New Asphalt Hot-Storage System for Aggregate Industries
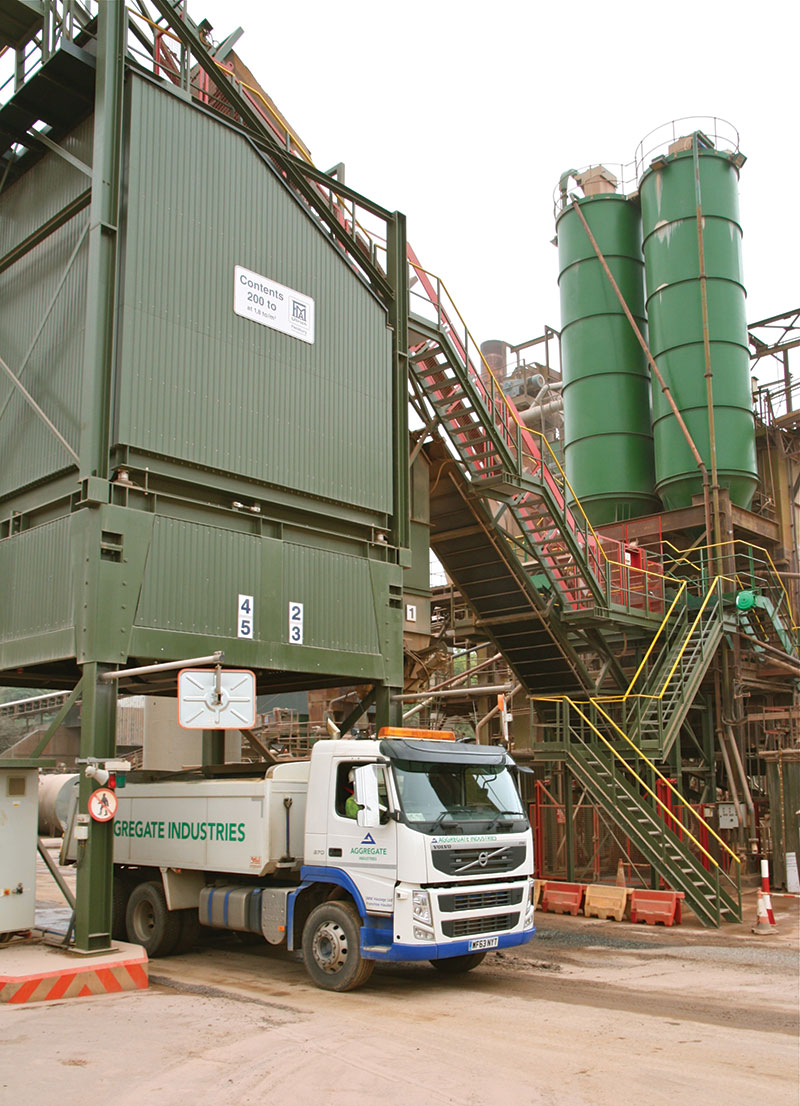
First published in the January 2015 issue of Quarry Management as Hitting the Hot Spot
BG Europa supply new hot-storage system to Aggregate Industries’ Westleigh asphalt plant
Asphalt and concrete plant specialists BG Europa have recently supplied an Ullrich 200-tonne S200/4 hot-storage system to the Westleigh asphalt plant, near Tiverton, Devon. Owned and operated by Aggregate Industries UK Ltd, Westleigh Quarry was well positioned during construction of the M5 motorway, with the asphalt plant installed at the site in 1972. Originally designed as a direct load-out plant with no storage system, over the years it has supplied material for the North Devon Link Road and for ongoing work on the M5.
Currently managed by asphalt area manager Matthew Bishop, it was not long after his arrival that he undertook a feasibility study to see whether the inclusion of a hot-storage system could be justified at the plant.
Mr Bishop commented: ‘Over the years demand has changed. In 1972 there was only base material, roadbase, basecourse and a surface/wearing course, with maybe half a dozen different mixes in total. Today every company wants to sell its best products and diversify into different products, offering customers a variety of solutions.
‘There is increasing demand, therefore, for a variety of materials, making hot storage essential. Sometimes direct loading on to trucks is not the most efficient approach. We needed the ability to load out different materials at the same time, which why we put together a £500,000 proposal to bolt a hot-storage system on to the side of the 42-year-old BG Europa asphalt plant.’
Supplied by Ulllrich agents BG Europa, of Wickhambrook, the new system was installed while the plant remained operational. With the civils completed by Aggregate Industries, the plant was closed off on one side and traffic redirected. Installation of the new system by the BG Europa team was completed on time, on schedule and within budget. The whole project was managed and scheduled on a daily basis by Matthew Bishop, overseen by Aggregate Industries project manager John Richards.
Ullrich 200-tonne S200/4 hot-storage system
The new hot-storage system comprises a four-compartment silo, arranged in a cluster (two 47-tonne compartments and two 53-tonne compartments), which allows the storage of hot asphalt in preparation for discharge to a vehicle via a single loading point. This offers the advantage of allowing all four bins to discharge into a single truck, if required, with the retrofit silo mounted on load-cells to allow accurate weighing of the material.
The Ullrich S200/4 hot-storage system installed at Westleigh offers 200 tonnes capacity at a density of 1.8 tonnes/m³ for a hot mix, and is in the form of a stationary construction connected to the existing 4,000kg batch plant, which has an output of 320 tonnes/h.
The system has numerous features including:
- In-transit weighing of skip and contents
- Automatic winch brake test function
- Skip elevator with automatic or manual operation
- Skipway with foldable skip rails and electric winch to facilitate direct truck loading
- Automatic skip spray system
- Electrically heated silo cones
- Remote-controlled discharge gates suitable for hot-rolled asphalt
- Discharge gates electrically oil-bath heated and regulated by thermostat
- Weighing system for four silos with four load-cells and amplifiers
- Fail-safe discharge door closure with emergency backup system
- Three-stage discharge door control to facilitate accurate and fast loading of small loads.
Major benefits
Specifically designed for short-term (ie overnight) storage, the silo compartments allow the production of material in preparation for vehicle loading. Vehicle waiting time is thus reduced and also, potentially, the number of vehicles required for a project (vehicles do not have to queue at the production site). Vehicles at Westleigh can now load in around 20–30 seconds, whereas loading time used to be around 10 min per load.
Matthew Bishop commented: ‘Essentially, the hot-storage facility increases our capacity; quite simply, 10 lorries waiting for 30 min equates to 300 min of inactivity, which allows trucks to be sent out on a local stone tip and back in the time they would have been inactive. Therefore, it increases the hauliers earning ability as they are not sitting here waiting, so it’s a massive change for them.’
According to Mr Bishop, there has also been a huge reduction in energy use since the installation of hot storage, with average total energy consumption down by 10%. The percentage of material heated and not used in the production of asphalt, but instead returned to stock, has also shown a decrease of 8%, while the RAP percentage has increased by 7.3% on binders and bases, thereby resulting a significant saving when compared with 2013.
‘The saving in bitumen by adding extra RAP has actually increased our profitability and environmental contribution by a significant amount. So now we have the energy saving and the bitumen saving through the addition of more RAP,’ said Mr Bishop.
He continued: ‘When we are processing a run of material it is easier to control our temperatures on production, so we can ramp up the temperatures to add more RAP to the process. With the grouping of production, it allows more time for ongoing maintenance, greasing checks etc. Prior to the installation of hot storage, the plant would achieve a maximum of 1,000 tonnes but now it’s capable of achieving around 1,400 tonnes in a day shift, simply because the plant is running more effectively. We are no longer doing as many individual loads or clean-outs; everything is more concentrated on production. Attention to planning the day before has been the key to the success of this system.’
Flexibility
The new storage system has brought greater flexibility as the plant can now rationalize production. Rather than producing purely for each vehicle, it can now produce longer runs of different materials and retain them in the bins. This helps reduce the number of batch tower clean-outs where the plant has to empty its hot-stone bins in order to produce a material with a different stone type.
Running the batching plant continuously also helps reduce energy consumption, as before the plant had to stop if there were no trucks. Westleigh can now continue to produce and store the material in the bin ready for the trucks to arrive.
Mr Bishop continued: ‘We can rationalize production, produce longer runs of material and hold it in the bin, which, in turn, reduces the number of batch tower clean-outs. We can also group production together; if I have 10mm and 20mm with different PSVs to mix, and I have one load of each throughout the morning, in the old days I would have had to clean out the whole plant when we swapped from one to the other. This meant any stone that had already been heated would be sent back to the stocking area to be put back through the system and reheated at some point, before we could run up new aggregate for the next mix. With the new system we have fewer clean-outs and, as each has a fuel cost, we are more efficient while satisfying our customers at the same time. It completely changes how we do things, especially as CE marking now cancels out fly changing, making hot storage the way forward.
‘Night work at the plant has also changed dramatically. In the past, if we had a large tonnage booked we would not normally have accepted additional orders. However, with hot storage we can bin up the extra order in addition to the night-work commitment. On night work the plant is not required to run as long, as once the required tonnage has been produced and fed into the bins it can shut down, thereby reducing the plant’s night-time environmental impact on the neighbouring community.
‘Overall, the system at Westleigh has been a huge success; the inclusion of hot storage allows greater continuity of mixing, reduced clean-outs, increased volumes, increased flexibility and new collect trade business. We will see a return on our investment within 18 months and as the plant is being operated less, there is also a positive environmental effect,’ concluded Mr Bishop.
For further information visit: www.bgeuropa.co.uk
- Subscribe to Quarry Management, the monthly journal for the mineral products industry, to read articles before they appear on Agg-Net