Not All Polymer-Modified Bitumens Are The Same
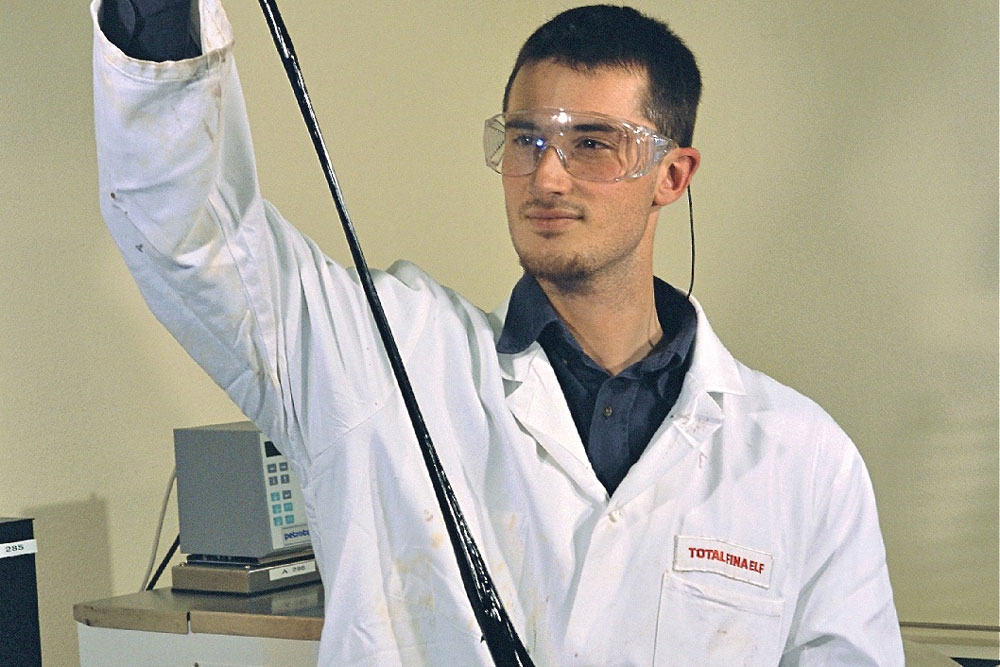
First published in the June 2017 issue of Quarry Management as A Common Misconception
PMB – it’s all the same, isn’t it? Rick Ashton, market development manager with the Bitumen Division of Total UK, looks at the reasons behind this widely held view and explains why polymer-modified binder is not all the same.
The assumption that all polymer-modified binders are the same is a common misconception among contractors and, unfortunately, sometimes even specifiers. Bitumen is a complex material with very useful engineering properties, particularly in terms of its adhesion and waterproofing qualities. It has thermoplastic and viscoelastic properties that bring both benefits and inherent limitations when in its unmodified form.
Unlike water, which is a solid at freezing temperatures and liquid at room temperature, bitumen displays both solid and liquid properties at all temperatures, which means this non-Newtonian behaviour can be tricky to understand. There is a competition to find which characteristic will take precedence in a given situation, which is dependent on factors such as temperature, load and frequency of loading.
Increasing the temperature of bitumen means it takes on a more liquid behaviour, which is useful for transporting the product in pipelines and for the coating of aggregates. Decreasing its temperature means the bitumen takes on a more solid form, and as the temperature drops further, a stiff, even glass-like, brittle nature. This is why, when applied to structural design, any stiffness quoted for bitumen or, ultimately, asphalt is only relevant to the temperature at which the testing is performed.
Increasing frequency of loading (faster loads) means the bitumen takes on more of a solid or stiff nature, whilst decreasing frequency of loading (slow creeping loads) means the bitumen takes on a more liquid behaviour. This is why rutting or asphalt deformation is most common at traffic lights or in HGV creeper lanes and bus stops, where slow or static loads are encountered.
Conventional or penetration grade binder is, therefore, limited in its ability to meet a wider range of temperatures and load variations. This is where polymer-modified binders (PMBs) can start to stretch the performance characteristics of the binder and, ultimately, the asphalt mixtures they are added to. PMBs can increase the range of serviceable temperatures so the bitumen can remain both solid enough to resist softening at high temperature, yet flexible enough to resist cracking at low temperature.
These shifts in performance characteristics can be identified by parameters such as plasticity range. According to BS EN14023, which is the specification framework for polymer-modified bitumens, this property is the numerical difference between the softening point (high temperature) and the Fraass point (low-temperature cracking point) of the binder. Thus, a PMB with a softening point of 75°C and a Fraass of –18°C would have a plasticity range of 93°C. By way of comparison, a 40/60 penetration grade with 50°C softening point and –2°C Fraass point would have a plasticity range of 52°C. Comparisons can be made between PMB products based on the various test parameters within this standard.
There are almost as many polymers available as there are asphalt mixtures, and understanding this is one aspect of getting the most from an asphalt design. SBS, EVA, SBR, crumb rubber and even plastic can all be added to bitumen to alter its characteristics. Understanding the contribution a particular polymer will impart to the bitumen is key to improving the fundamental behavior of an asphalt mixture in situ.
It is still possible to find end-clients asking simply for a ‘PMB’ in the bitumen column of the specification. This is a symptom of a lack of knowledge around the presumed ‘black art’ of PMB selection. Many PMBs are available and their selection should consider the application and previous failure modes encountered on site. A blanket ‘PMB’ specification could mean anything from the addition of a sprinkle of unspecified ‘fairy dust’ to the bitumen, to the addition of a highly modified elastomeric premium product. If the client gets this wrong and applies an inappropriate treatment to the highway, they may increase the possibility of repeat failure or even introduce a previously unseen failure mode.
It is possible to prove this with the 20-year Swiss’ Lavoc study, which was independently conducted by the University of Lausanne. In 1988, 16 sections of the mountainous CH-N9 highway were constructed using the same asphalt designs and foundations but with 16 different binders. The trial used a selection of modified binders and penetration grade binders. Each section was monitored over a 14-year period and a ‘crack-measuring index’ developed for each section. The test included binders with additives – plastomeric and elastomeric PMB binders. The results (fig. 1) show that some of the binders using additives and PMBs actually cracked sooner than the unmodified 80/100 penetration grade binders This indicates that these binders displayed early ageing, brittle or over-stiff characteristics unsuitable for fatigue resistance.
After 14 years the only section still intact was the section using Total Styrelf elastomeric cross-linked PMB. All 15 of the other sections had been replaced. The Styrelf section was left in place and was still serviceable after 20 years, proving the long-term durability of a well-engineered cross-linked PMB.
To further explain plastic and elastic behaviour – a polymer can be elastomeric (eg Total Styrelf) or plastomeric – using plastic modifier.
Elastomeric polymers bring additional cohesion-improving strength, fretting resistance and deformation resistance, and are particularly valuable in reducing the effects of fatigue. Fatigue resistance is crucial where cracking through either thermal movement or reflective cracking may have been a previous failure mode or in situations such as concrete overlays, bridge decks or evolved roads with uncertain structural integrity.
Plastomers tend to impart stiffness, which can be useful in some situations but is less valuable in fatigue resistance. Elastomer PMBs impart elastic recovery characteristics, whereas plastics resist deformation with stiffness but deformation is permanent, or in engineering terms ‘plastic deformation’, once load tolerance is exceeded.
When selecting a PMB it is important to understand which characteristic is required in the end product. Selection should be based on a holistic three-dimensional thought process that considers fatigue characteristics, stiffness, and material-handling and compaction capabilities (in most highway scenarios low stiffness with high flexibility or elasticity is a better choice than stiffness alone.)
Using the softest binder that can withstand the forces to be applied is generally the best way to avoid cracking. As binders age and oxidize roads fail through a process of fatigue or embrittlement. Starting with the lowest stiffness possible that is capable of bearing the predicted strains to be encountered will prolong the onset of the brittle point that, ultimately, will cause carriageway failure. Stiffness is not always the virtue some people believe it to be.
The production of PMB involves the dispersion of polymer units in bitumen. Performance is dependent on bitumen type and grade, polymer type, polymer size and quality of dispersion. In the case of cross-linked PMB, such as Total Styrelf, an additional manufacturing step that ‘cross-links’ the polymer units is employed. Using chemical bonds the polymers become networked and act as a single unit or ‘polymer matrix’ within the PMB.
The existing version of the PMB standard EN14023 is currently under review. Due to a desire by the asphalt and bitumen industry to have a greater understanding of the long-term ageing and rheological characteristics, and to assist in the selection and design of engineered pavement systems, more advanced bitumen test methods are expected to be included in the revision such as: the multiple stress creep recovery test (MSCRT); the determination of complex shear modulus and phase angle (DSR); and accelerated long-term ageing conditioning by a pressure ageing vessel (PAV)
Sustainability through durability
The proposed additions and developments in the standards should assist specifiers in choosing the optimum PMB for their application. As an understanding of PMB performance spreads throughout the supply chain it is certain that asphalt products will benefit in terms of durability. This, in turn, implies that the whole-life performance of a structure will become more predictable. Once deterioration modelling is understood asset management becomes more predictable. It should no longer be possible for a manufacturer to produce ‘holistically’ modified bitumen claiming it to be a PMB panacea, or simply add waste to bitumen claiming equivalence to a premium PMB which has attributes proven by standard test methods. As an expert practitioner who is known too many has always said ‘Give me asphalt, not trashfalt – the highway is not a landfill site.’
The Total Styrelf range also incorporates lower working temperature technology with Total Styrelf EC02. The addition of warm-mix additives to Styrelf allows a temperature reduction of up to 40°C during the mixing stage of asphalt production. This has many benefits. Warm-mix PMB is a reflection of current industry best practice in temperature reduction with penetration grade binders.
Warm mix-asphalts are starting to be seen as beneficial not just in terms of environmental benefits from energy reduction, but for the benefits they bring to the material, the contractor and the client. Lower temperature implies less premature ageing of the product and improved compaction is often cited. Greater tolerance to travelling and speed of opening of the newly surfaced road to traffic are all tangible benefits of these systems.
Historically, PMBs required slightly increased mixing temperature to cope with increased viscosity brought about by the modification of the binder. Additives added to bitumen in the asphalt production stage often require increased mixing temperature and potentially have an effect on the compaction time windows available on site. Ready-to-use pre-blended warm-mix PMB removes the manual addition of additives at the asphalt plant while reducing energy consumption and emissions, moving the industry in a responsible sustainable direction.
It is now possible now to engineer PMBs to specific applications. The Total Styrelf portfolio, for example, includes tailored PMBs such as Styrelf Intakt for resistance to fuel and chemical corrosion, such as that encountered in airfield applications, whilst motorsport-specific Total Styrelf GP is designed to withstand the stresses, strains and shear forces encountered on Formula 1 tracks and has been applied to surfaces such as the Monaco GP circuit.
Sustainability through durability is the responsible direction of the modern supply chain, which is being driven by the current drive for improved highways asset management.
To learn more about bitumen technology, visit the ‘MOOC’ the Massive Open Online Course (www.coursera.org/learn/mastering-bitumen). Developed by Total Bitumen in collaboration with French University Ecole de Ponts of Paris, this course aims to address the knowledge gaps around bitumen technology. MOOC is free to access and can be completed in your own time.
Acknowledgement
The author would like to thank Jonathan Tinsley and Gary Schofield for their contributions to this article.
- Subscribe to Quarry Management, the monthly journal for the mineral products industry, to read articles before they appear on Agg-Net.com