No Need To Dig Deep For Generator Solutions
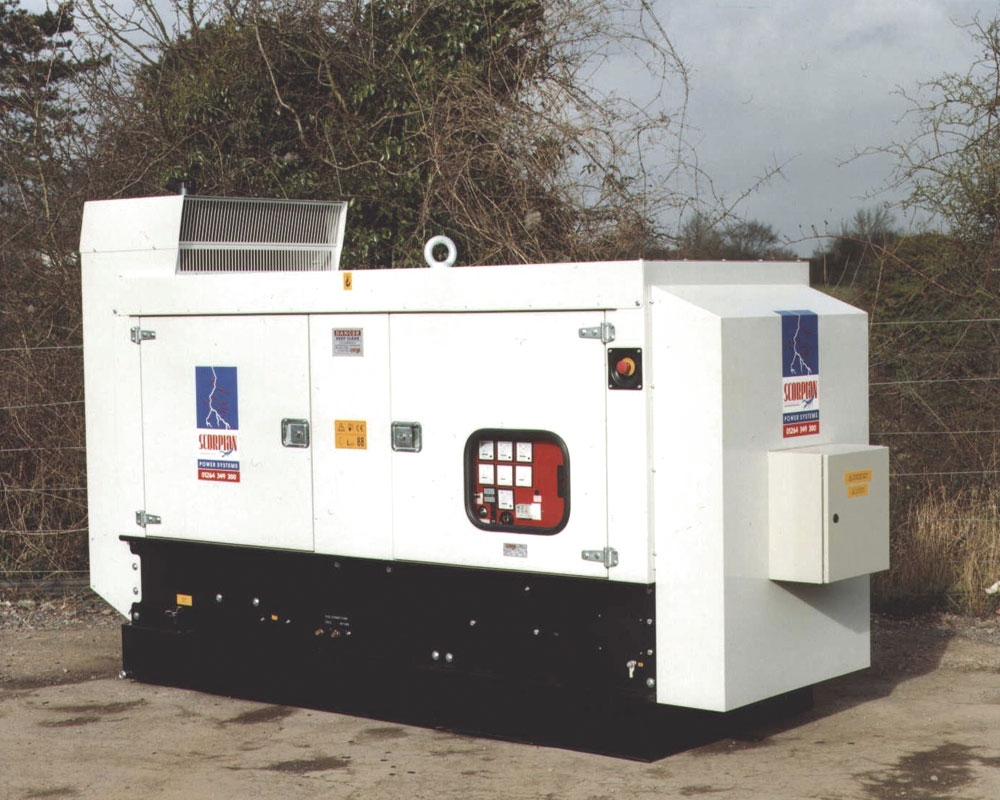
Guidance on generator selection and maintenance
Quarries are now usually connected to the national grid but are predominantly located in areas where power cuts frequently occur. Therefore, ensuring a constant and stable power supply to the site is essential to avoid disruption to services. The first step in providing power protection is to understand the leading causes of power-related problems. A myth that needs to be dispelled is that power is perfect. Research carried out on power supply disturbances throughout Europe shows great differences from place to place and between different types of installations.
Some important facts and figures about power outages include:
- Over one third of companies take more than a day to recover from the disruption caused by a power failure, and 10% take more than a week.
- Because of a power failure, 33% of companies lose between £10,000 and £250,000, 20% lose between £250,000 and £1 million, and 15% lose over £1 million.
- Insurance claims take a long time to settle – well after the disaster has occurred.
- Ninety per cent of all companies that experience a computer disaster and do not have a survival plan go out of business within 18 months (Source: Price Waterhouse)
For quarry managers who have adopted a ‘crossed-fingers’ strategy towards potential power-related disasters, now is the time to take action against the distinct probability of a potentially catastrophic mains failure. A wide variety of generators is available, ranging from small units that can power a single appliance to large systems that are suitable for all major prime power and standby power applications.
AC or DC generators
The mix of equipment making up the load will most likely decide the choice between AC and DC power for sites. When selecting an AC generator, a number of points needs to be considered. A proportion of the load is likely to consist of non-linear switch-mode equipment and this can adversely affect the alternator’s performance because of harmonic distortion reflected to the generator output. In extreme cases, the engine speed, and consequently the electrical frequency of the generator, can become unstable as the governing system overreacts to instantaneous load changes. Over-speed protection devices can also be fooled by the harmonic ‘peaks’, causing the generator to shutdown under false alarm.
Over-sizing the alternator capacity can greatly assist in meeting this problem and a minimum factor of 1.6 should be applied to the load rating to calculate the minimum alternator size. A true load characteristic printout should be obtained to accurately calculate the alternator size.
Where the bulk of the site load is DC, a DC standby generator is a better option. It brings the advantage of freedom from problems with harmonics, with no need for changeover switching equipment. Protection against rectifier failure as well as mains power failure is also eliminated.
These units are now available down to very small outputs and larger units can be paralleled to provide redundancy and greater power outputs. For powering test equipment and other light AC loads, a small commercially available inverter can be added.
Generators are not only used for standby power at quarries, but also for power-up equipment, such as excavators and saws. Regardless of their type, size or use, generators need regular maintenance.
Regular service and maintenance
Regular service and maintenance of all generators is essential to ensure consistent and reliable operation, whether being used as a prime power source or as a standby set in the event of a mains power failure. When selecting a supplier, it is important to ascertain the depth and variety of service and maintenance contracts covering their systems.
One of the most popular is Merlin Power Management’s annual PowerCare24 contract. This provides emergency cover 365 days a year, 24h a day, seven days a week with guaranteed responses and, in addition, two preventative services visits each year. On a contract covering a generator, one visit is the standard service and this includes a detailed visual inspection of the installation, from the cooling system and fuel storage system to the fuel pipework, fuel transfer system and control panel, as well as running the set to check correct starting and stopping procedures. The second visit (approximately six months later) is the ‘major’ service, which, as well the standard visit checks, also includes the changing of the oil, fuel filters, air filters, coolant, and the operation and calibration of the control panel, together with an on-load test using the site load. A PowerCare24 contract is also available that covers UPS systems.
Consequences
The loss of power to premises can be catastrophic. Power cuts are also no longer a seasonal phenomenon. Every year adverse weather conditions result in power cuts across the country as local power lines are hit by trees or fail due to lightening strikes, short circuits, human error etc, resulting in disruption to domestic users and businesses alike. Businesses with critical processes or essential facilities should ensure they have entered into a 365/24/7 maintenance agreement, as they can then rest assured that their business is protected at all times from all eventualities.
Case study
By using a super-silent generator from integrated power solutions company Scorpion Power Systems, Melbury Greenstone Ltd have been able to utilize their sophisticated stone-cutting equipment to full potential, while meeting strict environmental regulations on noise pollution. Their equipment is used for cutting stone into various sizes ranging from standard bricks to over a metre square for exclusive building projects.
A new enterprise started by farmer David Fear, the quarry is excavating around 2,000 tonnes a year of indigenous Shaftesbury Greenstone, which is being sold to local builders and developers via project managers, architects and surveyors in southern England. The green sandstone is being dug out of a re-opened quarry, from some 2–3m metres below the surface.
Once the stone has been quarried it is transported to a cutting area for stonemasons to process. The sophisticated saws are powered by a Scorpion DI115, 115kVA three-phase generator, which is housed in a super-silent canopy to provide noise levels as low as 58 dB(A) at 7m.
Scorpion supplied the generator with an electronic speed control to reduce the effects of variable loads and keep the output voltage constant. A 12h fuel tank is also fitted for continuous operation.
Shenton Group, Shenton House, Walworth Road, Walworth Business Park, Andover SP10 5AZ; tel: (01264) 349400; fax: (01264) 349411; email: chp@scorpionpower.com