Improving Conveyor Performance With AC Drives
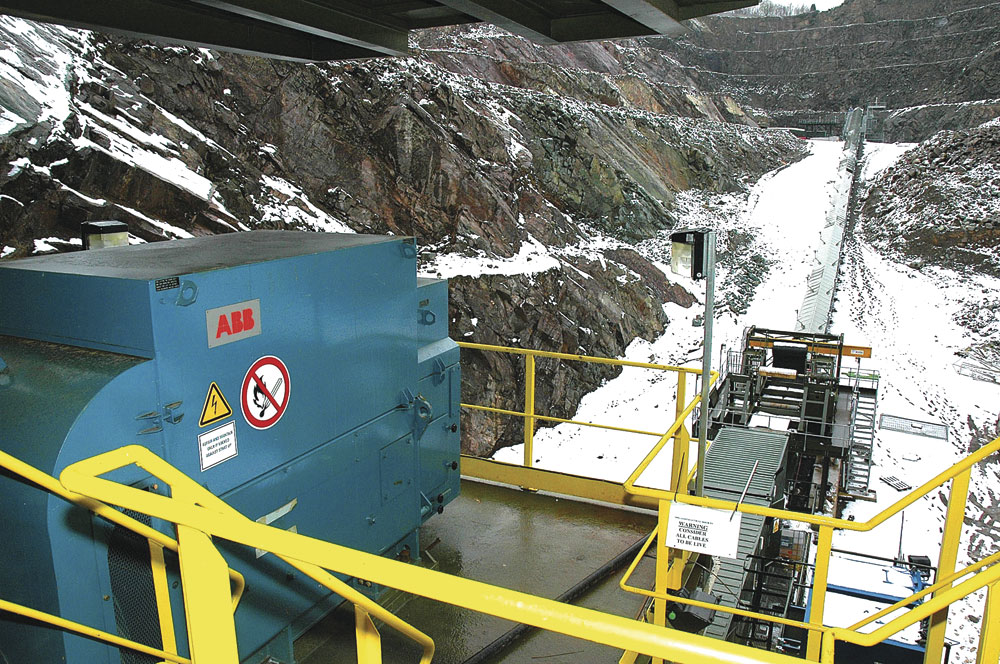
The use of AC drives on quarry conveyors gives more reliable operation, reduces maintenance and helps save energy. The smooth operation that AC drive conveyor motors provide reduces the strain on both the mechanical and electrical systems. Pekka Pulkki, cement & mining market manager for ABB’s low-voltage AC drives, outlines the benefits in greater detail
Conveyors are used extensively in many parts of the quarrying process, often in demanding conditions with the risk that the conveyor belt will be stretched, suffer slippage or break completely. Sustained wear can lead to reduced reliability or even failure of the conveyor belt, which can be catastrophic in an industry focused on maintaining uptime.
AC drives help protect belts and other mechanical equipment by offering smooth and accurate control of the motor speed and torque, prolonging conveyor life while lowering operational and maintenance costs. Also, if a joint within the conveyor belt needs repairing, the AC drive will allow the user to move the belt into position very accurately.
Improving reliability and control
Conveyors with a very high starting torque have the potential to damage both the mechanical equipment and the power supply. On long conveyors in particular, the loads can be very high as there is more material on the belt, with higher starting torque and more current required. Soft starters can be used to reduce the starting current, but they also reduce the torque. If the conveyor is fully loaded at start-up, it may not start at all if the torque is insufficient.
The AC drive offers high starting torque combined with low starting current, eliminating current peaks and voltage fluctuations on the network. In addition, power factor is close to unity at all times. With a more stable network, all electrical equipment on site will run more reliably, increasing productivity and reducing the need for maintenance. Smooth starting with accurate torque also minimizes belt stretching and slippage. On belts that are already stretched, the AC drive minimizes the risk of slippage.
As well as protecting the conveyor belt, AC drives provide efficient operation of the equipment by offering smooth and accurate control of motor speed, allowing adjustment of the speed to suit the needs of the process. The drive can also be connected to the plant’s automation system, which can monitor the load and speed and use these parameters for volume calculations.
Provided that the motor and the mechanical equipment are suitable for a higher speed, the conveyor speed can be increased freely. In applications where the speed needs to be reduced below the motor’s nominal speed, motor cooling can be an issue if self-cooled motors are used. This can be addressed by using force-cooled motors.
Saving energy
Energy savings can be made by eliminating reactive power compensation, which is not necessary when using an AC drive. Energy can be also saved by running the conveyor at reduced speed when full speed is not required.
Further savings can be achieved by using the power generated when a conveyor travels downhill; where conveyors run over long distances and across varied terrain, they are often generating for much of the distance. With an AC drive, it is possible to run the conveyor smoothly across the whole conveying distance, even if there are large differences in horizontal and vertical curves. All the braking energy can be generated back to the network when using an AC drive. Another way to utilize the braking energy is to use a common DC bus drive system, where several AC drives are connected together with DC busbars and braking energy is fed from the motors that are braking to the motors that are driving.
Further benefits are possible when using a drive with the direct torque control (DTC) motor control platform, available with ABB industrial drives. For example, load sharing can be arranged between motors on the conveyor. An equal load ensures that the motors do not overheat and trip out, thereby disrupting the transport of material.
DTC also detects when the load on the conveyor belt rises suddenly, increasing the torque requirement rapidly. This is detected instantly allowing the drive to react immediately to the change in torque. A drive with a less-sophisticated torque control system may trip in these situations.
AC drives power kilometre-long conveyor
In Leicestershire, Midland Quarry Products have one of the UK’s longest quarry conveyors in variable-speed operation at their Old Cliffe Hill site.
The conveyor is more than 1.5km in length and transports primary crushed granite from the quarry, through a 713m underground tunnel, before conveying it to a secondary processing plant.
Prior to being conveyed, the rock is crushed by a gyratory crusher powered by a 450kW, 3.3kV motor. The primary section of the granite process plant operates at 2,500 tonnes/h and is a key component of the overall process.
The conveyor system itself consists of six separate conveyors, each 1,600mm wide and of varying lengths. The speed of the conveyors is controlled by ABB industrial drives. One conveyor features two 200kW drives; three of the conveyors use single 200kW drives; and the final conveyor is fitted with a 132kW drive.
The two drives on the first conveyor feature master-follower software, which ensures that one drive dominates the control pattern and the second one follows. This avoids the motors fighting against each other, which could lead to conveyor belt damage.
Should the conveyor stop while loaded with granite, the drives offer the ability to soft start the motors, gradually bringing the conveyor back up to speed. Without this facility, the motors would be stressed and subsequently burn out.
The use of AC drives also means that the conveyor discharge speed into the bunker can be precisely controlled to place the material exactly where it is wanted.
Simplified design
AC drives also help to simplify the conveyor drive system, potentially reducing the investment costs as well as the maintenance needs. With the motor speed adjusted for the application, the gear ratio can be optimized and a simpler gearbox can be used. In some cases it may be possible to eliminate the gearbox altogether, improving the efficiency of the system. The simple asynchronous motor requires minimal maintenance.
The smoother control of the mechanical system reduces the stress on couplings and gearboxes, allowing for longer service intervals.
The AC drive can also help simplify maintenance by permitting reverse rotation of the motors. This makes it easy to reverse the belt and stop at the required spot. If the conveyor gets jammed, the drive detects this and stops the conveyor.
By offering improved reliability, reduced maintenance, better control and energy-efficient operation, AC drive control can offer a clear competitive advantage to mine and quarry facilities.