Metso assist in dewatering Celtic Energy’s East Pit site
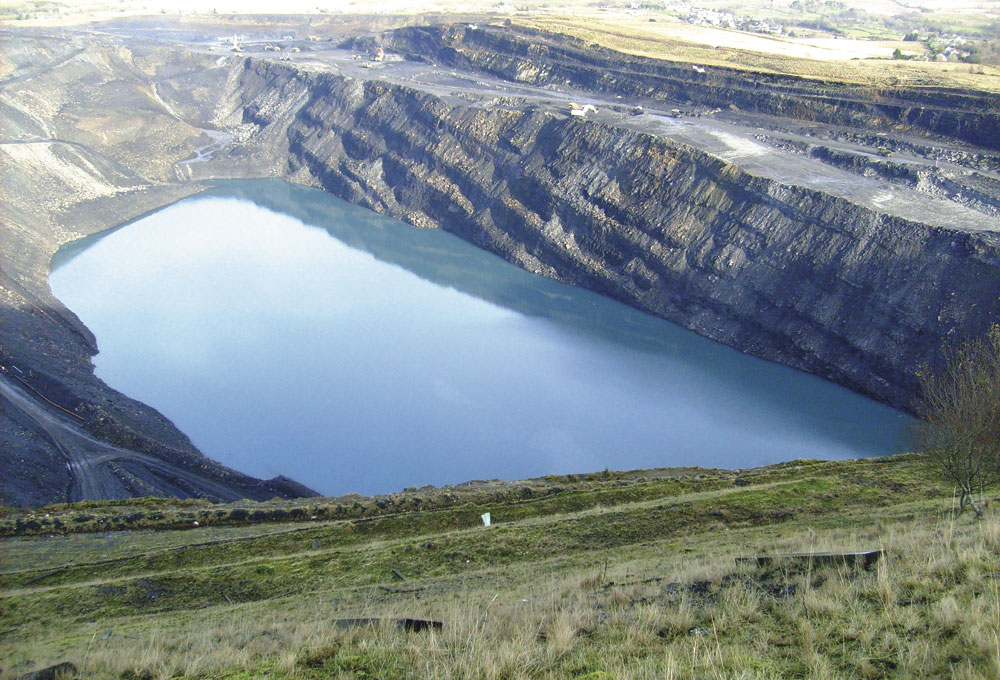
Celtic Energy reopen dormant opencast site
Celtic Energy are the leading coal mining operators in South Wales, with four surface coal mining sites – Selar, Nant Helen, Margam and East Pit – producing in excess of 1 million tonnes of high-quality coal each year for domestic, industrial and electrical-generation demand in the UK and elsewhere in Europe.
Last year, due to favourable market conditions, preliminary works began to reopen the company’s East Pit site, which had lain dormant since 2001 and, as a result, had accumulated a large body of water in the existing excavated void.
Metso were contacted with a view to assisting with the dewatering of the pit and, once dewatered, providing a permanent installation to maintain the lowered water level. The rate of dewatering requested was 800m3/h with the total differential head starting at 110m and increasing to 160m at the pit floor. The ‘dirty’ water removed would be pumped to existing water-treatment facilities before being discharged from the site.
The concept proposed by Metso and accepted by Celtic Energy was based on use of the Orion series HM250 10in end-suction heavy-duty slurry pump, which features an abrasion-resistant, high-chrome iron wet-end construction. Two pumps were installed in series, with the first stage HM250 unit pumping into a break tank and the second stage HM250 pumping to the discharge point.
The first-stage pump set is mounted on a pontoon (sourced by Celtic Energy) and supplied fully assembled on a common skid with Selwood automatic self-priming equipment, a 315kW WEG motor, wedge-belt drive and guard. This pump discharges into a break tank where the second-stage pump is installed in a fixed location and assembled on a common base with a 315kW WEG motor, wedge-belt drive and guard.
With the increase in the static head as the water level decreased, the speed of the first stage pump was increased by changing the wedge-belt drive. Using valves installed within the discharge pipeline, a constant volumetric flow rate was maintained to match the output of the second-stage pump.
During the commissioning phase in August 2008 a Metso site service engineer was present at all times; the engineer also returned subsequently to alter the running speed of the first-stage pump as the water level within the pit dropped. After 12 months of continuous pumping, and despite the best attempts of the Welsh weather, the pit was successfully dewatered and Celtic Energy are now able to gear up for full production at East Pit.
An estimated 2 million tonnes of coal will be produced at this site over the next six to seven years, helping to address the UK’s growing energy gap with safe and secure fuel. In addition, the expansion has created 90 direct and numerous indirect positions for local people as well as considerable investment in the local area.
Wayne Evans, site manager at East Pit, commented: ‘A mammoth task was presented to the pumps when they were installed; not only did they have to displace the large body of water that had developed but they also had to contend with the aberrant levels of rainfall and inflows from old deep mine workings.
‘Over the period, the performance of the pumps combined with technical and service support from Metso personnel resulted in the successful dewatering of the area with the minimum of disruption, creating invaluable tipping room for the next phase of our operation. Routine maintenance has been the only downtime since inception.’
Designed for the most arduous industrial slurry pumping applications, the effective hydraulic design of the Orion series of horizontal pumps is said to guarantee maximum efficiency throughout the life of their generously proportioned wear parts, thereby reducing both the rate of wear and the power consumed.
The pumps supplied to Celtic Energy incorporate a patented double-adjustment design feature, which allows the closure of the back and front impeller clearances, permitting optimum continuous performance of the pump throughout the normal wear life of all components. This simple operation can be made on site without disassembling the pump.
For ease of maintenance and routine inspection or repair, the bearing frame and rotating element can be removed as a single unit (back pull-out) or, alternatively, the casing can be removed after removal of the inlet and discharge pipework (front pull-out).
According to Metso, focused product development and over 60 years of experience from thousands of applications have led to continuous improvements in their range of horizontal and vertical centrifugal slurry pumps, resulting in numerous benefits to customers, the most significant being the lifetime cost savings.