New-generation Asphalt Mixes And Plants
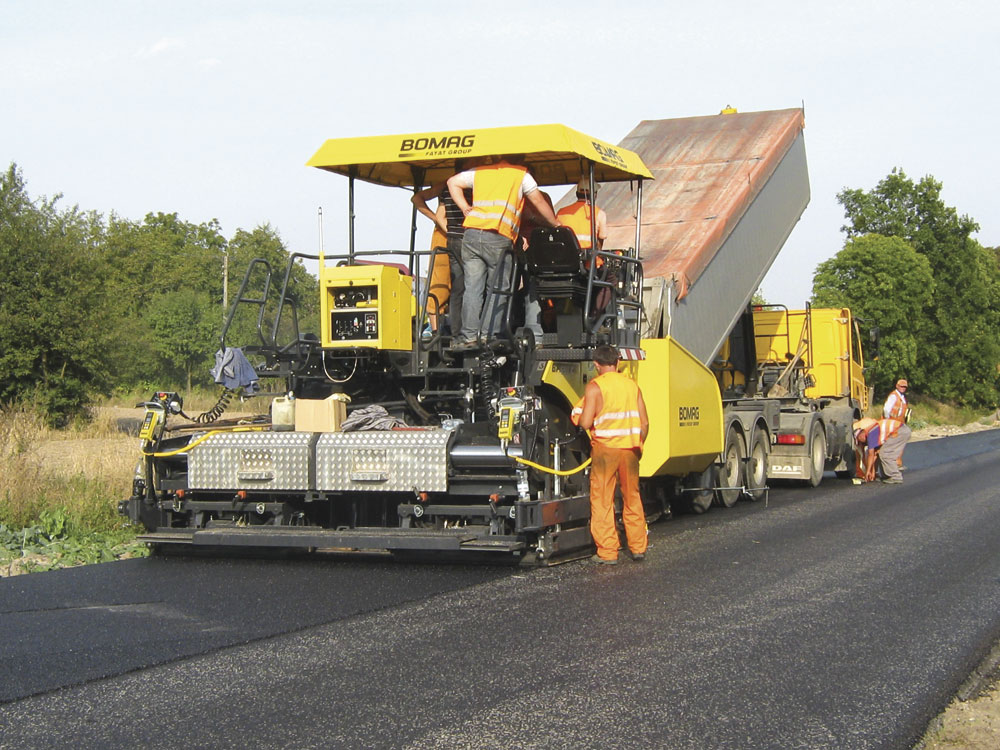
Developments in warm-mix production
Over recent years, a new term has come into usage in the asphalt vocabulary, namely ‘warm asphalt mixes’.
A general increase in environmental awareness means that a considerable amount of attention is now paid to this type of asphalt mix, mainly regarding the reduction of exhaust gases into the atmosphere, in accordance with the directives of the Kyoto protocol.
Recent developments in various warm asphalt mix production techniques have led to the release of a new range of products on to the market.
This, in turn, has resulted in the redesign and modification of asphalt plants, to cater for these new methods and to guarantee that the quality of the final product is, at the very least, equivalent to the quality of traditional hot mixes.
While the production temperature of traditional mixes ranges from 140°C to 180°C, new plant solutions and technical developments have now made it possible to produce asphalt mixes at temperatures between 90°C and 120°C, in complete compliance with work specifications.
Studies in this field were first carried out in 1995 and preliminary trials were conducted in 2000. Today, various well-tested technologies are available that allow work to be effected at low temperatures without compromising plant performance. Moreover, the roads built with this type of product and methodology have now been tested over long periods of time and their behaviour can be considered similar to, or in some ways, even better than traditional asphalt mixes.
But why is there a need to produce asphalt mixes with lower than standard temperatures? First, less energy is required (burner consumption estimated to be in the range of 20% to 40% less) with a consequent reduction in the fumes volume, especially CO2 emissions. As can be seen in figure 1, plant working conditions are considerably improved, with almost complete elimination of emissions and a reduction in the odour of the asphalt (working at temperatures lower than 130°C considerably cuts down on fumes/odour problems).
Of even more importance are the advantages experienced at the work site (fig. 2). Working at low temperatures greatly improves conditions for the paver-finisher workers, the road works can be quickly reopened to traffic, production time and laying time can be lengthened, and aspects of production may be improved, such as the reduction of oxidization with consequent bitumen ageing. Added to this is a reduced environmental footprint, especially in urban areas.
Why is there a reduction in burner consumption? Figure 3 illustrates the linear increase in fuel consumption as the temperature increases. When 100°C is reached a high burst of energy is experienced due to the heat of vaporization (burner consumption is linked to aggregate moisture). Once the aggregates are dried, the temperature continues to increase together with fuel consumption. Therefore, if the production temperature is reduced from 160°C to 120°C, the 40°C reduction in final aggregate temperature results in a saving of around 1kg of fuel per tonne of asphalt produced.
The present state of the art encompasses a range of additives which allow this type of work to be carried out using existing plants without having to make major alterations.
Solid additives may be fed into the mixer in the form of crystals that contain up to 20% of their weight in water, which is then released at temperatures exceeding 85°C, creating a ‘foam’ inside the mixer and encouraging correct bitumen adhesion to the aggregates, even at lower than standard temperatures.
To introduce these additives into the mixer, the plant must be fitted with a pneumatic metering system (trials have also been carried out feeding the additives from sacks on to special chutes, a method which has not, at present, been optimized).
Different types of wax may also be melted into the bitumen. Made from a type of paraffin that is fully soluble in bitumen at temperatures above 115°C, these reduce the bitumen viscosity, thereby allowing mixing at lower temperatures.
The asphalt plant must be equipped with a wax storage system and a system for feeding the wax into the bitumen circuit (alternatively, these waxes may be fed directly into the bitumen tanks but, again, this method has not been optimized, given the difficulty in managing the correct quantities of bitumen and additive).
Several liquid additives also exist that allow bitumen viscosity to be reduced to work temperatures. With this solution, the plant must be fitted with a feed system for metering small amounts of additive into the bitumen weighing receptacle.
There are further interesting technologies requiring considerable intervention on existing plants and/or completions on new plants, but which guarantee even better plant performance than other methods. In particular, the new generation of Marini Top Tower plants are already fitted out for use with all available market technologies (fig. 4).
The double-mixing method is especially interesting. The first mix involves low-temperature aggregates (around 120°C) with high-penetration bitumen, while the second mix involves low-penetration bitumen ‘foamed’ on its special ramp.
This technology allows work to be carried out at very low temperatures and with the incorporation of high percentages of RAP; this method does, however, require major plant adaptation, in particular with regard to bitumen storage (two tanks are required for the two special types of bitumen used), the bitumen feed circuit, water, bitumen ‘foam’ ramp and software management for the whole process.
Another technology utilizes the introduction of wet sand into the mixer. This process again involves two successive mixing processes: first, for mixing large aggregates at 140°C with standard bitumen, and secondly, for wet sands at ambient temperature whose water content creates a ‘foam’ effect and ensures the correct coating of aggregates even at low temperatures.
Excellent results have been obtained with this methodology in terms of energy savings and emission reduction. However, additional equipment must be added to the plant for feeding the sand into the mixer and, above all, equipment is necessary to correctly monitor the whole operation.
Warm asphalt mixes are a response to an attempt to produce a more eco-friendly product and to reduce its environmental footprint.
The difficulty in proving the validity of these products has now effectively been overcome; the main problem faced today is making the practical step of introducing these technologies into the work specifications of public authorities.
Presently, in Europe and throughout the world, ‘asphalt’ means hot mix, but in the space of just a few years asphalt will come to mean warm mixes and, when this happens, asphalt plants are ready and waiting to take part in the green revolution. There are no general rules that apply for all sites and all clients, so Marini’s stated intent is to work as a partner with each client, to analyze production requirements and to adapt each plant to suit each working situation.
Given the importance of this discussion, together with the fact that rising oil prices are making bitumen an increasingly precious product, many companies in the sector are now focused on solving the problem, at least in part, by developing technological solutions which utilize both warm asphalt material and RAP, without compromising the high quality of the final product.