Sustainable Developments
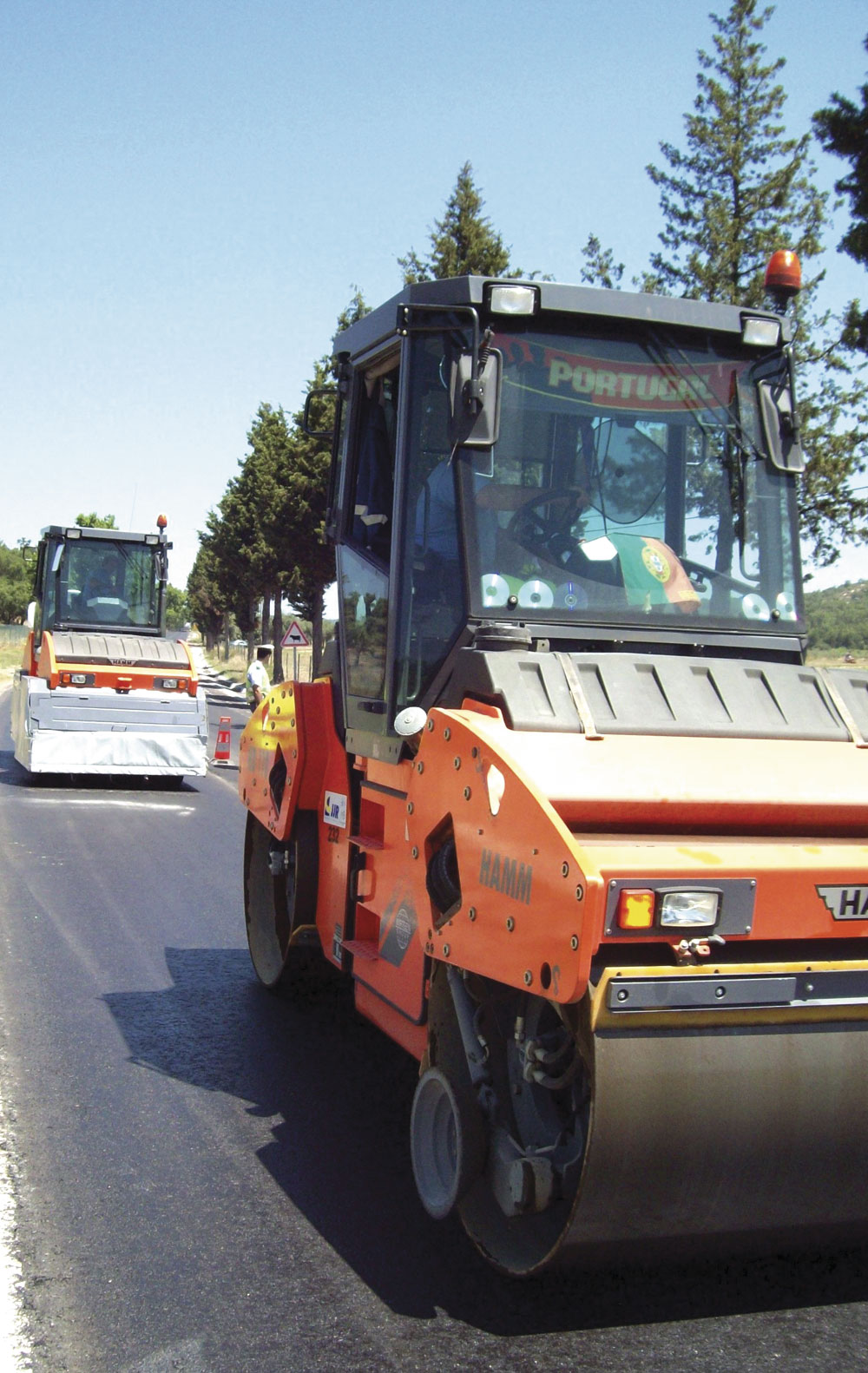
Allan Grossart, market development manager with TOTAL Bitumen, examines the industry’s response to environmental challenges
Global warming has increased awareness of environmental and societal challenges, leading to new regulations that have stimulated research towards a better acceptability of bituminous products. Sustainable development is a powerful engine for advancement – new techniques for lower-temperature applications, recycling, bio-concepts and increased durability of asphalts are some of the areas being studied.
TOTAL are aware of the constantly changing environments in which they operate and, after extensive worldwide customer consultation by means of TOTAL Bitumen’s Sustainable Development Survey, strategic development areas for both new products and applications have been identified. This will allow the company to pave the way in bitumen research and develop appropriate bitumen and mix designs to meet the needs of all users in the areas of hot- and cold-mix applications.
Durability
Durability is an essential performance indicator for asphalts, allowing longer-lasting pavements, reducing maintenance, minimizing traffic disruptions and promoting efficient asset-management practices.
A major factor limiting the use of pure bitumen in road construction is its performance at different temperatures. At low temperatures (less than –10°C) pure bitumen is glass-like and brittle and allows micro-cracks to propagate in the asphalt, leading to transversal and longitudinal fractures.
At higher temperatures (greater than 60°C) pure bitumen tends to soften and begins to lose elasticity and, as a consequence, can lead to pavement rutting and permanent deformation.
The addition of polymers modifies bitumen behaviour by decreasing its thermal sensitivity and widening its plasticity interval to all temperatures, thereby allowing asphalts to maintain good mechanical properties over a wider range of serviceable temperatures.
Elastomeric polymer-modified bitumens (PmBs) tend to be either physical blends or cross-linked, which requires an additional processing step to chemically cross link the polymer. This results in a three-dimensional polymer network within the bitumen matrix, which enhances the performance of certain mechanical characteristics of the asphalt. TOTAL’s Styrelf range of PmBs are cross-linked and have demonstrated enhanced storage stability as they are less prone to phase separation. Also, owing to their homogeneity at the micron scale, they offer increased resistance to oxidation and therefore age less quickly.
Also, the polymer network remains virtually unchanged after the rolling thin-film oven test (RTFOT) and pressure ageing vessel (PAV) test in the case of the cross-linked PmB (Styrelf), whereas the polymer nodules in the physical blend tend to shrink. The overall polymer content, measured through infrared characterization, decreases after RTFOT and PAV for physical blends but not for cross-linked1.
A study of the durability of PmBs has been conducted in an independent project by the University of Lausanne, in Switzerland, using 16 selected binders from a variety of suppliers. The asphalt was produced under identical conditions then laid in 300m sections. The work was undertaken in 1988 and has been monitored by the University ever since.
The graph below shows some of the results and highlights the benefits of cross-linked PmBs. Styrelf is the only section to remain intact since 1988; all the other sections have since been replaced.
Other benefits of cross-linked PmBs include:
- excellent rutting and fatigue resistance
- resistance to binder drainage
- increased flexibility.
Sustainability
Bituminous materials have the potential to be 100% reusable and, therefore, there are numerous techniques to reuse or recycle asphalt. If the recycling can be undertaken at reduced temperatures, this is another substantial advantage. Bitumen emulsions have been used with 100% recycled materials and mixed cold (40°C) to give an asphalt suitable for low-category roads and footpaths.
Another advantage is that the asphalt can be stockpiled for up to six weeks if stored correctly. TOTAL’s Emulsis MG has been used successfully in this way for more than five years.
Another innovation is the use of recycled asphalt planings (RAP) in Enrobe a Module Eleve (EME) products. This has proven successful in The Netherlands (patent filed in 2008) and the resulting asphalts have shown excellent performance in terms of stiffness and fatigue resistance.
Bio-products are also being introduced into the market and so far this has been concentrated in clear binder products.
Low temperature
Reducing the temperature at which asphalt is produced and laid is an effective way to tackle sustainability issues, specifically greenhouse gas emissions. As a result, products and processes that address this issue, through the addition of chemical agents to the bitumen or to the asphalt mixing process, have increased in popularity in recent years.
In addition to the environmental advantages, other benefits include:
- fuel savings – heating costs will be reduced
- lower temperatures mean less exposure to emissions for operators/workers
- road closure times should be reduced; asphalt will potentially have a longer workability window and compaction should be easier.
Some of the available technologies can be categorized as:
- Warm mix (mixing temperature: 110–150°C)
- Semi-warm mix (mixing temperature: 100°C)
- Cold mix
There are several additives available for warm-mix asphalt; these can be added to the bitumen or at the asphalt mixing stage.
A semi-warm mix is more challenging and often requires significant alterations to the asphalt plant. An emulsion-based technology, designed by the TOTAL Group in Spain, which requires only minor modifications to an existing asphalt plant is a recent example of innovation in the market. It is also possible to use this emulsion with up to 100% RAP. The two photos on this page show the asphalt being laid at approximately 90°C
Cold mix does not yet give the same early-life performance as hot-mix. However, this problem is being studied and, potentially, will be overcome. Currently, there are only a few products available with potential rewards, but with the recent launch of the asPECT carbon calculator (a collaborative research project between the Highways Agency, Mineral Products Association, Refined Bitumen Association and TRL Ltd, and further endorsed by the County Surveyor’s Society) as a standardized methodology to calculate the life-cycle greenhouse gas emissions or the ‘carbon footprint’ of asphalt used in highways, there will now be a much greater focus on the carbon footprint of construction materials.
Other product innovations include surface-dressing binders, such as Emulsis Ultra and Emulsis Satis, which can be used at 65°C (some 15°C lower than other conventional binders). The illustration opposite shows a thermal image of Emulsis Satis being used at a reduced application temperature.
In summary, binder innovation provides the operator with:
- energy savings
- fuel savings
- time-management improvements
- increased environmental awareness
- reduced carbon footprint.
All of the above technologies and processes demonstrate ways in which the industry is responding to environmental challenges to ensure future success.
References
- LAPALU, PLANCHE, J-P., MOUILLET, V., DUMAS, P., and F. DURRIEU: ‘Evolution of the rheological properties of polymer-modified bitumens during ageing’, Eurobitume and Eurasphalt Congress, Vienna, 2004.
- DUMONT, A-G., and M. OULD-HENIA: ‘Long-term effect of modified binders on cracking resistance of pavements’, Cracking in Pavements, RILEM Symposium, Limoges, 2003.