Remote surveying and geological mapping in quarries
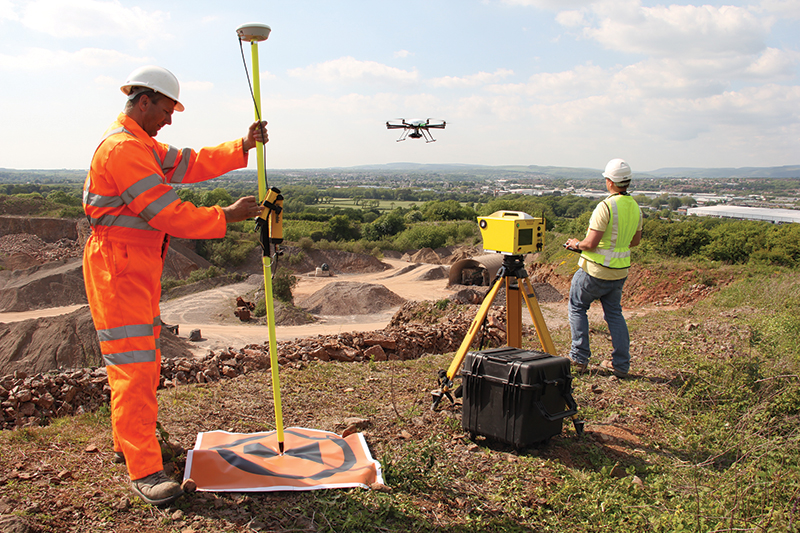
First published in the April 2014 issue of Quarry Management as Something in the Air
Remote surveying and geological mapping in the quarry environment using unmanned aerial vehicles (UAVs)
By A.C.Charters, QuarryDesign Ltd
In the March 2011 issue of Quarry Management A.P. Wilkinson of QuarryDesign wrote an article on the ‘hands-off’ approach adopted for geological and geotechnical mapping using long-range high-definition LiDAR surveying equipment. Since 2011, technical advances in unmanned aerial vehicles (UAVs) have allowed the remote collection of data from the air. The aerial collection of data complements ground-based LiDAR data and maintains QuarryDesign’s ethos of obtaining survey, geological and geotechnical data in a remote manner. The integration of both terrestrial LiDAR- and UAV-derived data was recently recognized by the Mineral Products Association in its 2013 annual Safety Awards, where this approach to surveying resulted in a ‘Runners Up’ award for QuarryDesign in the hotly contested Engineering Initiatives category.
Until the development of LiDAR and, more recently, commercial UAV systems, the collection of some survey, geological and geotechnical data had been difficult to obtain safely and quickly in the quarry environment. This paper outlines the training, legislation, UAV types and payloads, and flight planning methodology required to operate UAVs in quarries. Specific site examples are examined showing how remote data survey methods can eliminate the need for personnel to be exposed to safety hazards associated with quarry faces, stockpiles, lagoons, haul roads and moving vehicles or plant.
Commercialization of UAVs
Research in UAV technology has been increasing since the late 1980s. Initially, the applications for this technology were centred on military usage and were generally outside the commercial sector. The main reason for this is that military UAVs generally operate outside civilian airspace and do not have to comply with civil airspace standards and rules.
The use of photogrammetric techniques to carry out ground surveys of large greenfield or existing quarries is well established using manned light aircraft. However, flying at low altitudes and airspeeds to obtain high-resolution photography for detailed surveys comes with inherent risks, not to mention significant costs. UAVs are far cheaper to run and easier to launch, relocate and refuel. Also, with today’s increased environmental awareness, a UAV’s environmental footprint is significantly less in terms of material requirements and pollution than piloted aircraft.
Recent technological developments in the miniaturization of on-board GPS, battery technology, lightweight brushless motors and smaller-format high-resolution cameras have led to an explosion of commercial UAV systems being made available to a wide range of sectors, including agriculture, forestry, policing, civil engineering, and mining and quarrying.
Training and legislation
A quick search of YouTube will show that the use of UAV systems is widespread in the civilian population. The relatively low cost and simplicity of UAV design has resulted in a flood of vastly different models into the airspace. Not every aircraft is built to a rigorous level of safety (particularly kit models) and often operators are untrained fliers – a serious issue considering that these aircraft share the same airspace as manned and passenger aircraft. However, the requirement by the UK Civil Aviation Authority (CAA) to obtain a ‘Permission for Aerial Work’ when flying commercially requires operators to register and train with EuroUSC to obtain a Basic National UAS Certificate (BNUC). This qualification certifies the UAV airframe airworthiness and that the pilot has achieved a level of competency recognized by the CAA.
The majority of small UAVs used commercially in the UK are flown on a BNUC-s (small) Certificate for fixed-wing and rotary vehicles with a maximum take-off weight of less than 20kg. Currently, EuroUSC training is recognized in the UK and its territorial dependencies, Ireland, Spain, the Netherlands, Belgium and Hong Kong, and is being rolled out to the rest of the European Union.
The BNUC-s Certificate allows an operator to fly to a maximum height of 120m (400 ft) and up to 500m laterally from the pilot’s location. For missions extending more than 500m from the pilot a second pilot is needed and an additional Extended Visual Line of Sight (EVLOS) Certificate is required. Although it is a grey area under CAA rules, it is generally accepted that the use of photographic UAV systems requires the permission of the landowners that are being overflown.
Types of UAV
There are two main types of UAV that are suitable for surveying and geological work in the quarry environment:
Fixed wing
These systems, which generally incorporate a single propeller powered by a brushless electric motor with lithium batteries, are ideal for aerial mapping and terrain modelling of larger areas. They can be launched from a relatively flat take-off location using just the propeller, although some systems use an inclined catapult rail to assist take-off. Landing can be either manual or fully automatic and some systems utilize reverse-thrust propellers to minimize landing distance.
Advantages of fixed-wing systems
- Flight speed up to 50 miles/h
- Flight duration up to 50 minutes
- Extended range up to 40 miles
- Ability to fly in winds up to 40 miles/h.
Disadvantages of fixed-wing systems (compliant with BNUC-s)
- Need a relatively flat landing strip (up to 150m x 30m)
- Inability to hover to observe a selected hazard or geological feature
- Large turning circle at the end of each flight line
- Generally house ‘compact’ cameras which may produce lower-resolution images
- Generally operate without stabilized gimbals, which, in windy conditions, means that the photographs may be variably oblique and not vertical (this can result in holes in the final stitched orthophotograph).
Multi rotor
These systems generally have between four (quadcopter) and eight (octocopter) individual brushless electric motors/propellers powered by separate lithium batteries. They are able to hover, move vertically and horizontally, and rotate, which makes them ideal for detailed inspection work of inaccessible plant or potential rockfall hazards on high faces. The area required for take-off and landing is small and take-offs and landings can be either manual or fully automatic. Most multi-rotor systems offer some redundancy and retain the ability to fly with the loss of up to two motors (on Octocopter systems) or the loss of up to two batteries on four-battery systems.
Advantages of multi-rotor systems
- Small footprint required for take-off and landing
- Ability to hover, useful for hazard inspection in real time
- Stabilized camera on ‘active’ gimbals to reduce pitch and roll inaccuracies
- Generally greater payloads – up to 2.5kg (suitable for full-frame digital SLR cameras)
- Payload mountings can be easily modified to suit various camera types (DSLR, infra-red, thermal, multispectral etc).
Disadvantages of multi-rotor systems
- Reduced flying time (depending on wind speed, generally less than 20 minutes)
- Reduced air speed (although this is sometimes an advantage for face inspections)
- Generally reduced ability to fly in winds greater than 20 knots
- Smaller area coverage per individual mission.
Types of payload
Most small UAV systems can carry a variety of payloads, such as:
- compact to full-frame digital cameras used for traditional photogrammetric techniques
- multispectral cameras (useful in agricultural applications to monitor vegetation growth/fertilizer dosage, or the emission spectra of certain minerals or weathering zones)
- thermal imaging using mini thermal cameras (useful to identify temperature ranges to less than 0.1°C accuracy, and helpful for finding hotspots on plant or landfill sites etc).
UAV systems often carry an additional real-time video camera which transmits video back to the pilot via First Person View (FPV) goggles or an additional camera operator with a separate video screen. The latter method is particularly useful for undertaking hazard inspection of potential rockfall on high faces, old legacy benches with no safe access, or inaccessible plant.
Flight planning, survey accuracy and data processing
Commercial UAV systems generally use software on laptops or tablets to plan flight missions and monitor flight controls in real time during air operations. Google Earth or Bing imagery is used to plan the mission and a series of flight lines is generated depending on the area selected, flight height, image overlap and camera lens focal length. The co-ordinate waypoints for each leg of the flight are automatically calculated and sent via a wireless link to the onboard UAV GPS before the mission starts. Similarly, the software also controls the signal for taking photographs during the flight.
It is essential that sufficient overlap is allowed for each photograph (usually not less than 40%) to accurately generate a digital surface model (DSM) and associated orthophotograph (a computer manipulation that stitches all the photographs together to create a new vertical photograph). Some UAV systems geotag the photographs with a latitude and longitude position from the onboard GPS and this is used in the initial photogrammetric processing. However, these positions are not accurate enough (±5m) for tying to existing survey detail picked up by conventional total station or GNSS survey systems.
To increase the accuracy of the survey a number of ground control points (GCPs) need to be surveyed. Depending on the size and vertical range of the survey area, a minimum of four GCPs are required and generally the more the better. The GCPs can be either permanent markers set in safe locations around the quarry to allow repeat surveys, or temporary markers (often used for one-off surveys). It is essential that the GCPs are large enough to be seen on the photos during processing. With sufficient GCPs a variance of as little as 2–5cm can be achieved compared with traditional quarry survey equipment.
A typical mission flown by a multi-rotor system for a 500m x 500m area (25ha) will take around 9–12 minutes to fly (at 6–8m per second) at a height of 80–90m, and will generate an orthophotograph of around 1.5cm per pixel.
On completion of the flight, the photos are downloaded to 3D photogrammetry software where they are processed using the GCPs to achieve higher accuracy. A point cloud is generated which can either be processed on a ‘local’ co-ordinate system or geo-referenced to the national co-ordinate system in the same manner as traditional surveys. It can also be converted into a triangulated mesh or wireframe digital surface model (DSM), which may include vegetation and buildings, or a digital terrain model (DTM) where points above an interpolated ground surface are removed. Some photogrammetry and point-cloud software generates auto break-line data (top of face, bottom of face etc) and spot levels. From these DSMs or DTMs, the relevant data (break-lines, cross-sections, meshes or xyz points) can be exported into other suites of software for the production of plans or for further geological and geotechnical investigations or analyses (as detailed in A.P. Wilkinson’s March 2011 Quarry Management paper).
Site investigation by UAV
When a combination of both vertical and oblique photographs is taken by the UAV, some photogrammetric software suites will allow the generation of both normal and arbitrary vertices, which in turn generate 3D rock-mass orientation planes (even overhangs). Although not as precise as data collected using long-range high-definition LiDAR, integrating the rapid-acquisition UAV data and the more accurate LiDAR-acquired data can contribute greatly to the site investigation element of the ‘Regulation 33 Geotechnical Assessment’. An example showing the integration of these data sets is presented in figure 8, where QuarryDesign recently created an accurate geological and geotechnical survey of a particularly challenging large Alpine rock-mass.
A 3D digital terrain model produced from a UAV-derived orthophotograph produces a perfect match between the draped photography and the DTM break-lines. An extremely high-resolution photograph (2cm per pixel or better) can, therefore, be a very effective tool to digitize geological boundaries, such as bedding, faults etc, or other linear geological features.
An example of the type of detail obtained from a multi-rotor UAV employing a full-frame digital SLR mounted on an active gimbal is illustrated in figure 9. The UAV survey comprised four 10-minute flights in order to remotely inspect the quarry faces, determine geological boundaries and allow rock-fall analysis above historic inaccessible faces. A previous high-resolution LiDAR survey of the quarry had identified a large loose block. However, it was not possible to measure accurately by LiDAR the dilation on the block’s release joints because of the scanning angles (even from the quarry rim). Therefore, a remote inspection via UAV was planned over the target block and by employing photogrammetric modelling at the same time, the rockfall-retarding effect of the remnant benches and the more recent rock traps could be assessed.
The vertical photographs confirmed the width and nature of the release plane and assisted Aggregate Industries in developing an appropriate action plan for this area.
Aggregate Industries also wished to prove the efficacy of their rockfall mitigation measures adjacent to the main haul ramp. Their safe systems of work naturally exclude surveyors from working within or upon rock-trap bunds, and even by locating the LiDAR scanner at the rim of the quarry an accurate survey within the rock traps could not be obtained. By employing the UAV an accurate survey inside the rock traps was produced and more than 200 detailed cross-sections were quickly generated (of which 20 were analysed in Rockscience’s 2D RocFall software). The overhangs and ledges on the detailed UAV survey were clearly seen to be playing a major part in the potential trajectories of rockfalls. The survey also identified the potential loss of rockfall storage in partially infilled rock traps on remnant benches. The UAV survey and subsequent analyses proved the efficacy of the existing rock traps, and for a few short sections at critical points along the haul road additional measures were recommended.
Another example of the use of the UAV to survey difficult-to-access terrain was at Hope Construction Materials’ recently acquired Dowlow Quarry. Here, a large silt lagoon exists in a previously worked-out quarry void. As with the previous example, it would have been unsafe to survey this lagoon using traditional methods, so Hope requested that a safe remote UAV survey be undertaken (a 3D image of which is shown in figure 11).
In the last year or so there has been a significant increase in interest in the use of UAVs to undertake stock surveys in quarries and associated industrial operations. An increasing number of operators are expressing concerns about surveyors walking over large stockpiles or on stockpiles located above ‘live feed’ reclaim tunnels and/or under radial conveyors.
Figure 12 shows Hargreaves’ Energy & Commodities division coal-stocking operation at the Redcar steelworks operated by SSI and Tata Steel. The entire stock field covers 63ha and can be surveyed in a day using a UAV (comprising seven flights), compared with three to four days by traditional survey methods. As well as the high-definition aerial photograph which can be draped over the resultant stock DTM, the time stamp for each stockpile photograph is also useful to reconcile against stock additions and depletions in this continuous 24h operation.
Conclusion
As with all equipment, by carefully selecting the right UAV for the task, these systems can remotely (and hence safely) obtain valuable video and photographic data. Such data can be used to perform remote face inspections and can be processed to create accurate 3D models of the quarry, from which vital geological and geotechnical information can be obtained.
For more information, contact QuarryDesign Ltd on tel: (01275) 543983; or email: info@quarrydesign.com
- Subscribe to Quarry Management, the monthly journal for the mineral products industry, to read articles before they appear on Agg-Net