Instant Impact
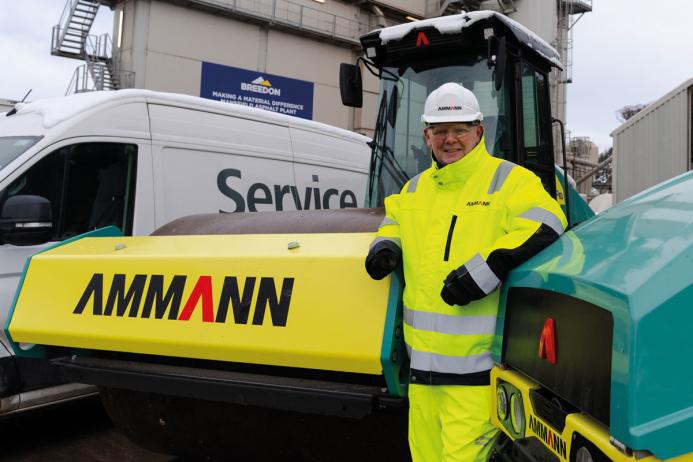
First published in the January 2025 issue of Quarry Management
The relationship between OEMs and materials producers has traditionally been a transactional one, with the customer taking full responsibility for the performance, reliability, and maintenance of their equipment and assets. However, aftermarket support has become increasingly important in today’s asphalt and road construction industry, and the supplier/client relationship is now much stronger and more collaborative. David Hunt, managing director of Ammann UK, talks about the company’s long-term commitment to providing a complete service to its customers, ranging from project planning and plant optimization to full servicing and maintenance agreements
Established in 1869, Ammann have come a long way over the last 156 years and, as a new calendar year begins, the company shows no signs of slowing down anytime soon.
What started out as a mill workshop in Madiswil, Switzerland, is now a major global OEM that operates in more than 100 countries, employs over 3,500 people worldwide, and supplies a comprehensive product range of industry-leading equipment for road construction, transport infrastructure, and sustainable asphalt production and recycling.
Still family-owned, Ammann’s story is a testament to humble business beginnings. Hans-Christian Schneider – current chief executive officer of the Ammann Group – is the sixth generation to run the company and, under his strategic direction, the Swiss manufacturer continues to be at the leading edge of innovation in the mineral processing and road construction sectors.
The UK’s journey towards a more sustainable building industry is well under way as challenges surrounding climate change have become paramount, with the Government driving policies to reduce carbon emissions and meet net-zero targets. Technology trends such as digitalization, artificial intelligence (AI), electrification, and the use of drones are already being embraced by construction materials suppliers large and small.
Such key investments play a pivotal role in helping materials producers to not only reach their net-zero emission targets, but also to stay competitive, increase their customers’ green credentials, forecast future production levels, and reduce operating costs. In the asphalt and road-building industry, Ammann products are specially designed with sustainability as a top priority.
‘As a forward-thinking and innovative organization, we are deeply committed to providing the best and most environmentally driven technologies to our customers,’ commented David Hunt, managing director of Ammann UK. ‘Delivering technological solutions and product innovations which prioritize sustainability – from reducing fuel burn and CO2 emissions to using more recycled content – are key to our business strategy and approach.
‘In the asphalt and transport infrastructure industry, equipment reliability is critical. Every hour of downtime leads to lost production and increased costs – and our goal is to develop game-changing sustainable solutions that can help our clients boost productivity, reduce machinery downtime, and maximize profitability.’
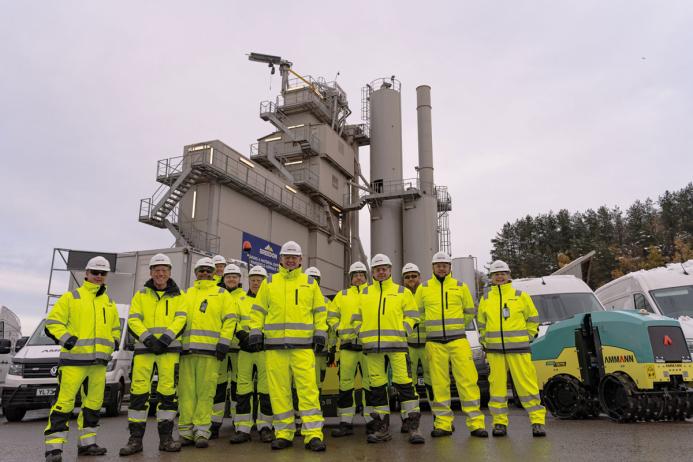
Sustainability promise
At Hillhead 2024, Mr Hunt said last year’s record-breaking show provided the perfect platform for bringing new/prospective customers up to speed with the company’s innovative products and service offerings, whilst keeping them informed of the latest technological advancements in asphalt production sustainability.
Visitors to the Ammann stand were able to see a wide selection of pioneering sustainable technologies and how these product developments and innovations are reshaping the road construction and mineral processing sectors.
‘As a renowned global equipment manufacturer, it is imperative to exhibit at major international trade events such as Hillhead to show customers – new or old – how we can help them transition to a lower-carbon future,’ remarked Mr Hunt. ‘With environmental sustainability at the core of our business growth strategy, it was important to share our carbon-reduction story with customers and take them through the product innovations and updated equipment available from Ammann.’
Demonstrating their sustainability credentials, and accelerating their green efforts, the ‘Green Plant Initiative’ is Ammann’s renewed commitment to reduce or halt CO2 emissions at every stage of asphalt production. At Hillhead 2024, the company’s stand provided attendees/customers with a chance to learn more about its eco-friendly asphalt production efforts, including emissions abatement technologies.
These included Ammann’s innovative H2 hydrogen burner – the first asphalt-mixing plant burner on the market capable of utilizing 100% green hydrogen. It eliminates all CO2 emissions associated with the burner and can use other fuels (eg tall oil, wood dust etc.) if required. Visitors to the Ammann stand also showed strong interest in the company’s electric-drive compaction equipment range, such as the eARX 26-2 light tandem roller and eATR 68 Rammer.
Mr Hunt said: ‘Ammann have a long-standing reputation for pioneering environmentally friendly asphalt-mixing practices, manufacturing high-quality road construction equipment, and helping customers to find the best materials-processing solutions. We are constantly developing new products and sustainable technologies that lower the emissions and energy usage of asphalt plants, whilst making a positive impact on the environment.
‘As the road-building and transport infrastructure industry continues to innovate and reduce its carbon footprint, we will anticipate future challenges and support the acceleration of our customers’ journey towards net zero. We recognize that we – as a leading OEM in the sector – have a pivotal role to play in shaping our industry’s approach to sustainability and delivering low-carbon, energy-efficient asphalt production methods and products.’
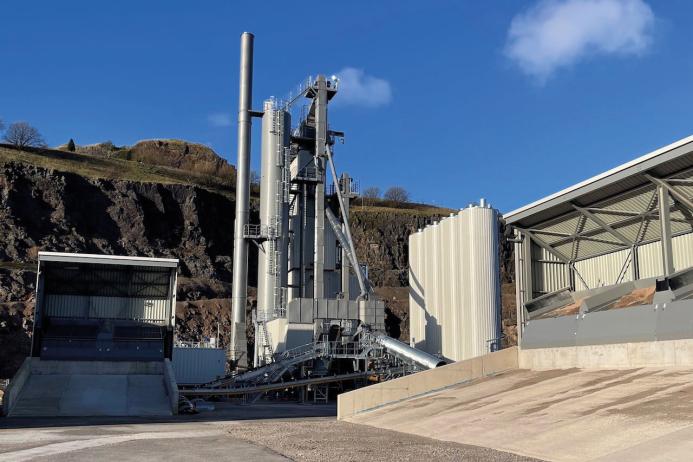
Staying ahead of the curve
Over the next few years, the mineral products sector will go through enormous changes as it embraces emerging technologies and innovative approaches to drive efficiency, sustainability, and circular economy practices. Managing equipment effectively, addressing the much-publicized skills shortage, and reducing operational/production costs are just some of the critical challenges facing the road surfacing and transport infrastructure industry.
To align with these changes and meet the latest requirements from authorities and customers, more and more heavy-side building materials producers/suppliers are outsourcing key tasks, such as asphalt plant optimization and maintenance, to OEMs and equipment suppliers/dealers.
‘Preventive maintenance and aftermarket service support have become much more important in today’s quarrying and asphalt sectors,’ emphasized Mr Hunt. ‘The OEM/customer working relationship is no longer a transactional one, but one that now fosters a stronger and collaborative approach. Keeping our clients at the centre of our business has always been, and continues to be, a core focus for Ammann – and in the British and Ireland markets that’s something I want Ammann UK to lead on.’
With more than 28 years of experience in the highway maintenance and road surfacing sector, Mr Hunt is a familiar face in the heavy building materials world, having worked for several industry majors. He has held a variety of operational, supervisory, and management roles, and his extensive asphalt experience and background ranges from plant operation and maintenance through to project management and, ultimately, sales.
Like all directors, Mr Hunt is clearly excited by the commercial prospects and challenges that lie ahead in the asphalt and road construction segments and believes Ammann UK are in a better position than ever to help customers achieve higher equipment uptime, improve workplace safety, minimize operating costs, and support materials suppliers with their carbon footprint reduction programmes.
‘Over the last year, we have invested significantly in ensuring the company has the right service support infrastructure in place to provide a wide range of sales and aftermarket offerings and ensure that UK and Ireland customer requirements are dealt with more rapidly and efficiently than ever,’ he said. ‘Importantly, we now have a highly skilled and vastly experienced team of eight mobile service engineers strategically located across the country – 12 months ago we only had two service engineers.’
A major part of Ammann UK’s business growth strategy is to provide an unrivalled total-support offering to their customers, and much of this ambition – according to Mr Hunt – can be achieved through partnership, collaboration, and transparency.
‘For us to compete, we need to be a lot more proactive in supporting our UK customers in all aspects of sales, service, aftermarket support, and spare parts,’ he explained. ‘In the European Union, delivering full-service backup and after-sales support is not the same as the UK asphalt market. In Continental Europe, they have a completely different mindset to the British industry, whereby materials production facilities shutdown for months at a time and are doing significantly less output than their UK counterparts.
‘Many maintenance service contracts and breakdown plant repairs are also carried out in-house, whilst in the UK and Ireland construction materials firms and road-surfacing contractors are increasingly looking to OEMs/plant suppliers to provide ongoing maintenance support and take responsibility for the optimal performance of their equipment assets.
‘With the mineral products sector changing at a rapid pace and new technology becoming available, we have taken strategic steps to increase our competitiveness and offer enhanced after-sales services to our UK clients, which may not have been of the finest in the past.’
To help optimize asphalt plant performance and reliability in the field, Ammann UK have boosted their customer-support services, which range from comprehensive site surveys and rapid breakdown response cover to preventive-maintenance packages and full technical support.
Greater access to a vast stock of genuine spare parts and the delivery of the equipment are equally important, and Mr Hunt has worked rigorously to improve stock control and parts availability for the company’s UK and Ireland operations, to ensure it offers the best aftermarket service possible.
‘Rock-to-road’ ethos
Choosing an OEM who understands the rigorous demands of the asphalt, aggregates, and road surfacing segments and the environment in which customers are working is paramount.
As part of their rock-to-road philosophy, Ammann are always innovating and continuously improving their product offering by establishing a ‘one-stop-shop’ for all equipment needs, wears and spares, and aftermarket support in the highways construction and mineral products sector.
The company has a long-standing reputation for manufacturing and supplying industry-leading asphalt/concrete plants, pavers, and light and heavy compaction equipment, not to mention delivering lifecycle solutions to meet their customers’ materials processing needs.
Among Mr Hunt’s key responsibilities as Ammann UK managing director is to further strengthen the Ammann brand and consolidate the business’s position in the core markets it serves.
‘The streamlining of the company’s internal structure and operations in the UK has been a significant factor in enhancing our efficiency, driving growth, and providing complete road-building solutions for the industry,’ said Mr Hunt. ‘Having listened to feedback from our customers and recognizing the current market trends, I saw a natural opportunity to further develop the business.
‘Ammann UK is now a larger, more diverse organization offering cradle-to-grave solutions – giving us unparalleled expertise and capability to deliver complete turnkey packages from the earliest stages through to ongoing operations.’
Indeed, these include planning, design and specification; sourcing and supply; groundworks and civils; fabrication and mechanical engineering; build and installation; testing and commissioning; plant operation; continuous improvement and maintenance; and refurbishment and relocation.
While there are many OEMs and plant suppliers offering similar construction options in the industry, Mr Hunt pointed out Ammann are always on the front foot when it comes to delivering bespoke innovations and developing zero-emission technologies for their customer base.
‘The future in the UK and Ireland looks very bright and for us there has never been a better time to be operating in the aggregates, asphalt, and infrastructure sectors,’ he commented. ‘We have the technical expertise and experience to solve the most complex engineering challenges and help our customers deliver the lowest-cost-per-tonne production in the safest and most environmentally friendly way.’
Last year, Ammann UK commissioned an asphalt plant at Aggregate Industries’ Cauldon Low Quarry in the Staffordshire Moorlands. Providing asphalt for ongoing road maintenance and infrastructure projects across Staffordshire, Derbyshire, Cheshire, and the M6 corridor, the Ammann ABP 240 Universal asphalt-mixing plant has been an instant success for AI and was chosen for its reliability, flexibility, efficiency, and sustainability.
The Cauldon Low plant – which can produce up to 240 tonnes of asphalt an hour – has the capability to accommodate high volumes of RAP (reclaimed asphalt pavement) for reuse in new products, whilst the supply of stone from the adjacent quarry has reduced lorry movements and carbon emissions.
The modern production facility is also equipped with the latest environmental technology and highly energy-efficient systems, resulting in less noise, dust, and odours, as well as a 30% reduction in carbon emissions compared with a traditional asphalt plant.
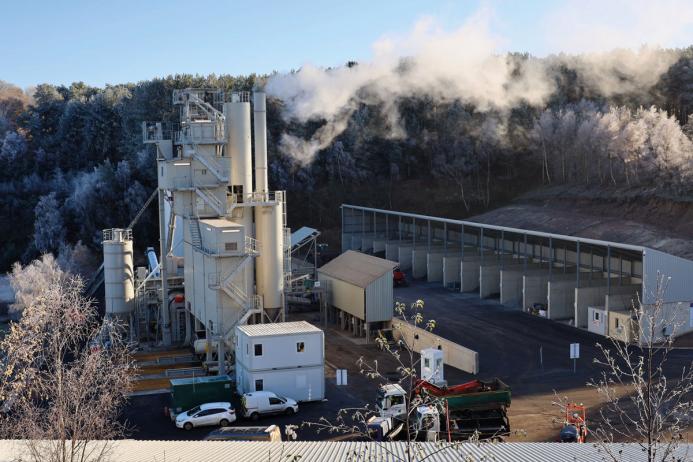
Other high-profile plant installations for Ammann UK include: Breedon Group’s ABA 260 UniBatch asphalt manufacturing facility in Mansfield, Nottinghamshire; and a brand-new high RAP-capability asphalt-mixing plant in Belfast, Northern Ireland, for building material producers Northstone.
Public sector spending on UK road maintenance and transportation projects is expected to rise in 2025 and Mr Hunt is delighted with Ammann’s recent acquisition of Volvo Construction Equipment’s ABG paver business.
‘Building on Ammann’s legacy of technology and innovation with market-leading products and a strong focus on the customer, ABG pavers and screeds are a highly complementary fit to our product portfolio,’ he commented. ‘ABG is a strong brand synonymous with cutting-edge technology, quality, ease of operation, and reliability. The acquisition will enhance our existing construction equipment offering and establish Ammann as a leader in the global road infrastructure sector.’
The UK mineral products and transport infrastructure industries have made huge strides towards the delivery of sustainable roads and Ammann have a vast range of advanced products, low-carbon emitting technologies, and customer support services encompassing the whole value chain, from asphalt processing, mixing, and recycling to paving and highways rehabilitation.
For Ammann UK, one of the major areas of emphasis going forward will be the continued drive towards delivering a superior customer experience, as Mr Hunt concluded: ‘We have closely analyzed and monitored every aspect of our business in the UK and Ireland to find ways in which we can better work with our dealers, supply chain partners, and customers.
‘All of our aftermarket programmes and services dovetail into pillars of safety, productivity, energy efficiency, and environmental sustainability. We pride ourselves on providing our clients with cutting-edge sustainable solutions in line with the latest thinking on low-impact road construction. And I am confident that Ammann’s global leadership, technology, innovation, and research and development resources will significantly improve the services we offer our customers – driving forward our mission to provide the best products in the industry and become the partner of choice for the UK’s critical infrastructure delivery.’
Watch the full interview on Agg-NetTV
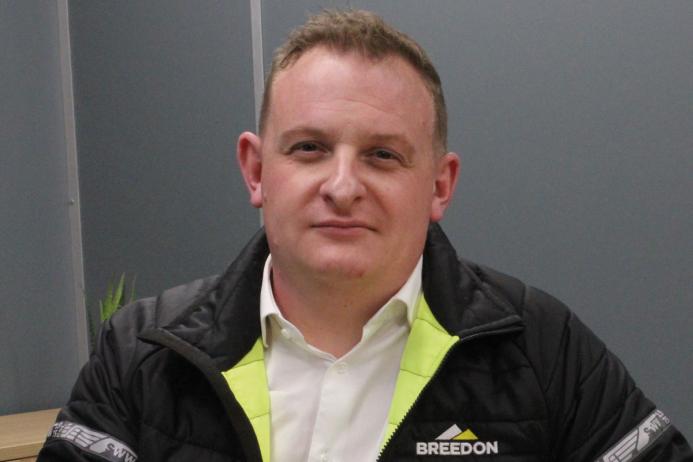
Mansfield asphalt plant revisited
Two years ago, QM reported on Breedon Group’s investment in a new, state-of-the-art Ammann ABA 260 UniBatch asphalt mixing plant in Mansfield, Nottinghamshire. Replacing an earlier plant that was no longer efficient or economical to run, the new plant was designed with a strong focus on sustainability, reliability, and efficiency. Last month, we caught up with Matthew Gelsthorpe, Breedon’s aggregate and asphalt operations manager - Midlands, to find out whether the plant is living up to expectations.
‘Two years on, I’m delighted to say the plant is going better and delivering more than we ever thought it would,’ he said. ‘It’s had a massive impact on production. The output we are achieving at the end of 2024 is 40–50% more than we originally envisaged when production commenced at the start of 2023. In terms of fuel consumption, we are now saving 3–4 litres/tonne, compared with the previous plant. Also, having variable-speed drives throughout the new plant means we’re no longer running motors flat out all the time, so our electricity consumption has fallen too, yet our tonnage is up. The additional value this has delivered was an unexpected and pleasant surprise.’
Mr Gelsthorpe added that the EcoView software module incorporated within the plant’s future-oriented Ammann as1 control system had proved crucial in reducing energy consumption and optimizing production, providing key operational performance indicators such as fuel consumption and aggregate wastage. EcoView’s intuitive display provides the plant operators with all the data they need to adjust throughput and material control to maximize savings and efficiencies. It also determines the values of emitted CO2 and calculates the resulting energy costs when adjustments are made.
‘In terms of sustainability, the reductions in energy consumption have driven down our CO2 emissions massively,’ continued Mr Gelsthorpe. ‘Moreover, we’ve been able to utilize a far greater percentage of recycled asphalt planings (RAP) in our mixes than we expected. The plant’s RAH50 system is designed to allow the introduction of up to 50% cold RAP into the dryer, but we’ve been able to keep pushing this and have gone way beyond the 50% mark with no problems at all.
‘Reliability within the entire plant has been exceptional. A few teething problems were always to be expected in the first few months, but since then the plant has gone from strength to strength and both it and Ammann have really delivered. The Mansfield operation runs 24h a day and the team at Ammann are happy to provide round-the-clock support if required – no one else does this. The project has gone better than any of us could have hoped for and has surprised us all. The plant itself just keeps on delivering and I think it still has a lot more to offer.’
‘Over the last two years we’ve had a great relationship with Ammann. They’ve worked with us to provide both off-the-shelf and bespoke additions and solutions at Mansfield, as well as at several of our other asphalt sites, including a new RAP system for Corby in 2023 and a current full-tower RAP retrofit project for our site at Longwater, Norwich. Going forward, we are also looking at other new asphalt plants with Ammann. Their products, reliability, and support have made a big impact for Breedon.’
Subscribe to Quarry Management, the monthly journal for the mineral products industry, to read articles before they appear on Agg-Net.com