Modular Machine Design Pays Dividends
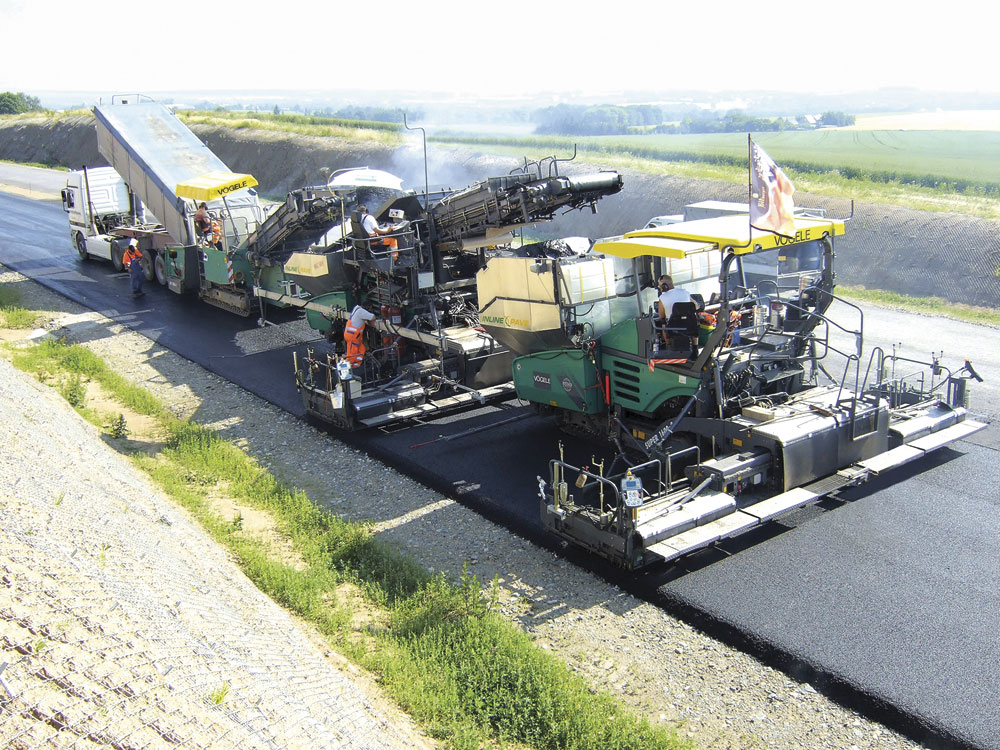
Vögele InLine Pave train used in construction of new Federal highway in Germany
During construction of the B178(n) Federal highway near Löbau, in Germany, the focus was on a high standard of pavement quality, particularly for the asphalt surface course, as well as a high level of cost-efficiency. To ensure fair competition, in letting the contract Bautzen Roads Authority refrained from making technological restrictions by allowing bids for ‘compact pavement construction’ as well as for ‘conventional paving’. Ultimately, however, it was the InLine Pave technique, using two pavers, that won the contract. Particularly high demands were made with regard to the overall quality of the road, as the B178(n) will link the A4 motorway to Poland and the Czech Republic in the Zittau region. A high traffic load is expected with a large proportion of heavy goods vehicles.
The 5.9km stretch of the Federal highway included eight bridges, and six of the bridge decks required paving with a 40mm surface course on top of the existing mastic asphalt. Two other large bridges could not be accessed by the pavers, as construction work had not yet been completed. On the sections between the bridges, the task was to place binder and surface courses featuring perfect bonding and interlocking of layers.
The paving team of contractor Strabag AG, Direktion Strassenbau Sachsen, met these challenges with their InLine Pave train comprising a Vögele MT 1000-1 mobile feeder, a Super 2100-2 IP for paving the binder course and a Super 1600-2 for placing the surface course. According to Strabag, a crucial factor when using this technology is an optimal rhythm in terms of mix supply to the pavers. If this is achieved, the costs of paving can be cut significantly from the very first metre.
‘Hot-on-hot’ paving
Vögele developed the InLine Pave train especially for the innovative ‘hot-on-hot’ paving technique, to build compact asphalt pavements. InLine Pave, however, is equally suited to carrying out conventional paving jobs both economically and to a high standard of quality. With InLine Pave, the binder course and surface course are placed in a single pass, which yields not only a perfect bonding of the layers, but also intense interlocking, both of which are basic requirements for the longevity of the road.
InLine Pave is based on machines of series production that undergo only slight modification for the hot-on-hot paving process. For construction contractors, this means that each machine in the InLine Pave train can also be deployed on conventional paving jobs, thereby substantially increasing both the productive utilization of the contractor’s equipment pool and the return on investment. This also makes the InLine Pave technology an attractive option for medium-sized construction companies.
Paving surface course on the bridge decks
Initially, surfacing of the bridge decks appeared to be a difficult job. However, the InLine Pave technology demonstrated a unique advantage in this respect – its modularity. The machine design allows the MT 1000-1 Mobile Feeder and the Super 2100-2 IP paver for placing binder course to be uncoupled from the InLine Pave train. On the six bridges where just surface course was to be placed, the Super1600-2 operated alone to pave the deck to the specified thickness of 40mm, in the conventional manner. After the bridges had been completed, the three machines resumed work as a team and continued paving hot on hot.
The InLine Pave concept demonstrated an additional advantage. When carrying out secondary work on the highway, such as surfacing approach and exit lanes, the correct individual machine was always available, without the need to move any further machinery on to the job site. This boosted the contractor’s flexibility considerably.
Most of the paving work between the bridges was routine for the paving team. Although the Löbau job was the first time Strabag’s crew had worked with the InLine Pave train, they quickly got to grips with the equipment, largely due to the fact that the paving train is made up of series-production Vögele machines that have undergone only slight modification.
The ErgoPlus operating concept was an important factor in this respect. The paver operators quickly become familiar with the ErgoPlus console, on which paver functions are arranged in logical groups. Once familiar with this system, users can operate all other pavers of the dash-2 generation without any additional training. The team working on the B178(n) Federal highway benefited from this advantage, placing 100mm binder course and 20mm surface course without any problems. The team worked to a width of 7.5m in both highway directions, paving a total area of around 88,500m2.
Perfect evenness achieved
The InLine Pave concept is designed to deliver maximum evenness of the final pavement. The use of two pavers operating separately, each equipped with a floating screed, helps to perfectly level out any irregularities. Moreover, the concept does not make any special demands on the evenness of the road base. A tolerance up to 10mm, usually specified for basecourse, is sufficient for InLine Pave to achieve a final surface of highest accuracy.
On the Löbau contract, the paving team worked with a Niveltronic Plus system for automated grade and slope control, combined with a modern sensor system from Vögele. The paver placing the binder course was equipped with a Big MultiPlex Ski to scan the road base, which served as a reference for grade and slope control. A particular advantage of this system is that even long irregularities, such as undulations, can be reliably levelled out. The combination of the paver’s self-levelling capability and the Big MultiPlex Ski meant that excellent results were achieved and the contracting authority was fully satisfied with the pavement quality.
Final density produced with HAMM oscillation compaction technology provided excellent interlocking of the two hot-on-hot paved layers.
Following immediately behind the paving train, two Hamm DV 90 machines, one with an oscillating roller, produced the final density of the new asphalt pavement. For InLine Pave asphalt packages, the superiority of compaction with an oscillating roller is primarily due to the relative thicknesses of the two layers. In conventional asphalt paving, the thicknesses of binder and surface courses are 80mm and 40mm respectively, but when placing two layers hot on hot, binder and surface course thicknesses are 100mm and 20mm. According to Gerd Lenz, applications consultant with Hamm, the load exerted by vibratory compaction is so great that the thin surfacing could be displaced. The use of oscillating rollers avoids this risk; the pavement is compacted dynamically and quickly, achieving a perfect surface finish and an excellent initial grip.
This was the end result on the Löbau job: the DV90 VO roller operating in oscillation mode produced the specified density after just three passes, while the DV90 VV vibrating roller operated in static mode.