Asphalt circularity: the untapped opportunity
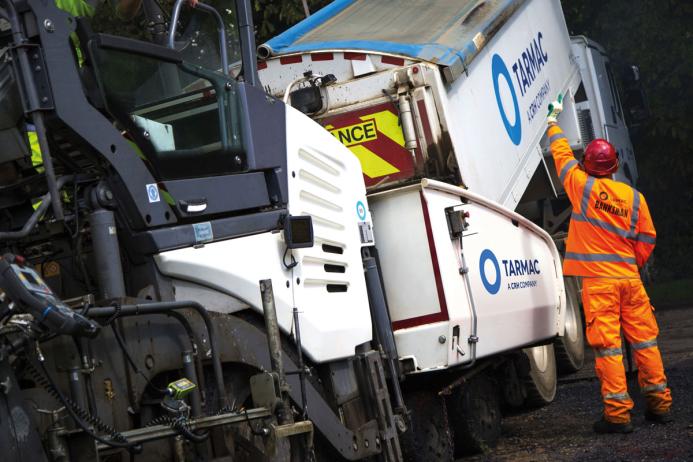
First published in the January 2025 issue of Quarry Management
By Jessica Tuck, national technical director, Tarmac
'Industry owes it to society to conserve materials in every possible way. Not only for the element of cost in the manufactured article, but mostly for the conservation of those materials whose production and transportation are laying an increasing burden on society.’
Sound familiar? This could be a statement that you could read or hear at an industry event today. However, it was actually said by Henry Ford, the American inventor and industrialist, in 1926.
Transitioning from a ‘take-make-waste’ linear economy to a circular economy, where waste is designed out and materials are kept in use and reused across their lifecycle, is not a new concept, but the opportunity to fully drive material circularity across our infrastructure and road asset is still not being fully maximized in the UK.
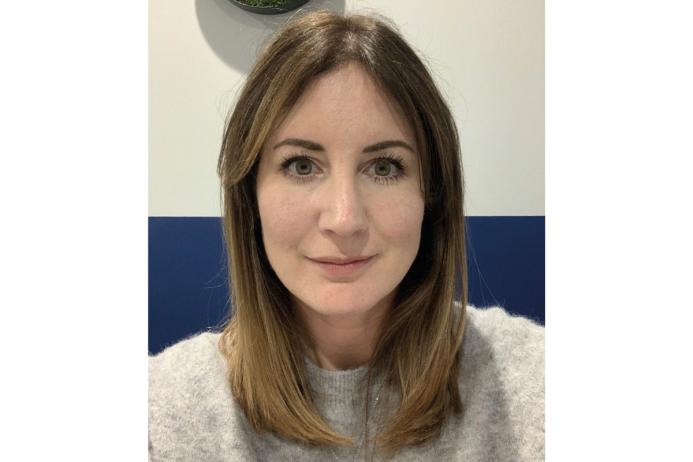
During an event last year I asked a group of senior clients from across infrastructure how many currently had a plan to work with their full supply chains to drive material circularity. Those who said that they did were in a small minority. If I had asked the question about carbon reduction across the supply chain, it would have been a very different answer.
The reality is that delivering circularity will help our commitment to net zero. Circular economists believe that 45% of the world’s greenhouse gas emissions are embodied in everyday products such as our cars, clothes, buildings, infrastructure, and food.
Radically changing how we use resources and keeping materials in service for as long as possible is key to carbon reduction and net-zero delivery. There is now an opportunity for clients and asset owners to make circularity a priority through the supply chain.
The reality is that we have to plan for circularity. At an operational and project level you need to have an understanding of what is in the asset and how its materials can be maximized and recycled.
However, there is an important step before this. Strategically, infrastructure clients need to ensure that their supply chains prioritize circularity and align industry effort. A change of mindset will require our sector to better design road schemes for circularity and for us all to be better in sharing learnings.
Get this right and it will deliver greater proportions of recycled materials, cost savings, and carbon reduction.
The opportunities for recycling and reuse are significant and as a highways industry we have already come a long way, with asphalt being one of the most recycled materials in the world.
There are a lot of opportunities to increase the use of recycled asphalt planings (RAP) in both the surface course and the lower layers of roads.
The surface course continues to represent both a challenge and opportunity. At the moment surface course asphalt materials are recycled into new asphalt products and placed back in our roads. However, it is common practice to use only the finer recycled material in new surface course materials. Consequently, the industry is not getting the benefit of recycling precious nominal size high polished stone value (PSV) aggregates that are finite and key to delivering skid resistance on our roads.
It is technically viable to recycle high-PSV aggregates back into surface courses. To do so we need to understand the PSV of the coarse aggregates in the planings.
We do not currently have an industry system for tracking the PSV of the aggregate in the asphalt planings. Data on the PSV composition of the existing asset do not always exist and are not commonly shared as standard practice within the supply chain.
In the absence of available data, to enable the recycling of high-PSV aggregates in surface course asphalt, contractors need to plane off the surface layer and store the planings separately from the lower layers so that the PSV of the coarse aggregate can be confirmed before recycling into a new surface course.
Once the RAP aggregate has been quarantined, the next steps are to recover the binder and take PSV samples. This can be a time-consuming process and requires a lot of space to store materials, which is another reason why high-PSV aggregate is not being recovered and reused.
A digital approach is being explored by National Highways within its pavement community, which, if developed, would unlock opportunities for increased circularity of high-PSV stone.
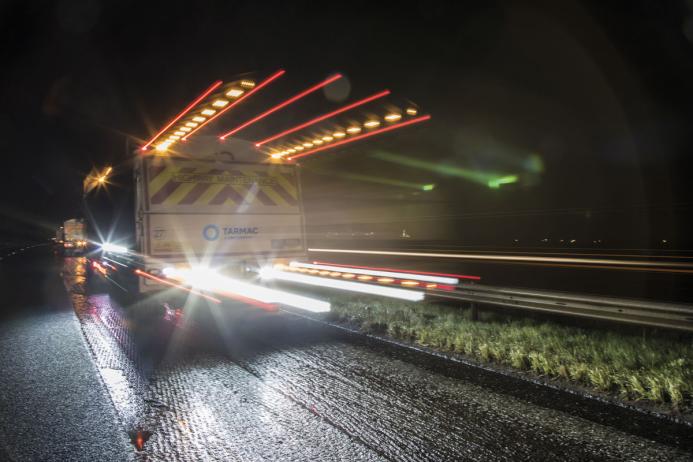
Conceptually, the asset owner would provide existing data relating to the area from where the asphalt is to be removed to enable its reuse without the need for PSV testing. There are no similar prolonged activities involved when it comes to binder testing, so these protocols would remain unchanged.
Across the industry, a number of potential avenues for boosting materials circularity are being explored. Although there are no plans to allow the reuse of polymer-modified bitumen (PMB) binders currently, this is an option that is being explored in conjunction with PMB suppliers and warrants some further research to fully understand whether PMB properties could be assumed or verified for such reuse.
Tackling the constraints around materials circularity and unlocking the opportunities available remains a significant priority for Tarmac.
Tarmac are net users of waste. Put simply, we reuse more waste generated by other people than the volume of waste we produce. In 2022 we recycled 99% of the waste generated across our operations and our goal is zero waste by 2030.
Each year we recycle more than 1 million tonnes of recycled asphalt planings in new asphalt – translating to 15% of our asphalt production. We also recycle more than 7 million tonnes of waste and secondary materials as raw materials or fuels from other sectors.
Maximizing the opportunity at an industry level requires clear client leadership and supply chain collaboration, alignment, and engagement. Materials mattered to Henry Ford in the 1920s. In a world transitioning to net zero with a greater appreciation of resources, they need to matter to all of us today.
Subscribe to Quarry Management, the monthly journal for the mineral products industry, to read articles before they appear on Agg-Net.com