Remote Survey Success
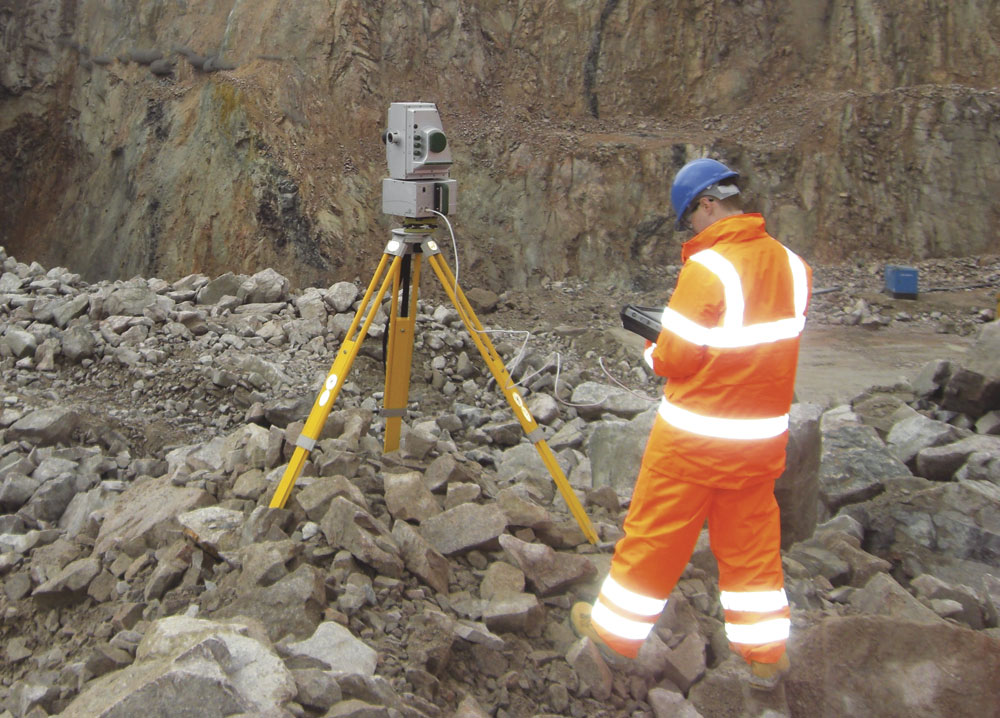
Maptek technology and Oakes Surveys help relieve quarry survey pressure
Working in partnership with Oakes Surveys, providers of measurement solutions throughout the UK and Europe, Maptek have developed an innovative approach to monitoring quarry rock faces.
Managers at a large quarry in Leicestershire wanted detailed information on the quantity and size of rocks that were falling from the quarry faces. As the site had been operating for several decades, weathering of the higher benches had resulted in loose rocks falling to the quarry floor. Finding the source of the break-offs was vital to ensure continued safety for the quarry’s staff.
Andrew Beardsley from Oakes Surveys approached Maptek’s I-Site sales manager, Graeme Cowie, for help in collecting and processing data to improve the understanding of changes in the quarry excavations. Maptek had the 3D survey technology, with their I-Site 8800 laser scanner able to measure data at the appropriate point density for detecting 150mm changes in a rock face from a distance of more than half a kilometre.
The challenge was to identify the location of the dangerous faces which were the source of the rockfalls, as well as the number of falls in a given time and the size of the rocks. Once the quarry management had a better understanding of where the danger areas were, they could execute appropriate safety procedures to protect the workforce. Laser scanning was perfect for collecting this information and Maptek’s I-Site Studio software ensured accurate interpretation of the data to produce useful results.
This project gave Oakes Surveys and Maptek an opportunity to combine skills and expertise to develop a solution for quarry management.
Surveying a 150m deep quarry measuring approximately 1,000m by 600m required a scanner capable of delivering high point density at long range. The minimal noise delivered in the I-Site 8800 scan data ensured an error-free digital representation of the quarry faces.
After completing test scans, quarterly surveys were conducted from the beginning of 2011 to record changes in the rock faces. Safe areas were created by site engineers to provide access to positions where the view of the quarry faces would give the best data – this allowed safe access to preferred locations, although the long range and portability of the I-Site 8800 negated some access issues. Weather conditions could have affected data collection, but as the scanner is certified to regulation IP65 for weather protection, work was able to continue unabated.
The inbuilt camera of the I-Site 8800 scanner provides a panoramic preview photograph on the hand-held tablet, allowing accurate and easy definition of scan parameters. Scan acquisition is integrated with survey control, with particular attention given to tight control over each scan set-up on every site visit to ensure the best possible scan registration.
High-definition scan data was recorded from several scanner set-ups to collect point data for the entire quarry. The team set up the scanner at the same location on subsequent visits to record complete quarry point data sets. Hundreds of millions of data points were collected at each session, with the X, Y, and Z for every data point accurately located within the site co-ordinate system.
The point-cloud data was processed and accurate triangulated surfaces were created using I-Site Studio software. Quarry surface data was divided into panels for comparing surfaces between quarterly site surveys.
The I-Site Studio ‘Analyse Surface Change Tool’ was used to analyse the difference between data sets. Displaying the data with a colour spectrum clearly showed the size and location of the changed surfaces. Areas of change down to approximately 150mm were reported along with the location and size of the material that had fallen. Moreover, it was sometimes possible to reveal where material had landed by identifying changes to the bench surfaces.
Data from consecutive visits could be easily compared. In addition, recent data could be compared with that from the first visit to indicate change from the start of the project, leading to greater understanding of how the faces are developing and changing over time.
The software report highlights areas where rock is falling or not falling. Accurately identifying the location of the dangerous zones means management can take the appropriate steps to place safety and ‘stand-off’ berms to protect personnel from falling rock.
Detailed cross-sections of the quarry faces can also be generated from the data for rockfall analysis in simulation software. The highly detailed rock surface profile gives a far more accurate representation of the face for producing better simulations.
According to Maptek, this method of monitoring rockfall from quarry faces is cost-effective for site operations. Understanding the danger areas allows management to manage the risk without installing expensive netting on large areas of the quarry which have a low risk of rockfalls.
Management can target their response appropriately to danger areas, placing safety berms and complying with health and safety laws. The Health and Safety Executive ‘Target Zero’ initiative is more likely to be met as the risk-control effort becomes more tightly co-ordinated.
Accurate data that better indicates the source of break-offs helps ensure safer working conditions, and planning becomes more efficient with safer face monitoring. The result is a new approach to analysing rock faces and structures that is safe, cost-effective and accurate. The bonus for Oakes Surveys is that they can roll this solution out at other quarry sites.
For further information contact Maptek on tel: (0131) 225 8447; email: graeme.cowie@maptek.co.uk; or visit: www.maptek.com