First anniversary of Hope Construction Materials
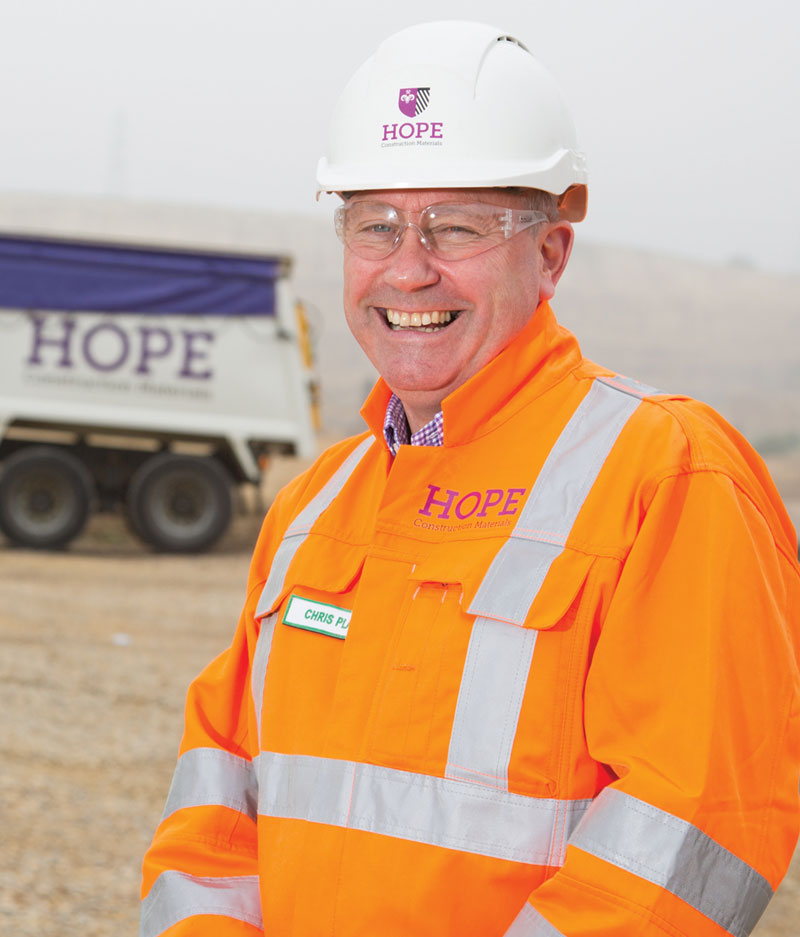
First published in the January 2014 issue of Quarry Management as A New Beginning
Hope Construction Materials, the UK’s largest independent supplier of building materials, mark their first anniversary this month. QM spoke to Chris Plant, chief executive officer, about the major challenges that the company has had to overcome in the last 12 months – and the different approach it is taking to meet the needs of the construction industry
When Hope Construction Materials officially opened for business in January 2013 following the acquisition by Mittal Investments of more than 180 former Lafarge and Tarmac facilities, Hope became the first major new name in the UK building materials sector for more than a decade.
The company bills itself as ‘Britain’s leading independent construction materials supplier’ – and rightly so. The materials firm has around 800 employees, plus 400 contract drivers, and operates 156 ready-mixed concrete plants, several aggregates operations (quarries, rail terminals and a marine wharf), two asphalt plants and four cement facilities, including the UK’s largest cement works at Hope, in Derbyshire, which lent its name to the new firm.
One year on
Celebrating the company’s first year in business, Chris Plant, chief executive officer of Hope Construction Materials, has good reason to be optimistic about the future. As the UK moves out of recession and the construction sector slowly returns to sustained growth, he sees this as an ideal opportunity for the materials firm to become an even ‘stronger competitor’ in the marketplace.
But a year ago it was a completely different story for the newly formed business. When Mr Plant was appointed as chief executive officer, his first task was to set in motion a three-phase development programme of mobilization, stabilization and optimization.
‘Starting a breakaway business in the time and with the resources we had was one of the most challenging tasks I have ever encountered,’ recalled Mr Plant. ‘As part of the mobilization stage, we had to meet existing staff and recruit new staff, set up management and operations systems, and begin the task of replacing two legacy IT platform with our own high-tech communications infrastructure.’
Of the company’s 800-strong workforce, some 200 highly motivated and ambitious former Lafarge and Tarmac employees actively sought to join Hope, creating a dynamic team that Mr Plant describes as ‘entrepreneurial self-starters’ and ‘best of the best’. The remaining 600 or so employees were transferred to Hope under the Transfer of Undertakings (Protection of Employment) Regulations (TUPE).
‘During the staffing process we wanted individuals who were enthused by the prospect of establishing a brand new business,’ he explained. ‘Equally important, we looked for candidates with multidisciplinary skills and backgrounds, and ‘T-shaped’ professionals, ie persons who not only hold a thorough knowledge and strong skill-set in one area, but can also work beyond their specialist expertise to collaborate in numerous other disciplines or fields.
‘If we are going to fulfil our strategic objectives and compete in the market, we must ensure that our workforce has the necessary skills, experience and competence to take on greater responsibilities when opportunities arise. I strongly believe a key factor to our future success, and the impact we make with our customers, will be the wide ranging points of view, expertise and creativity Hope employees can offer.’
Creating a strong brand identity
One of the key components of any brand is the corporate logo, and Hope – in conjunction with award-winning design agency FutureBrand – have rolled out a striking ‘shield’ logo designed to represent the pride and heritage of the industry, and the location of two of the company’s biggest assets – Hope Cement Works and Dowlow Quarry – in Derbyshire.
‘The shield is more than just a logo; around 20% of Hope’s workforce is based in Derbyshire so it was important we incorporated a ram and pair of pick axes to make a historical reference to the region,’ said Mr Plant. ‘On the right hand side of the shield, the black bar at the top represents the asphalt side of the business, while the black diagonals reflect the way concrete is depicted in architectural drawings. All in all, it’s a logo that we are very proud of and one that I am confident will stand the test of time.’
When asked about Hope’s corporate colour (purple), Mr Plant pointed out it was company chairman Amit Bhatia’s decision to go with something that is ‘fresh, different and stands out from the crowd’.
Mr Plant explained: ‘We want to be an innovative and dynamic company, and having ‘purple’ as our corporate colour reflects the company’s sheer determination to bring something refreshing and unique to the construction industry.’
The most important brand identity, however, was a recognition by the management board to put Hope’s core values at the heart of the business. ‘We are all very passionate about our company values and a lot of thought, time and effort has gone into communicating these strategic objectives to customers, local communities and stakeholders,’ enthused Mr Plant.
As part of the branding development, interviews were held with Hope employees and customers to carefully observe the aspirations and expectations of a new company in the construction materials sector. This, subsequently, helped Hope and FutureBrand to identify four strong company values: reliable; understanding; entrepreneurial; and responsible.
‘These core values underpin everything we do,’ said Mr Plant. ‘Being reliable is about understanding the importance of meeting customer expectations and producing high-quality products on a consistent basis.
‘But it is not just about supplying construction materials; we are also very keen on establishing close working relationships with our customers and seeing things from their perspective. We are actively seeking and analyzing client feedback and taking appropriate actions that will benefit them – and that is where understanding and entrepreneurial come into play.’
An example of Hope’s ‘entrepreneurial’ approach to business is highlighted in how Hope are bringing the operation of a new multi-million pound fleet of Caterpillar machines in house through a strategic alliance with Finning.
There is now a growing trend among construction materials suppliers, not least Hope, to be forward-thinking and innovative in their approach to sustainability and delivering energy cost savings. The company, for example, is increasingly focusing its attention on environmental management, sustainable transportation methods, renewable energy supplies and supply chain efficiency.
‘As a responsible, efficient materials supplier, we clearly want to make a positive impact on the environment and take responsibility for our actions,’ commented Mr Plant.
‘Any measures which can be taken to improve efficiency and reduce carbon emissions are fully embraced. For example, around 60% of the cement produced at Hope works is transported by rail. We’ve also looked at how we can manage our heavy plant fleet more efficiently by reducing fuel consumption, which, in turn, will minimize our CO2 footprint and save running costs.
‘Another important focus for us is to work closely with our partners (in the supply chain) and customers to develop sustainable solutions that can help meet their green agendas and improve their overall environmental performance.’
Workforce engagement
Hope are fully committed to health and safety improvements and, like many other mineral operators, have invested in staff training and rigorous safety management systems and procedures.
But to maintain good health and safety management, Mr Plant believes it is vitally important for operators to focus on new ways of getting their staff more involved with the overall process of workplace safety.
‘For me, it’s all about behavioural safety,’ he explained. ‘Worker participation requires a strong commitment from companies to encourage their employees to take ownership of health and safety, and to challenge them on how they are undertaking work activities. It is important to ensure that visible felt leadership is integrated at all levels of the business and promote the development of an interdependent team safety culture.’
Indeed, Mr Plant is no stranger to raising health and safety standards. Before taking on the CEO role at Hope, he was vice-president of health and safety for Lafarge’s Aggregates & Concrete Division worldwide, where for two years he ‘preached’ the principles of strong safety management leadership combined with active worker participation to his international peers.
Prior to this Mr Plant, a chartered civil engineer, was managing director of Lafarge UK's asphalt and surfacing businesses, overseeing some of the country’s biggest highway and airport runway schemes. During his tenure, he also helped the UK division achieve world-class health and safety performance status.
Mr Plant went on to explain that the creation of a strong safety culture had been fundamental to this success. ‘It doesn’t matter if a company has the best safety equipment on site or management procedures in place, the key contributing factor in maintaining a good health and safety performance level is changing the mindset of employees,’ he said. ‘I’m a strong believer in promoting the need for responsible personal behaviour throughout the whole workforce.’
Mr Plant is also a great believer in developing a fully trained and competent workforce. With skills shortages on the horizon across the mineral products, extractives and processing industries, the company has quickly responded with the recruitment of five apprentices at Hope cement works as well as a number of others at its laboratories and quarries, with further apprenticeships planned at other sites.
Booming business
With Hope up and running, and the stabilization of the business completed (from January 2013 to October 2013), Mr Plant, like all directors, has now set his sights even higher.
‘We’re now in the optimization phase, which involves identifying growth opportunities and developing a longer-term strategic approach to the business,’ he said. ‘I’m hopeful this will strengthen our position in the market and, in line with the UK construction recovery, allow us to operate more commercially.’
Assisting in this process, the company’s seven-strong management team also comprises: Amit Bhatia, chairman; Dallas Taylor, chief finance officer; Mike Cowell, managing director - cement; Simon Phillips, managing director - concrete, aggregates and asphalt; Jim Verity, human resources; and James Stirk, legal director.
The company’s aggregates, asphalt and concrete operations are divided into three main regions: north; central; and south, while the cement division is managed nationally, with four distribution depots covering the South East, Midlands and north of England.
The organizational structure has been designed to strengthen product orientation and meet local customer needs (sales, distribution and technical advice), as Mr Plant explained: ‘It is important we position the company for long-term success in what is already a highly competitive marketplace, and our structure and high-quality services strongly focus on customer relations and logistics performance.’
Since its inception, the materials firm has produced and delivered in excess of 4 million tonnes of aggregates, more than 2 million m3 of ready-mixed concrete and over a million tonnes of cement.
Mr Plant now wants to take Hope to the next level and has projected that over the next three years the company will refine its fiscal performance, resulting in significantly higher sales than the company’s current £300 million annual turnover.
‘Although 2013 was a pretty good year, this year we can actually start to move the business forward without any influence from the effects of the Lafarge Tarmac merger,’ he continued.
‘With our ambitious and innovative growth plans, the next goal for the company is obviously to expand as we look to refine our footprint in the construction products market.’
Mr Plant also believes there is a need for Hope to embrace advanced technologies and be pioneering, bringing new ideas, solutions and working practices to the table. The company, for example, will have an enhanced IT platform integrated into its system that will provide a reliable, single point of contact for all purchasing and customer-related services, including invoicing.
‘Our chairman, Amit, is a highly successful entrepreneur who operates in the fast-paced technological world,’ commented Mr Plant. ‘One of the key components in formulating the business model with Amit was the benefit of embracing new technology solutions into the firm and leveraging that technology to work for us. This is a good example of the exceptional value he brings to the firm.’
Hope are clearly a dynamic organization with a strong commitment to redefining services provided in the minerals processing industry. The company’s client-focused approach, aspirations and long-term goals will continue to strengthen its position as the UK’s leading independent supplier of construction materials.
Mr Plant concluded: ‘I’m relishing the challenges ahead, particularly maintaining the quality ethos of the company and staff, and further improving our product offering. This is an exciting time for everyone involved in the business – and a clear indication of our huge ambition.’
- Subscribe to Quarry Management, the monthly journal for the mineral products industry, to read articles before they appear on Agg-Net