DP Cold Planing invest in Cat cold planers
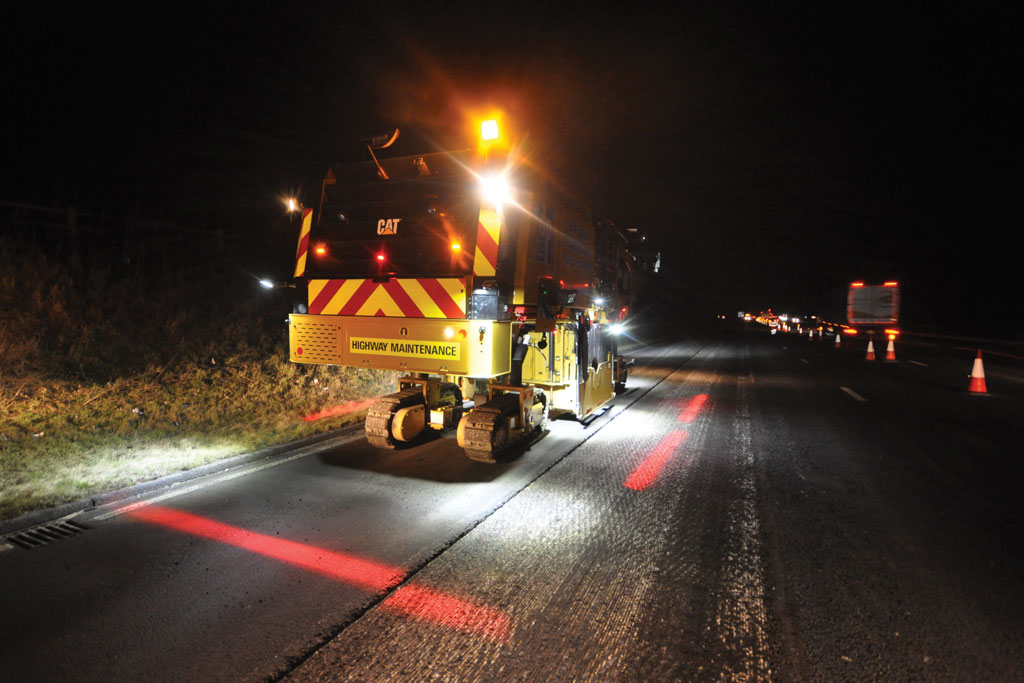
First published in the January 2019 issue of Quarry Management as Planing it Safely
DP Cold Planing drive industry forward following purchase of new safety-focused Cat PM620 cold planers
As part of their continued expansion, national road planing specialists DP Cold Planing Ltd have been putting their new safety-focused fleet of Cat PM620 cold planers to the test, completing numerous projects, including nightworks on a stretch of the M6 motorway.
With the cold-planing sector undergoing significant technology-driven change, in addition to playing a much bigger part in the circular economy of road maintenance, it is important that the sector develops a much more sustainable vision for the future by being able to reuse the valuable aggregates that make up the UK’s road surfaces.
‘Making the right blend of technology, economics and sustainability is all part of a much longer-term vision for the future,’ said director Anthony Prescott, who has overseen the development of a network of recycling facilities across the UK.
His vision for DP Cold Planing is clear: ‘It’s all about balancing the recycling capabilities we have as a business, without simply adding road miles by centralizing an operation into one big site.
‘We also know from our experience that different parts of the country use different aggregate mixes for road surfaces, so it is important to be able to effectively manage stockpiles to meet grades and demand. Having now opened up a fourth recycling facility, we have the capability to recycle more than 400,000 tonnes of road aggregate a year.
‘All the materials we produce are now recycled, and I’m sure we will be cold planing and recycling them again in the future. This is why, when we recently looked at how we would move the business forward with new innovations and technology, we sought a more collaborative approach to working with a partner that could embrace our transformational vision.
‘In doing this, we focused on how we could, first, deliver the best and safest working environment for our staff, and, secondly, ensure that by doing this we were also having a positive impact on productivity and the overall quality of work.
‘For example, a lot of the work in our sector is carried out at night, all year round, using large equipment. So, when we made our recent decision to purchase our first ever fleet of Cat PM620 cold planers from Finning, it was driven by our own goals to make ourselves future-proof. This meant having flexible equipment that was road, motorway and 3D machine control ready, as well as capable of being adapted to our own enhanced vision of health and safety on site.’
Combining light and sound for enhanced safety
Mr Prescott continued: ‘By working with Finning and Caterpillar we were able to model and install a new, innovative lighting system that tackles two very important safety aspects of machine operation, the first being to establish a visual safety ‘red light’ zone around the machine for both operatives and site equipment, and the second to combine visual and audible reversing indicators.
‘Designed in collaboration between our experienced site operatives and Finning engineers, this solution has combined with our use of radio communication headsets on site to deliver a complete solution, which has already had positive feedback from our own staff and customers.’
Letting the machines do the talking
‘With our staff also finding the new touch-screen control technology beneficial, our set-up times have been reduced and we have noticed a quite dramatic difference in cutting tool wear. But what is really interesting and will be more important in the future, is how the machines themselves are talking to us through the Cat Product Link GPS monitoring system, which is fitted to each unit.
‘Product Link feeds information on the location and health of the machine to both our staff and the Finning Finsight engineering team in Cannock. This allows us to monitor each machine and also send alerts when there are service or maintenance requirements. Although the machines are only a few months old, I can see the benefits of this information in the future, as we rely heavily on uptime and availability in this industry.
‘If we can see trending data that shows a machine will need maintenance down the line, when the weather inevitably prevents work taking place, our fitters or Finning engineers can be called upon to do this work, reducing downtime. This is particularly important, with machines potentially being anywhere in the UK.
‘So, when we start 3D planing, technology will help us achieve even greater accuracy, whilst ensuring our trucks are correctly loaded with the right amount of recycled aggregate, to fulfil our customer needs and help us deliver our circular economy vision.’
For more information visit: www.finning.com
- Subscribe to Quarry Management, the monthly journal for the mineral products industry, to read articles before they appear on Agg-Net.com