Taking The Fretting Out Of Direct-mounted Gearboxes
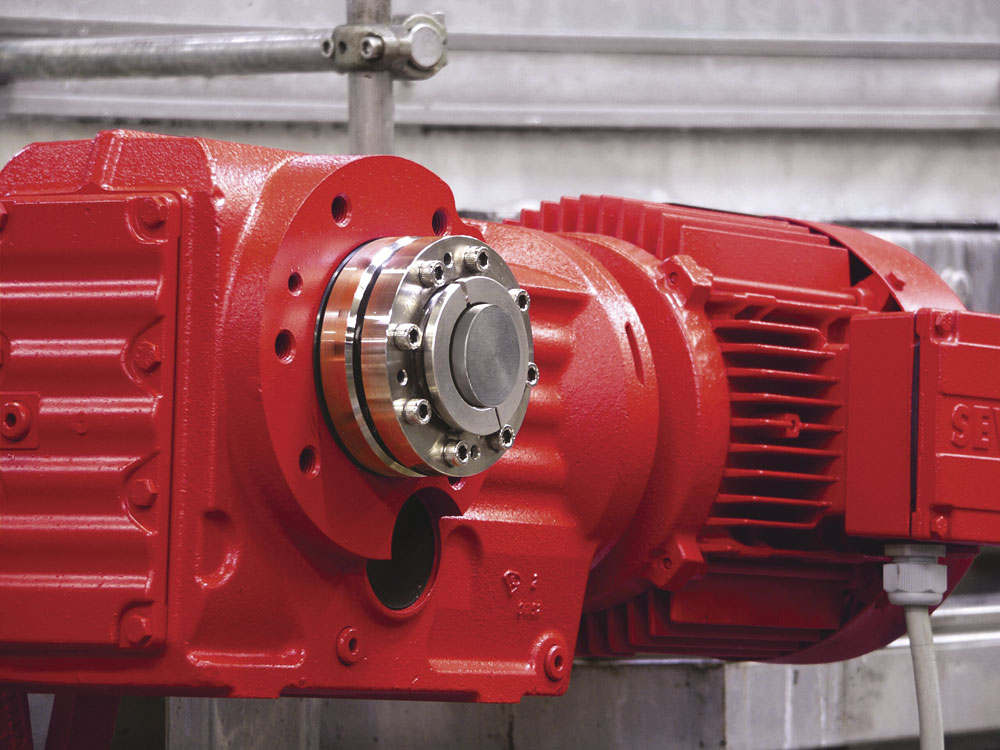
While the use of hollow-shaft-mounted gear units has reduced transmission losses, increased safety, and minimized set-up time, it has led to a greater frequency in the incidence of fretting corrosion. Ian Tribe, SEW-Eurodrive national product manager for industrial gear units, explains what fretting corrosion is, what causes it, why it is a problem, and what can be done to mitigate its effects
Shaft-mounted gearboxes are a relatively contemporary development in the drives solutions industry. Prior to their adoption, gearboxes were connected to drive applications through flexible couplings or via parallel shafts interlinked by means of sprockets or V-belt pulleys. These traditional drive solutions require accurate alignment and, therefore, tend to be time-consuming to set up. The additional transmission elements also tend to reduce drive efficiency. Moreover, the exposed couplings require extensive guarding to prevent operator injury.
To remedy many of these issues, a solution was devised whereby a gearbox with a hollow shaft could be directly mounted on the customer’s shaft, eliminating the need for additional transmission elements. This design has many benefits, including an easier and quicker initial set up, without the same degree of alignment issues. The reduction in exposed transmission elements both increases the transmission efficiency and reduces the need for much of the safety guarding previously required. However, this solution does result in a new problem for the drives industry – fretting corrosion.
Micro-welding
Fretting corrosion is widely experienced throughout industry and is just as widely misunderstood. A common misconception is that rusting is to blame. Although its appearance can be similar to oxidation, fretting corrosion is not reliant upon the ingress of water and can occur in totally dry environments. It arises due to relative movement between contact surfaces, which results in micro-welding between the two. For a direct-mounted gearbox, the interface between the inner face of the hollow gearbox shaft and the outer face of the solid customer shaft provides the contact surface. Fretting corrosion here can effectively lock the two shafts together.
While this is not a significant problem during gearbox operation, it becomes a serious issue when the gearbox needs to be removed from the customer’s shaft for routine maintenance or replacement. It is not uncommon for ‘stubborn’ gearboxes to require the use of presses – often exerting forces in excess of 100 tonnes – to effect their removal. This is not only time-consuming, but can also result in damage to the gearbox shaft, the customer’s shaft, or both.
Damaged shafts frequently require resurfacing or even replacement as a consequence of the force used to separate them. In extreme instances, where it is not possible to remove the gearbox by the application of force, the shaft may need to be cut, creating additional challenges in restoring the gearbox and the customer application. Whatever remedial action is required, fretting corrosion causes disruption, increased delays and elevated costs for gearbox removal and reinstatement.
It is, therefore, advantageous to minimize fretting corrosion, and to accomplish this it is necessary to understand how it originates. Fretting corrosion occurs in non-positive or positive connections where the surfaces make relative movements under the influence of force. In many cases, the amplitude, type and speed of this relative movement has a direct effect on the extent of the build up of fretting corrosion. Relative movement between the two shafts can occur on a number of axes and take a number of forms.
Fretting factors
Axial instability between the two shafts can cause relative movement, as can angle errors caused by incorrectly mounted shafts. Where concentricity of a customer’s shaft is not consistent, relative movement between this and the hollow shaft can result. Likewise, insufficient insertion depth of the customer shaft into the gearbox hollow shaft can also cause excessive movement – a consequence of the fact that hollow shafts tend to be manufactured with a larger internal diameter in the centre of the shaft compared with the ends.
Similarly, the choice of torque arm can have a bearing on the occurrence of fretting corrosion. The use of rigid torque arms can generate constraining forces that are transmitted to the shaft. These are often chosen to alleviate ‘wobble’ issues, but do so at the expense of fretting corrosion. Torque arms with flexible elements, by contrast, tend not to mitigate wobble issues, but can prevent the constraining forces that increase the severity of fretting corrosion.
Fretting corrosion is further exacerbated by the presence of large normal forces between the surfaces, high temperatures and a long strain duration. While not reliant on the presence of water to occur, fretting corrosion tends to be more pronounced where there is an ambient medium (such as moisture from cleaning agents) and where there is an absence of lubricants. Where these factors can be avoided or minimized, the severity of fretting corrosion may be mitigated. However, it is important to note that the formation of fretting corrosion cannot be completely prevented, only minimized.
Mitigation methodologies
A common method of minimizing fretting corrosion is by the use of shrink discs. If these are designed and installed correctly, the shafts can be prevented from moving relative to each other. However, shrink discs used in isolation at the non-drive side of the gearbox may cause alternative damage, especially if the overhung loads on the output end are too high. In this scenario, the bushings at the output end of the gearbox might widen, which, in turn, can result in bending loads being transmitted to the customer’s shaft, leading to the possibility of catastrophic failure.
SEW-Eurodrive have taken development of the shrink-disc solution a stage further with their TorqLOC key-less hollow-shaft mounting system. This design comprises a shrink disc, a clamping ring and two conical slotted bushings (made from bronze, nickel-plated steel or stainless steel) that are inserted into the hollow shaft at each side.
TorqLOC reduces fretting corrosion to almost zero as there is no longer a clearance between the customer’s shaft and the hollow shaft. With this solution, fretting corrosion is only able to occur, if at all, on the bushings, allowing for much-simplified gearbox removal. Once the shrink disc has been released, the gearbox will slide off the customer’s shaft relatively easily, leaving the bushes behind. Even after a long running time, these bushings are easy to remove with minimal force, given their split design and the fact that they are made of a non-corrosive material.
The use of the tapered bushing also means that TorqLOC offers great flexibility in achieving conformance between the customer’s shaft and the hollow shaft. Unlike alternative designs, there is no requirement for the customer’s shaft to be machined to quality level h6, as the system can accommodate tolerances up to drawn material at h11. Furthermore, by using SEW-Eurodrive’s interchangeable bushings, the one hollow-shaft system can be adapted to different standard metric and imperial shaft sizes, up to 5mm below the nominal diameter.
Summary
With the ability to disassemble the direct-mounted gearbox from the customer’s shaft simply and quickly, servicing requirements are facilitated with a negligible chance of damaging the customer’s shaft or the hollow shaft of the gearbox. This can allow the gearbox to remain in service for longer with reduced downtime. As a result, end-users can now enjoy the many benefits of direct-mounted gearboxes, without having to contend with the long-suffered problem of fretting corrosion.