Total Innovation
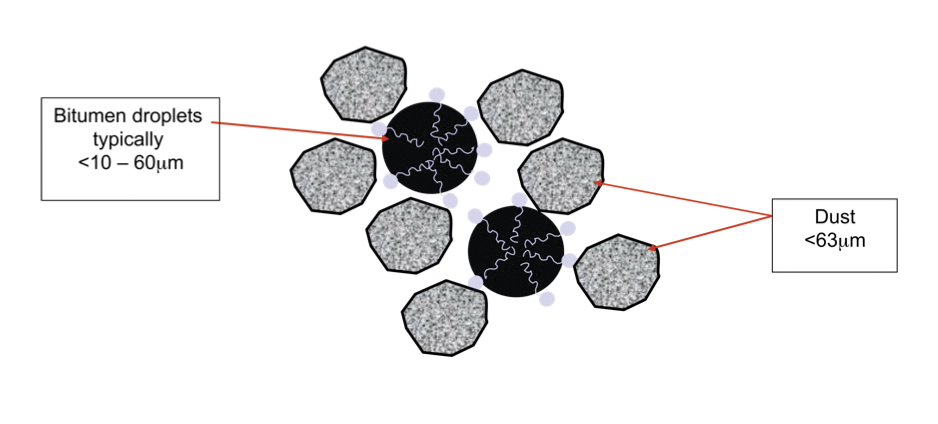
How technical innovations from Total Bitumen are delivering practical and successful solutions
Following the introduction of Total’s new Styrelf range, the product’s profile has been raised to a new level in the UK, leading to an increased client awareness of its technical benefits. Likewise, trials with Azalt Eco2 have provided Total’s customer base with ‘ready-to-use’ lower-temperature bitumen which has equivalent in-situ performance levels to that of hot mix.
In addition to Styrelf and Azalt Eco2, however, Total’s range of emulsions has just as much to offer the asphalt sector in terms of innovation and sustainability in today’s challenging physical and commercial environment. The following are just two examples of innovation that have led to practical and effective solutions for use in the maintenance programme:
- Emulsis MG – for cold-mix recycling.
- Total Chip Clean – an innovative bitumen emulsion for binding dust away from stone aggregate surfaces.
Emulsis MG
Used in a UK-designed cold-mix process, Emulsis MG (Mixing Grade) emulsion has been developed to accept up to 100% recycled aggregate of varying chemical nature. Emulsis MG’s primary function is in base and binder course applications with future development aimed at surface course solutions too.
A key benefit of Emulsis MG is the ability to stockpile the mixed asphalt. The material can be designed to gain strength at varying rates and, dependent on design requirements, QVE or SVE material can be produced.
Moreover, Emulsis MG has the potential to reinstate tar arisings without the need for foaming or special handling requirements, as it is mixed by conventional cold-mix asphalt plant.
Total Chip Clean
Users of conventional cold-mix emulsion technologies within the road surfacing industry will be aware that adherence to careful design criteria is key to its success. If such criteria are not adhered to, problems relating to poor coating of the large aggregate sizes within the matrix can occur.
Deviations from design include:
- too many fines within the aggregate matrix
- not enough bitumen emulsion added
- emulsion chemistry incompatible with aggregate chemistry
- insufficient water within the mixture.
In a cold-mix asphalt or surface dressing, poor coating of the large aggregate particles can create a material with poor mechanical properties and poor visual appearance.
By using Total Bitumen’s Chip Clean process, the problematic fine particles (<65µm) coating the larger aggregate sizes react with the bitumen in the emulsion and are bound together to create discrete bitumen-bound particles that no longer interfere with adhesion.
The larger aggregate particles are, therefore, effectively cleaned of dust, making what might otherwise be regarded as waste stone aggregate, suitable for use again in a road application. This innovative process applies a specially formulated emulsion in order to remove the dust from the surface of the larger aggregate particles without coating them. The resultant material can then be stockpiled ready for recycling into asphalts or surface dressings.
This simple process can be applied in situ to clean surface dressing sweepings, thus reducing the carbon footprint involved in transporting the material to cleaning plants. Furthermore, it generates minimal waste as the dust particles become an inherent part of the chipping mix and the water evaporates. It can also be used on virgin chippings, where washing can often prove to be problematic.
Application
Screening
The aggregates, whether virgin or recycled, must first be screened into the nominal aggregate size for subsequent use.
Mixing
A simple mobile cold-mix plant is used to produce the treated aggregate. The aggregate is fed into a mixer along with the emulsion plus any additional water that may be required. Residence time within the mixer is less than 10s, as care has to be taken to ensure the material is not over-mixed. This reduces the possibility of aggregate abrasion leading to the generation of further dust particles.
On mixing with the dusty aggregate, the emulsion disperses evenly throughout the mixture and reacts with the surface of the aggregate dust, breaking and then adhering to the dust surface.
Under mechanical action and during relaxation on the stockpile, the coalescence of the bitumen binds the dust aggregate particles together into larger particle conglomerates. These larger particles become distinct entities separate from the large aggregate particles. This dissociation has the resultant effect of cleaning dust from the surface of the large aggregate particles.
Careful control of the bitumen/fines ratio and emulsion design ensures success in this process (see figure 1).
Performance
More than 4,000 tonnes of recycled aggregates have been treated and used in surface-dressing operations in the UK to date. All sites have been monitored with the following observations.
- No aggregate loss experienced over cold winter months.
- Excellent adhesivity of the surface dressing to the aggregate exhibited (essential for successful surface dressings).
Conclusions
The use of a bitumen emulsion to bind together dust particulates away from an aggregate surface has proved to be a successful technical solution for utilizing an otherwise waste aggregate in surface dressing operations.
The application of the process has environmental benefits for the user as aggregate can be reused at the site location rather than having to transport virgin aggregate over potentially large distances.
When utilizing recycled aggregates such as previously reclaimed chippings swept from newly installed surface dressings, Chip Clean offers commercial benefits as the user does not need to purchase as much high-value virgin aggregate.
Moreover, as the amount of emulsion used is very small (typically around 1.0%w/w, depending on dust content), the cost of the process is far outweighed by the cost of bringing new primary aggregate from a quarry.
These two examples of innovation leading to commercial success in the emulsion field, characterize Total Bitumen’s approach to understanding market needs and understanding their products.