Process Pump Perfection
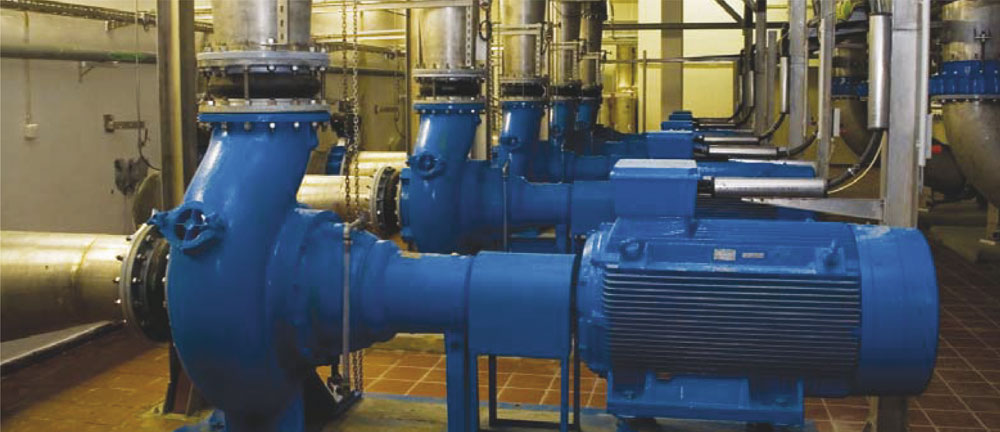
Optimizing centrifugal process pump performance and efficiency
By Jeremy Salisbury, managing director, Brammer UK
Centrifugal process pumps often work in hostile and stressful operating conditions. Consequently, they can fail prematurely – resulting in lost productivity from unplanned downtime.
Improved reliability, reduced maintenance and lower energy consumption are all achievable by ensuring pumps operate at optimum speed and efficiency.
Common problems
Cavitation is a significant cause of wear, especially in pumps required to start quickly. When a liquid undergoes rapid pressure changes, cavities form in its lower-pressure regions. When entering high-pressure areas, these bubbles collapse, causing cyclic stressing and, ultimately, surface fatigue to the impeller, pump housing, or both.
Consequences of unscheduled stoppage or failure
Rapid pump stoppage – or failure due to poor maintenance – can also create significant problems. A sudden flow reduction can mean a valve closes rapidly, resulting in water hammer (also called fluid hammer or hydraulic shock), ie a pressure surge or wave resulting when a fluid stops or changes direction suddenly. This can cause noise, vibration, blown valves, leaks and even pipe collapse in highly pressurized systems.
Meanwhile, vibration from component wear or misaligned and poorly balanced shafts can increase energy usage and maintenance costs, and even result in product failure.
Optimizing efficiency through speed control
Variable-speed drives (VSDs) or inverters are proven in reducing energy usage as well as helping optimize reliability and closing the loop with regard to PID (proportional–integral–derivative) functionality.
For example, a VSD which reduces by 10% the speed of a 22kW pump operating 24h a day for 300 days annually can pay for itself through reduced energy usage in just eight months, depending on electricity costs.
Energy is key given that many pumps are specified larger than needed for the application. A small speed increase to raise flow rate can potentially increase power demand significantly, meaning contingencies are successively built into the design process. However, a VSD delivering a 4% speed decrease typically pays for itself in around two years through reduced energy costs.
The only rider is that VSDs cannot be fitted to pumps operating under high head pressures. This is because pressure varies in proportion to speed, as per the pump affinity laws. In these cases, speed variation using any method is not advisable without due caution.
Other options include v-belts, especially where it is impossible to directly couple an online motor to a pump. Potential issues, such as slippage, have been largely circumvented by the latest synchronous belts, which, once fitted and tensioned, do not require regular re-tensioning.
Meanwhile, the latest synchronous carbon belts offer far greater power-carrying capacity than was previously achievable as well as exceptional flex fatigue resistance, meaning they bend more easily around pulleys and deliver a typical 5% energy-efficiency advantage over v-belt drives.
VSD or soft start?
The choice between VSD and soft start depends on system conditions, number of starts, load on the pump and how it is currently being started.
For smaller pumps, a VSD is generally preferable, while a soft start typically becomes economical for 22kW pumps or larger. However, there is a crossover area where either method is suitable, depending on application requirements. For example, an application starting once per month and running at a constant speed will require soft start, however a VSD will be more appropriate if demand from the pump varies.
Overall performance can also be increased by fitting pressure sensors in applications with variable throughput. The sensor will feed back any reduced flow requirement to the VSD, which will cause the motor to slow accordingly, delivering energy savings with no risk to the pump.
Combating ragging
‘Ragging’ – fouling of impellers – can be highly damaging to pump performance. It can cause partial or complete blockage, with problems of downtime extending over several days, as well as cleaning costs, with back-up systems placed under additional pressure. The worst cases can cause effluent leakage with all the associated financial, legal, environmental and reputational costs.
This can be negated by an intelligent pump-control system which monitors overall performance and triggers an automated cleansing cycle if performance crosses pre-programmed ‘out of profile’ boundaries.
Importance of condition monitoring
As in any industrial application, identifying problems before they occur is integral to optimizing efficiency and minimizing downtime.
This is best achieved through modern condition-monitoring systems, such as sensors and accelerometers, which monitor vibration levels and temperature changes with information downloadable to a hand-held system or, for remote or hard-to-access locations, fed into a central system which can provide warnings of unusual or undesirable readings, allowing planned maintenance for minor issues or a complete shutdown for major work or replacement. The leading innovators have developed software tools which suggest likely causes and prescribed remedial actions, based on data provided.
Key proactive maintenance points
Pumps should always operate on a stable baseplate with shafts optimally aligned and regularly lubricated according to manufacturer instructions. If either condition is not satisfied, poor performance and, ultimately, failure are almost inevitable. And, as with any other component, simply replacing parts without detailed investigation into a problem’s root cause will not re-establish optimum performance.
When disassembling a pump, the engineer should always check whether the coupling guard is rubbing against the coupling; whether there is grease or oil on the inside of the coupling guard and on the baseplate of mechanically flexible couplings; and whether the flexible coupling displays any indication of distress.
Before the coupling is taken apart, shaft alignment measurements should be taken and compared against previous measurements to see if any change has occurred. The cause of any shift should ideally be identified.
The flexible coupling should then be disassembled, noting the presence and condition of any lubricant in the coupling and signs of excessive wear, comparing it with a new coupling if necessary. A worn coupling may need replacement.
The pump should be visually inspected for problems such as loose foot bolts and pump casing bolts, cracked casings, low lubricant levels, loose shim packs or missing shims, leakage from seals, and shaft discoloration.
The amount of shaft ‘freeplay’ should then be established. This will indicate the existence of any bearing problems in the pump or driver. A check should also be made for excessive shaft or coupling hub runout. Both of these can be simply undertaken using a dial indicator.
The level of piping stress on the pump should be checked, with adequate piping supports fitted in the suction and/or discharge piping if excessive stress is found. In extreme cases the piping may need to be cut and refitted. Finally, the piping should be disconnected and a check for excessive ‘soft foot’ problems made using an appropriate alignment measurement tool.
Once a pump has been effectively configured and any repairs undertaken, condition monitoring should continue to identify any areas for improvement in efficiency and productivity.
The following points should be checked monthly: priming speed, capacity, noise in the pump casing, gaskets and O-rings, shaft seal leakage of air and water; hose, hose washers and suction strainer. Six-monthly checks should include: impeller wear; clearance between the impeller face and the volute; shaft seal wear; and shaft sleeve wear; while the casing and volute passages should also be cleaned.
This combination of regular checks and proactive maintenance, coupled with appropriate control methods, will contribute significantly towards optimizing efficiency, minimizing downtime and reducing whole-life costs.
For further information visit: www.brammer.biz