Plant Reporting
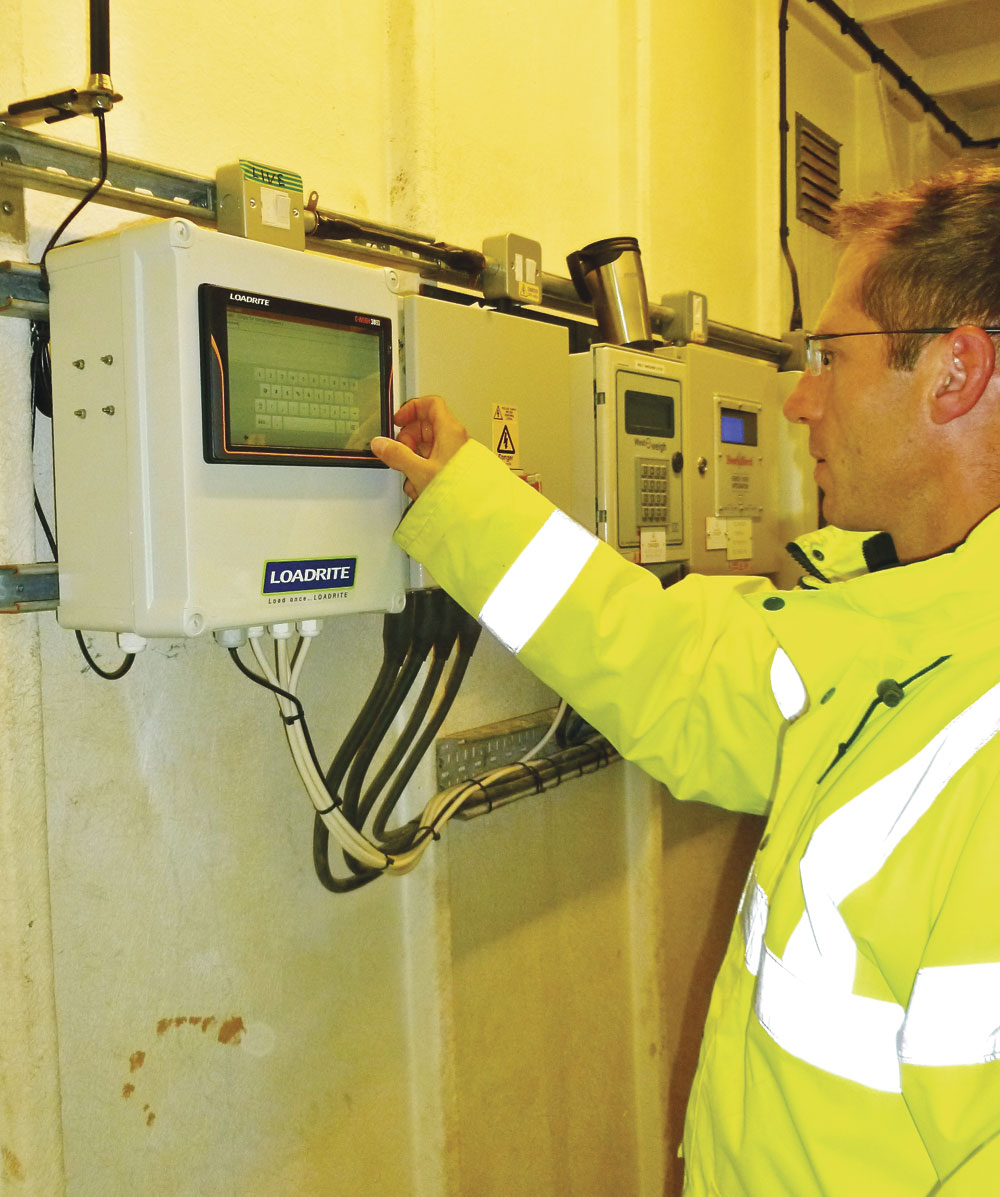
Know exactly what your plant is producing with Loadrite’s C-Series belt-scale reporting solutions
The need to control costs to a finite degree in the mineral extraction industry has never been more important. With rising fuel costs, parts and labour charges and extremely tight margins, any cost savings which can be applied to a particular area of a company’s business model cannot be ignored. Whether the cost savings are implemented by streamlining manufacturing techniques and production processes, a reduction in staff and overheads or the replacement of plant and machinery with more economical modern equipment, it is these large, high-value, high-cost areas that often see investment or swingeing cuts. While these areas need to be kept under control, in respect of running costs there are other facets of the mineral extraction industry where things may be overlooked, costs are incurred on a regular basis, regular breakdowns occur and maintenance budgets are exceeded.
Whatever the mineral operation is, operators will undoubtedly use one or more conveyor systems, and while many operations will keep their conveyors in good working order and believe them to be working to their full capacity at all times, Loadrite, through their UK dealer Halomec, have recently brought to the market an innovative package to accurately monitor conveyor productivity, downtime and reliability.
With more than 30 years of weighing experience and rigorous testing behind it, the Loadrite range incorporates excavator and wheel loader on-board weighing systems and has recently been expanded with the C-Series conveyor weighing system.
The Loadrite C-Series provides performance information that can help quarry managers to optimize their equipment utilization, resulting in more tonnes per hour, lower energy consumption and extended performance of wear parts, ultimately reducing costs and increasing production. Not only does the system enhance the ability to monitor the equipment and, therefore, help identify unused capacity, it also allows real-time tracking of the actual production from certain areas of the plant, such as crushers and screens, and will also give managers the ability to track material movements to stockpiles and monitor loads leaving the site via truck, port or rail.
The C-Series is designed to work as a stand-alone system with as little as one scale, right through to multinational companies using multiple conveyor systems across a number of sites. Such is the flexibility of the system and its associated software, that a glance at a computer screen can reveal the tonnage of a certain product at a facility on the other side of the country.
Equipment such as mobile crushers and screens are easily retrofitted with the Loadrite C-Series, allowing accurate figures to be compiled of the actual output of the mobile plant. Easy to fit and simple to maintain and calibrate, the system is coupled to an easy-to-read printer with the ability to either store information in a web-based system or have it available directly via email. With static plants, the C-Series, when fitted directly after the primary crusher, allows the monitoring of tonnes per hour, total tonnage and average tonnes per hour of material passing through the crusher. The C-Series also allows managers to see the time that the conveyor starts and stops, as well as the time of the first and last loads of the working shift.
The Loadrite system is also able to monitor and report on times when the conveyor is running partially loaded or empty. This facility is particularly useful as an aid for the plant manager in redeploying machinery to maintain a steady flow of material entering the primary crusher. Additionally, placing a scale on the final product belts allows managers to track inventory of crucial products as well as identifying waste and leak points. The full power of the C-Series system is evident when fitted throughout the quarry's production system. Throughput of primary, secondary and tertiary crushing systems can be monitored along with the effectiveness of screening and washing plants. Measurement of weights, downtime and performance of multiple belts allows for accurate production planning to meet sales forecasts and, therefore, reduce waste.
While the technology behind Loadrite C-Series is evident in the amount of data able to be gathered and monitored, it is the simplicity of the installation which makes it an attractive proposition for those in the extraction industry looking not only to cut production costs, but to increase productivity without increasing day-to-day running costs. An agile range of scale assemblies and speed sensors, tailored to fit specific conveyor systems, measures vertical forces sending an accurate weight signal to the C-Weigh 1850 integrator.
Two versions of the scale assemblies are available: the F12 with a capacity of between 30 and 2,500 tonnes/h and a belt speed of up to 4m/s; and the F3 with a capacity of up to 5,000 tonnes/h. Both scale frames are available to fit conveyors from 400mm up to 1,800mm in width and on an incline of ±30°. Manufactured from zinc-passivated steel for the frames and aluminium for the load-cells, the scale assemblies have an overload capacity of 150%, ensuring the product can withstand even the harshest of conditions, and are also rated for operation in temperatures as low as –20° Celsius and up to 60° Celsius.
A speed sensor provides a signal to the integrator for the calculation of the belt speed, flow rate and total weight of materials passing through the system. The C-Weigh 1850 integrator is the system’s processor, turning the signals from the load-cells and speed sensors into weighing data and displaying total weight, running rate and belt speeds in both metric and standard measurements. The C-Series integrator provides near real-time viewing for operatives on the quarry floor, allowing them to make timely decisions based on the information received.
On a site with multiple conveyors, the integrators, however may there are, are linked to the C-Weigh 3860. Specifically designed for the quarry control room, the C-Weigh 3680 monitors all live production figures, plant availability and utilization, and key performance indicators remotely on one display, allowing the control room operator to react faster to changes in the production process. Machine downtime can be remotely monitored with specific coded reasons set up within the system to identify causes of inefficient plant performance. The control room operator is able to view the current production status or review production figures for the previous 24h, and can also zero and clear the whole system remotely from the one device.
Although tailored to the Loadrite system, the C-Weigh 3860 can also be configured to work seamlessly with any third-party belt scale with a 4–20mA and pulsed output. This feature makes the C-Weigh 3860 a suitable integration tool for connecting to existing conveyor belt scales.
Weighing and plant efficiency data can be sent directly from the C-Weigh 3860 to INSIGHT, Loadrite’s web-based plant reporting software, without being redirected through any other computer. Producers can also track ‘black belt’ time, calculated when the plant is running but not producing, and keep tabs on downtime. Immediate access to this information means companies can properly assess their procedures and confirm the impact of their operational changes.