Hose Pumps for Quarry Duties
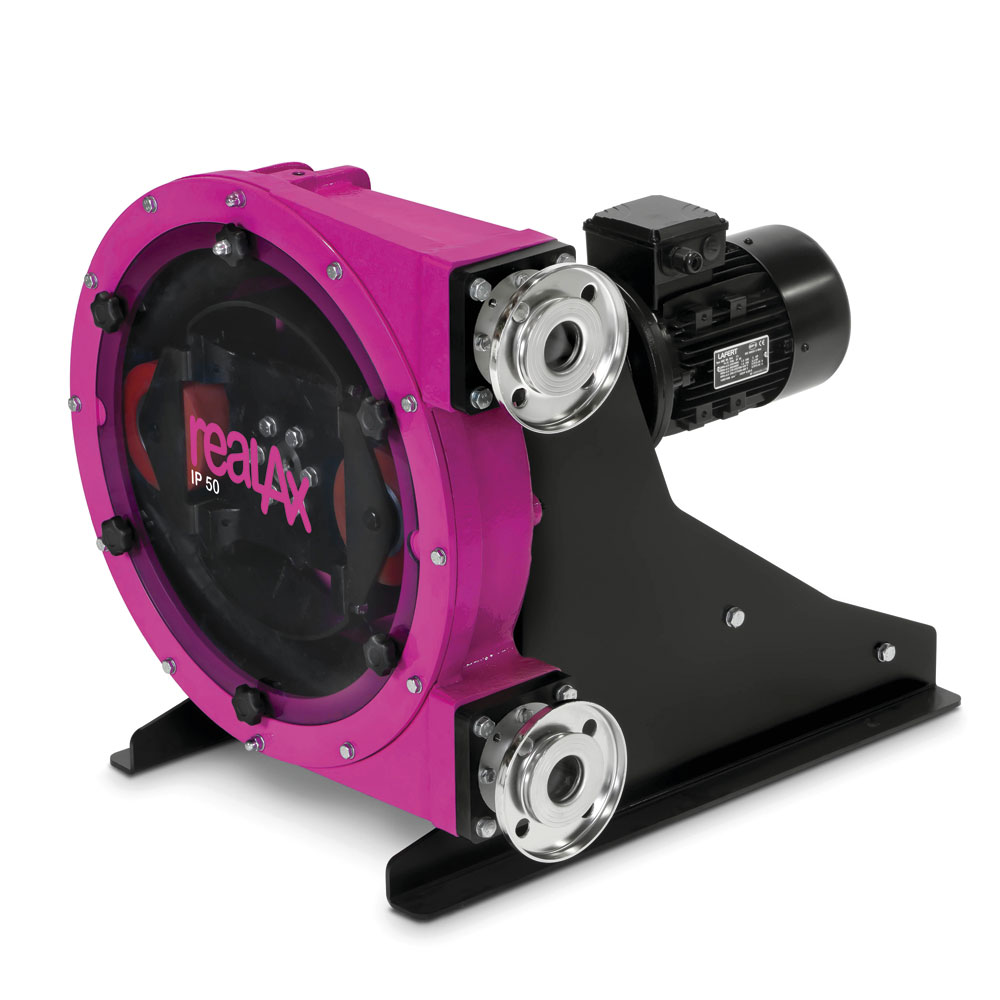
By Tony Peters, managing director, AxFlow Ltd
The transfer of solids-laden water encountered in quarrying demands a type of pump that is extremely robust, low maintenance and capable of standing up to the aggressive nature of the pumped liquid. While rotating pumps containing open impellers can perform outstanding service, there is always going to be the problem of impeller wear and damage to the pump housing, making maintenance a constant requirement along with frequent parts replacement.
An alternative pump type that should be considered is the hose pump. Suitable for applications ranging from precision dosing through to transferring sludges and slurries, the hose pump delivers leak-free operation, is ideally suited to challenging open environments and, most significantly, is easy to maintain.
The main features of these peristaltic pumps include:
- Seal-free design
- Valve-free
- Dry self-priming
- Gentle pumping action
- Dry running
- High suction lift
- Abrasion resistance
- Low maintenance
- No slip
- Reversible
The hose pump is a positive-displacement pump where the fluid is contained within a hose or tube inside the casing. The fluid is moved into and out of the tube/hose by the action of rotating rollers or shoes which alternately compress and relax the tube/hose. This ‘peristaltic’ process ensures that the fluid is transported accurately and without any variation in volume. Moreover, the dosing pump is economic with the liquid pumped because at the end of the processing cycle or operation, the pumping motion can be reversed and any fluid remaining in the hose/tube can be returned to its source for future use, thereby draining the tube/hose.
Shoes or rollers
The decision to use a shoe or roller hose pump is largely dependent upon the application and the operating pressures required for the application. Rollers are more suited to lower-pressure applications, typically up to 4 bar, and are usually limited to a maximum of 8 bar. Therefore, smaller drives are required which results in less power being consumed. Roller technology is also easier to maintain, with simple hose replacement and less waste fluids due to the elimination of hose lubricant.
Shoe compression pumps are more suited to applications demanding operating pressures up to 16 bar and higher flow rates. This type of pump is a robust workhorse built for the most arduous of operating conditions and fluids.
The hose pump is now regarded as a mature product and a proven technology, so making improvements can present a challenge for pump designers. However, AxFlow have recently introduced a new design of hose pump that offers users a combination of pressure versus flow options. The four models in AxFlow’s ‘realax’ pump range provide capacity rates from 0.16 millilitres/rev to 20 litres/rev, and pressures from 2 to 15 bar.
The realax APY Series roller compression hose pumps are the smallest in the range, developed for low-volume, low-pressure dosing applications. The ISI and IP Series (fig. 1) are both roller compression pumps with capacity rates from 0.023 litres/rev to 10 litres/rev at pressures between 2 and 8 bar. Both can be used where sludges and slurries are to be transferred.
The RP Series (fig. 2) of shoe compression pumps provide pressures up to 15 bar and capacity rates of between 0.3 litres/rev and 20 litres/rev. Each model comes in four versions: bare shaft, gear reducer (fixed speed), integrated inverter and mechanical variable speed.
Accessories for the realax pump range include: leakage detector; batch controller; vacuum equipment; and discharge pulsation dampeners. For quarry applications, natural rubber hoses offer optimum abrasion resistance for long service life.
The realax pump range also addresses the issue of making maintenance easier by incorporating a new design of inspection window on the pump housing. Generally, the inspection window of a hose pump allows the operator to check the oil lubricant level in the pump housing. AxFlow’s large inspection window eliminates the need to remove the front cover of the pump case, making it easy for the operator to access the rotor and the hub, and to change the number of shims in order to accommodate pressure changes demanded by the application.
Pump development programme
‘For quite some time, our customers have demanded a hose pump that operates efficiently at low pressures while continuing to give high levels of accuracy. Easier maintenance was another key issue,’ commented Hakan Bjernér, manager of business development with AxFlow Holding AB.
‘This new range of peristaltic pumps allows AxFlow to address the low-pressure end of hose pump applications. Whether the application involves dosing small, precise quantities of fluid at low pressures or high accuracy pumping of large volumes of viscous or abrasive products, peristaltic and hose pumps provide an effective solution.’
For further information visit: www.axflow.co.uk