further with the development and production of ultra-high-strength concretes, where strengths can exceed 200N/mm2, although to date there is limited application and production of such materials.
Self-compacting concrete
Self-compacting concrete (SCC) has developed rapidly since it was first demonstrated in Japan in the late 1980s. Developments in admixture technology and a better understanding of the rheological characteristics of SCC have allowed producers to reliably produce materials which can be placed without vibration, leading to benefits from increased efficiencies on site, reduced environmental impact and improved surface finish.
However, the design of SCC is complex, often including multiple powder and admixture combinations to ensure that the desired properties are achieved, and further research and development is required to ensure greater robustness of the mix designs.
Designing for sustainability
The use of secondary cementitious components is commonplace in the industry and the use of such materials can reduce the CO2 footprint of concrete by up to 40%.
Water-reducing admixtures are routinely used to reduce water contents and thereby present opportunities to meet specified strength requirements with lower cement contents.
The use of recycled water and the elimination of wash-out waste is now the benchmark in the industry, and larger production units will have reclaimer facilities to recover materials from any returned concrete.
The use of recycled aggregates is often seen as a logical way of reducing the environmental impact of concrete. However, the use of recycled aggregate (RA) or recycled concrete aggregate (RCA) needs careful consideration, as their use can significantly increase the cement content.
Detailed consideration of the overall sustainability benefits of using RA or RCA is required to ensure that the full impact on sustainability is understood, as it is often the case that locally sourced natural aggregate is a more sustainable solution than the importation of recycled materials.
PRODUCTION TECHNOLOGY
The basic requirements for producing concrete are little different today than when the industry was born almost 80 years ago – the homogeneous mixing of cement, aggregates and water to produce a material that can be transported for up to 2h and still be usable at the construction site.
However, the world has changed and developments in cement and concrete technology have led to increasingly complex mixtures requiring ever more sophisticated mixing and control techniques to meet the demands of modern-day construction methods.
Computerization, advances in material measurement and the availability of advanced admixtures allow the ready-mixed concrete producer to design and produce a huge array of complex, technically demanding concretes that were simply unachievable even 10 years ago.
Increasing environmental awareness has driven significant changes to the design of modern concrete production units, with new plants being totally enclosed and no waste ever leaving site as concrete and water recycling units become the norm.
From the outside, a modern concrete production plant may not look very different to those built 60 years ago, but the technology and sophistication of the modern plant and the materials it produces are light years from the first plant built in the UK in 1930.
CONCLUSIONS
The last 30 years have seen many innovations in the field of concrete technology, particularly relating to the development of alternative cementitious components and ever more powerful and flexible admixture systems capable of modifying the fresh and hardened properties of concrete.
More recently, the focus on environmental issues and the concept of sustainability have led to changes in the way that raw materials for concrete production are manufactured and used. There has been an increase in the use of recycled and alternative materials which, together, can reduce the environmental impact of concrete, and further developments in this area are expected.
These developments have been adopted by the ready-mixed concrete industry and the nature of the products produced by the industry has changed significantly. Production units are now more sophisticated, stocking a broader range of cements, admixtures and aggregates that allow the production of a wide range of high-specification concretes engineered to meet the most demanding applications.
REFERENCES
- SCRIVENER, K.L., and R.J. KIRKPATRICK: ‘Innovation in use and research on cementitious material’, Cement and Concrete Research 38 (2008), pp128-136.
- BAMFORTH, P.B.: ‘Enhancing Reinforced Concrete Durability’, Concrete Society Technical Report No. 61, 2004.
- Guidance on the use of macro synthetic-fibre-reinforced concrete, Technical Report No.65, 2007.
- Guidance Document on ‘Sustainable Concrete Design and rating Systems’, British Ready-Mixed Concrete Association, 2008.
- MEYER, C.: ‘The greening of the concrete industry’, Cement and Concrete Composites, 2009.
This paper was presented at the 37th Annual Technical Symposium of the Institute of Concrete Technology (ICT) in April 2009 and subsequently published in the 2009/10 edition of the ICT Yearbook. It is reproduced here by kind permission of the ICT.