Texas Overlay Test for Asphalt
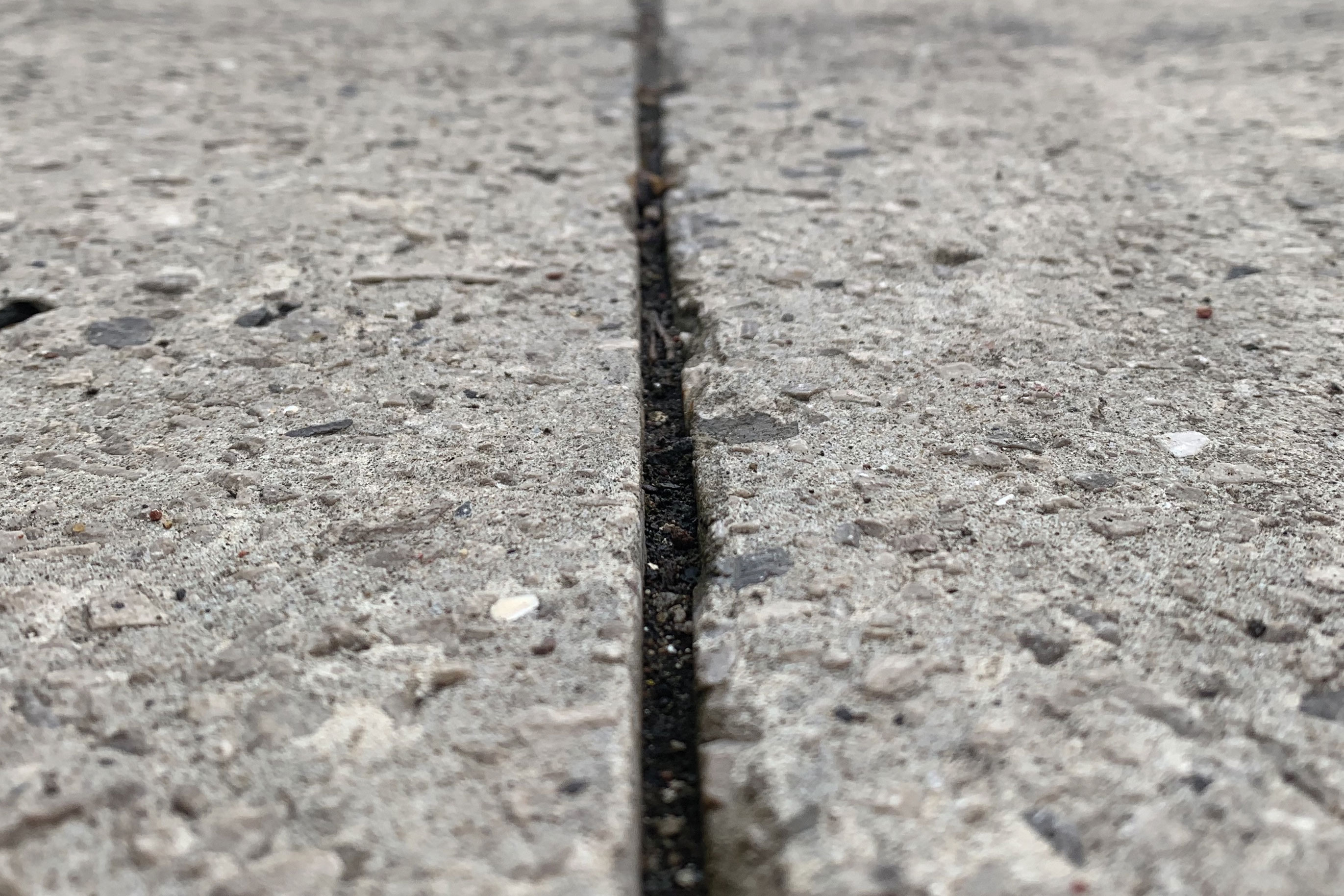
First published in the June 2019 issue of Quarry Management as Texas Overlay Test
Rebecca Ann Haigh, asphalt manager with Total UK Ltd, assesses whether pushing the boundaries of this test can provide a better understanding of asphalt overlay behaviour, performance and design
Highways England’s strategic road network has more than 1,200km of concrete pavement throughout its system, with the local authority network containing even more. Bridges, flyovers and other concrete structures also require special consideration when asphalt surfacing is applied, due to exaggerated movement from thermal and dynamic forces. Overlaying these pavements with an asphalt thin-surface course improves ride quality, reduces noise and can maintain a deteriorating surface. This combination of concrete and asphalt places unique strain characteristics on the material. The overlay may suffer from reflective cracking due to thermal expansion and contraction cycles in the underlying concrete as well as the effects of traffic loading. Any cracking in a pavement is undesirable, as this leads to water ingress and, ultimately, pavement failure.
One effective method to assess a material’s resistance to these thermally induced strains is the Texas Overlay Tester (TOT). The TOT compares the performance of asphalt overlays and their constituents in a controlled environment. The TOT maintains a regular cyclical movement at a controlled temperature, assessing the load required to do so. The AASHTO standard requires set voids in the material, a test temperature of 25°C, 1,000 cycles and samples manufactured through gyratory compaction of a 150mm core that is then cut to size. This paper looks at pushing the boundaries of this test, to better assess and understand the materials being used within asphalt overlays.
To reflect in-situ performance, real materials at their designed void content were used. The impact of temperature was explored to obtain a more detailed impression of the performance characteristics of the material. On the high-performing material, extending the number of cycles to failure, to push the material to its limits was explored. Finally, sample preparation techniques were varied to monitor their effect on performance and the spread of results.
The data provided by this equipment build up to create a more detailed explanation of the characteristics of the material in this mode.
Background
The behaviour and performance of asphalt is determined by the relationship between the bitumen characteristics and the aggregate interlock. Bitumen exhibits two key behaviours; it is both viscoelastic and thermoplastic.
Viscoelastic behaviour can be broken down into the viscous (flow) and elastic (solid) contributions to the response of an asphalt when a stress is applied. The viscous element allows the material to flow or deform and is more evident at higher temperatures and lower-frequency forces. The elastic portion resists movement, displaying an immediate and opposite response, and is more evident at low temperatures or higher-frequency forces. A viscoelastic material such as bitumen displays a combination of these characteristics. The balance of these behaviours dictates the overall performance levels of the specific bitumen type.
Thermoplastic behaviour relates to the change of behaviour with temperature, namely increasing flow with rising temperature (due to the higher contribution of the viscous component) and increasing solidity with decreasing temperature (due to the higher contribution of the elastic component).
Within the viscoelastic range the asphalt is able to relax impacted strain. This allows the material to react to the applied stress and relax rather than fracture. Outside the viscoelastic range, applied stress can mean the material loses its ability to relax. This can be related to temperature with thermoplastic behaviour, and frequency of force with viscoelastic behaviour. Elastomeric polymers are often added to enhance this characteristic at extremes of temperature, widening the window where the binder will resist deformation or fracture.
THE TEST PRINCIPLE
The TOT simulates the effect of a temperature change of 14°C, in a concrete construction with set distance of 4.5m between joints, in an accelerated test (fig. 1).
The load required to make the 0.635mm movement throughout the test is recorded in a performance graph. When studying these graphs there are three distinct phases within the results (graph 1).
- Rapid decline – there is an initial rapid drop-off of load, seen to be the initial yield point, where the level of elastic behaviour reduces and the plastic behaviour becomes more dominant.
- Settling curve – there is then a settling-down period, where there is a more gradual curve and the relationship between plastic and elastic tips at a steady pace showing the capability of the binder to relax strain.
- Equilibrium – the third phase shows more of an equilibrium of solid and liquid behaviour with a longer, lower gradient.
Method
Cores measuring 150mm in diameter x 127mm in height are gyratory compacted. Two samples measuring 150mm x 76mm x 38mm are cut from each core to create a pair of ‘lozenges’. Epoxy resin is used to fix each lozenge to two base plates (fig. 2). Each sample is temperature conditioned for a minimum of 2h, then the machine cycles a load on the sample, opening and closing the gap between the two plates by 0.635mm, returning to its start position within 10s. The peak load is recorded and the cycle repeated. The test ends when either 1,000 cycles have taken place or the load needed to complete the cycle is reduced by 93% from the initial load. Once the test is completed, assessment of visible cracks takes place and the results are recorded. The ASTM test is at a standard 25°C; an assessment of an adjustment in temperature would give a greater understanding of the material.
Assessment protocol
The aim was to assess the impact of binders with different polymer contents and stiffness levels on the performance in a standard single asphalt design. The boundaries of this test were pushed in order to better understand the materials used within asphalt overlays. Temperature assessment took place, investigating how it would affect the initial stiffness and retention of stiffness, and was then used to compare equi-stiffness materials.
The use of a ‘real’ material at its designed void content was to reflect in-situ performance. The temperature range was used to assess temperature susceptibility. On the high-performing material, extending the number of cycles to failure was assessed, to push the material to its limits. Finally, sample manufacturing techniques were reviewed for repeatability and practicability, and to see how these would affect the test performance of the samples. The data from these results build a more detailed explanation of the characteristics of the material in this mode.
Assessment at three temperatures – 20°C, 15°C and 10°C – on a high binder content asphalt concrete design took place. The range of Total normal paving grades and Total Styrelf binders selected was in order to gain a broad understanding of the materials and the test. The binders were: 40/60 (target 50dmm) Pen; 50/70 (target 70 pen) Pen; Total Styrelf X70; Total Styrelf eXcel 70; Total Styrelf eXtreme 70; and Total Styrelf eXtreme 100.
During testing the TOT displays the loading and unloading cycle performed on the sample, with a line recording the initial load and displaying the continuing reduction in load required for movement (fig. 3). The load is applied in a cyclical triangular wave form taking 5s to move out and 5s to move back to the starting position again. Figure 3 shows the force required to perform this action. The initial load increases at a steep rate, then there is a slight plateau as it finds a suitable load for the constant movement, with a final peak at the extreme of the motion. The return load shows a rapid drop in load as the elastic behaviour assists in the return, and again a slight plateau and final drop off as it returns to point zero.
Binder results
Binder | Softening point (°C) - BS EN 1427 | Penetration (x0.1mm) - BS EN 1426 |
50 Pen | 50.6 | 52 |
70 Pen | 47.6 | 68 |
Total Styrelf X70 | 52.8 | 66 |
Total Styrelf eXcel 70 | 56.6 | 69 |
Total Styrelf eXtreme 70 | 66.6 | 67 |
Total Styrelf eXtreme 100 | 90.5 | 95 |
Samples
Six lozenge samples were prepared for each material at each of the three test temperatures and four of these samples were tested. One outlier from each set was rejected and the average of the remaining three samples reported. If there was any evidence of de-bonding of the material from the plates, rejection of the sample took place and the fifth and sixth samples were tested as necessary. De-bonding was of specific concern regarding the performance of the epoxy resin at the lower test temperatures. The lowering of temperatures could cause shrinkage and contraction of the plates, causing unnecessary stress and de-bonding. To eliminate this possibility, the conditioning of the plates, jig and sample took place in a temperature-controlled incubator for 2h at the required test temperature, before bonding the samples to the plates in this temperature-controlled environment.
Test results
Graph 2 presents the final percentage decline in load after 1,000 cycles for each material, at each temperature. Three factors are shown to affect the final percentage decline and, therefore, the destruction of the material. First, the percentage load decline at 1,000 cycles increases in each material as the test temperature is decreased. This is due to the thermoplastic characteristic of bitumen stiffening the material with the cooling temperature. This reduces the level of relaxation capability within the material required to prevent crack propagation within the sample.
Secondly, it can be seen that the percentage decline reduces when the polymer content is increased. This demonstrates the elastomeric behaviour of the binder contributing to the recovery of the material at each cycle and slowing down crack propagation. The higher the polymer content when comparing the same polymer, the greater the elastic recovery and reduced destructive behaviour.
The third difference that can be seen within this graph is how the increase in penetration can affect the percentage decline. There is an identifiable step change between Styrelf eXtreme 70 and Styrelf eXtreme 100, where the increased penetration of the material presents a more forgiving nature and a reduced percentage decline within this test. The higher the penetration the lower the stiffness of the material. The two non-polymerized materials did not complete the 1,000 cycles and, therefore, show a 100% failure flat line in this representation of results.
Graph 3 represents one material, Total Styrelf eXtreme 100, and shows how the load reduces over the length of the test at the three test temperatures. The starting load increases with the reduction in temperature due to thermoplastic behaviour. As discussed previously, there are three phases of the graph, the rapid decline, the settling curve and the equilibrium. This graph shows that the lower the test temperature, the shallower and longer the settling curve is. This could be due to the more solid behaviour taking the lead over the liquid behaviour at the lower temperature.
Graph 4 relates the load required to complete the 0.635mm expansion and contraction over 10s to the final percentage decline of the material. This allows comparison of materials in a more detailed manner to consider how the plastic and elastic behaviour relate in equi-stiffness materials. The polymerized 70-pen materials group closely with regard to initial load at set temperatures. The Total Styrelf eXtreme 100 results show how the high polymerization and softer base pen work together to offer less resistance to loads and less permanent damage to the material.
The initial load required at each individual temperature on all of the 70-pen materials group in the same area, relating the initial load more to the penetration than to the polymer content. The red line identifies two very different materials at different test temperatures with a similar initial load. The Total Styrelf X70 is of low polymerization with a lower penetration, at 20°C, and Total Styrelf eXtreme 100 is of high polymerization, with a higher penetration, at 10°C. The comparison is displayed in graph 5. Unusually, the Total Styrelf eXcel 70 results appear to buck the trend with a higher than expected initial load at 10°C. This could be due to issues with sample preparation – over tolerance, sample age, temperature control, equipment fault etc. A repeat of the testing would be necessary to iron out these issues.
Graph 5 looks at the relationship between tests with the same initial load, and therefore the stiffness of the material, with the reduction in load cycle. The two materials have different penetration, polymer content and test temperatures, but this combination provides the same initial load and the same initial performance. Over the 1,000 cycles the Total Styrelf X70 shows a greater reduction in load with a slight increase in the rate of loss. This is a good representation of the performance of a well-selected binder for the environment in which it is required to perform.
Sample preparation
With two samples having to be cut from a 150mm diameter core, and with three cores prepared for each material at each temperature, the repeatability of the cutting was very unstable as the cores are an awkward shape to handle and the tolerances are quite tight at ±0.5mm. Considering the consequence of sample preparation, it was felt that compacting the asphalt in one slab and cutting six bricks from each slab would remove any error from mixing and compacting multiple samples, and give good sample repeatability and greater control when cutting. It was also felt that with the critical test section being in the centre of the lozenge, the sharper-cornered brick-shape sample would not affect the test results.
Also, recent experimentation with water-jet cutting on four-point bending samples had led to much greater repeatability and it was thought the tight tolerances required in this specification would benefit from the greater control offered by this cutting procedure.
Adopting these adjustments to sample preparation produced a greater repeatability between test samples, resulting in fewer samples being needed to obtain reliable results. Graph 6 – core compacted, saw cut, shows an average of 85% decline with results within a range of 81–93%, a difference of 8%. Graph 7 – slab compacted, water-jet cut, shows an average of 87% with a range of 85–89% and, therefore, a difference of 4% – halving the level of repeatability and halving the number of samples required.
Discussion
Sample age
A third party prepared the samples and all testing was completed within two weeks of manufacture. An assessment of samples past these two weeks took place with a variation in results found, mainly the material gaining stiffness over time. All samples tested were in the order of 20°C, 15°C and 10°C. Exaggeration of this stiffening of the material could have occurred with the ageing of the material along with the reduction in temperature. It was hypothesized that a more reliable comparison might be achieved by allowing a set time to pass before testing takes place, allowing the material to stabilize, as with other EN standards such as four-point bending.
The tolerance of ±0.5mm on these samples was very difficult to obtain on the circular saw, and more often than not resulted in samples slightly over or under the allowed tolerances. Cutting samples from a 305mm x 305mm x50mm slab using a water jet solved this problem. The initial results showed 100% success rate on passing the tolerance of ±0.5mm, and the samples were compacted with lower air voids, within the range, than what was possible with the gyratory compactor. The samples per set were more uniform with six samples produced from one slab. Initial results have shown an excellent level of repeatability and a tighter control of sample preparation. As yet, there has been no negative effect on the performance recorded by the Texas Overlay Tester.
Results
Graph 2 shows a good relationship between the varying materials and the temperature reduction. Neither of the unmodified materials reached the 1,000 cycles at any temperature. The increase in modification shows a reduced percentage decline in the load.
In graph 4, the Total Styrelf eXtreme 100 shows an even further reduction in percentage decline, due to the softer penetration of the binder. The initial load was more than 50% less than any of the 70-pen materials, therefore showing less resistance and more of a flow of material. Explaining this behaviour is possible with the use of the Dynamic Shear Rheometer (DSR). The phase angle δ reported from the DSR represents the relative contribution of liquid and solid behaviour the material displays – 0° demonstrating complete solid behaviour and 90° being a complete liquid. The Total Styrelf eXtreme 100 has a lower phase angle than the Total Styrelf eXtreme 70, displaying a more liquid behaviour and, hence, the greater flow of the material.
Although the higher penetration material shows a lower initial load required for the movement, the final load at 1,000 cycles is only 0.16kN difference between the eXtreme 70 and eXtreme 100. The Total Styrelf eXtreme 100 material shows a strong resistance to cracking.
Further assessment of the graph shows the three phases of the results; rapid decline, settling curve and equilibrium over the largest portion of the graph and, therefore, the test. This is showing an initial relaxation, then a steady decline. Pinpointing the finite turning point of these phases may be a helpful comparison point in future testing.
Temperature range
The temperature reductions from the specification are within the capabilities of the incubator. A recent upgrade of the equipment has allowed the incubator to achieve a reduction to 5°C comfortably, and to 0°C possibly a little less comfortably. Lower-temperature assessment in this format could give greater insight into the material performance. These lower temperatures have been excellent for assessing the behaviour of polymerized bitumen. They are a little harsh for the assessment of straight pen bitumen as the test of these materials never reaches the full set of 1,000 cycles. The testing of Pen bitumen at 25°C may be more suitable for this study.
Stretching the limits
The testing officially stops at 1,000 cycles, according to specification, and it is only possible to extrapolate from the data how the material would perform in continuing cycles. An extended test to failure could help to further understand and differentiate between materials.
Through stretching the limits of the pre-programmed test cycles, it was possible to reach 1,600 confidently and with no negative effect on the data – this is not a great stretch from the traditional test. Continuing development with the manufacturers is looking to extend all testing to destruction, so in this case a reduction in load of 93% from initial load.
Now that slab compaction and water-jet cutting are a proven and suitable method of sample preparation, building up layers of different materials and cutting different dimensions becomes an option. This is something that would be very difficult to achieve using cores. Studying the effect of stress-absorbing membrane interlayers (SAMIs) on the prevention of reflective cracking through the asphalt can be assessed. SAMIs come in a range of forms from geo-synthetics to highly polymerized mastics, and all types can be compared directly through this testing.
Looking at longer-term storage of the samples before testing to allow relaxation and good repeatability could assist in results which represent real-life reflective cracking.
Assessing the ageing of the material by exposing the samples to a range of temperature differences over time before testing may result in this being a reliable and repeatable ageing test in the future. This could reflect the loss of capability of aged bitumen in the asphalt to relax any induced strain.
All testing so far has been on this specific asphalt concrete. Further investigation into other asphalt designs will help to build a picture of the performance of materials in this failure mode. This can help ensure the right designs with the required performance in the right environments, to improve the durability of the pavement.
Initial indications on this equipment are very positive with a lot of interesting data and options becoming available all the time. It is relatively early in the process and there will be a lot of fine tuning and repeating of tests to verify the data, but the data so far provide increasing confidence in the test being a predictive tool for asphalt behaviour an design.
For more information visit: www.total.co.uk
- Subscribe to Quarry Management, the monthly journal for the mineral products industry, to read articles before they appear on Agg-Net.com