A Better Focus on Bitumen Tank Levels
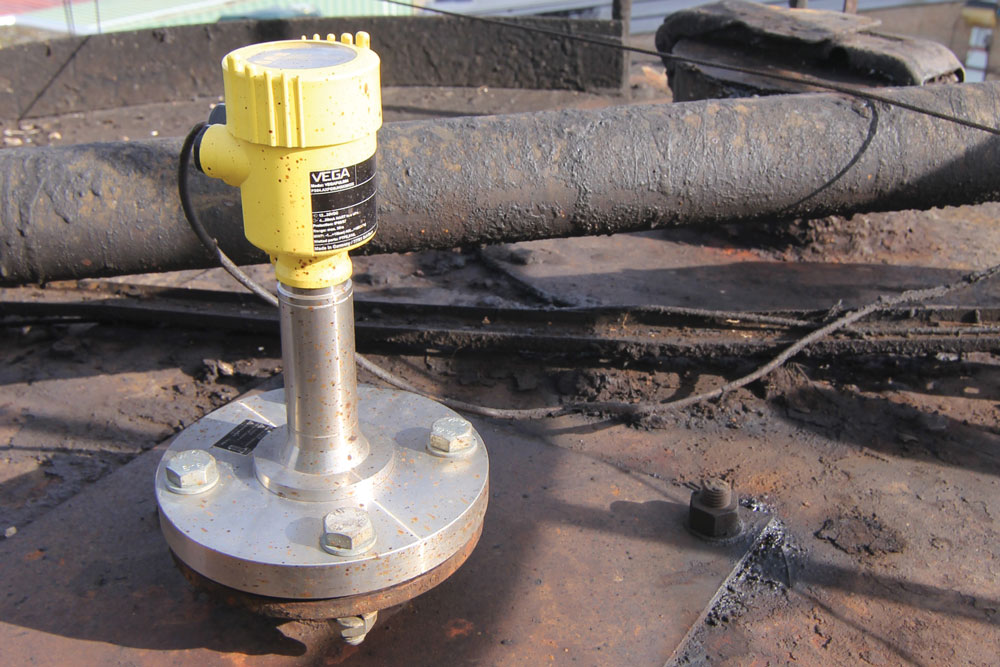
First published in the July 2018 issue of Quarry Management
Increased bitumen tank safety and security with 80GHz radar technology
Bitumen is a difficult and challenging product to measure, with high temperatures, build-up, splashing, sublimation and ready adhesion to contend with. Its handling safety parameters are also very high, with comprehensive safety guidelines from bitumen suppliers’ organizations and industry regulators. As part of this, effective and reliable level control for tanks is of paramount importance.
An 80 GHz radar is currently proving an effective solution for bitumen storage tank levels at Chase Protective Coatings in Rye, East Sussex, who, for more than 70 years, have been developing and manufacturing high-performance industrial coatings, tapes, adhesives and sealants for use in high-reliability applications in range of industries. Among the product lines produced at the Rye plant are cold-applied bitumen tapes for light-, medium- and heavy-duty pipe wrapping, along with other specialist tapes, moulding compounds, grids, marine tapes and PVC pipe wraps.
Chase installed the 80GHz radar – one of the first of this new generation of level sensors in the UK – in the spring of 2016. It has been in operation ever since, already providing a ‘long term’ testimony for what is still a relatively new technology. Its application also provides a valuable insight to where the difference lies between various radar frequencies.
One of the bitumen storage tanks at the Rye plant is not a new vessel and, at around 6m high, nor is it particularly tall either. The previous level device used on it was another manufacturer’s 6Ghz technology radar transmitter. It had never been able to measure the full vessel contents because a very wide beam angle and the presence of a number of internal plates meant it detected too many ‘false reflections’ for the sensor to deal with.
As a result, below a certain point it was impossible to measure the bitumen level in the vessel, as the ‘echo picture’ was too confusing. This caused problems for production planning (how much is left?) and concerns for safety during filling (how much can we safely put in?), so a new solution was sought. Ideally, Chase wanted a device that would measure the level all the way down to the bottom of the tank, without any contact with the product, and be easy to install.
VEGA supplied their latest 80GHz technology radar sensor, the VEGAPULS 64, on a sale or return basis. It was put forward for two main reasons: its performance with regard to build-up and its focusing capability.
When measuring bitumen, the build-up on sensors caused by splashing during filling and the sublimation of tar fumes from heating during storage are challenges that have to be overcome. The high-sensitivity electronics in the latest technology from VEGA benefit from the fact that even heavy build-up has minimal affect on sensor performance, which works consistently without requiring cleaning. Moreover, radar has an additional benefit in that it measures liquid surface level/volume, so its accuracy is not influenced by changes in product density.
Focusing is another great advantage of Chase’s new 80GHz radar, especially when compared with its 6GHz predecessor. The VEGAPULS 64 measuring beam is approximately 10 times better and more sharply focused. Comparing a radar from each technology, both equipped with a 3in antenna, the 6GHz measuring beam would be in the region of 30°, whereas at 80GHz it is just over 3°.
Improved focusing means that the radar signal path between the sensor and liquid surface does not ‘see’ any interference from the vessel walls or pick false signals from rings of build-up or vessel internals. This results in non-contact radar devices that are easier and faster to set up, and less likely to need tweaking to ‘remap’ false signals in vessels, thus delivering greater accuracy and reliability in the long term.
After the trial period ended in mid-2016, Chase purchased the VEGAPULS 64 device. The main benefit to them is the ability to measure reliably and safely down to the bottom of the vessel, thereby allowing smoother planning of production and effective scheduling of bitumen deliveries. Moreover, this device also is also equipped with Bluetooth communication technology, which means that it can be remotely and safely accessed at any time, to check level readings or diagnostics, without anyone having to climb the vessel and without a physical connection to the sensor.
The engineering manager at Chase Protective Coatings in Rye is particularly happy with the decision to purchase the device. ‘We ‘haven’t had a reading down at that level for years,’ he remarked.
For more information visit: www.vegcontrols.co.uk
- Subscribe to Quarry Management, the monthly journal for the mineral products industry, to read articles before they appear on Agg-Net.com