A Greener Shade Of Black
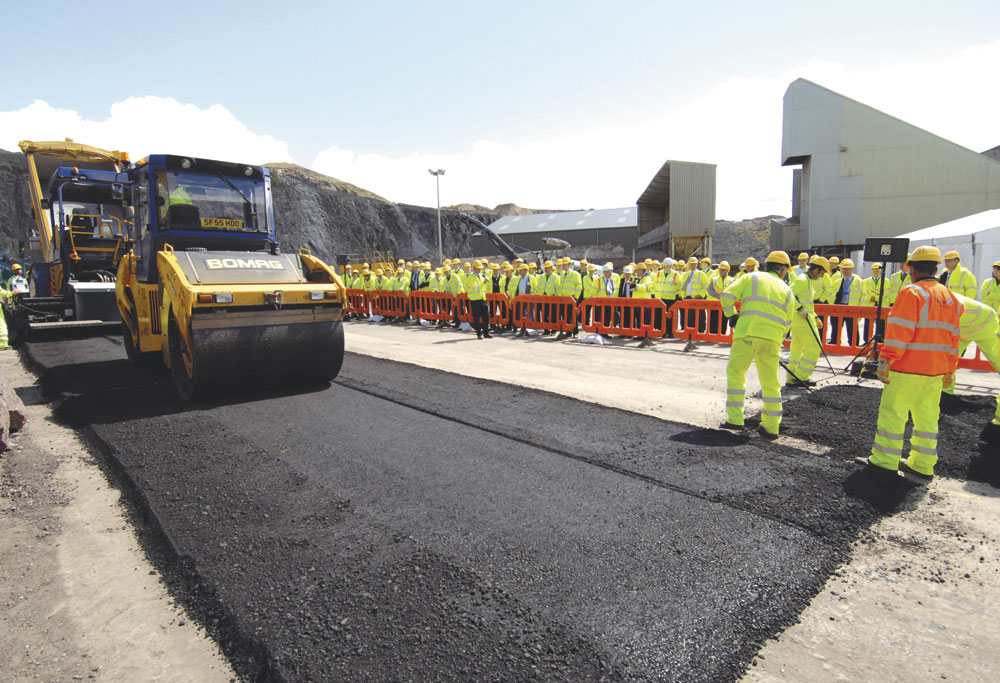
Tayset – a sustainable asphalt developed for Scotland
By Dennis Day, Nynas UK, Richard Cranney and Wayne Fortune, Tayside Contracts, and Moray Newlands, University of Dundee
Tayset is a cold-mix asphalt which makes maximum use of recycled asphalt pavement. Intended to suit Scottish weather, the material has been developed and trialled over several years and has been welcomed as a truly ‘green’ asphalt.
In 2003, Scottish local authority organization Tayside Contracts considered developing a strategy for reducing the carbon footprint of its road application materials and also minimizing the materials it sent to landfill. An approach to government department The Scottish Enterprise Trust for advice on project funding led the company to the Knowledge Transfer Partnership (KTP) fund.
The KTP programme – funded by the Technology Strategy Board – is intended to bring together industry and academia for the benefit of both.
Approval was gained for a research project entitled: ‘Adding value to recycling of construction aggregates by developing and implementing a cold-mix bituminous recycling technology’. The intention was to maximize the use of recycled asphalt pavement (RAP). The partnership formed was between Tayside Contracts, the University of Dundee’s Division of Civil Engineering and Nynas Bitumen.
Plant development, laboratory design and plant mix optimization were the three areas targeted during the development process.
One hot-mix plant was identified within Tayside Contracts’ organization as the means of manufacture. Initial discussions among the partners concentrated on how the plant could be adapted to manufacture cold-mix asphalt using recycled asphalt pavement. Various obstacles were identified, including maximizing the addition of cold RAP into the mixer; processing of RAP feedstocks on site; safe and accurate delivery of cold emulsion binder; and controlling moisture and optimizing the mixing processes.
A project plan for the manufacturing process was developed following a plant and site audit. Government funding from the Waste & Resources Action Programme (WRAP) was available at this time and was applied for successfully.
Laboratory mix design was carried out by Dundee University’s Division of Civil Engineering with advice from Nynas. Nynas have considerable experience of working on cold-mix and also own and operate an asphalt testing facility at Eastham in the UK. Development work targeted a structural grade for use as a pavement base and/or binder course. The feedstock was mainly of dense base macadam (DBM) or hot-rolled asphalt (HRA). The need to add virgin aggregate material was soon identified, to maximize density and reduce the binder contribution in the mix arising from the RAP.
Screened RAP was taken from the crushing and screening process and blended with virgin aggregates of varying proportions. The materials were dried before pre-wet water was added at levels of 0–6% and each was mixed with between 3% and 5% of a 60% bitumen emulsion manufactured using a 40-60 grade bitumen binder. A gyratory compactor was used and the cores were cured at 28°C for up to six months. Core samples were tested at regular intervals to monitor moisture loss and stiffness development. The resultant data indicated two possible candidates.
Once the laboratory study was complete, the focus then moved on to production, ensuring accurate control measures were put in place to achieve the target grading and levels of additive addition identified from the study. The storage life of the mixed material was also studied and optimized at this stage. Stockpile material was monitored and sampled daily and the material
was found to have a shelf life of 21–28 days.
Several road and footway trials were then conducted with varying degrees of
site factors relating to traffic volumes and loading, to establish the material’s suitability of use.
The first of these trials was carried out at Collace Quarry in July 2006. A section of road leading up to the quarry was planed off and the cold mix was laid as a binder course material to a depth of 60mm. The section was then overlaid within 1–2h with hot SMA to a thickness of 30mm. A conventional paver was used to lay the cold mix, which was compacted using a steel-wheeled roller in combination with a pneumatic-tyred roller.
This trial was seen as a robust test for the material’s resistance to permanent deformation. There were no signs of deformation after 44 months – a period when 1,168,000 tonnes of aggregate were transported over the site.
In September 2007, a housing estate road was the site of the next trial. The cold-mix material was offered as an alternative to conventional asphalt as confidence in the new material grew. The construction consisted of 60mm of binder course with a 30mm layer of SMA. A conventional paver and a steel-wheeled roller were used. Planning for this trial included laying parallel sections of cold mix and an AC20 dense bin 100/150 hot mix. Immediately after laying and again after 24h, the in-situ stiffness was monitored for both sections using a Prima 100 dynamic plate tester.
The next trial, undertaken in May 2008, was the most onerous to date. Stirling Council was developing a new Park & Ride scheme for which Tayside Contracts had been contracted to supply hot mix from its Collace Quarry asphalt plant. Stirling was approached about using cold mix for part of the project.
The cold material was approved for use as a basecourse layer in a section of works which included a sharp turning circle for buses. This meant the material had to cope with the heavy stresses of buses turning on very sharp bends. The construction used 500 tonnes of material and saved an estimated 12 tonnes of CO2 compared with traditional hot-mix equivalents.
In the late summer of 2008, John Swinney, Member of the Scottish Parliament and Cabinet Secretary of State for Finance & Sustainable Growth, officially launched and endorsed Tayside Contracts cold-mix asphalt, now known as ‘Tayset’. Following this, in November of the same year, government agency Transport Scotland agreed to Tayset being trialled on a section of the Scottish trunk road network – the first time cold mix had ever been used on a trunk road.
An 800m section of the A90 Perth to Dundee road was rebuilt using cold mix as the basecourse layer. The material was laid in two layers of 150mm during day and night-time working and showed good stability to site traffic.
It also allowed a more rapid construction of the section, due to its ability to withstand traffic immediately without the need for cooling. The constructed trial section saved 43 tonnes of CO2 relative to hot mix. The daily traffic volume along this section of road is approximately 19,500 vehicles per lane per day. Fifteen percent of this is multi-axle heavy goods vehicles.
The trial sections continue to be monitored but, by the summer of 2010, it was clear that the partnership project had successfully delivered a product which has the equivalence to at least an AC20 dense bin 100/150 hot-mix material. The material offers further advantages of reduced construction time due to its ability to withstand immediate trafficking and overlaying without the need for delays arising from cooling.
Tayset is now being positively marketed with the claim that the material represents ‘a greener shade of black’. Tayset is approved for use in the Tayside area and specified as the preferred material of choice for certain applications.
The partnership project has demonstrated that cold-mix asphalt materials can be considered as an alternative to hot mix under certain conditions, and can certainly help industry improve its carbon footprint.
Green asphalt results
The typical results achieved for the cold-mix product are presented above using the British wheel tracking test to BS 598-110:1998 at 45°C; and the Indirect Tensile Stiffness Modulus to BS EN 12697-26:2004. Densities of materials tested during the project were typically between 2.25 and 2.5Mg/m3. Material was also subjected to the wheel tracking test to BS EN 12697-22 at 45°C. This material was cured for 72h at 60°C prior to testing to 30,000 cycles using the large-sized device.
The average rut at the end of the test was between 6 and 6.7%. This result demonstrated the material’s ability to withstand traffic loading. In-situ testing of stiffness using the dynamic plate demonstrated the early life in-situ stiffness of the cold-mix material compared to the AC20 dense bin 100/150 hot-mix material. This again demonstrated good equivalency to hot mix by the cold-mix asphalt during its early life.
Project data and results of extensive testing on the cold mix have demonstrated the material’s suitability for use on category 2, 3 and 4 roads in Scotland; where type 4 represents a minor urban and rural road, and type 2 is suitable for regular bus and HGV traffic up to 10msa.