Playing a part in a lower-carbon future
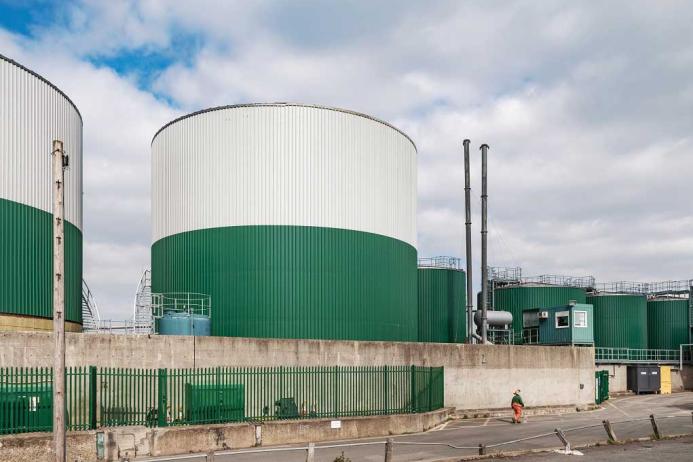
First published in the July 2023 issue of Quarry Management
Improving the longevity and durability of road surfacing materials can help highway clients achieve their carbon goals and reduce maintenance costs
This is a particularly challenging time for publicly funded highway authorities. With budgets being squeezed and costs going up, they need to find ways to maintain their road networks while also working towards the net-zero carbon targets that have been set by both local and national governments.
‘We can see the pressures our clients are under, whether it is to reduce carbon in the materials they use, or to reduce energy usage or the number of times they resurface a road,’ explained Mark Flint, technical director at FM Conway, whose highway clients include London boroughs, county councils, Transport for London and National Highways.
Mr Flint believes the best way to address these pressures is to provide surfacing products that increase the lifespan of the road, so ongoing maintenance – and the carbon emissions that go with it – is kept to a minimum. ‘If you can lengthen the life cycle of a road to 20 years instead of 12, this not only saves costs, but when you come to analyse carbon there is a massive reduction,’ he said.
FM Conway produce their own asphalt at seven plants around London and the South East and are the only UK highways materials manufacturer and contractor to produce their own polymer-modified bitumen (PMB). ‘We could buy PMBs from other suppliers but ours are tailor-made for what we need and are aligned with our recycling capabilities,’ explained Mr Flint. The business is well known for its expertise in incorporating recycled asphalt products (RAP) in surfacing materials, and recently carried out a project to resurface a section of the M3 in Hampshire with materials that included 70% RAP content in the binder course and 50% in the surface course.
The PMB is manufactured at FM Conway’s Imperial Wharf bitumen terminal on the river Thames at Gravesend, in Kent, where the company imports over 100,000 tonnes of bitumen a year by ship and has the capacity to store 7,500 tonnes. ‘The terminal gives us a very good level of resilience and gives security of supply to our clients and partners,’ said Mr Flint.
The modifier in the PMB is SBS (Styrene butadiene styrene), which enhances the bitumen’s performance characteristics by providing greater resistance to rutting and fatigue cracking, and by preventing damage at high or low temperatures. As a result, the firm’s asphalt mixes containing PMB can improve the durability of highways assets and extend their service life, as well as providing resilience to the impacts of changing weather patterns caused by climate change.
With the capability to produce PMBs, FM Conway can provide a bespoke solution for client specifications, including softer binders for high RAP content mixes, standard penetration (or ‘pen’) grade bitumen products, and PMBs for heavily trafficked roads, airports and ports and situations where durability is paramount. The business also uses additives to create warm-mix asphalts, which help in slowing down the hardening rate of the bitumen.
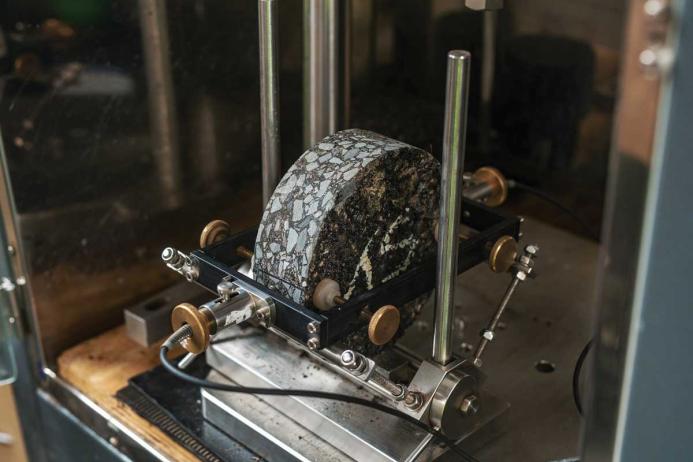
Developing products to meet clients’ requirements for performance, durability and carbon reduction requires constant research and development, which is one reason why FM Conway have invested more than £500,000 in their own UKAS-accredited Technology Centre. ‘The business has made that investment in expertise and specialist PMB and bitumen testing equipment – some of which is not usually found outside of academia – so we can test durability and the effects of high temperatures and low temperatures,’ explained Mr Flint. ‘You need to know how your material is going to work in the real world.’
Equipment at the Technology Centre’s laboratory includes a pressure ageing vessel (PAV) to simulate long-term ageing of bitumen; a dynamic shear rheometer (DSR) to characterize the viscous and elastic behaviour of asphalt binders at medium to high temperatures; and a bending beam rheometer (BBR) to provide a measure of the low-temperature stiffness and relaxation properties of asphalt binders, which together give an indication of the binder’s ability to resist low-temperature cracking.
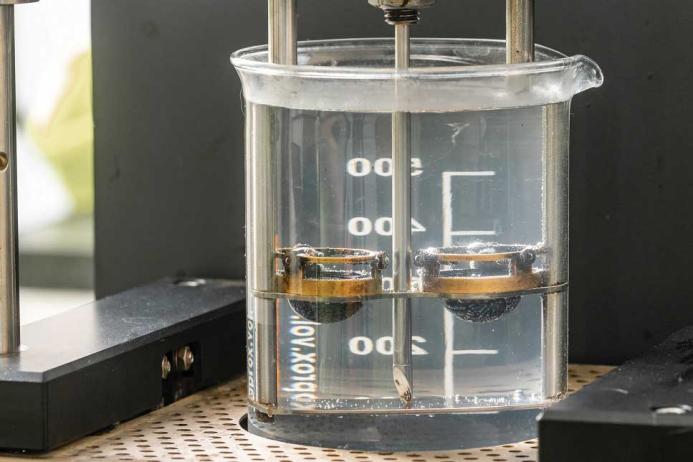
‘When you buy bitumen, the specification is only based on the penetration and the softening point,’ explained Mr Flint. ‘But these tests don’t tell us anything about the long-term behaviour of these bitumens or how they behave under extreme conditions. That’s why we want to do our own performance testing. We take them through the ageing process, both short and long term, using both the RTFOT (short-term ageing) test and the PAV (long-term ageing) test, which can simulate up to 10 or 15 years’ in-life service.’
This significant investment in the Technology Centre has allowed FM Conway to give their clients much-needed reassurance about the longevity and durability of the materials that are being laid on their roads. As Mr Flint said: ‘If you are going to use a particular surfacing material, it is imperative to ensure that it lasts to minimize cost, environmental impact and disruption to the community.’
Similarly, the business has carried out extreme low-temperature testing to show that an asphalt surfacing product being laid on an RAF airfield will not crack at temperatures as low as –23°C.
‘The investment we’ve made in the Technology Centre has been massive, not only in enabling us to develop PMBs, but also in demonstrating that our asphalts can last the length of time we’re making claims for,’ said Mr Flint. ‘Without that investment, we wouldn’t be able to give our clients that reassurance.’
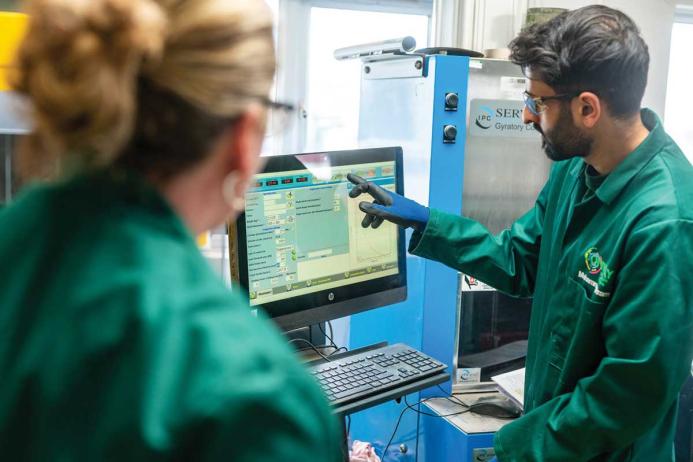
Having their own laboratory also allows FM Conway to study whether a bitumen can be recycled at the end of its life, and to look at the impact of additives both on performance and recyclability. ‘A lot of manufacturers send us additives that they are bringing to market,’ said Mr Flint. ‘We have developed a suite of tests that allow us to very quickly work out if something’s going to work, and if it does, we will develop it.’ This is likely to increase as companies try to develop alternatives to oil-based products, such as bio and synthetic binders.
‘It’s a very fluid situation in terms of the different types of materials we’re trying to produce, and the additives we’re using,’ said Mr Flint. ‘Everything is focused on what we can do to make roads last longer, but we have new factors to consider now – like electric cars. They are far heavier than petrol or diesel cars, so will that affect the life of the road? And what other types of traffic or other types of tyres might be developed and what will their impact be? We are already working with tyre companies to get an idea of what the future looks like.’
Mr Flint added that while there is no escaping the fact that producing bitumen-based road materials involves using oil-based products and carbon-intensive processes, they can still be part of a lower-carbon future. ‘It is carbon intensive, but if we can use recycled materials responsibly and make these roads last longer, then we can be part of the net-zero carbon conversation.’
Subscribe to Quarry Management, the monthly journal for the mineral products industry, to read articles before they appear on Agg-Net.com