New Jet-Pump Transfer System for Tarmac
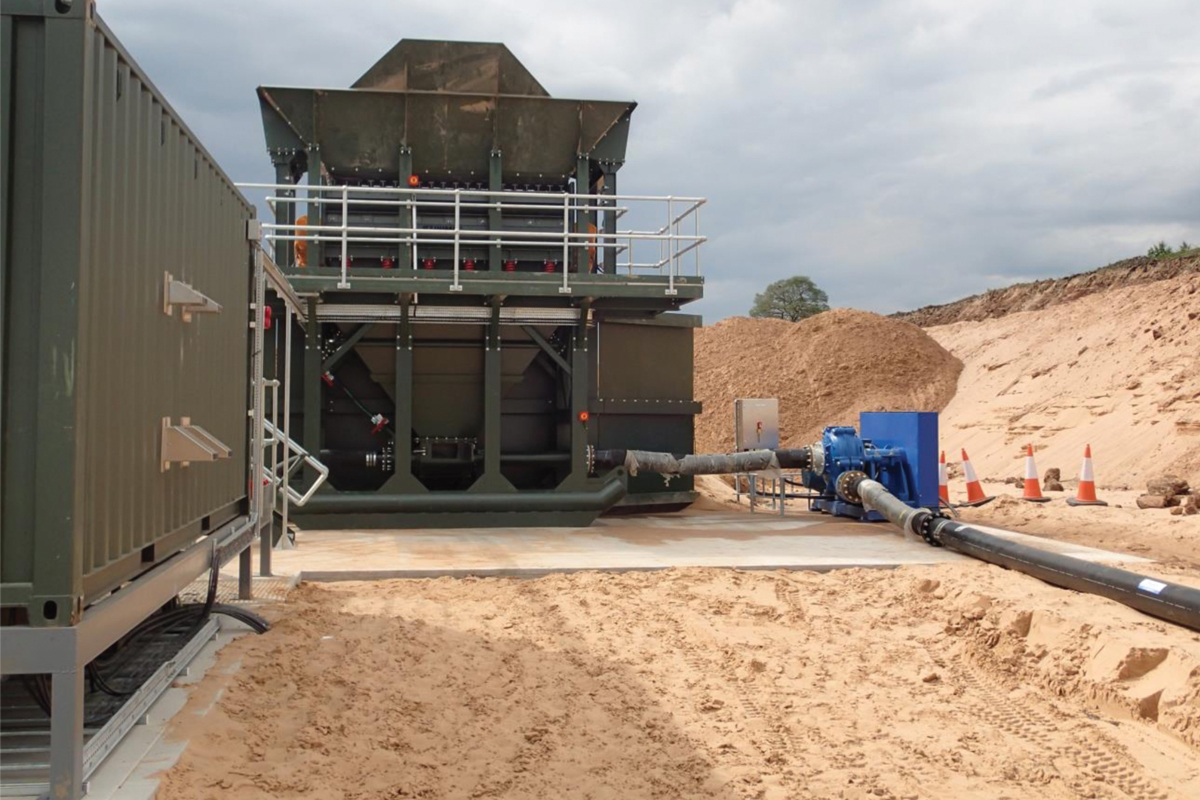
First published in the July 2019 issue of Quarry Management as Jet Propelled
Tarmac install new 250 tonnes/h jet-pump transfer system at Eaton Hall Quarry
Tarmac have added to their existing jet-pump transfer systems by installing a second 250 tonnes/h set-up for their new northern extension at Eaton Hall Quarry, near Congleton, Cheshire. Opened in the 1970s, the site is worked for sand and small gravel above and below the water table using a 250 tonnes/h ground feed hopper with pre-screening deck for dry digging, together with a 43m long jet-pump dredge capable of extracting material up to 20m deep. Installed by Genflo, these systems have run with very low maintenance requirements for 45 years and only two pipes connecting the dig to the processing plant. There is no need for dumptrucks or conveyor systems and with only a wheel loader operator is required to feed the ground hopper. The dredge system is now fully automated with no-one on board and the whole system runs from the main control room.
When Tarmac were given permission to open up the reserves to the north side of the existing lagoon, they decided to stick with what was already working and approached Jet Pumps UK Ltd (formerly Genflo) for another system. Apart from maintaining the 250 tonnes/h capability, the new set-up also had to be remotely controlled and the pipeline taken across the lagoon to cut the transport distance and power requirement, with a total line length of around 500m.
The reasons for incorporating a jet pump, as opposed to any other sort of pump or mechanical excavation in a solids transfer system, or indeed most other solids transfer or relocation systems, relate to both the hydraulic and physical attributes of the device. First, a jet pump has no moving parts; secondly, it has a pumping characteristic resistant to the formation of pipeline blockages; and thirdly, it can be placed within the deposit and covered by it with impunity.
A jet pump is powered by a supply of pressurized fluid (usually from a conventional centrifugal pump), which is known as the motive flow. The motive nozzle converts this pressure energy into velocity energy, creating a high-speed jet that induces solids through a shroud or suction duct and into the mixing chamber. The streams combine within the mixing chamber to produce a combined discharge against the head required to drive the pipeline. Fluidization nozzles are used to help mobilize and acquire the material. The absence of moving parts lends the jet pump to being embedded in the deposit, ideal for unsupervised bypassing applications.
The jet pump’s most important attribute, however, is its ability to stabilize the flow in pipelines, translating into increased reliability and productivity. This is achieved in two ways. Immediately, an increase in pipeline head, perhaps due to a random change in material grading or induced concentration, is countered by an equivalent rise in head developed by the jet pump, without the large drop in flow rate that would occur in the case of a centrifugal pump. The system keeps running. Following this, the rate of induction of solids falls, gradually reducing the pipeline head and restoring steady flow.
This regulation process is fully automatic and cannot be improved by any automatic control system or operating personnel. Jet pumps can, therefore, be shut down at any time and restarted at will.
At Eaton Hall, the system comprises a shore-based Ideal motive pumpset fitted with a 75kW motor. The pump intake is mounted on a pontoon to allow for changes in water level. Pressurized water at 5 bar from the motive pump is transferred, via a 10in steel pipeline, some 100m to the Jet Pumps UK 130mm jet pump, which is mounted on the base of the feed hopper and above which sits a double-deck vibrating screen with grizzly bars on top and 60mm woven-wire mesh screens below, to reject any oversize. The hopper is fed by a Bell L2606E wheel loader with a bucket capacity of 4.4m3 (heaped). The hopper is also fitted with high- and low-level fluidization jets driven via a take-off from the motive feed line. These jets serve to fluidize the material and aid its induction into the jet pump.
The material leaving the jet pump passes via a diffuser and into a Weir Minerals 10/8 FM rubber-lined pump fitted with a 132kW motor. This unit serves as the booster to drive the slurry the 500m to the existing transfer station, from where another jet pump and booster sends it the final 800m to the processing plant.
The discharge pipeline comprises a mixture of 12m and 6m HDPE pipe, linked with 3m SWA flexible sections to allow for movement when crossing the lake. Once afloat, the line is supported by two-piece plastic floats filled with closed-cell foam and spaced every 3m. The HDPE pipes are linked with Straub Plast-Pro joints for easy connection and dismantling.
The whole system is controlled from electrical cabinets in an air-conditioned container alongside the hopper. The motors for the motive and booster pumps are inverter controlled and there is a local touch-screen control panel. The remote control is effected by a radio link from the main control room.
Tarmac operations manager Kim Shilcock said: ‘Over the life of the site we have found the jet-pump systems to be very reliable, simple to use and low cost in operation. It made sense to stick with this now well-proven technology when moving into the new extension.’
For further information visit: www.jet-pumps.co.uk
- Subscribe to Quarry Management, the monthly journal for the mineral products industry, to read articles before they appear on Agg-Net.com