Lafarge Tarmac talk about the challenges and opportunities ahead as a joint-venture company
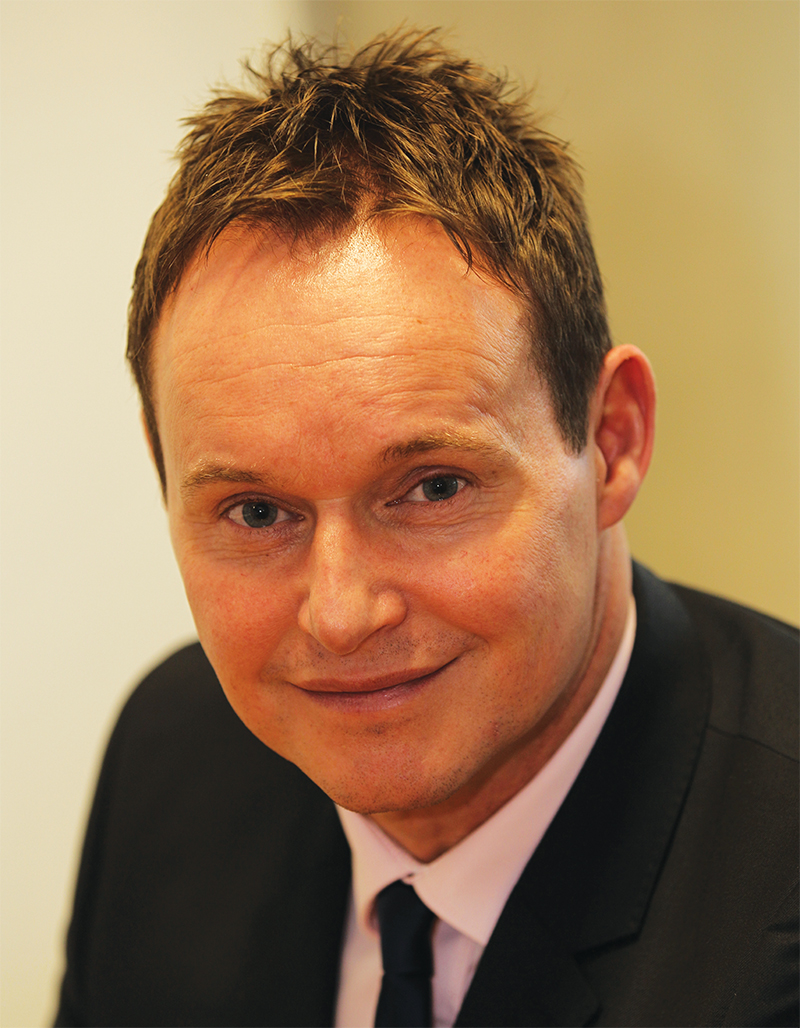
First published in the March 2014 issue of Quarry Management as Leading the Way
After a two-year period of integration and stabilization, Lafarge Tarmac are now moving forward as one joint-venture company. QM spoke to Martin Riley, managing director of the company’s Aggregates & Asphalt division, about the unprecedented challenges and opportunities ahead, and its clear vision to be the first port of call for innovative, value-added sustainable solutions for the construction industry
When the chance arose to interview Martin Riley, managing director of Lafarge Tarmac’s Aggregates & Asphalt division, it was an opportunity just too good to miss.
It’s not that he doesn't like doing interviews, but with a hugely demanding schedule, not to mention responsibility – Mr Riley spearheads a very important part of the UK’s leading construction materials firm – it is safe to say the executive director has a work diary filled with appointments week in week out.
Mr Riley did, however, find time to speak to QM about the major changes taking place at the newly formed company and how it is working in partnership with customers to deliver more sustainable and efficient construction, and working to leave a skills and training legacy by investing to create the next generation of industry talent.
When two become one
The merger of the Tarmac and Lafarge businesses in the UK may have been a significant undertaking, but this should come as no surprise given the size of the portfolio of assets of each company, their combined resources, and the separate legacy products/services that they both had to integrate into one new organization.
From the start, bringing together the strengths of two of the UK’s leading and most influential materials companies – Lafarge (with their strength in cement products, strong focus on R&D and innovation) and Tarmac (with their national footprint and strength in aggregates, road contracting, and strong ethic of customer service) – was always going to be a herculean task.
Lafarge Tarmac, after all, have an annual turnover of almost £2 billion and a strong UK-wide presence with 5,500 dedicated and knowledgeable employees operating at more than 300 active sites across the country.
The integrated company comprises four business units – Aggregates & Asphalt, Readymix, Cement & Lime, and Contracting – that have been strategically structured to complement one another to provide a total construction solution offering for customers.
Lafarge Tarmac are also looking to strengthen their building materials portfolio. As part of its wider growth strategy, the business has plans to acquire Tarmac Building Products (blocks, mortar, bagged aggregates and cement) from Anglo American which would, importantly, increase Lafarge Tarmac’s footprint in fast growing rejuvenated markets such as house building.
Looking ahead, the business has every right to be excited about the future and Mr Riley is clearly enthusiastic about the opportunities for Lafarge Tarmac across their entire operations.
‘This year we can finally operate as a single organization without any distractions from the effects of the merger process,’ said Mr Riley. ‘The amalgamation of two of the UK’s leading players in the building materials market was never going to be a straightforward process. During the integration and stabilization phases we had to maintain customer relations with a ‘best of both’ (Lafarge and Tarmac) approach to continue the legacy businesses’ leadership positions and customer service excellence.
‘On top of this we had to retain workers, hire new people, rebrand the business and monitor the overall performance of the company. It was extremely challenging for everyone involved but a fulfilling part of my job is that we can now move forward at a time when the wider construction industry has started to pick up.’
Supporting UK infrastructure
The Coalition Government’s role in the economy has been key to the recent recovery of the construction sector and Mr Riley, like many of his industry peers, welcomes the Government’s pledge to put UK infrastructure at the heart of the economy with a planned £375 billion pipeline of public and private sectors projects up to 2030 and beyond.
In the context of this brighter outlook for UK construction – which may see a return to the levels last seen in 2007 – Mr Riley has firm views about how these future construction projects will be procured and delivered in the longer term.
‘The Government’s Construction 2025 report (launched last year) has raised some key challenges in the way it has set out far-reaching ambitions on sustainability, efficiency and international growth,’ he explained.
Among the headline targets of the Construction 2025 strategy are: a 33% reduction in both the initial cost of construction and the whole-life costs of assets; a 50% reduction in the overall time from inception to completion for new build/refurbished assets; a 50% reduction in greenhouse gas emissions in the built environment (from a 1990 baseline); and a 50% reduction in the trade gap between total exports and total imports for construction products and materials.
If these recommendations are fully implemented by 2025, it is hoped that UK construction will deliver significant cost savings, faster project delivery and a leaner, greener industry for the benefit of the wider economy.
‘We see Construction 2025 as both a challenge and big opportunity for the company,’ said Mr Riley. ‘As a leader in sustainable construction solutions, we want to use our expertise to help bring these solutions to the marketplace.
‘We fully endorse the industry’s strategy and our aim is to be the customers’ preferred choice for sustainable products – in practice, this means that we want to be who the marketplace turns to when there are problems that no one else can solve, and who can anticipate customer needs and provide value-added solutions – not just supply materials.’
Whether the wider construction industry will meet these targets over the next few years remains to be seen, but if Construction 2025 is to be a real ‘game changer’ for the sector, Mr Riley points out that there needs to be stronger collaboration throughout the whole supply chain and a ‘radical rethink’ of the construction processes, methods and materials used in major infrastructure, such as new highways, housing developments and schools.
‘If you look at the business environment – and what the Government is asking us to deliver as part of the Construction 2025 strategy – I don’t think the wider construction industry will be able to meet these ambitious goals by continuing as it has done in the past,’ warned Mr Riley.
‘To achieve the vision set out in the strategy, everyone in the construction supply chain must strategically work together to remove out-dated and wasteful practices, and deliver a more resource-efficient process that makes best use of materials, water and energy over the life cycle of built assets. Fundamentally, this will require a re-engineering of the construction process, and material suppliers will need to be firmly involved at a project’s conception.’
Mr Riley continued: ‘The main aim is to gain a better understanding of how construction materials will perform in the built environment of the future, and, importantly, how these properties can be further developed and enhanced to help customers achieve their own sustainability ambitions, while supporting the drive to meet government targets.’
Building a sustainable future
Sustainability will be critical to ensuring the delivery of sustainable UK economic growth – and construction products manufacturers and suppliers alike will no doubt play a key part in helping the building industry to operate more sustainably – something that Mr Riley highlights as not only a long-term challenge, but also a strong growth area for the business.
‘A major benefit of the merger between Lafarge and Tarmac has been the amalgamation of the two companies’ trademark products to form an industry-leading array of offerings,’ explained Mr Riley.
‘The founding businesses each have a long and proven legacy of environmentally sustainable performance, products and solutions. And we’ve reflected this new integrated approach and increased product offering by rebranding all the Lafarge Tarmac products and services under the ‘Ultimate’ umbrella brand.’
He continued: ‘We’ve carefully chosen the word ‘Ultimate’ as the new product masterbrand because it represents our ambition to be the best at what we do and encapsulates the way we work with our clients and customers; from understanding their needs and taking a consultative approach to delivering whole-life sustainable solutions that will allow them to reap the full environmental and cost-saving benefits of having a more sustainable built environment.’
Importantly, Mr Riley believes good sustainable practice is about looking at the bigger picture.
‘Sustainability is at the core of our business and we need to set a prime example across the wider construction industry,’ continued Mr Riley. ‘We want our existing and new customers, as well as the subcontractors and suppliers, to see that the whole company works in a truly sustainable manner by addressing the environmental impacts across its operations, from planning and extraction to manufacturing, recycling and transportation.’
In the UK highways sector, reducing the carbon footprint for asphalt production has been a largely overlooked opportunity. Lafarge Tarmac, however, have bucked the trend and identified a new, innovative, low-energy method of building roads that will be open to the industry.
The company – in partnership with the Carbon Trust – has recently announced the findings of a three-year study to improve carbon efficiency in the manufacture of ‘low-temperature asphalt’ (LTA), which has the potential to save the industry £46.2 million in energy costs over the next 10 years, as well as reduce carbon emissions by up to 39%. It will also assist in cutting the environmental impact of road congestion and slow-moving traffic, as well as reducing project timescales, as LTA can be driven upon sooner than traditional hot asphalts.
The pioneering project allows mixing and working at lower temperatures, yet bonds road materials as effectively as conventional production methods.
Lafarge Tarmac are also leading the way in the use of recycled and secondary aggregates. They have, for example, worked rigorously with their customers to increase industry uptake of recycled asphalt planings (RAP), which has seen the company divert 350,000 tonnes of waste from landfill, reduce 3,000 tonnes of CO2 and, significantly, further reduce its reliance on oil-based materials.
It has been widely accepted by the quarrying industry that rail can often have an environmental edge over roads, and Mr Riley said the Aggregates & Asphalt division, along with the other business units, will be making extensive use of the national rail network by working closely with rail freight operators, Network Rail and the Government, to maximize the opportunities to transport more products by rail each year.
‘From an environmental point of view, we often see rail freight as a better alternative than road transport,’ said Mr Riley. ‘Supply chain efficiency is also becoming ever more critical as our customers continually strive to enhance their logistics and to reduce escalating costs. With the proposed High Speed 2 rail network, which will, importantly, provide the UK’s railways with increased capacity, better connectivity and quicker journeys, we hope to transport more aggregates by rail.’
Skills for the future
One of the biggest challenges facing the construction industry is addressing an alarming skills gap, with more than 400,000 workers set to leave in the next 5-10 years, according to the Construction Industrial Training Board (CITB).
The mineral products, extractives and processing sectors also face a similar skills shortfall. Mr Riley believes now is the time to change the way the construction products industry is viewed, to make it a more aspirational career choice for young people, and to invest in the necessary training to up-skill the existing workforce.
‘We need to attract new talent and incentivize careers in quarrying,’ he said. ‘More qualification-led training, graduate trainee schemes and apprenticeships have, therefore, become increasingly important to help tackle the skills shortages in the industry. We also need to improve the image of the wider construction industry and make it an aspirational career choice for more young people.’
Lafarge Tarmac clearly value employees as their most important assets, and the company’s strong commitment to staff training/education, development and recruitment will ensure it has a fully competent workforce to meet the growing needs of customers as market demand picks up.
As a former industry apprentice himself, it comes as no surprise to learn that Mr Riley is fully supportive of the company taking on new apprentices and delivering long-term training, with many being offered further opportunities to build upon these skills.
‘Apprenticeships are about showing a real interest in young people and nurturing them to develop their skills, knowledge and talent,’ commented Mr Riley. ‘We currently have an active apprenticeship scheme in place that will see the recruitment of 60 or more apprentices, 25 graduates and five university placement students annually. Within my part of business, we’ll also be taking on an additional 10 higher apprentices and training them at the University of Derby, so they achieve qualifications while also receiving practical experience through working for us.’
With competence playing a key role in sustaining the health and safety standards of the industry, Lafarge Tarmac are fully behind the MPQC’s suite of competence-based training courses and industry-specific QCF qualifications (at all levels).
The firm is also an advocate of the Institute of Quarrying’s PRIME (Professional Recognition in Mineral Extractives) project, which has been designed to give all employees the benefits of tailored CPD and professional recognition of their skills and the contribution each person makes to the success of the business in which he or she works.
Safety focus
With a strong focus on health and safety, and continuous training firmly rooted in Mr Riley’s agenda, Lafarge Tarmac’s Aggregates & Asphalt division is clearly working hard to meet the industry’s ‘Zero Harm’ targets and create a sustainable safe working environment for the benefit of all employees (and visitors).
‘Safety is something that you can never stop working on,’ explained Mr Riley. ‘As a new company, we’ve had the chance to look at best practices from the legacy businesses and from outside our industry, and we are implementing them in Lafarge Tarmac.
‘For example, we’ve just launched a ban on using hands-free mobile phones across the company, as we saw an opportunity to reduce risk. Before launching this we took time to work through it with our teams to ensure successful implementation and to make sure that it would not impact our customers.
‘We’re also rolling out a programme of training and development to support safety. This is based on key analysis of risk areas, incident reviews and near misses. But, of course, staff training and rigorous safety management systems and procedures do not always empower employees and contractors in the proactive management of health and safety.
‘What is most important is worker involvement, and my team and I spend a significant amount of time visiting sites and coaching supervisors to ensure we have a strong safety culture embedded across the organization with the right behaviours and mind-sets.’
The message from Mr Riley is that everyone in the workforce has a key part to play in achieving health and safety best practice: first, by delivering their personal responsibilities; and, secondly, by looking out for themselves and their colleagues.
‘Employees need to be aware of their responsibilities and take ownership of their behaviours and actions,’ continued Mr Riley. ‘This requires the involvement of everyone in health and safety discussions and improving safety standards. This is key in establishing a safety-conscious culture across the wider aggregates industry and ensures the safety and well-being of everyone within our organization.’
Mr Riley also emphasized how the industry, as a whole, can play a pivotal role in improving the health and safety performance throughout the supply chain by being actively open and sharing good management practices.
‘We need to build on the competence and operational best practice that has already been achieved in the aggregates sector and set an example for other manufacturing industries to follow,’ he said.
As UK construction takes a huge leap forward in operating in a more sustainable manner, evolving client expectations mean that building materials companies need to keep up with changes and take a sustainable approach to helping customers manage their projects more efficiently, provide a safer and more productive site, reduce costs and demonstrate how they are managing their environmental performance.
Lafarge Tarmac’s operational excellence, improved logistics and extended portfolio of value-added products/services across a wider geographic area puts them in a perfect position to meet the sustainability needs of the future.
But as Mr Riley stressed, a more holistic approach – which takes full account of the supply chain – will be key to ensuring a sustainable UK built environment is delivered. Lafarge Tarmac will be leading the way forward in sustainable construction to help ensure this vision becomes a reality.
- Subscribe to Quarry Management, the monthly journal for the mineral products industry, to read articles before they appear on Agg-Net