A Warm Mix
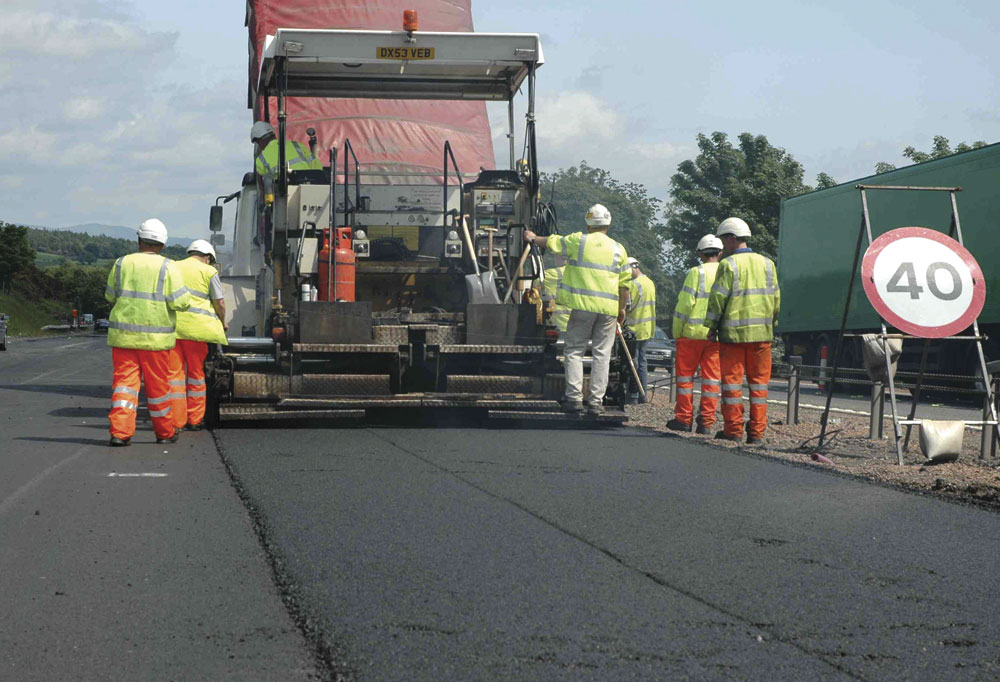
The drive for carbon-efficient road construction and maintenance is gathering pace, with the benefits of foamed bitumen becoming increasingly recognized. Mike Walter reports on ‘Nyfoam’ and other developments
Efforts to introduce energy-efficient asphalt production methods on a wider scale in the UK have been boosted with the launch of a comprehensive new carbon calculator by road research body TRL. The adoption of less carbon-intensive approaches to road building is of interest to bitumen suppliers such as Nynas, who are promoting the use of ‘warm-mix’ asphalt and, in particular, the technology of foamed bitumen.
TRL’s Asphalt Pavement Embodied Carbon Tool – known as asPECT – has been brought to market following three years of research carried out by the Highways Agency and the Asphalt Industry Alliance.
The asPECT software calculates the overall carbon footprint generated by producing and laying asphalt. Specifiers using the new tool may then be encouraged to seek more sustainable road construction materials or processes.
‘This tool considers a wide range of factors including where raw materials have been sourced from and the energy consumed at an asphalt plant,’ said TRL senior consultant Matthew Wayman. ‘The next phase of the project is to look at durability and maintenance of roads so that specifiers can see which materials tend to last longer than others and choose products with a lower overall carbon impact.’
In a further effort to encourage energy-efficient material use, the Carbon Trust is making available funding of up to £500,000 to companies willing to carry out research to help accelerate the ‘development of a market for lower-temperature mixed asphalt’.
Quantifying the carbon benefits of one material over another is undoubtedly good news for suppliers of asphalt products and bitumen binders designed with sustainability in mind. Nynas, as mentioned above, are heavily involved in development of warm-mix asphalt technology as an adjunct to their conventional hot-mix activity.
Asphalt described as warm mix is typically heated to between 100°C and 140°C, around 40°C less than hot-mix asphalt. Nynas also offer a ‘half-warm’ mix whereby asphalt is produced at between 70°C and 100°C. Lowering the mixing temperature of asphalt not only reduces the energy needed to heat raw materials during production, but also generates fewer emissions.
Despite its environmental benefits, the use of warm-mix asphalt in binder and surface-course applications is seen by some in the highways sector as a lesser alternative to conventional hot mix. In an effort to boost the use of warm mix, Nynas are actively promoting their foamed bitumen binder, Nyfoam, to manufacture asphalt at slightly cooler temperatures.
Foamed bitumen is produced when water is introduced to hot binder in small quantities. Water turns to steam and the viscosity of the bitumen is consequently reduced. This allows it to flow more readily and coat stone more effectively at a lower temperature than conventional hot mix. The foaming action can also increase the length of time an asphalt remains workable on site, without the use of chemical additives. Bitumen can either be foamed before it is added to a mix, or during the mixing process. Either virgin aggregates or a blend of recycled and secondary stone can be coated with a foamed bitumen.
Nynas’ product application manager for cold paving technology and surface treatments, Dennis Day, explained: ‘The use of foamed bitumen allows us to manufacture a durable asphalt with the performance characteristics of a material created using a hot binder, but at a lower temperature. It also has the added benefit of allowing asphalt to be laid at temperatures as low as 60°C, which improves safety for operatives by reducing the chance of workers suffering burns.
‘We believe that our Nyfoam range of binders has better and more consistent foaming characteristics compared to other binders, and is suitable for a wide range of applications using cold, half-warm or even warm-mix processes.’
Introduction of Nyfoam for warm-mix asphalt upper layers marks a departure for Nynas, who until now have promoted foaming binder for lower pavement layer materials, mixed cold. For more than 20 years, the company has supplied bitumen to the European market, which has been used for foaming on to aggregate at between two and three per cent of volume to enhance the characteristics of basecourse material.
According to Mr Day, if a higher percentage of foamed bitumen is added to an asphalt – matching the levels used in conventional hot mix – the resulting material can be used successfully in binder and surface courses. The key is to ensure aggregate particles are coated fully. Asphalts mixed warm have been used by Nynas’ customers on road construction projects in Holland since 2002. Products featuring the Nyfoam binder include the lower-temperature road surfacing material LT-AsfaltR.
Nynas now hope that warm-mix applications in upper layers will begin to be used in the UK. They are one of a series of bitumen suppliers who are working on warm and half-warm mixes for use in this country.
‘In the next 10 years, I believe a major part of the UK’s asphalt market will swap from using hot mix to warm mix,’ added Mr Day. ‘Benefits for producers are likely to include reduced energy costs and carbon emissions. Specifying warm or half-warm mixes could save as much as 50% on fuel consumption and Nynas’ range of Nyfoam binders are there to offer the optimized performance solution to the producer.’
Asphalt suppliers looking to develop and trial warm-mix products are welcome to work alongside Nynas and make use of their comprehensive laboratory and testing facilities in the UK, Belgium and Sweden. In some cases, asphalt mixing plants may have to be modified to accommodate the manufacture of warm-mix materials and specialist staff from Nynas can help asphalt suppliers to invest in upgrades to their infrastructure wisely.
A four-year study into the performance of foamed bitumen, along with two other reduced-temperature asphalt techniques, is coming to a close in Belgium. The research project is led by Nynas and the Belgian Road Research Centre.
The three techniques selected for the study are the addition of wax to produce warm asphalt, the addition of zeolite to produce warm asphalt and the use of Nyfoam to produce a half-warm temperature asphalt, known as LT-Asfalt.
Extensive laboratory studies were conducted on all three reduced-temperature techniques, with an emphasis on workability and compactability. Field trials followed on a heavily trafficked stretch of public highway. There was found to be little difference between the performance of the warm and half-warm mixes against a section of road laid using hot-mix asphalt.
Early results gathered from the study have pointed towards the conclusion that the same degree of compaction can be achieved in a foamed bitumen produced at 90°C as a hot mix produced at 150°C.
asPECT (Asphalt Pavement Embodied Carbon Tool) was launched on 21 October at the Asphalt Industry Alliance Conference 2009, held in Coventry.
Developed under the 2008–11 Collaborative Research Programme – a joint initiative funded by the Highways Agency, Minerals Products Association and Refined Bitumen Association, and delivered by TRL – the asPECT software tool will help the highways industry to identify processes that have a high carbon impact and will allow specific areas to be targeted for carbon reduction.
The development team and focus group set out to create a ‘sustainability management system’ for the highways sector. The first phase of the project focused on the key issue of greenhouse gas emissions with the aim of creating a standardized method of measuring the contribution to climate change that asphalt products and applications make.
The tool itself is based on Microsoft Excel software but appears to the user as a series of entry forms. The user is guided through the available functions to enter data and select options to produce detailed results for each stage of the road lifecycle.
The asPECT software is freely available from www.sustainabilityofhighways.org.uk along with the accompanying protocol for the calculation of life-cycle greenhouse gases generated by asphalt, as used in highways, and accompanying guidance notes.