Rubber, Roads and Recycling: Reshaping the nation’s highways
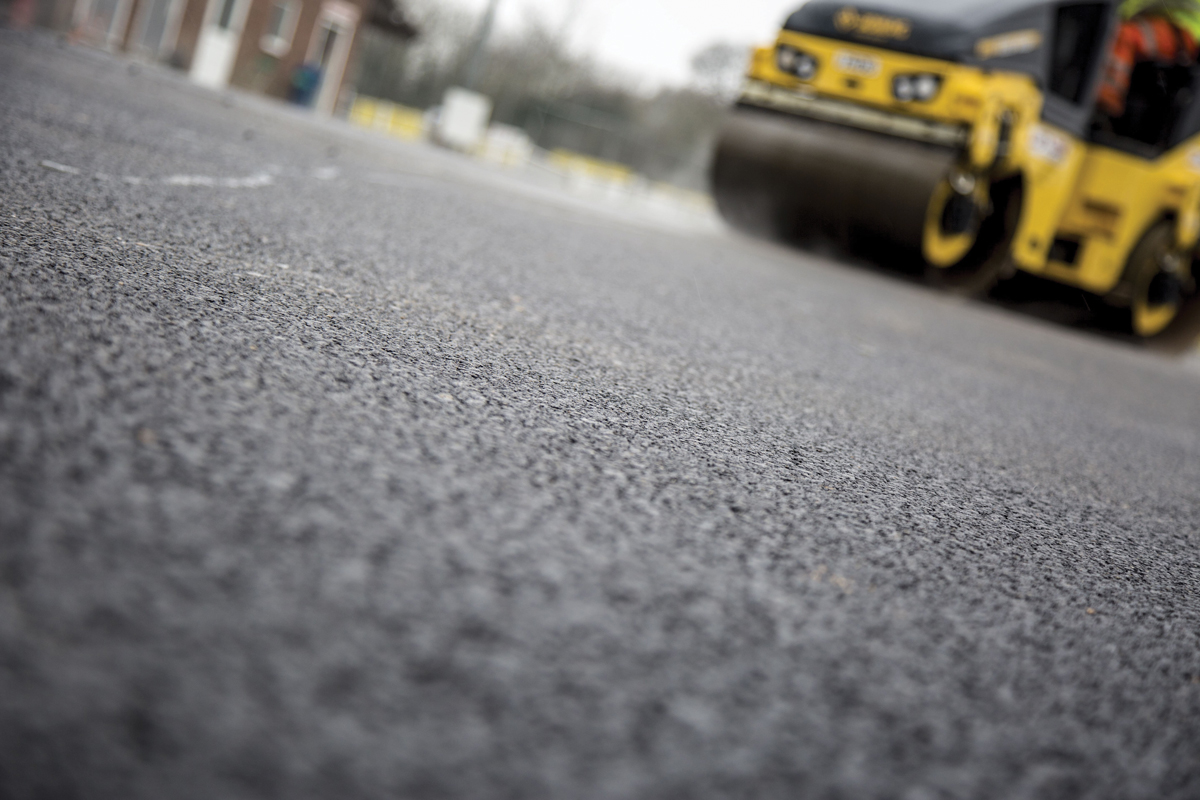
First published in the January 2020 issue of Quarry Management
Tarmac are leading a sustainable revolution in the UK asphalt sector with the introduction of a new rubberized asphalt which utilizes recycled waste tyres. National technical director Brian Kent discusses how this innovative technology has the potential to reshape the nation’s roads
The so-called ‘Blue Planet effect’, borne out of Sir David Attenborough’s televised environmental activism, has seen the UK put a renewed focus on driving down plastic waste and improving the recyclability of packaging. However, with single-use plastics dominating media headlines, other significant waste streams continue to be overlooked.
The UK has long grappled with how to dispose of waste tyres, with many industry outsiders not even fully aware of the scale of problem or the options available to recycle them. While ‘end-of-life’ tyres in asphalt mixes have been used since the mid-1990s in places such as the state of California in the US, the burgeoning technology is now increasingly being adopted in China, Malaysia and South Africa.
Our commitment to sustainable working practices has seen our business recycle 8.7 million tonnes of waste every year from other industries. This includes using end-of-life tyres as fuel in our cement kilns, for example. However, the UK has not paid close enough attention to the wider possibilities and opportunities available and, consequently, low demand for end-of-life tyres has resulted in a surplus of 120,000 tonnes of rubber waste being shipped abroad annually, with the UK’s tyre-recovery sector processing more than 40 million used tyres every year.
Creative thinking
Tarmac’s introduction of the UK’s first rubberized asphalt using recycled tyres is set to revolutionize waste tyre management and disposal. We first began investigating the use of end-of-life tyres in asphalt back in 2011, but by combining our technology with that of our parent company CRH in North America, who have been using rubber for more than 20 years, we have been able to accelerate progress to make this solution available now.
The US experience has found that the presence of rubber in the surface course restricts crack propagation and delivers additional benefits over standard penetration-grade materials by providing a cost-effective low-grade polymer option for clients.
Until now, UK clients have been faced with the straight choice of using a pen-grade binder or a polymer-modified binder (PMB). This new option offers a mid-cost and mid-performance alternative and will be of particular interest to clients where they feel their site condition needs more than a pen-grade material can provide, but probably doesn’t require all the benefits that a high-performing PMB will deliver.
In terms of usage, each tonne of rubber-modified asphalt incorporates one tyre, therefore, depending on thickness of layer, there will be approximately 500 tyres included in each kilometre of pavement. We are also only supplying rubber-modified asphalt at warm-mix temperatures, which further improves the overall sustainability of the product.
Future-proofing
Our production process involves the addition of a fine-milled rubber at our asphalt plants and we’ve recently modified several of these to allow accurate addition. The modifications involve the installation of automated addition systems, an additional silo, feed adjustments and alterations to the plant software. The cost for these modifications varies depending on the plant, but other facilities will be upgraded as demand for this innovative technology strengthens.
These upgrades present us with an opportunity to further our own commitment to the circular economy, in which we keep resources in use for as long as possible, extract the maximum value from them while in use, then recover and regenerate products and materials at the end of each service life. By investing in the necessary modifications to our facilities today, we can ensure that we are playing our part in cutting waste and contributing to the growth of a sustainable strategic road network.
Opportunity knocks
Trials of the new material are already well under way. On the M1 motorway, Highways England is carrying out initial field tests on a section of road between junctions 23 and 22 on the southbound carriageway near Leicester, which has been laid with the new rubber surface material. However, in this case the rubber incorporation has been increased to 1.3 tyres per tonne of asphalt as Highways England and Tarmac push further to explore the potential benefits for the strategic network.
Commenting on the testing, Martin Bolt, corporate group leader at Highways England, said: ‘Our trial could well be the first step to rapidly reducing the number of tyres piling up in the UK and beyond. The economic and environmental potential of this new asphalt is significant, and we are delighted to be working with Tarmac in this trial.’
Equally, the new surface has not gone unnoticed at a local level. In Coventry, for instance, we’ve already supplied the city council with the rubber asphalt mix. Rob Little, senior engineer - highways technical, stated: ‘We hope we can use more of the product across the city in the future to help divert waste tyres from landfill and incineration, to reduce the carbon footprint for road construction projects in Coventry. We’re proud to be providing road surfaces which are delivering significant environmental benefits for our communities.’
Reducing waste exports
The trialling of this technology across the UK is the first step towards reducing tyre waste exports and is already capturing the imaginations of industry professionals. Peter Taylor OBE, secretary general of the Tyre Recovery Association, observed: ‘While there has been significant progress in reusing and recycling waste tyres in the UK, there is still an over-reliance on the export of used tyres to countries such as China, India and Pakistan, which are importing fewer tyres as they become self-sufficient.
‘The UK needs a second disposal route for used tyres. Tarmac’s commitment to developing rubberized asphalt provides an excellent opportunity to achieve this and deliver environmental savings for this under-used waste stream.’
With many local authorities now identifying schemes using rubber-modified asphalt, this technical innovation has the potential to reduce the number of waste tyres exported across the globe and benefit the growth of the circular economy – contributing to the success of a more sustainable road network.
- Subscribe to Quarry Management, the monthly journal for the mineral products industry, to read articles before they appear on Agg-Net.com