Asphalt Economics
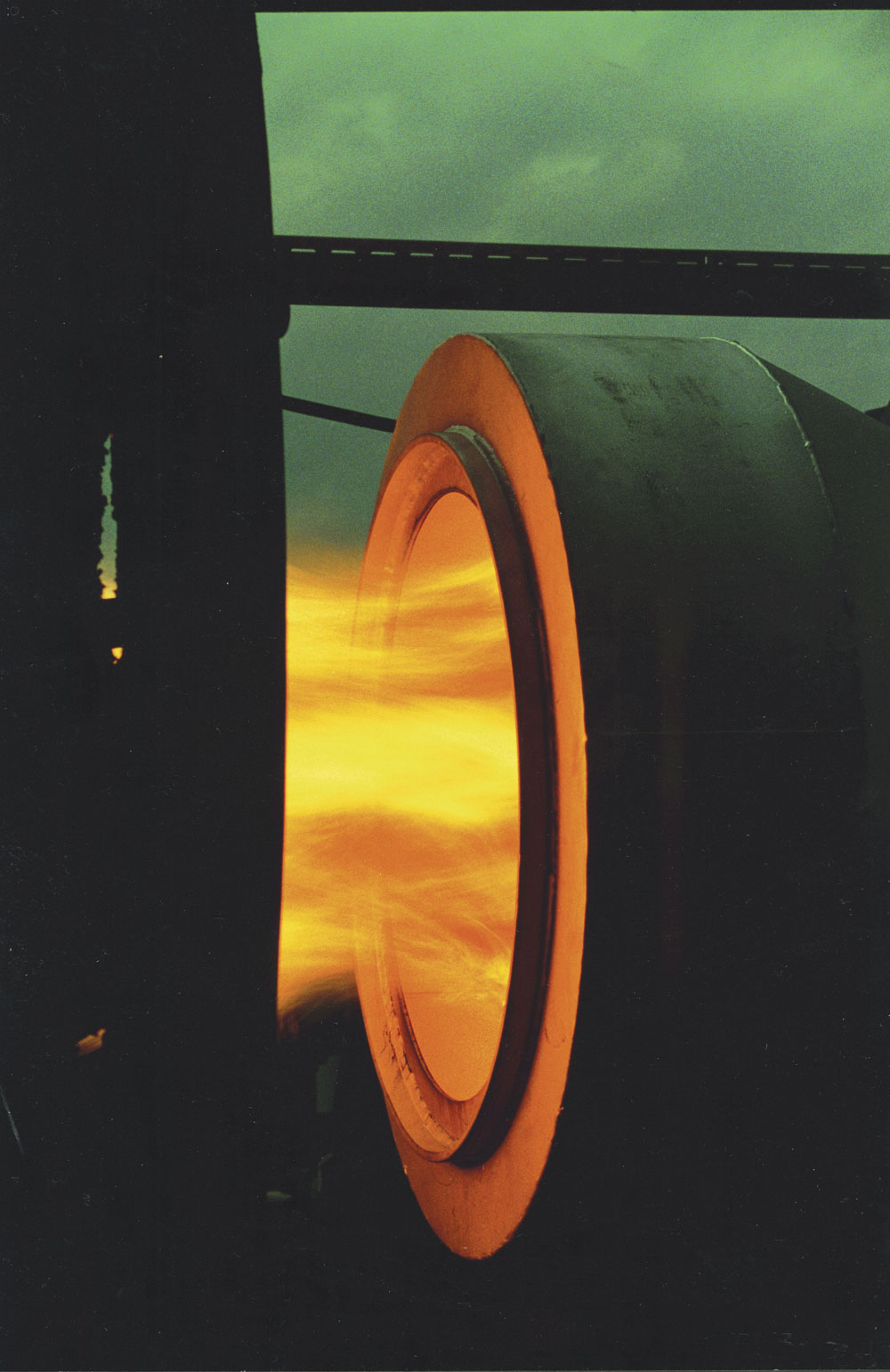
Harold Wylie of Enviroflo Engineering Ltd explains how to turn a commercial downturn into an upturn, by ‘not burning money’ in asphalt plants
In any production downturn the natural reaction is to reduce overheads in as many areas as possible. Reduction of labour, operating hours, consolidation of production assets and reduced margins on product sales are all examples of familiar tactics. Historically, however, the production process itself was hardly ever analysed and little research was directed towards the production costs involved. The question ‘Can these costs be reduced?’ was rarely asked, but from Enviroflo’s perspective, the answer is yes.
Enviroflo Engineering Ltd – now a NALCO company – have been involved in the aggregates and coated materials industry for more than 30 years. In addition to providing dust control for crushing and screening plants, the company offers bag filters for asphalt plants. As a result of their vast experience in this field, Enviroflo have become experts in the above processes and are often called upon by leading quarry companies to correct process problems, in a consultancy capacity.
The aim of this article is not to lecture companies on how their businesses should be run, but to try and quantify the effects of thermodynamics associated with rotary dryers and the influence of moisture in both virgin aggregates and RAP.
Crushing and screening aspects
Generally, there are few cost savings to be made during the mechanical process of crushing and screening, provided that the crushers are appropriate to the aggregate and have been optimized to perform the required task, and that the screening is laid out in a logical manner. If aggregates are to be stored externally it is of paramount importance to keep them as dry as possible, preferably in covered stockpiles. Sometimes ground stocks are badly positioned in low-lying areas, preventing drainage of excess moisture.
Coating plants
The majority of savings associated with coating plants relate to moisture content in the aggregate feed to the dryer. The graph in figure 1 illustrates the high cost of allowing moisture into aggregates that are to be used for coating. As an exercise, operators should calculate the cost of fuel based on their annual production and using their average moisture content. The conclusion is often staggering but rarely is anything done to stop this haemorrhage of cash from the production process. It is also worth remembering that moisture in the feed material will also reduce production rates, requiring the plant to run longer to achieve daily outputs. Moreover, steam produced in the dryer reduces the amount of air available for combustion. At the design stage, the bag-filter system will need to be increased in size in line with increased moisture in the aggregate and filter, and the fan will also need to be larger and will require more power.
There is often a tendency to fit an oversize dryer on an asphalt plant to ensure it is capable of drying the aggregate at a given rate. This philosophy is flawed as the aggregate should have its moisture content reduced, thereby allowing a smaller dryer to be fitted with the resulting savings in capital, power and operating costs.
The graph illustrates the approximate costs of heating up aggregate based on moisture content. It illustrates the fuel consumption per tonne of aggregate on the left-hand side and the cost per tonne on the right-hand side, based on both gas oil and reclaimed oil.
Recycling of RAP
The introduction of RAP is now commonplace in the UK. It conserves new aggregates stocks and a certain quantity of the original bitumen can be assumed to be in the planings, thus reducing virgin bitumen addition by up to 1%. In the UK, RAP is normally makes up around 10% of the total aggregate feed (although higher figures are possible in new plants), which means that virgin aggregate makes up only 90% of the material going to the dryer. The RAP is added either at the base of the hot-stone elevator or directly into the mixer where it comes into intimate contact with virgin aggregate from the dryer causing the RAP to heat up to a common temperature before it is coated. RAP should always be kept under cover to keep the moisture content as low as possible, eg no more than 1.5%. The author has witnessed RAP containing up to 5% moisture interfacing with the heated aggregate and causing an explosion of steam. This steam release extracts ‘latent heat of evaporation’ from the virgin aggregate. Thus, the 90% virgin aggregate has to be heated to a much higher temperature to support this evaporation and no savings in dryer fuel may be realized. The steam also has to be evacuated to the filter causing the fan to absorb power proportional to the amount of steam evaporated.
Bag filters on asphalt plants
Bag filters are installed in the production process to control the emission of dust to the atmosphere. Their importance is extended as they also act to induce combustion air (depending on type of burner) and evacuate the steam released from the aggregate, plus the products of combustion via the associated fan. The higher the exhaust volume, the greater the power demand on the exhaust fan. Volumetric output needs to be controlled to give an optimum extraction rate as variations can occur due to feed rate, temperature of the stone, type of aggregate and the volume of evaporated steam. This is often achieved by maintaining a constant vacuum in the dryer (normally about 5mmWG depending on the degree of sealing of the dryer). The pressure transducer measuring the vacuum is normally located on the front plate of the dryer and is linked to a frequency inverter. This modulates the fan speed to maintain a constant vacuum. Filters must be inspected to confirm no undue leakage. The ducting between the dryer and the fan inlet should also be inspected for leakage, as any leakage or excess air will increase the power consumption of the fan and reduce the production rate of the dryer. Enviroflo Engineering recommend the use of pulse-jet filters on asphalt plants. Reverse-air filters are subject to leakage and generally do not run successfully via a frequency inverter because of their particular method of cleaning. As such, they are best suited to crushing and screening applications where the use of foam suppression is not appropriate.
Dryer burner optimization
A considerable amount of fuel can be lost if the dryer flame does not burn out completely. This can be shown initially by testing for carbon monoxide on the outlet ducting from the dryer (with no leakage air to dilute the results). It can also be tested at the burner end on some types of burners, while the stack can be tested for unburnt carbon. Carbon monoxide values above 20ppm mean that the flame is not burning out completely and the full calorific value of the fuel is not being realized. Where burners use reclaimed oil with a viscosity of around 52cStokes (200sec Redwood), the temperature of the oil, as fed to a normal burner, should be in the region of 60°C to allow it to burn efficiently. This temperature should be checked frequently, as carbon deposits can build up on the heating elements within the main line heater and one or two banks of elements could burn out, thus lowering the fuel oil temperature and resulting in inefficient combustion. If the burner does not operate efficiently and unburnt fuel is passed to the bag filter, this can cause bag blinding or a bag filter explosion or burn out, resulting in the plant being put out of operation.
Excess filler (mainly associated with urban plants)
If the –63 micron content in the 0–5mm dust is above around 14%, the amount of filler collected by the skimmer and the bag filter will almost certainly be in excess of the storage capacity available or the amount that can be returned to the mix. These fines are often removed from site by tanker for disposal or are fed through an on-site dust-conditioning unit prior to transport to a suitable landfill area. This exercise is very expensive and it is suggested that the dust should be changed so that the –63 micron content is no more than 12%.
Excess filler means that it has to be crushed, transported to site, heated up to around 180°C and then disposed of. The additional heat used together with the transportation of the filler to and from site is expensive and should be avoided. Moreover, the additional filler may cause excessive wear on the skimmer, ducting and filter parts.
Fan optimization
Fan size and power consumption is influenced by high moisture content in the aggregate to be dried. As mentioned earlier, it is important that the fan is optimized as it is one of the largest consumers of power within the plant. The power consumed varies as the cube of the speed, so any reduction in speed can bring about worthwhile savings. Fan blades need to be inspected frequently to avoid out-of-balance operation and fan impeller disintegration.
Small orders
The production of small orders, ie less than 6–8 tonnes, can increase fuel consumption disproportionately, as much larger amounts of aggregate have to be heated/dried to produce this amount. The excess aggregate is, in most cases, dumped (‘cleaning out’) and the overall fuel used can be in the region of 50 litres/tonne of coated material.
Dryer flighting
The purpose of dryer flighting is to transfer the heat from the flame into the aggregate. If the flights are worn or ineffective, high-temperature exhaust gas will enter the bag filter (eg more than 120°C when producing dense mixes). It is important, therefore, that the flighting is kept in good condition or a serious loss of fuel and production will ensue.
Water treatment
Where single-size aggregates need to be cleaned they are normally passed over a rinsing screen arrangement. In some cases the water storage lagoon may be so small that it allows recirculation of suspended solids back through the spray nozzles and on to the aggregate being cleaned. Generally, therefore, it is important to add a flocculating agent to the water supply to the sprays in order to reduce the recirculation of solids to a minimum. This will produce cleaner chippings (eg for surface dressing), as well as reducing wear on pumps and nozzles.
Summary
The following list summarizes those
areas of asphalt production that can ‘burn money’:
- Location and lack of cover over ground stocks.
- High moisture content in aggregate fed to the dryer.
- High moisture content in RAP.
- Poorly designed and sealed bag filter and ducting system.
- Inefficient burner combustion.
- Excess filler in urban plants.
- Exhaust fans.
- Small orders.
- Ineffective dryer flighting.
For further information or assistance in reducing operating costs, contact Enviroflo Engineering Ltd on tel: (01902) 784848; fax: (01902) 784242; mail: sales@envirofloeng.com