A New Age Of Asphalt Production
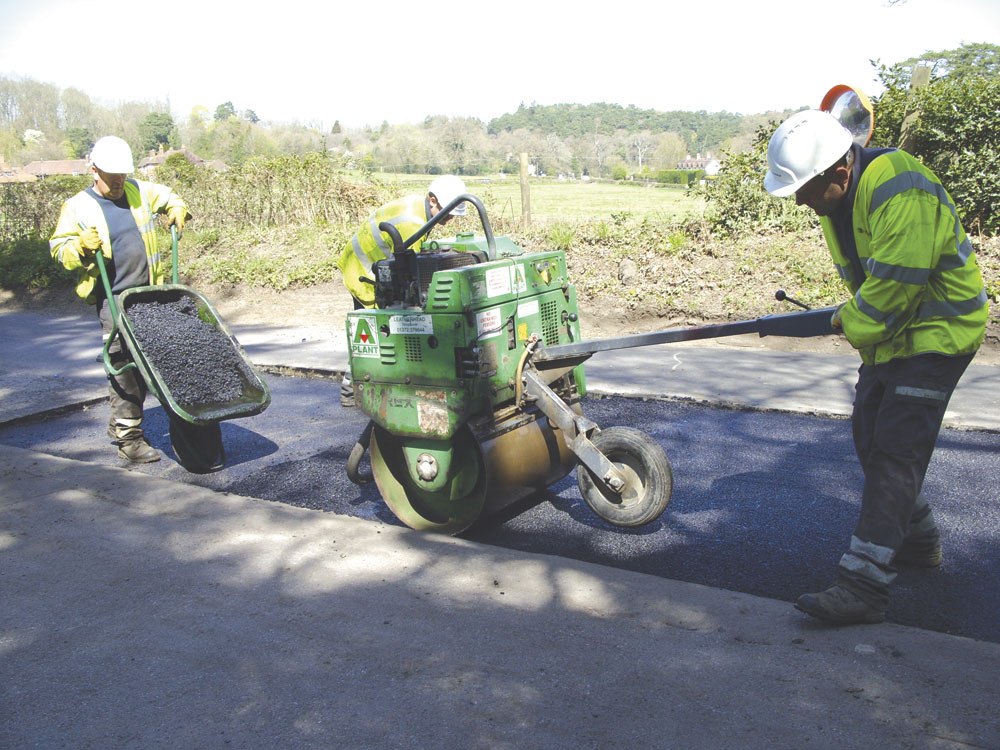
Hanson say they have become the first company in the UK to produce and lay low-energy asphalt in a move that reduces the level of carbon emissions associated with asphalt production for road laying by 50%. The company has launched Hanson ERA (energy reducing asphalt), a production process that allows the material to be produced at temperatures between 80 and 95°C – compared with up to 190°C for equivalent hot-mix asphalt.
The process involves micro-foaming the bitumen in the asphalt plant mixer and has been used across Europe and in the US for more than five years, but is new to the UK market. Hanson chose their West Drayton depot, in Middlesex, to introduce Hanson ERA for the first time and found the production process to be problem free.
Warm- and cool-mix technology is increasingly being used in road surfacing projects as it offers the industry an opportunity to improve the performance of the asphalt and the efficiency of its application – as well as improving environmental credentials.
‘Hanson ERA is laid by conventional asphalt paving equipment and we found that it had good compaction and workability,’ said Richard Pay, site manager at Hanson Contracting, who carried out the first lay of the material.
‘It presented a lower risk of burns, due to the lower temperature, providing a safer working environment for the laying contractors.
‘It was also quick to lay and requires less cooling time between courses, significantly increasing the amount of material we can lay in a standard shift. I can see this technology helping to minimize disruption for motorists when it is used for resurfacing works.’
There are a number of additives which provide reduced-temperature hot-mix asphalts, but Hanson chose Hanson ERA because it is a production technology, rather than a product. This means it can readily be incorporated into a number of the company’s asphalt plants across the country – providing nationwide availability – with very little disruption as it is compatible with plant configuration and materials. It is said to provide excellent temperature reduction with no loss of performance and the process can be applied to almost all of Hanson’s base, binder and surface course asphalts.
Hanson ERA can also use up to 50% recycled content, while the asphalt itself is 100% recyclable, providing the opportunity to produce a greener product to help meet the environmental targets of today’s road-building projects.
According to Hanson, the impressive temperature reduction results in no loss of performance. In fact, the company says material produced in this way has proved to be more durable than traditional hot-mix materials. This is because binder ageing is directly related to the production temperature of the mixture. With Hanson ERA, the reduced production temperatures result in the retention of many of the more volatile bitumen fractions that are lost during traditional hot-mix asphalt manufacture.
Case Study – Surrey County Council
The Hanson ERA production process can be applied to a wide range of base, binder and surface course asphalts. Over the last few years the company has been working with Surrey County Council to develop a proprietary one-layer patching material to improve the performance of pothole repairs.
This was successfully introduced three years ago and now, to further improve waste prevention and carbon reduction, the material has been trialled using the Hanson ERA production process and using 20% recycled material within the mix.
Iain Simpson, an engineer with Surrey County Council, said: ‘Our materials laboratory, within the asset planning operations group, is proactive in trying to reduce waste and carbon – and hence potential costs – to drive both carbon reduction and efficiency savings going forward.
‘This is reflected in the fact that we are registered as both a CRC (carbon reduction commitment) county and with WRAP in a memorandum of understanding regarding the use of recycled materials.
‘We are also constantly driving innovation to improve the durability of materials and processes to ensure best value. Part of this was to work with Hanson to develop the one-layer patching material and, subsequently, to ask the company to improve the green credentials of the material, initially by including some recycled aggregates within the mix.
‘Hanson’s development of Hanson ERA technology also gave us the incentive to try to reduce the embodied carbon by lowering the mix temperature.’
In the road trial, two options were tested. The first incorporated 20% recycled aggregate in the mix, while the second included the recycled content and was also produced using the Hanson ERA process. Workability and quality of finish were both good with the first option but the real interest was in how the Hanson ERA material would perform.
The first batch of the energy-reducing asphalt was used to regulate the patch and proved extremely easy to compact. The patch was then surfaced in two layers of approximately 70mm and 30mm. Once the binder course had been completed, surfacing commenced immediately as the rolled material was solid.
The final surface course was laid around 4h after loading and the temperature in the middle was still around 80°C. A technician measured the temperature prior to rolling at 54°C and the material laid extremely well and gave an excellent finish.
According to Iain Simpson, the mixing, laying and compaction temperatures were reduced by almost half compared with standard hot-mix asphalt.
‘We are continuing to work with Hanson to make asphalt produced using the Hanson ERA process the patching material of choice within the Surrey network. I hope that our pioneering use of the process will pave the way for general industry acceptance of low-energy asphalt technology,’ he said.
Conclusion
Hanson ERA is a reflection of Hanson’s commitment to carbon reduction. The company has also been using the Highways Agency’s asPECT tool to show the benefits of localized sourcing and intelligent mix design to address the imbalances in aggregate demand, which benefit the end-user in both financial and environmental terms.
‘As a business, we recognize the need to work smarter,’ said Tony Zigler, Hanson technical services manager. ‘Demand over recent years for single-sized PSV aggregates, usually delivered by lorry over long distances, has been extremely high. Intelligent material design and testing has shown that equivalent – or, in many cases, better – performance can be achieved using undersized and oversized aggregates combined with locally sourced and recycled materials.
‘This intelligent design goes hand-in-hand with the Hanson ERA production process, which can be applied to the majority of the asphalts we produce.’