Modern Quarry Management: Challenges and Opportunities
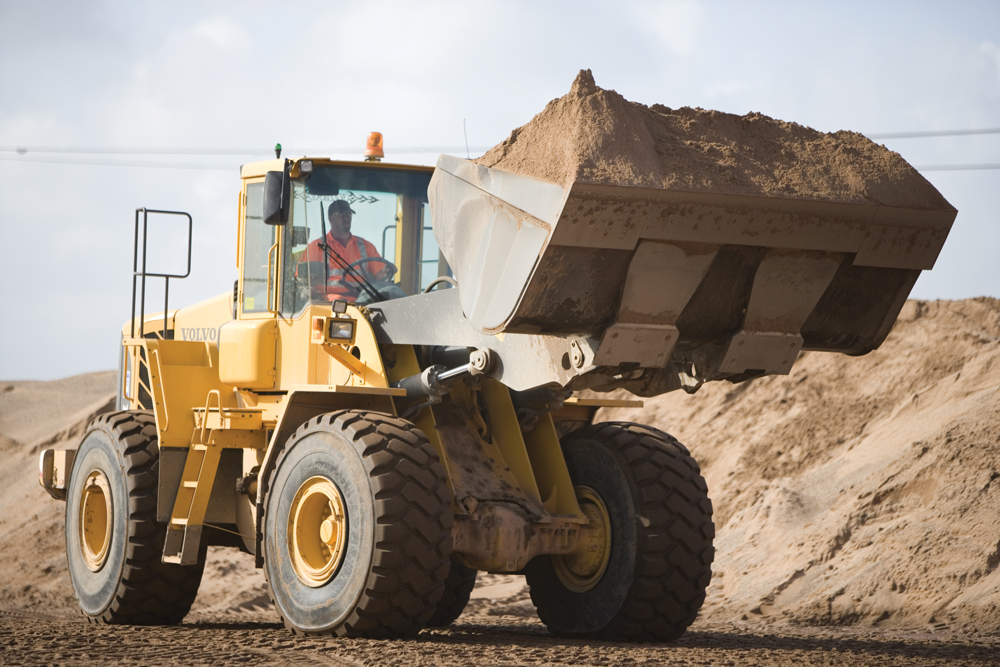
First published in the February 2018 issue of Quarry Management
Quarrying has been an essential part of construction since the dawn of time and in some ways, its guiding principles have been preserved over hundreds of years. However, despite this familiarity, the challenges facing a modern quarry manager are changing. With years of experience and numerous active quarries across the UK, Aggregate Industries are well placed to understand the pressures facing quarry management today. In this article, they report on the challenges, the solutions, and what the future has in store for managers from three different quarries.
In general terms, the key challenges for the modern quarry manager are similar to those faced by previous generations of managers, ie balancing production requirements with the available resources. However, the changing nature of legislation, employment practices and the introduction of technology are all impacting the role.
Some problems are all too common
Today’s quarry manager is more likely to be found at his desk than out on site, according to Matthew Sharpe at Little Paxton, a new Aggregate Industries plant based at a reopened quarry site. ‘There is a wide range of areas covered on sites from operational and safety issues through to local engagement – managers not only need to have an understanding of the topics, but also the time to ensure these issues are attended to. With increasing demand for data and information, more time is spent on a computer, which can sometimes make getting out on site to see what is going on and speak to employees and contractors more difficult.’
Paul Sargent at Aggregate Industries’ Garside Sands, in Leighton Buzzard, echoed this: ‘The ever-changing legislative requirements can sometimes result in a quarry manager being more office based. However, we always look to ensure that we still get to spend time on site so we can see what’s happening on the ground first-hand and engage with our employees and contractors.’
Craig MacMillan, trainee quarry operations manager at Aggregate Industries’ Glensanda operation, in Scotland, is also in agreement whilst commenting on the changing workforce: ‘With a rise in the use of contractor staff at our sites, the challenge comes in trying to manage and provide leadership for these individuals whilst implementing legislative and company requirements which, in some cases, may be new to the contractor.’
Specific challenges require specific solutions
Little Paxton is a quarry that had been postponed for six years and was reopened 18 months ago. The historic workings of quarries in the area had been restored into a nature reserve and there are now several footpaths around, and through, the site. Reopening the site, therefore, raised a number of unusual issues for the team to resolve, one of which was educating walkers who had become used to the free range of the old haul routes and now had to keep to the footpaths. A second challenge was the site’s close proximity to the new nature reserve and the ongoing restoration works. This required the team to work closely with the local liaison groups, especially as the site plays host to several European Protected Species.
Mr Sharpe explained how he and the team resolved the challenges posed by the reopening: ‘Our starting point was building strong relationships with the nature reserve and the landowners. By establishing regular meetings with both parties we were able to create the platform for proactive planning, identifying and preparing for any issues we may encounter. The team at the nature reserve was particularly helpful in making their visitors aware of the importance of using the correct footpaths.’
For Paul Sargent at Garside Sands, it was the age of the quarry that provided some challenges, having to solve the obstaclesnt farmers and our own employees. Each of these groups has specific requirements and by working together in a systematic way we are slowly managing these challenges.’
Progress through technology
While the fundamentals of quarrying remain constant, technological progress is a key part of modern quarry management and at each site it is seen as a key element in improving operations, especially in terms of efficiency.
Mr Sargent commented: ‘We may be behind other sectors, but technology is having an impact on the industry. Many of the crushing and screening methods are still the same, but technology is being applied to them, especially in terms of monitoring and the level of data produced. The key is ensuring we can utilize this data efficiently.’
At Little Paxton, Mr Sharpe feels technology is improving processes as well: ‘It is starting to make a positive impact on modern quarrying, with quarry design, stockpile management software, and newer, more modern, mobile plant technology coming to the site, meaning operations are more productive and better maintained by our suppliers.’
Craig MacMillan added: ‘At Glensanda, we have a condition-monitoring system installed in our fixed plant with a dedicated team utilizing this technology to dramatically reduce unplanned shutdowns of the plant. We are also using a drone, which we have found to be an instrumental tool with various uses, from recording blasts to carrying out inspections.’
Quarry Management: 2050
Increasing use of technology and technological developments are expected to reshape the face of quarry management over the next 30 years, reducing the physical nature of the work. Posed with the question of what the quarry of 2050 would look like, the managers saw technology and reserve depletion as key factors shaping the industry’s future.
Matthew Sharpe believes that many parts of the future can be seen already. ‘Having worked in Australia for four and a half years, I think the modern quarry is already here. Technology has given us mobile plant operations requiring no drivers, modern computer software, larger machines and drones completing quarry surveys and stockpile inspections, as well as daily quarry inspections.’
Paul Sargent added: ‘Personal protective equipment (PPE) will become more than just passive equipment, and will be an aid in the work we do, for instance exoskeleton designs that aid with heavy lifting or shovelling.’
However, there will be a downside to increasing reliance on technology. As remotely operated and then autonomous vehicles come in, there is a feeling that this may lead to a slight decrease in employment, with one operator able to monitor several work vehicles. Mr Sharpe commented: ‘The quarry in 2050 will probably have fewer people operating within it, however while this will be fine where there is predominantly one main source of raw material, where reserves are depleted and operators are trying to maximize remaining reserves, there will always be a need for an experienced quarry manager and support team.’
The need for qualified and experienced quarry managers to deal with decreasing reserves was reiterated by Garside’s Paul Sargent: ‘With natural mineral reserves depleting, there will be more emphasis on making the materials we have available go further, both through recycling and changing construction methods and materials. Adopting and adapting to these changes will be a big challenge for the industry, and will require good leaders and support teams throughout to gain the full benefits.’
Trainee quarry manager Craig MacMillan had the final word: ‘It’s hard to say what the quarry of 2050 will look like. With new technologies being developed all the time, it’s difficult to picture what will be available in 30 years. For us at Glensanda, we want to continue to expand, improve efficiencies, and deliver on our promise of zero harm across our business. There are certainly some interesting times ahead for the industry and I look forward to being a part of it all.’
- Subscribe to Quarry Management, the monthly journal for the mineral products industry, to read articles before they appear on Agg-Net.com