Automated Data Capture, Reporting and Analytical Tools Help Support the Quarry of the Future
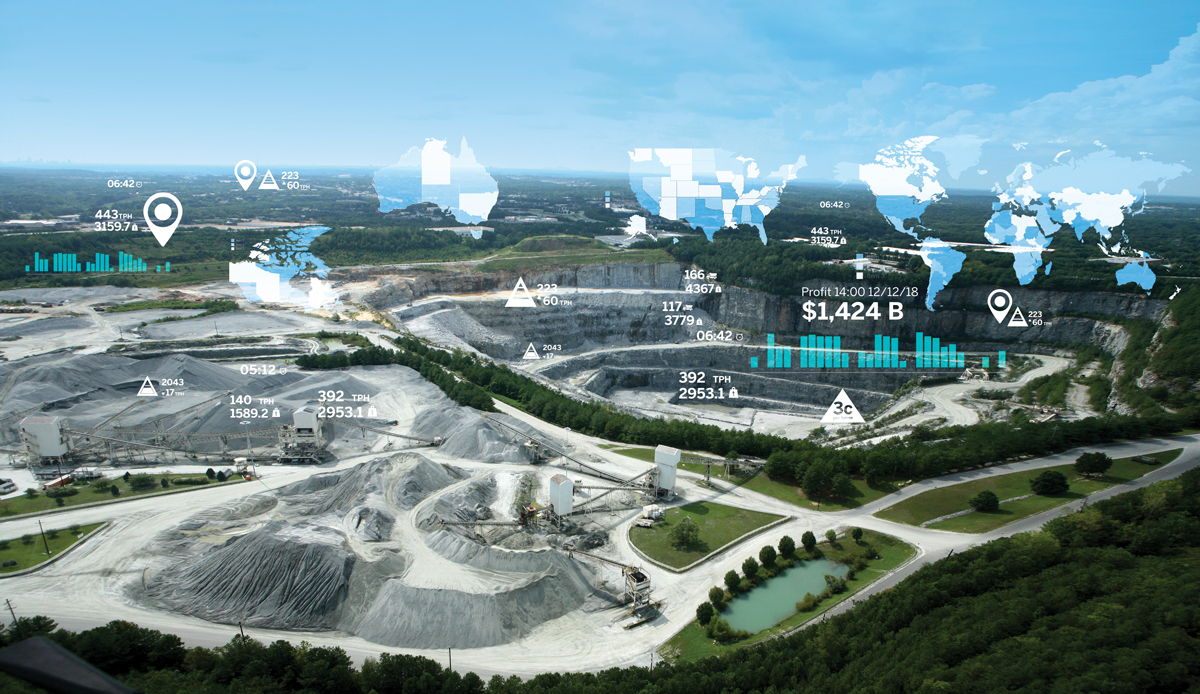
First published in the August 2019 issue of Quarry Management as Seeing the Bigger Picture
How automated data capture using network-connected devices, web-based reporting and advanced analytical tools is driving improvements across aggregates operations
Today’s aggregates executives have much to keep them up at night. Like most business leaders, the pressure to maximize returns while decreasing overheads is constant. But executives in the aggregates industry also face increasing pressure to improve operational efficiency, sustainability and safety performance, while maintaining a competitive advantage and exploring new revenue streams. Add to that the desire to make technology decisions that can help drive improved efficiency and cost performance, and it is a wonder these decision-makers have any time for rest.
With so many priorities to juggle, how do quarry executives lead their teams and operations into the future? What levers can they pull to make significant productivity improvements, enhance transparency across the business to reduce waste, and optimize operations?
Fortunately, a fresh perspective on operations management and advancements in quarry technologies is transforming the aggregates industry. A combination of automated data capture using network-connected devices and web-based reporting and analytics tools will help support the quarry of the future. These technologies give quarry owners, chief executives, chief operating officers etc (ie, C-level executives) greater visibility across extraction, processing and load-out as well enhanced transparency for smarter inventory planning and forecasting.
Advanced analytics and reporting tools are also providing deeper insights into processes across the organization by looking at current data compared with historical data and forecasts or targets. With an understanding of what is happening within their quarries and accurate forecast data, leaders will have the ability to better plan production over various time horizons, to closely track productivity and performance across their entire operation, and to drive organizational change in new and exciting ways.
Some readers may already have heard the following wise words from business management guru Peter Drucker: ‘If you can’t measure it, you can’t improve it’. It all comes down to the fact that if you cannot measure something, and know the results, it is very difficult to achieve sustainable improvement. The good news is, measuring outcomes in quarry operations is easier than ever before with the proliferation of the Internet of Things (IoT) and network-connected devices.
Today, automated capture and measurement technologies are the foundation of the connected quarry and the quarry of the future because they can very accurately measure data and share that information in near real time. This includes onboard loader scales to measure payload, belt scales that record production, haul truck monitors to optimize the haul cycle and other tools that track production activity to optimize material movement.
Improvements to asset- and fleet-management technology also make it efficient to track everything from high-valued powered equipment, to towed and non-powered assets, to fleet vehicles. With this detailed information, managers have access to detailed activity reports that can help the business better manage asset performance and costs.
Another example is the Trimble load and haul management connected solution that automates data capture of the extraction work process using the Loadrite X2350 excavator scale to record pit extraction tonnage and measure load cycles, while Trimble’s H2250 haul truck monitor tracks truck fleet and material movement. The integrated solution eliminates the need for paper tally sheets and automatically counts, records and breaks down haul truck cycles. These capabilities remove the chance of human error and keep operators focused on safe and productive materials movement. It also improves safety and maintenance needs by monitoring speed and tyre pressure, capturing hours of operation, and providing payload measurements.
Automated data capture
Loader scales, belt scales and fleet and asset solutions are critical building blocks for efficient and productive quarry operations. These interconnected sensors and smart scales make it possible to deliver visibility across operations. Managers can then measure actual production versus sales forecasts and share that analysis with regional managers and executives further up the chain. Using this information, they can then identify potentially costly bottlenecks, find areas for improvement and identify opportunities to apply best practices for running more efficiently.
‘In the connected quarry, we rely on automatic data capture as the first step to measurement and increasing visibility across operations,’ said Johan Smet, general manager of Trimble’s aggregates division. ‘By removing the human element of monitoring, we remove the burden of error-prone manual data collection and tedious transcribing and tallying. These capabilities give executives insight to answer critical questions about operations because they see what’s happening at a granular and aggregated level. This gives them greater visibility, transparency, and error-free and timely data to make smarter decisions.’
Various questions – eg ‘How much downtime did we have last quarter? Are we maximizing margins? Are we maximizing sales? Are we minimizing inventory and write-offs? Are we reducing safety risks and controlling overloading to prevent community complaints? – can be answered by leveraging automated data-capture tools, such as Loadrite’s weighing systems, and pulling that data into a centralized database, such as InsightHQ, for systematic reporting and analysis.
‘Answers to all of the most important questions start to come into focus with automated data capture as the foundation,’ said Mr Smet. ‘Gathering data you can trust, without the hassle of chasing down multiple reports from multiple locations, is the first step toward making better business decisions.’
Using the data
The next phase is putting systematic processes in place to work out what to do with the information that has been collected. What may have worked in the past, such as relying on spreadsheets or home-grown systems, is no longer adequate to manage these large or complex data sets.
The key is relying on powerful, more agile reporting and management tools that can aggregate data collected across the manufacturing operation to provide a complete 360o operational view. Cloud-based applications that can compile data collected across the enterprise from crushers, loaders, excavators and trucks give managers and executives an accurate and detailed understanding of their processes. Web-based management tools are ideal because they can be accessed anywhere with an Internet connection and on any mobile device. With productivity, availability and performance metrics about extraction, processing and load-out functions at their fingertips, managers have the detailed information they need to make smarter day-to-day decisions. Moreover, executives have a high-level, 360o view of operations along with the ability to dive deeper into specific quarry data when needed.
‘Imagine all of the data from across 12 sites that make up a region being aggregated into one number or a couple of numbers,’ said Kevin Vonesh, worldwide strategic accounts manager for Trimble Loadrite. ‘Having the ability to drill down into a report to see if there was a metric in the red, and drilling down further and seeing there’s a plant with its main crusher down – that’s what C-level executives need to see to make effective change happen.’
Web-based reporting tools such as Trimble’s InsightHQ are helping teams to meet these challenges. InsightHQ allows users to identify issues and respond much more quickly than reporting that relies on manual processes and generally shows a narrow view of individual metrics.
‘We see many C-level executives who are disconnected because the information is not readily available and accessible, and often not reliable,’ said Mr Vonesh. ‘What we’re doing with InsightHQ is providing ease of use and the ability to see that information and use that data in the day-to-day decisions of running the organization.’
Real-time data
The advantage of continuous monitoring and access to real-time data is that performance and optimization provide immediate feedback. For instance, ongoing analysis and insight is much more valuable than a once-a-month reporting exercise that includes data about total tonnage, operating rate, or what products are being produced. With comprehensive web-based tools, executives can log into their management portal to see live reports about key processes and sub-processes across the business, with very accurate measurements broken out by machine, product and customer. Users can then look deeper to investigate load-out obstacles, or they can view changes over time, adjust reports for individual quarries and regions, or by shift, day, week, month or year. Greater access to real-time data across quarry operations will continue to give leaders the ability to respond to issues much more quickly and to optimize productivity, availability and performance of their assets.
‘By making the information about operations much more accessible via a cloud-based model, executives can quickly see efficiencies achieved with belt scales, loader scales, excavator scales, or haul truck scales, which all adds up to saving the business money,’ said Mr Vonesh.
With a better understanding of the operating parameters, thanks to intelligent data collection and smarter data analysis, executives can quickly see how changes to capacity will impact other phases of operation.
Smaller quarries, big insight
With smaller quarry operations there is even greater pressure on operators to keep costs in check and maintain transparency across the site.
‘In Europe, especially, we see smaller quarries in tighter concentration, because aggregate is very expensive to transport across long distances,’ said Patrick Gruber, strategic accounts manager for Trimble Loadrite in Europe and the Middle East. ‘When competition is intense, leaders have to make pricing decisions quickly while making sure costs are under control. Detailed monitoring of daily production, stock-on-hand and forecasting is critical. Access to this data ensures operators produce the right product at the right time to meet demand.’
Prioritizing improvements
Greater transparency gives executives the ability to make informed decisions that can help quarry operations reach new levels of productivity and efficiency. Executives may determine, for example, that a site may benefit from fewer but higher-capacity trucks to transport maximum throughput. Other quarries may benefit from adding additional smaller trucks and the increased flexibility in capacity that brings to react to demand fluctuations. In every case, being able to see the impact from a change in one area of the quarry on overall production will improve decision-making.
In each scenario, C-level executives are responsible for identifying productivity improvements made possible through investments, supporting a trial and rolling out the change throughout the operation. For example, teams may determine a bottleneck in load-out and re-evaluate their scale house processes. By rolling out Trimble’s Loadrite 360 application, for example, companies can transform the process to safely speed-up truck cycle times through the weighbridge to improve customer service. Loadrite 360 connects the loader and scale house to provide data sharing of load-out jobs. Essentially, jobs are automatically sent to the loader operator, so they know precisely what products and what weight each truck requires, before it arrives at the stockpile. This holistically improves the load-out operation and safety through performance metric tracking, automation and real-time job visibility. Not only that, Loadrite 360 reduces the need for manual data entry, which improves operator job satisfaction and reduces errors.
‘These technologies give executives the breadth and depth they need to drive improvements across every aspect of the business – from the pit to the gate, from the chief executive officer to the operator,’ said Patrick Gruber. ‘If load-out is identified as a bottleneck, tools such as Loadrite 360 can improve it, with further improvement down the supply chain.
‘Loadrite 360 empowers the operator because they can finalize the load with a click on the scale, the data is automatically sent into the management portal, and the job is closed. Reports are then made accessible via the cloud. This means the truck doesn’t even have to go back on the weighbridge before leaving the quarry. This saves time and is safer because drivers are not leaving their truck cab, and by making load-out smoother, you can load trucks faster.
‘These tools empower teams to be more productive through automation, accurate measurement and reporting. Plus, when teams have access to accurate data at a granular level and at a high level, they can make smarter decisions.’
‘Outside the gate’ planning
In addition to managing internal operations, quarry executives have to have a constant eye on balancing their cash flow and managing financial performance across multiple individual quarries. This is challenging when orders are continually changing and manual, spreadsheet-driven reporting cannot keep pace. Moerover, building a forecast report that shows materials demand in different time intervals is an incredibly tedious process.
Today, however, automated data-capture technologies and cloud-based reporting systems such as Trimble’s PlantDemand, are changing that. PlantDemand provides managers with a ‘single source of truth’ when it comes to aggregate, asphalt and concrete production and inventory planning and forecasting (see QM, Sept 2018). With real-time information, managers can adjust plant, hours, modes and sales and can see how these changes will impact current production and future orders. C-level executives can then solve multi-site inventory issues far in advance before a customer experiences a problem.
‘Improved planning technologies make it possible to fine-tune production to market needs, maximizing the output of desired products and minimizing the output of by-products,’ said Johan Smet. ‘This analysis can all be done by looking at the real capability constraints of the plant. Whether this leads to a more diverse product portfolio depends on the range of market needs, but it will certainly lead to a portfolio that better matches those needs and improves overall profitability.’
Attracting talent
Technology is also helping C-level executives to keep pace with a changing workforce. When aggregate and construction professionals retire, it puts pressure on organizations to fill the skills gap and bring young professionals into the business. Leveraging technology innovations and automating many of the manual tasks across quarries will help attract the next generation of quarry professionals who have grown up using technology and are ‘digital natives’. With continuous monitoring and a single system to view and report on quarry production and inventory information, individual employees and managers will be more engaged, better equipped and, therefore, more successful. Moreover, C-level executives can establish a culture of success and innovation built upon real data, empowerment, greater accountability and communication.
‘Technology helps shorten the learning curve across almost every business, and people like to work with new technology,’ said Kevin Vonesh. ‘You can’t teach 20 years of experience in two weeks, but you can explain to new employees how to interpret what the system is reporting and help teams benchmark themselves against targets and use those targets to improve. Teams want to do a good job and technology can help by automating some of those mundane tasks, and they’ll learn things, so they can keep their skills current.’
- Subscribe to Quarry Management, the monthly journal for the mineral products industry, to read articles before they appear on Agg-Net.com