New Control System For Day Group IBA Plant
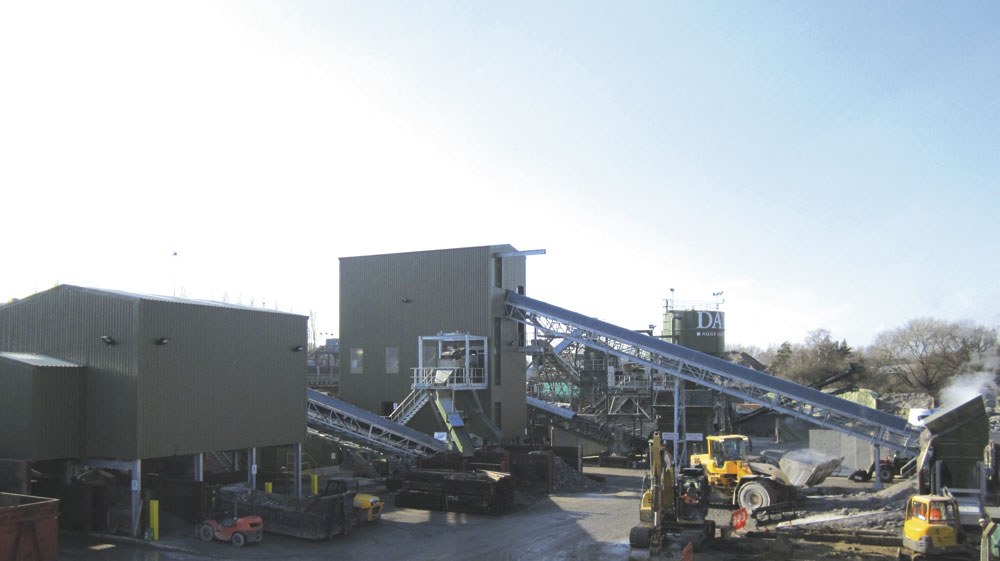
Axon Power & Control help install advanced control system at Day Group’s Brentford Works
Axon Power & Control have been one of the most trusted providers of electrical engineering and control system solutions to the industrial and materials handling sectors in the UK and Ireland for almost three decades.
The company works with its customers to provide turnkey solutions from early stage design through to build, installation and final commissioning. In addition to these services, Axon Power & Control offer full after-sales maintenance, inspection and testing services.
Recently, in conjunction with the LJH Group, Axon Power & Control were contracted to design and install the control systems automation for an incinerator bottom ash (IBA) processing plant for Day Group at their Brentford works.
The project comprised the design and build of the plant motor control panel, the plant electrical services installation, including power factor correction equipment, and final testing and commissioning of the installed equipment in conjunction with LJH engineers.
The plant automation was specifically designed to incorporate all aspects of the plant control in one central control system; from this location the operator can monitor the running of the complete plant and all ancillary equipment.
At the heart of the control system is a Schneider Electric PLC system, which relays information from ancillary panels, such as those controlling the eddy-current separator equipment, electromagnets and belt weighers, and transfers this information to the PLC. These data are then converted and displayed as operator friendly information on the human-machine interface (HMI) display terminal.
The layout and functionality of the display terminal was designed to maximize ease of use and productivity. The terminal allows the operator to see the status of the plant graphically at a glance, with more detailed information available as necessary.
In order to more accurately control plant throughput, the belt weigher was integrated with the PLC system, thus allowing instantaneous and accurate feed-rate control via the set point, as determined by the operator. The production rate can be viewed in real time on the display terminal, or the information can be viewed via the historical trend graph, which plots actual productivity against the operator set point.
All of the information gathered regarding tonnes per hour, motor current, plant alarms etc are logged to a removable USB pen drive. This information can then be transferred to a PC where the customer can create a record of the plant’s performance with minimum effort.
The trend graphs can easily be viewed using standard spreadsheet software, allowing the plant manager to effortlessly scan through the production records. Similarly, alarm logs can also be viewed in a spreadsheet or table format showing the time, date and the nature of the alarm condition.
For more information about Axon Power & Control services, contact: shannon.montague@axon-online.com; or visit: www.axon-online.com