Building The Road To Improvement
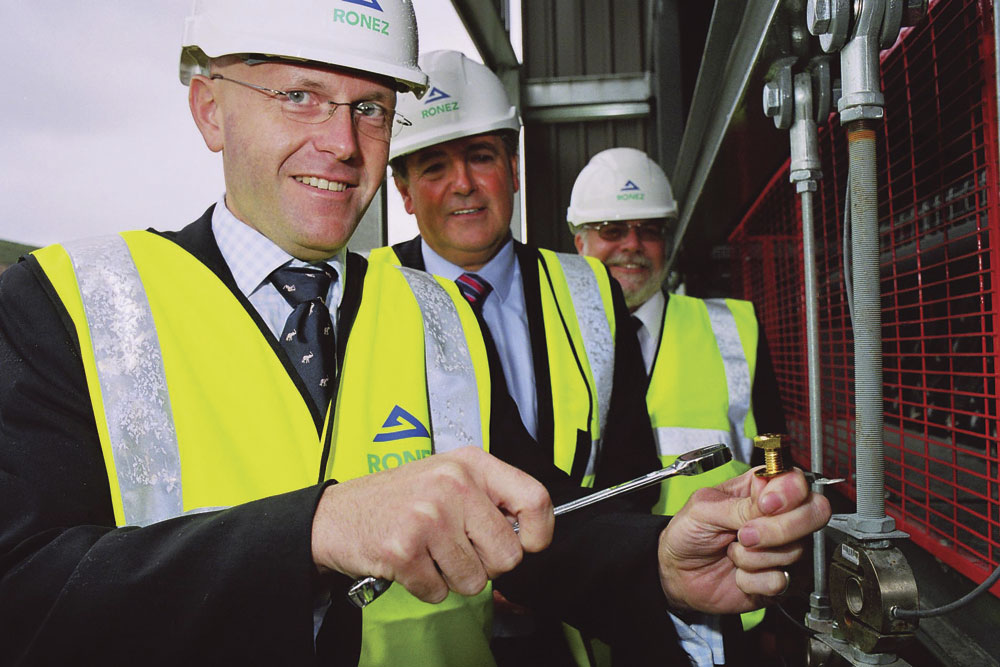
Ronez Ltd choose an environmentally compatible KVM asphalt plant to maintain Jersey’s roads
In September 2005 Jersey-based Ronez Ltd (a subsidiary of Aggregate Industries) began asphalt production from a brand new 25m-high plant. Manufactured and installed by Danish firm KVM International A/S, the finished plant was commissioned on time and ready for production at Ronez’s St John Quarry within two years of planning permission being granted.
The state-of-the-art plant is the result of co-operation between KVM and Ronez, and is more fuel-efficient, quieter and more environmentally friendly than the unit it replaces. With a capacity of up to 120 tonnes/h, the new plant uses technology and innovations in asphalt and macadam production that were not available when the old asphalt plant was constructed. As well as using less fuel, it also creates less dust, makes half as much noise as its predecessor and, even more importantly, recycles asphalt for reuse on the island’s roads.
Ronez are Jersey’s biggest producers of bituminous macadam, most of which is used by the company’s Road Contracts Division in surfacing the island’s roads. With the division playing a major role within Jersey’s infrastructure services, the views of the island’s politicians and the general public also had to be taken into consideration.
Lee Goulder, Ronez’s general manager, said: ‘The new plant has received a good response from Jersey residents and politicians, as well as the industry. Every year, tonnes of waste asphalt are dug up from Jersey’s roads during resurfacing work. The new plant has reduced the environmental impact and allowed the company to provide Jersey’s construction industry with a more efficient and environmentally friendly service.’
The asphalt plant is the latest addition to St John Quarry where, as well as an extensive quarrying operation, there is a modern, quality-assured concrete-batching plant and a computer-controlled block-making facility.
Plant specifications
Aggregate is fed to the asphalt plant via an 11m3 six-compartment feed hopper. A 500mm wide variable-speed belt feeder regulates the feed from the hoppers; material is then discharged on to a dryer slinger conveyor that feeds the drying plant. Fitted with a RAP system, allowing up to 10% recycled material to be added to the mix, the plant comprises a 2m diameter insulated dryer running on individually driven polyurethane rollers. Featuring a 9.3MW gas/oil burner and a double-skinned fuel tank, the dryer drum can be accessed from both ends via a service platform for ease of maintenance.
The plant is equipped with a 40,000m3 capacity, low-energy consumption KVM type-S8-40M bag-filter system with frequency-controlled ventilator and a 37kW variable-speed fan, providing a guaranteed maximum emission of 20mg/m3.
Heated aggregate discharged from the dryer is delivered to the top of a 2,000kg capacity 120 tonnes/h Viking 2000H mixing tower. A bucket elevator discharges the hot stone into a totally enclosed 1.25m x 4m screen. Screened aggregate is then discharged into an insulated six-compartment, hot-aggregate bin section with continuous level indication and overflow pipes to a hopper. The mixing tower is equipped with four load-cell-mounted scales that weigh the aggregate, bitumen and filler, colour pigments and fibre pellets; the latter two being held in two 2.5m3 storage silos. The aggregate and bitumen scales hang freely inside an enclosure to eliminate interference from auxiliary exhaust or any other changes in internal/external pressures. A 40m3 silo is used for the storage of reclaimed filler, with tanker load-out and a filler conditioner for disposing excess filler.
Bitumen storage comprises two 60m3 vertical electrically heated bitumen tanks with submerged pumps.
Weighed ingredients are dispensed from the various weigh scales into the plant’s twin-shaft paddle mixer. Once mixed, the material is discharged into a horizontal, self-propelled, variable-speed skip for delivery to a 33m3, 60-tonne capacity mixed-material section. This is divided into two 25-tonne and one 10-tonne silos, all operating on one set of load-cells positioned below the mixer.
Designed for one-man operation, the plant is controlled by a PC/PLC-based control and management system type-KVM 3000 that includes an energy program, data back-up on to CD-Rom and ‘round-the-clock’ service assistance via telephone modem to KVM’s central PC.