The Way Ahead
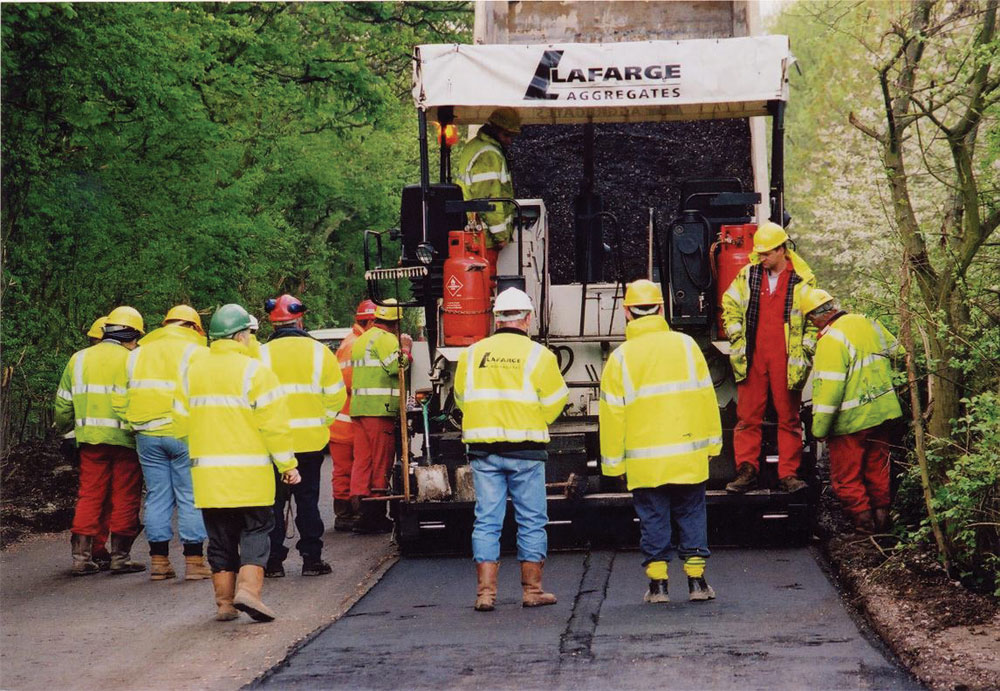
Environmental asphalt — WAM-Foam
In recent years the asphalt industry has seen significant interest in manufacturing asphalt at lower temperatures. Advances in technology, coupled with growing environmental concerns, have led to research being carried out into producing more energy-efficient asphalt mixtures. To date, product-development work has concentrated on asphalt mixes such as cold mixtures and intermediate-temperature warm mixes, and has tended to be restricted to the research laboratory.
In 1995 Shell Bitumen and Kolo-Veidekke, a Norwegian contractor, initiated a joint product-development programme designed to develop a product and process for manufacturing asphalt at lower temperatures. The main objective was to develop a material that has equivalent properties to those of traditional hot-mixed asphalt, the result being the Warm Asphalt Mixtures (WAM) range of products. Shell and Kolo-Veidekke have obtained a patent for the WAM process and products, which include WAM-Foam and WAM-Emulsion.
Following these developments, Lafarge Aggregates recognized the environmental potential of the WAM-Foam process and joined Shell Bitumen to carry out a series of trials in the UK. Product-development trials have been successfully transferred from a laboratory environment to real-life situations, with mix designs carried out in the laboratory being transferred to full-scale production and laying operations.
With the introduction of Local Agenda 21 there is growing support and demand for pavement reconstruction to include recycled aggregates. Materials that would previously have been considered as waste are now being incorporated into new materials and Lafarge and Shell have successfully combined the benefits of recycled aggregates with WAM-Foam to produce a range of highway materials. The laying trials included a series of 20mm dense bitumen macadam basecourse mixtures incorporating various types and blends of recycled aggregates.
As foam technology and recycling are becoming increasingly popular, this paper examines the concept and environmental benefits of WAM-Foam.
WHAT IS WAM-FOAM?
In order to describe the environmental benefits of WAM-Foam, it is best to compare the process with that of conventional hot asphalt.
Conventional hot-asphalt mixtures
The majority of today’s highways and pavements are constructed from asphalt products that consist of bitumen and mineral aggregate. The aggregate component is usually a mixture of coarse and fine fractions and filler. As illustrated in figure 1, the aggregate is mixed with bitumen at temperatures typically between 150°C and 180°C. The mixed material is then compacted at temperatures usually in the range 130–150°C. The bitumen is heated to a high temperature to ensure that it has a suitable viscosity to coat the aggregate particles. The asphalt is compacted while it is still hot and workable because, as the temperature is dissipated, the material can become more difficult to compact as workability decreases.
WAM-Foam
WAM-Foam manufacture is a two-stage process consisting of hard and soft components (fig. 2), which allows asphalt to be manufactured at temperatures between 100°C and 120°C. The aggregate is heated to approximately 120°C and mixed with the soft component. The hard component is then added to the mixture in the form of a ‘foam’. The foamed bitumen is introduced into the mixture at a temperature of between 150°C and 190°C; the temperature of the foam is dependent on the penetration grade of bitumen used. The mixture is then transported to the laying site where it is paved, laid and compacted using conventional equipment.
Soft component
The soft component, used to coat the aggregates, has a penetration of approximately 1,000dmm at 25°C and a maximum viscosity of 0.3Pas at 100°C. As a result of the low viscosity, the soft component can be mixed with the aggregates at 100°C.
Hard component
The hard component is added as foam at a temperature of between 150°C and 190°C. Depending on the final mechanical properties required from the pavement, the hard component could consist of any grade of penetration bitumen.
Foamed bitumen
Foamed bitumen is a colloidal mixture of air, steam and bitumen. The production of foamed bitumen involves the addition of a small amount of water into hot bitumen. When the water comes into contact with the hot bitumen the temperature of the water rises until it exceeds 100°C, at which point it boils and its physical state changes from liquid to gas causing a massive increase in volume. To put this into context, only 18g of water is required to form 22.4 litres of steam under normal conditions. The steam expands until a film of bitumen holds the steam and air in bubbles. At this point a state of equilibrium is reached between the surface tension of the bitumen and the pressure of the steam and air.
The properties of foamed bitumen are commonly classified by means of an expansion ratio and half life (fig. 3).
Expansion ratio
The expansion ratio is defined as the ratio between the maximum volume achieved in the foamed state and the volume of unfoamed bitumen.
Half life
The half life is defined as the time it takes for foamed bitumen to decrease in volume from its maximum value to 50%.
Foaming characteristics of bitumen
The foaming characteristics of bitumen are influenced by the accurate control of the following parameters:
- temperature
- the rheological properties of the bitumen
- amount of water added to the bitumen
- bitumen pressure.
From a laboratory study of these factors it is possible to optimize the foaming characteristics. The process is complex and accurate proportioning and mixing are paramount.
In order to produce foamed bitumen in a commercial-scale mixing plant, various modifications are required. The most important modification involves the addition of a foaming bar which consists of a number of individual chambers that mix the bitumen, water and air to produce the foamed bitumen (fig. 5).
Lafarge product trial
The WAM-Foam process has been trialled in Norway and has demonstrated that it can be used to manufacture conventional asphalt materials. Wearing course, basecourse and roadbase, as defined in BS 4987, can be mixed in the same proportions for WAM-Foam as conventional asphalt. Twenty millimetre dense bitumen macadam was chosen as the candidate mixture for the Lafarge product trial. Control sections of conventional hot-mix and traditional foamed materials were laid sequentially with
WAM-Foam materials for control and comparison purposes.
Binder content
The total binder content is equal to the sum of the soft and hard components, where the amount of each component used in the mixture depends on:
- the desired equivalent binder grade
- the grade of bitumen used for the hard component.
Shell designed the ratio of soft-to-hard component, in order to achieve the theoretical performance of an equivalent hot mix (fig. 6).
Aggregates
The aggregates were chosen from a number of locally available Lafarge sources. It was decided to use locally available recycled aggregates and recycled asphalt planings as the main constituents for the WAM-Foam and traditional foam materials, as this had the added benefit of keeping lorry movements to a minimum. The aggregates used for the control section were from a source with a known track record.
How it happened
The technical departments of Lafarge and Shell jointly worked on the optimization of the material compositions.
Lafarge’s production personnel co-ordinated the extensive modifications to the asphalt plant. This included installation of the foam bar and associated pipework, which was by far the biggest and most technical feature. A series of complex bitumen storage tanks and recirculation pipework was also installed to facilitate the flow of bitumen to the foam bar. Shell co-ordinated the delivery of the bitumen components to the production unit.
The commissioning of the foam bar was carried out by specialist suppliers. A full series of ‘commissioning’ mixes were carried out in order to verify the foaming process. Once the process was fully operational a number of different mixtures were mixed, transported and successfully laid on a pre-prepared surface. Lafarge Contracting laid the materials over two-and-a-half days using conventional paving equipment. The type and amount of compaction was closely monitored.
Test specimens were cored from the WAM-Foam pavement a few days after the material had been compacted and the mechanical properties were measured. Figure 7 shows that the appearance of the WAM-Foam is identical to that of conventional hot-mixed 20mm dense bitumen macadam asphalt.
Conclusions
The Lafarge/Shell WAM-Foam trial has successfully demonstrated a number of advantages.
Environmental advantages:
- reduction in the amount of particulate emissions from the fine aggregate
- reduction in the amount of greenhouse gases generated
- reduction in the amount of bitumen fumes generated; this is especially relevant around the paving machine
- reduction in the amount of non-renewable fossil fuel used
- a product range with the potential for incorporating recycled aggregates and recycled asphalt planings.
Technical advantages:
- WAM-Foam mixtures are made at lower temperatures than conventional hot mixtures
- WAM-Foam can be manufactured in modified conventional asphalt plants
- the workability of WAM-Foam is similar to conventional hot mixtures
- the WAM-Foam process is suitable for roadbase and basecourse applicationsthe mechanical properties, including stiffness modulus and indirect tensile fatigue ??characteristics, are equal to the properties of equivalent hot mixtures
- the physical properties, such as density and air voids, are similar to those of conventional hot mixtures.
Bibliography
‘Coated macadam for roads and other paved areas’, BS 4987: Part 1:
‘Specification for constituent materials and for mixtures’, BSI, 1993.
KHWEIR, K.: ‘Foamed bitumen using a 15pen bitumen’, Heriot-Watt University, 2001.
KOENDERS, B.G., D.A. STOKER, C. BOWEN, O. LARSEN, D. HARDY and K.P. WILMS: ‘Innovative process in asphalt production and application to obtain lower operating temperatures’, 2nd Eurasphalt & Eurobitume Congress, 2000.
READ, J.M.: ‘A simple guide to viscosity and rheology’, Shell Bitumen, 1998.
WHITEOAK, C.D.: The Shell Bitumen Handbook, 1990.
WHITEOAK, C.D.: ‘Testing and specifications of bitumen’, Shell Bitumen, 1998.
The author, David Strickland, is technical manager (roads and airfields) with Shell Bitumen. This article first appeared in the Institute of Asphalt Technology's Asphalt Yearbook 2002 and is reproduced here by kind permission of the IAT.