A66 Eden Valley Resurfacing Scheme
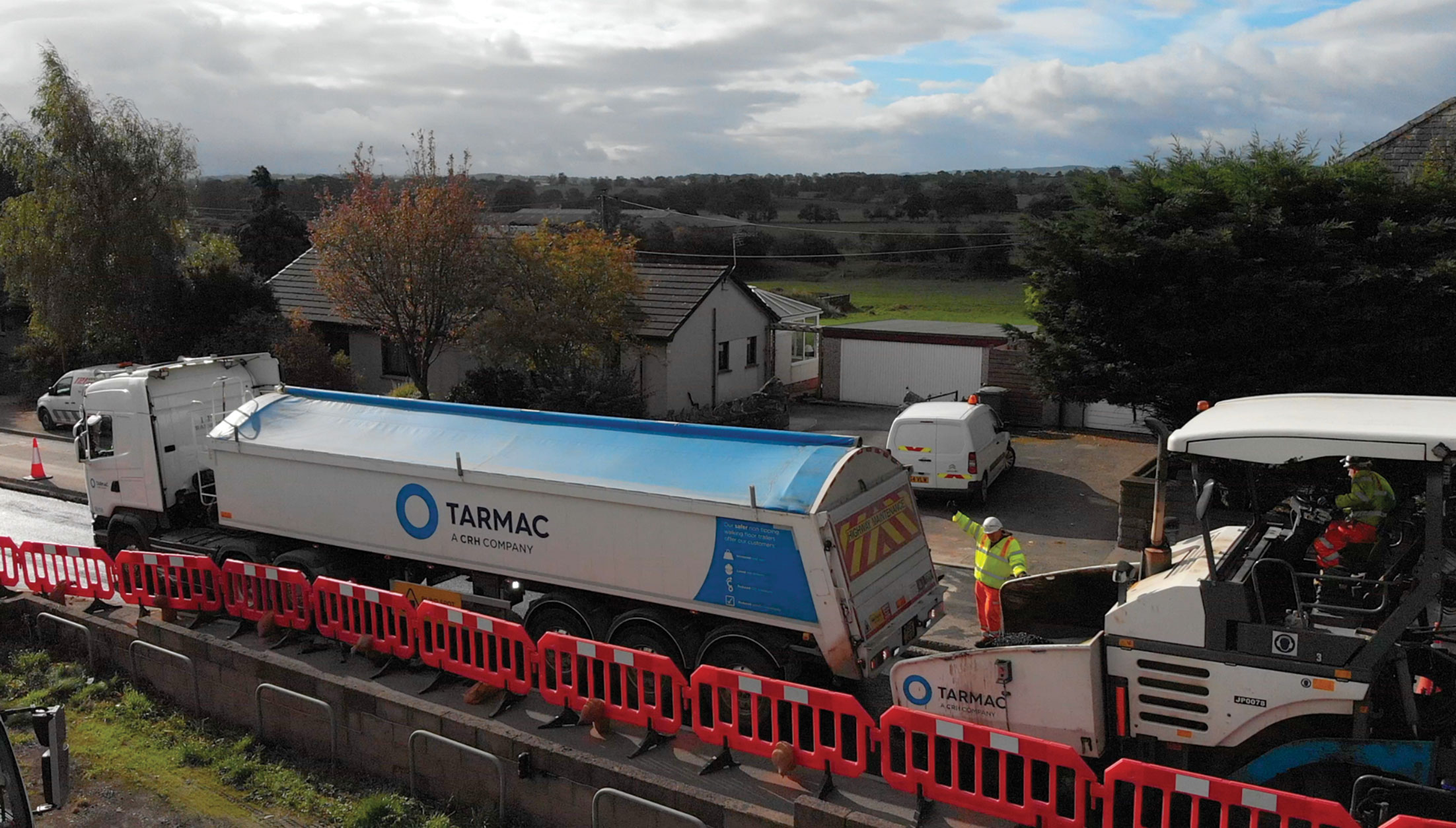
First published in the January 2019 issue of Quarry Management
Total Bitumen and Tarmac demonstrate industry-leading collaboration
The A66 Eden Valley Scheme between Penrith and Kirkby Stephen in north Cumbria was recently resurfaced by Tarmac for Highways England. This road is a strategic link between the North West and North East and, as such, required the works to be completed with as little disruption to the travelling public as possible. The goal of the project was to provide a newly constructed carriageway to modern standards of ride quality with minimal vibration and noise for residents along the route.
Unusually nowadays, to achieve this the works were completed under full road closures during weekends throughout October 2018. Around 10,000 tonnes of asphalt were installed on the project with a total value of £5 million. The logistical implications of the project meant productivity targets could only be achieved through the use of warm-mix asphalt, which is increasingly being seen as beneficial not just in terms of environmental gains from energy reduction, but also for the engineering benefits it brings to the material, contractor and client. Lower temperatures can lessen premature ageing of the product, whilst improved compaction, greater tolerance to travelling, and speed of opening of the newly surfaced road to traffic are all tangible benefits of these systems.
Ian Carr, regional technical manager for Tarmac Contracting North and Scotland Region, explained: ‘Using warm mix, typically mixed at 40oC cooler than standard, allows us to work that bit longer to maximize our output and release the site back to the road user quicker. It’s important to Tarmac that we have good durability within our surface courses, and for this reason we chose Total Styrelf eXtreme 100 polymer-modified binder (PMB), as we’ve used this for a number of years in our Ultipave M surfacing and Clause 943 hot-rolled asphalt. A great advantage of this PMB is the variety of asphalts we can manufacture with this one product, allowing us to stock a single PMB at the plant that can make many special products.’
Rick Ashton, Total’s market development manager, commented: ‘The versatility of Total Styrelf eXtreme 100 is one of its key attributes. The product is comparable to a Swiss Army knife because it’s a real multi-tool binder. This PMB can produce many specialist asphalts that comply with the most rigorous end-client specifications. Manufacturers can produce mixtures compliant with Class 2 Clause 943 HRA, TS2010 Transport for Scotland and premium thin surfacing for the highest-stress applications. This is all achievable with this one grade of cross-linked polymer-modified binder. The advantage of this is that most producers have only one storage tank dedicated to polymer-modified bitumen. With more specialist asphalts now being specified, it’s a real boon having one binder that fits nearly all specifications and it’s becoming an increasingly attractive proposition to manufacturers.’
Another problem for producers is the sometimes-sporadic nature of specialist asphalt supply. If PMB is stored for long periods between production runs, phase separation of the polymers from the bitumen can start to occur. This can result in a head of bitumen in the top of the tank with unmodified bitumen below ready to be drawn off. Many non-cross-linked PMB’s are really only storage stable for a couple of weeks or no more than a month. This is a real issue when there are gaps in production for specialist products. Total Bitumen have done extensive laboratory analysis on storage stability and have found Styrelf eXtreme 100 to be fit for purpose after more than 100 days in storage. This reduces waste and loss of high-value constituents into lesser-valued products as material does not spoil in storage.
Productivity gains on the A66 allowed 1,000 tonnes of asphalt to be installed during each shift. Total’s ECO2 technology was used in the binder course and surface course, and despite Storm Callum hitting during the scheme the works were completed on schedule.
Pre-blended warm-mix PMB removes the manual addition of additives at the asphalt plant while reducing energy consumption and emissions, moving the industry in a responsible sustainable direction. The warm-mix asphalts were produced at Tarmac’s Sandside and Barrasford plants, with the ready-to-use, pre-blended, warm-mix bitumen produced at Total Bitumen’s Preston facility.
Another benefit derived from the use of Azalt ECO2 on the scheme was a lack of steam generation during the paving operations. This improved visibility and was a real safety improvement for the workforce, particularly in damp or humid conditions. To achieve optimum durability the layers of the base, binder course and surface must be properly bonded together to stop water ingress and thus de-bonding of the pavement layers. An innovative solution to this on the A66 was the use of Total Emulsis NBC50 bond-coat emulsion. This has non-stick properties when tipper vehicles drive on it to deliver their loads to the paver.
Conventional bond coats can be picked up on the tyres of construction traffic leaving a bare surface to receive the new asphalt. This phenomenon can expose the carriageway to the future risk of potholes, as the surface layer can de-laminate from the binder course. Emulsis NBC50 does not lift on tyres and stays non-sticky on the planed surface until the hot asphalt activates its highly adhesive bonding properties. The success of this could be seen by the lack of black contamination lines on the surrounding roads as delivery vehicles left the site.
Ian Carr commented: ‘Tarmac strive to be the most sustainable supplier in this sector. Using warm-mix asphalt such as Azalt ECO2 allows us to reduce carbon emissions by around 25% over conventional hot-mix alternatives. It’s very easy to specify because it complies with the same specifications as the hot-mix material. It truly is a product that I don’t believe has any detracting features to it at all.’
This collaboration between Tarmac and Total is just one of the many innovations helping to maintain and improve the UK’s roads today. For further information visit: www.bitumen.total.com
- Subscribe to Quarry Management, the monthly journal for the mineral products industry, to read articles before they appear on Agg-Net.com