A Spark Of Innovation
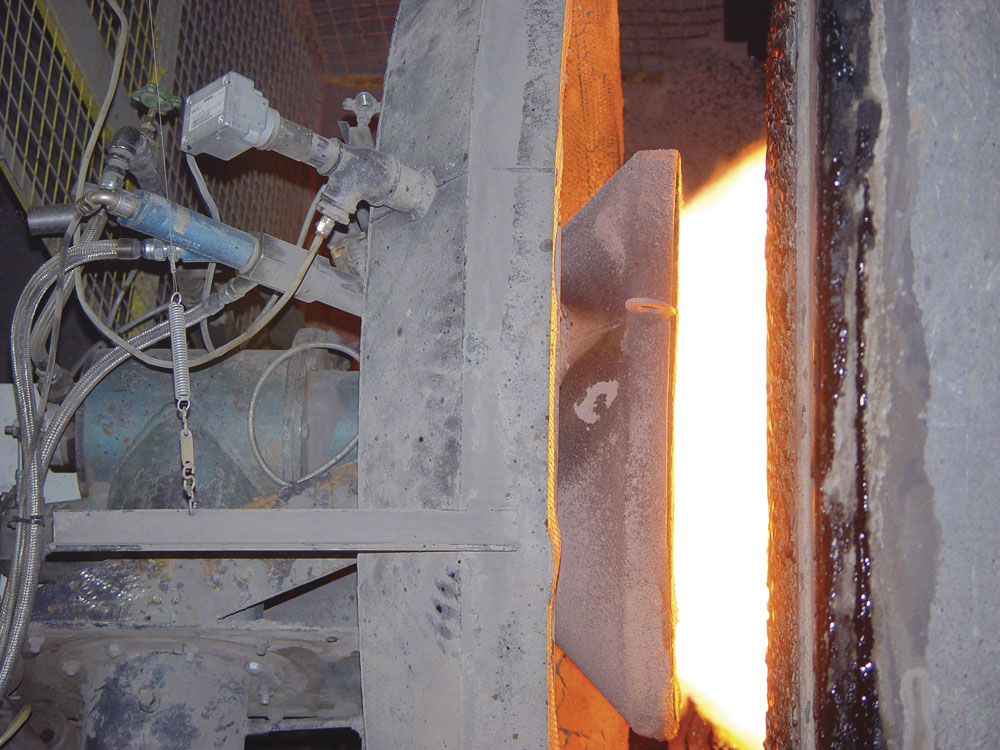
MQP eliminate the use of virgin fuel oil across their West Midlands asphalt plants by developing a groundbreaking ‘igniter’ system with Mixlance
As the UK gears up for a low-carbon economy, one of the biggest challenges facing the quarrying industry is reducing the environmental impact of its operations and materials. With sustainability now a core objective, it comes as no surprise to learn that many operators are embarking on a drive towards an environmentally sustainable future.
Energy efficiency, minimizing waste and reducing carbon emissions have become central to the way many companies in the aggregates sector and related industries operate, as now – unlike a few years ago – they have key regulatory responsibilities and sustainability targets to fulfil.
Midland Quarry Products’ (MQP) vision is to minimize the environmental impact of their operations and products. Andy Read, area operations manager for MQP, explained why the company is focusing on sustainability and a ‘greener’ way of operating.
‘MQP aim to be at the forefront of sustainability and environmental consideration – our objectives are to cut energy consumption, improve energy efficiency and reduce the level of CO2 that can have a detrimental effect on our environment.’
Indeed, the company is constantly seeking the latest technological developments and improvements in cutting its carbon footprint and that of its customers as part of its commitment to promoting sustainable solutions.
‘With sustainability at the core of our business growth strategy, it’s important that we support the research and development activities taking place, encouraging innovation and developing new environmentally friendly products and processes,’ explained Matt Read, unit manager at Ettingshall Works.
A good example of this is the recent installation of a pioneering ‘igniter’ system, which was trialled and tested on a Mixlance batch-heater plant at Ettingshall.
Developed by coating plant specialists Mixlance, the igniter replaces the need for an oil- or gas-fired pilot assembly, an integral component of the conical-flame burner with a ‘light-on-demand’ gas ignition system, which managing director, visionary and batch- heater custodian Jed Smyth believes represents the next step up in the evolution of asphalt plant technology.
‘The design of the igniter is based on the concept of delivering light on demand’, he explained. ‘As most asphalt suppliers will testify, pilot assemblies can sometimes be unreliable. They have to be permanently lit, consuming 12 litres of oil/gas equivalent per hour. The problem with this is that energy is wasted by constantly burning fuel, together with associated costs and detrimental environmental impact.
‘Oil-fired units can have a tendency for high maintenance, which is further complicated by the reducing availability of some spare parts, thereby potentially increasing operational downtime, which, in turn, can have a detrimental effect on customer service. There are also vibration and safety issues associated with oil-fired pilot assemblies, further increasing the health and safety risk to maintenance personnel.’
Working closely with MQP, Mixlance installed and commissioned the ignition system over the Christmas holiday period and the 12-week trial at Ettingshall has been a huge success in delivering cost savings, reduced carbon footprint and improved energy efficiency for the company’s customers. So, how does the igniter work?
The control unit of the system sends a signal to the igniter to spark for around 4s while opening the air and gas valves, with a flame-detection circuit in operation after the spark ceases. Thanks to its compact design, the ignition system uses a single electrode, facilitating easy maintenance. The igniter itself consists of two concentric tubes and in the centre tube, a premixed air and gas flame is retained in a burner head, providing a hard stable core to the overall shape of the flame.
Additional boost gas is supplied through the annulus between the two tubes; it mixes with the main burner air and burns around the outside of the core premix flame, resulting in a larger heat release and longer flame. The size of the outer flame, however, can be varied during commissioning to suit the burner installation for improved burner light-up while minimizing gas consumption.
The PLC/PC or plant operative would normally shut down the igniter during main burner flame detection so this leaves low-volume purge airflow to help keep external matter out of the igniter burner head.
‘If we are going to take a more proactive approach to managing the environmental and social impacts of our products then we need to fully endorse the continued development of technology that minimizes any impact on the environment,’ said Andy Read. ‘Mixlance have a reputation for developing specific products adapted to meeting the green agenda and the igniter is the latest example of offering MQP good sustainable practice.’
Following successful trials and commissioning at Ettingshall, the ignition pilot has demonstrated a host of environmental benefits and potential cost savings for MQP, including significantly lower fuel and electricity costs.
Unlike the oil-fired pilot assembly which runs on gas oil, the igniter uses propane, which is far more cost-effective than the former. More importantly, the ignition system does not have to be constantly burning fuel, consuming electricity and, effectively, increasing the carbon footprint.
‘The recent field trials have shown that the igniter can help cut around 120 tonnes of CO2 emissions annually at Ettingshall,’ said Matt Read.
The simplicity of the igniter also provides minimal failure rates, improved reliability and lower maintenance costs (Mixlance provide a cost-per-tonne maintenance contract at Ettingshall Works to maintain optimum plant availability).
Simon Willis, managing director of MQP, commented: ‘Sustainable development is a top priority for MQP and we are taking the initiative to use sustainable and cost-effective fuels, with the aim of reducing or eliminating our use of virgin oil products. The igniter is an important step in ensuring we are engaged in more environmental friendly practice, reducing our carbon footprint and maintaining our sustainability drive.’
Taking the sustainable approach
Mixlance are the first UK company in the industry to have been awarded funding from the European Commission’s ‘LIFE Environment’ programme for the development of their low-level modular batch-heater coating plant. Following completion of the project, the company was awarded the prestigious ‘Best of the Best’ accolade – the first UK participant to achieve this honour.
As well as designing, developing and maintaining coating plants, Mixlance also produce a range of filtration systems. Falling under the company’s ‘Optimization’ range and ‘Save Initiative’ programme, Mixlance promote and deliver the most sustainable solutions for the environment, offering reduced energy consumption, optimum performance, cost savings and major reductions in carbon emissions.
For example, the company has recently taken an order for a new 5-tonne batch- heater barrel incorporating the ‘Hibernation Mode’. Features of the barrel include: double-skinned shell, redesigned sub-frame, thrust roller and lifter profile; automatic hydraulic lifting cradle; and reduced noise and greenhouse gas emissions, resulting in optimum electricity, fuel and consumable usage, as well as cost savings, improved health and safety/maintenance procedures and minimized environmental impact.