New Low-temperature Bitumen Binder for Asphalt Suppliers
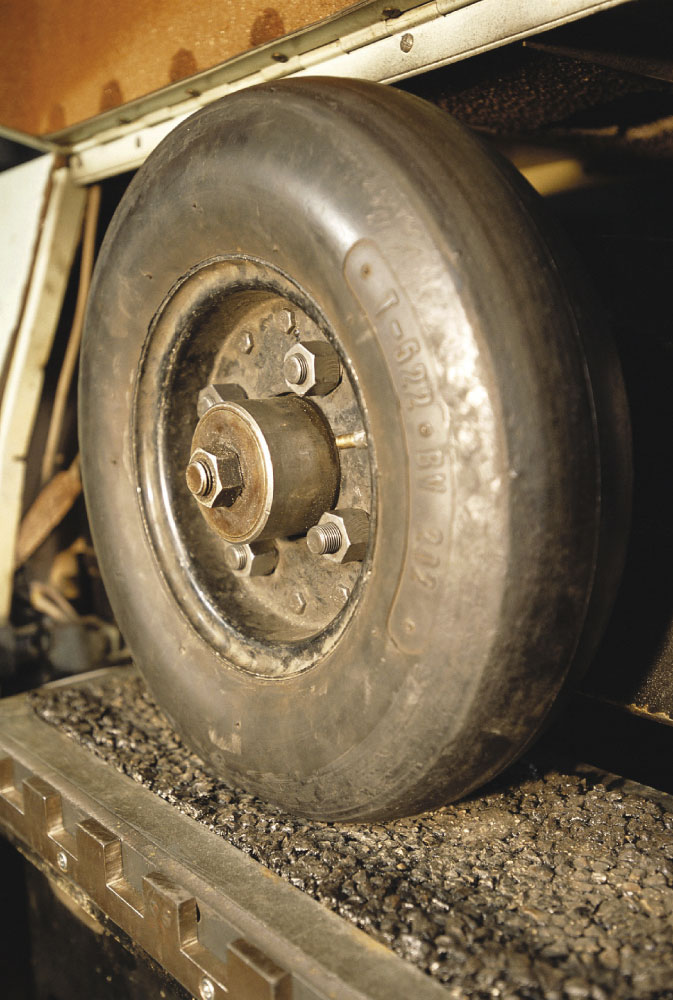
First published in the July 2013 issue of Quarry Management as Enhanced Ecosolution
Azalt ECO2 – a ready-to-use low-temperature binder from Total Bitumen’s Ecosolutions programme – offers a range of operational, environmental and economic benefits
Binder produced in the UK that contains special additives is now being offered by Total Bitumen, allowing asphalt suppliers to mix lower-temperature materials without having to invest in new production equipment.
The company’s new ‘Azalt ECO2’ binder range was launched in the UK last year and typically allows for a 40°C reduction in asphalt mixing and laying temperatures. Tests in France and the UK have demonstrated that the final product offers comparable performance to standard hot-mix materials.
This bitumen’s main benefit is that the binder is supplied with additives already incorporated, which means producers can mix lower-temperature asphalt across a wide range of mix types without having to make a capital investment in modifying their plants. There is no need to inject water or other additives, such as adhesion agents, into the mix, or to foam the bitumen or modify it in any other way during production; it comes ready to use in the conventional mixing process but is simply mixed at lower temperatures. The product can also be mixed at more conventional temperatures without degrading the performance of the bitumen, potentially allowing longer working opportunities for compaction.
Offering an enhanced pre-blended binder to producers of warm-mix asphalt could help asphalt manufacturers save more than £250,000 by not having to fit new hardware, such as spray bars and steam-evacuation equipment, to their plants as is needed with other methods of warm-mix asphalt mixing, according to Total Bitumen’s market development manager, Rick Ashton.
Two trials carried out by Total Bitumen in France during the last two years have demonstrated the binder’s favourable performance in warm-mix applications. Azalt ECO2 was developed at Total’s research centres in Lyon and Preston as part of the Total Group’s Ecosolutions programme.
The first trial site at Blois, in central France, utilized 500 tonnes of Azalt ECO2 modified asphalt for a new surface course on a heavily trafficked route. The asphalt was manufactured at 120°C against a control section of hot mix.
The mixing plant’s bag-house filter was monitored for efficiency and no blocking was experienced. Energy consumed by the burner at the asphalt mixing plant was found to be 35% less with the warm mix compared with hot mix. Overall, airborne emissions were 47% lower during manufacture, helping to reduce airborne odour, which is particularly beneficial in urban environments, while carbon dioxide emissions were down by 30% on stack measurements over the hot-mix control asphalt.
Extensive laboratory analysis of the mixes revealed that the performance of the warm-mix material was as good as, if not better than, the trial control hot mix in terms of compaction, deformation resistance and water sensitivity.
Material featuring Azalt ECO2 was applied to the road in Blois at 115°C and compacted at around 110°C, some 40°C cooler than conventional hot-mix material. In addition to the laboratory studies, after one year an in-situ inspection of the surfacing revealed no visual differences between the Azalt ECO2 asphalt and the hot-mix control section, and no evidence of deterioration in surface regularity or binder stripping. Variations in texture were not apparent between the two mixes, confirming that the material had performed within the tolerances expected for the site.
A second trial site at Rennes, in Brittany, looked to provide further validation of the material’s performance when the product was laid on an access road and parking area used by heavy goods vehicles.
Recycled asphalt pavement (RAP) was included in the material for this next stage of the binder’s environmental assessment, with the surface containing 10% RAP and the base containing 20% RAP.
Close investigation was undertaken to ensure that the binder gave good coating of the aggregate and to see if the mix could be compacted well at a reduced temperature. The warm-mix asphalt was mixed at a temperature of 125°C, applied to both surface and base courses at 120°C and compacted at around 100°C. The surface course used a 10mm nominal aggregate, the binder course a 14mm nominal aggregate.
With the inclusion of recycled asphalt into mixtures becoming increasingly critical to today’s asphalt manufacturers, the latest development work in Holland has introduced RAP to Azalt ECO2 mixes at levels greater than 50% with positive results. This offers manufacturers further economic and environmental benefits.
Energy consumption at the mixing plant in the second trial was reduced by 20% and visual observations of the road after 18 months found no signs of deterioration.
Compaction was actually slightly better on the warm mixes compared with the hot-mix control sections in the trials. This is reflected in some feedback from the US which seems to indicate that where compaction performance is linked to contractual payments, this is acting as a driver in the selection of warm-mix asphalts on certain schemes, with more than 25% of asphalt produced in the US now being warm mix.
Since the two trials were completed around 20,000 tonnes of asphalt containing the Azalt ECO2 binder has been applied at a series of sites across France, from Bitche in the North East to Bordeaux in the South West. In France the product has gone beyond the trial stage and is now recognized as an off-the-shelf, commercially viable binder. Operatives report that they like using Azalt ECO2 modified warm-mix material because it looks and handles so much like conventional hot-mix asphalt.
There is market interest in lower-temperature ready-to-use bitumen that does not require any plant modification or investment, and the strong technical relationships within Total Bitumen’s expanding worldwide activities allow the transfer of technologies from one country to another. As a result, Azalt ECO2 trials have now started in the UK.
Selecting warm-mix over conventional hot-mix asphalt has the advantage of reducing fuel costs and cutting carbon emissions during manufacture. Starting with a cooler material on site means that the road can be reopened to traffic sooner, which is a big advantage when clients are working to restricted hours of traffic management or trying to install thick-lift installations in a single shift.
‘Warm-mix asphalt manufacture is now possible without specialist knowledge, plant modifications or the need to pay on-going royalties,’ stated Rick Ashton.
‘Total Bitumen’s Ecosolutions technology and lower-temperature binders are set to continually evolve in the asphalt market. The next big step for Total Bitumen in low-temperature binder production is the development of Styrelf ECO2 – Total’s low-temperature polymer-modified binder which has already undergone trials in France and will soon do the same in the UK.’
For further information visit: www.bitumen.total.com
- Subscribe to Quarry Management, the monthly journal for the mineral products industry, to see articles before they appear on Agg-Net